CAMBRIO and SigmaNEST Keep Innovation at the Forefront of Everything They Do
CAMBRIO aims to help shape the future of manufacturing and assist its customers in meeting changes head on. CAMBRIO’s brands, including SigmaNEST, comprise a diverse set of smart end-to-end design and manufacturing software solutions. The acquisition by Sandvik allows CAMBRIO to collaborate with the Sandvik family and put those resources to work for the benefit of customers.
Posted: January 31, 2022
SUPPLIER PROFILE
By Rachel Duran and Joe Hazelton
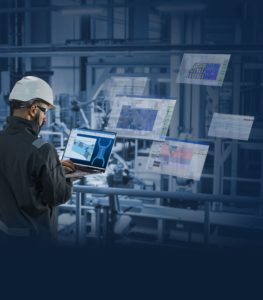
The past year has been an exciting one for Cincinnati, Ohio-based CAMBRIO, which offers design and manufacturing software to the fabrication, toolmaking, and production-machining industries. CAMBRIO, which formed in 2020 and brought together three brands, was acquired by Sandvik in 2021.
“Sandvik wants CAMBRIO to remain its own brand. The Sandvik philosophy of management is decentralized,” said Glenn Durham, vice president of engineering for CAMBRIO. “This means that CAMBRIO retains its own brands and its customer-centric focus while working together with the other brands in the Sandvik family of engineering companies. This brings significant value to our customers as we collaborate in innovation with the diverse Sandvik teams. All of that allows us to deliver a better product in the end.”
With the acquisition, Sandvik’s aim is to provide customers with software solutions that enable automation of the full component manufacturing value chain — from design and planning to preparation, production, and verification, according to press materials from Sandvik. Computer-Aided Manufacturing (CAM) plays a significant role in the digital manufacturing process. By acquiring CAMBRIO, Sandvik aims to establish an important position in the CAM market that includes both toolmaking and general-purpose machining. The effort will complement Sandvik Manufacturing Solutions.
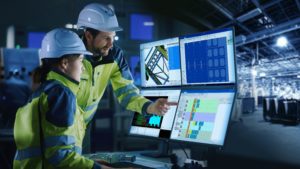
Added Durham: “Sandvik recognized that many of their customers needed and wanted solutions in computer-aided manufacturing. So, the acquisition of CAMBRIO really brings a whole new dimension to the Sandvik portfolio by offering industry-leading solutions in the CAD/CAM field.”
Sandvik brings the wisdom and strength of an industry leader with 37,000 employees, 60 R&D centers, and 5,000 active patents, and a business focus on customers, agility, employee value, digitalization, sustainability and growth, noted Marc Freebrey, vice president of marketing for CAMBRIO. He added “At the same time, Sandvik values each individual brand as well as CAMBRIO’s business plan and is equally passionate about serving the customer. This will have a positive effect on CAMBRIO and SigmaNEST that is visible to “our customers, not only in the products, but also the way we do business.”
“We are investigating what it means to be integrated into the Sandvik family and how we can make use of the many resources that are available and put those to work for our customers,” Durham said. “There are a lot of different, interesting things Sandvik is able to do because of their size and diverse portfolio.”
As the manufacturing industry continues to find ways to change the future, from automation to electrification to sustainability, CAMBRIO will assist in shaping the industry. “As part of the Sandvik Design & Planning Automation division, we are excited to collaborate and increase productivity in the broader value chain,” Freebrey noted. “In particular, SigmaNEST provides software that impacts the full range of fabrication workflow, from quoting to production to shipping.”
Strong Manufacturing History
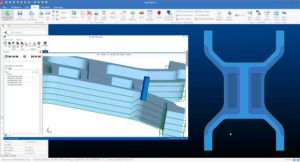
CAMBRIO’s three brands include SigmaNEST for sheet metal fabrication; Cimatron for mold and die; and GibbsCAM for production milling, turning and mill turn operations. Each brand brings with it more than three decades of strong manufacturing histories. The goal is to be a leading CAD/CAM innovator serving these industries.
CAMBRIO’s software offerings are comprised of a diverse set of smart end-to-end design and manufacturing solutions that assist customers in expanding their potential. Plus, each brand is machine agnostic, which is a huge benefit to manufacturers with equipment from a variety of suppliers throughout the world.
For example, SigmaNEST offers extensive integration capabilities through their modular Connected Shop software suite for fabricators. The software modules include scheduling, quoting, and logistics, which are informed by shared data and CAD/CAM nesting intelligence in nearly every type of cutting, punching, routing, tube and bending machines. The nesting component allows fabricators to draw parts in the software and automatically orient the parts close together to produce as much as possible from a piece of sheet metal.
The Connected Shop allows fabricators to connect all the information and activities taking place in a shop as opposed to dealing with isolated pieces of information. Durham said with the Connected Shop, companies can share accurate and timely information across their systems. As an example, team members can view what is available in inventory, as well as what inventory is scheduled to be used during the next month. The software provides details such as vacation time for operators so that shops can give an accurate delivery date for a customer’s project at the time of the quote.
Streamlining the Fabrication Process
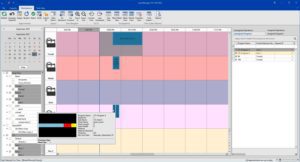
Fabricators and machinists know how to manufacture parts. However, computer programs such as SigmaNEST, allow shops to do their work more precisely, Durham noted. One such customer is Tampa Bay Steel (Tampa Bay, FL) that predominately uses SigmaNEST for manufacturing. The company specializes in cutting both flat products and structural shapes in various grades of carbon steel, stainless steel and aluminum. The company’s laser center features six advanced TRUMPF and Mazak machines, and the recent addition of a Mazak FG 220 DDL tube laser. Tampa Bay Steel has an eight-person engineering team.
The company appreciates the machine-agnostic and user-friendly approach to SigmaNEST. The company’s engineering team formerly utilized the proprietary software that came with each machine, which resulted in one programmer who knew how to run a laser, one programmer who knew how to run the waterjet and so on. Tampa Bay Steel’s cutting machines were operating as islands that required specialized programming, which created bottlenecks and machines that were sitting idle. “Now we have consolidated with SigmaNEST, and I can throw any program at any team member and have them program it for any machine to match workflow capacity,” said Dave Carpenter, Engineering and Estimating Manager for Tampa Bay Steel.
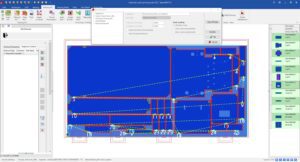
Carpenter added that Tampa Bay Steel purchased SigmaNEST with future machine purchases in mind. The team didn’t want to be constrained by relying on the proprietary software that came with each machine, but instead utilize a software system where they could select the best machine for the manufacturing process. “SigmaNEST allows us to focus on our core business while entrusting nesting and CNC programming to the experts,” Carpenter said.
Tampa Bay Steel’s leadership wants to stay ahead of the industry trend line to ensure they remain competitive and profitable. “SigmaNEST has been hugely beneficial as it’s allowed us to improve all areas of the manufacturing workflow, from quoting through to production,” Carpenter said. “Our estimators are all using SigmaNEST and can push jobs directly into production knowing the job will be programmed exactly as quoted.” What’s more, Tampa Bay Steel has added new machines and expanded the capabilities of the company without having to add more employees. When Tampa Bay Steel added a Mazak OptiPlex 3015 Fiber Laser, the machine was up and running in one day using SigmaNEST software.
What’s Next? Building the Future of Manufacturing
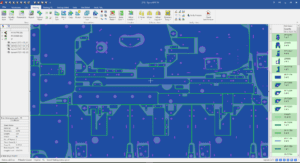
Due to labor shortages and supply chain disruptions, manufacturers continue to work towards achieving greater efficiencies, automation, and better utilization of resources, Freebrey pointed out. The move to more automation and smart factories plays an influential role in the growing importance of managing data both in and out of devices. Software systems that detail the entire production workflow help customers exploit added value from data.
Freebrey noted reshoring of manufacturing operations back to the United States is gaining momentum and as a result manufacturers will adopt more agile and demand-driven business models. They will operate on shorter lead times, with reduced inventories and flex production. “SigmaNEST fully supports this methodology and continues to develop comprehensive software on both ends of the production workflow that focus on optimizing material utilization, machine motion, manpower and data management,” he added.
“Companies need and want to have information available to make better decisions,” Durham said. “That is huge. That is every day.” He added that the continuing globalization of business and economies means more companies insist on a flexible software solution that allows them to manage data from various locations across the globe.
These capabilities are driven by CAMBRIO’s focus on innovation. Durham said that sometimes when referring to a company that has been around for 25 years, customers may begin to wonder if the company might lose their spark. “That is not who we are,” Durham said. “That is why Sandvik acquired CAMBRIO; we are not that way.”
Rather, Sandvik wanted to know where CAMBRIO would be 10 to 20 years from now — what the future might hold. Sandvik was attracted to CAMBRIO due to its dedication to innovation. “That is my 100 percent focus: how can we innovate?” Durham noted.
Future developments include a hybrid solution where customers can utilize cloud-based solutions as well as web browser solutions that use an on-site server. “We see that as adding tremendous benefit and value to our customers,” Durham said.
CAMBRIO’s goal is to produce software customers will love. “Our developers and product managers keep this slogan in the forefront as they develop the software. In addition to being software providers, we also use many software tools. So, we began to examine the software we use and ask: ‘Okay, what is it I really love in this software?’” Durham noted. “With that sensitivity, it changes the way we develop products for our customers.”
CAMBRIO’s diverse end-to-end design and manufacturing software solutions assist customers in reaching their potential. With the acquisition of CAMBRIO by Sandvik, the CAMBRIO team is part of a family with a wide array of resources, which they can put to work for their customers. The company will help customers create the future of manufacturing. Which bodes well with CAMBRIO’s philosophy: “Not, what would our customers simply like? What would they love?” Durham said.
CAMBRIO’s Agile Software Development Process
CAMBRIO’s developers have built the infrastructure necessary to shorten the distance between itself and its customers to ensure they are more responsive to customers’ needs. It’s all about the feedback loop.
“We did the infrastructure work,” said Glenn Durham, vice president of engineering for CAMBRIO. “We use some really advanced tools, like Microsoft’s Azure DevOps. These kinds of infrastructure tools and this kind of development philosophy are not features that we advertise or sell. However, it is the critical and efficient infrastructure. It’s like the bridges that make transportation work.”
Azure DevOps and related supporting systems assist CAMBRIO — and SigmaNEST — in managing the process of gathering feedback from customers and turning it into products that satisfy customers’ needs. Durham said SigmaNEST software for sheet metal fabricators has implemented a much more robust product release life cycle in the last five years.
“We’re able to deliver our products in a timelier manner, more robustly,” Durham said. “What I mean by that is: better testing, and more targeted releases than we’ve ever been able to do before. That really helps customers.”