Hermetic Seam Sealing Enables Reliable Welds and Protects Electronic Devices from Harsh Environments
A primer on the two processes – parallel gap resistance seam welding or opposed electrode projection resistance welding – you can use to win customers in the highly demanding aerospace, industrial 5G commercial communications, medical device, and military electronic industries.
Posted: November 9, 2020
BY MARK SUNICO
Seam sealing, or seam welding, is a variation of resistance spot welding most often used to join the lids to the cans of electronic packages. The process uses two motor-driven electrode wheels positioned on opposite sides of the package and rolled along the perimeter, conducting current through both components to create the seal.
Hermetic seam sealing completely seals the package into an airtight metal or ceramic housing using one of two processes: parallel gap resistance seam welding or opposed electrode projection resistance welding. It’s key to manufacturing sensitive microelectronic devices used in industrial and commercial communications, transportation, military and aerospace industries, which often include optical sensors, pressure sensors, communications devices, thermal and laser imaging and power amplifiers.
Hermetically sealing these packages prevents degradation of the electronic components inside and extends lifetime usefulness by protecting these highly sensitive components from contaminants such as air and moisture. Implantable medical devices, like pacemakers and defibrillators, also require hermetic sealing to protect both the device and the patient.
Two Types of Microelectronic Packages
There are two primary types of packages: metallic tub and ceramic (Figure 1).
FIGURE 1: At left, a metal tub package; at right, two types of ceramic packages.
The preferred material for metallic tub base packages is Kovar, which has a similar coefficient of thermal expansion (CTE) as glass. The material prevents the metal-to-glass seals of the package’s feedthrough connectors from leaking due to material expansion from heat generated during the welding process.
Ceramic packages are made of a ceramic substrate with a brazed metal seal ring. Kovar is also used in ceramic packages; the Kovar is brazed onto the ceramic base as a seal ring to which the lid is welded.
Parallel Gap Resistance Seam Welding
Parallel gap seam welding is one of two ways to execute a hermetic seal. A seam welder with rolling wheel electrodes is connected to a power supply that delivers electric current across the electrodes through the lid and the package. The seam welder delivers multiple overlapping weld spots, thus creating a continuous weld (Figures 2 and 3).
FIGURE 2: Schematic of parallel gap seam welding.
FIGURE 3: Schematic showing electrodes and spot welds forming seam.
Opposed Electrode Projection Resistance Seam Welding
Opposed electrode projection welding uses opposing electrodes to join a header, which contains the electronic device, to a cap with a ring or annular projection by running current across the electrodes through both the cap and the header. The heat that’s generated is directed through the projection to weld the parts together (Figure 4).
A successful weld should have at least a 50%-to-90% projection collapse. Linear displacement measuring device sensors, also known as linear variable differential transformers (LVDT), can be added to the weld head to measure this collapse. Additionally, a fillet formation is typically seen at the perimeter of the cap indicating a successful weld.
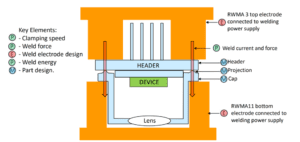
As with parallel gap seam welding, the part design of the metal packages in opposed electrode projection seam welding is very important. The projection can be on the cap or the header, but there must be a constraining feature between the two so the parts self-align.
Once again, the preferred material is Kovar. For best results, the projection should be located in the middle of the flange, so that as the projection collapses, the displaced material is evenly distributed across the width of the flange.
Testing and Troubleshooting
Weld strength destructive testing can be performed to ensure welds are secure. In destructive testing, seeing at least a 25% weld joint still intact after significant attempts to mechanically separate the lids or caps from the base is a good indicator that a strong weld was achieved.
Other testing methods include helium fine leak and gross leak bubble testing, optical fine leak detection, internal gas analysis, particle impact noise detection, and temperature cycling.
The Future of Hermetic Seam Sealing
Hermetic seam sealing technology can be critical to success in such demanding applications as industrial 5G commercial communications, aerospace, and military electronic devices. Ensuring an excellent seal through welding is extremely important, and only trusted weld device manufacturers who account for the demands explained above can ensure highly accurate and reliable welds.
Manufacturers are incorporating these standards into controlled-environment welding technology and developing technology that will enable even greater accuracy and weld success. The future of hermetic sealing is likely to be robot-assisted seam sealing pick-and-place with smart vision systems, which have the potential to eliminate current margins of error and lead to even greater success in hermetic sealing of sensitive electronic devices.