Streamlining the Transition to Robotic Welding
Modular welding cells and an intuitive programming interface simplify the adoption of robotic welding for SMEs.
Posted: January 31, 2022
ADVANCING AUTOMATION
By Tom Fuhlbrigge
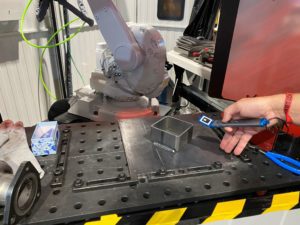
An interesting dichotomy exists in the metal fabrication industry in North America. While readily available statistics indicate the market is expected to expand at a CAGR of more than 4.8 percent through 2025, according to the American Welding Society the well documented shortage of welders will reach 400,000 by 2024.
With the average age of a welder ranging in the mid-50s, more and more companies are turning to robotic automation to meet the demand for the vast array of parts and products that require welds. Supported by recent technological advancements that have simplified the procurement and programming of welding robots, a big part of the growth is coming from small and mid-size enterprises (SMEs). And not just for simple welds, but for those in the more complex range, in high-mix, low-volume production scenarios.
Increased throughput, flexibility, consistent quality
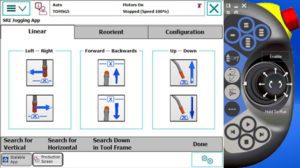
Robotic welding systems do far more than pick up the slack for the dearth of manual welders. When properly installed and programmed (more on this below) they provide exceptional throughput, product quality and manufacturing flexibility.
A robotic welding cell can generally achieve three-times the throughput of a good manual welder. A human welder usually has a 20-to-25 percent arc on time, which is the percentage of time that they are actually welding. The rest of the time they are adjusting the part or doing other tasks, or simply taking a break since welding is physically demanding.
Equipped with two workstations, a one-robot welding cell typically achieves a 75 percent or better arc on time. While the robot is welding on one station, the operator can unload a finished welded part from the other station, and then load the next part to be welded. Once the robot completes one part it can immediately switch stations and start welding the new part.
The path accuracy of a top-of-the-line industrial robot dressed for welding provides unmatched production consistency and quality, never tiring or wavering from weld to weld. A virtually unlimited number of weld programs can be stored in the robot controller, providing the flexibility, with the press of a button, to weld parts in small batches, or piece by varying piece, depending on the production needs.
The return on investment (ROI) calculation on a robotic welding cell includes a number of variables, but a throughput improvement from 25-to-75 percent, coupled with improved weld quality and unmatched flexibility are the lead drivers of the equation.
Pre-engineered robotic welding cells expedite installation
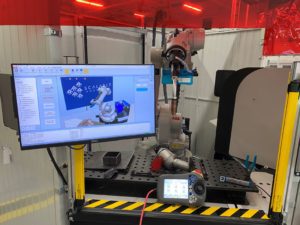
In recent years the major industrial robot manufacturers have developed pre-engineered welding cells that come with all the components necessary to get started with robotic welding, greatly expediting the adoption process for SMEs no matter their technical resources.
One example is ABB’s line of FlexArc® robotic welding cell, which are available in a variety of modular packages, allowing an end-user to select the model that best suits its production requirements.
All standard FlexArcs feature one or two robots and often an additional workpiece positioner. The equipment is all installed on a common platform, providing shorter commissioning times and the ability to easily relocate the cell within the production facility. The cells are equipped with centralized power distribution with all components powered from one source.
If there are any doubts about the weldability of certain parts, ABB can perform welding tests in its own laboratories. The robotic cell is then pre-built and tested at an ABB service center, where the customer has the opportunity to verify that its configuration meets expectations before it is transported to the production plant.
All that is needed on the customer site is the connection of air, gas and power, and in many instances, the system can begin welding the same day it is delivered.
Intuitive Programming Interface
Objectively speaking, the biggest barrier to entry for SMEs adopting robotic welding has been the concern about the potential monetary and labor investment needed to program the system to weld a broad range of parts, of varying complexities. Even a “ready-to-weld cell” needs to be programmed.
Fortunately, the most significant advancements in robotic welding have been the recent trend towards more intuitive and easier-to-learn programming interfaces. Some require no CAD or robot code for the programming.
One such intuitive programming platform is from Scalable Robotics, which allows a human welder to teach a task to the robot in the same way he would teach another person — just by pointing to where the weld should be applied and letting the robot learn the path on its own.
The Scalable Robotics platform will generate a weld path that is validated within RobotStudio®, ABB’s powerful offline simulation programming software. The operator can then make any final modifications, and the robot will auto-tune the program using standard sensing technologies.
The modest cost of a FlexArc cell coupled with the easy and intuitive Scalable Robotics programming platform assuages the concerns of excessive capital investment and a lengthy learning curve.
How it Works
The Scalable system adds a simple, low-cost 3D camera in a protective box to the robot end-of-arm tooling. The Scalable touchscreen interface guides the welder through simple steps: Scan, Teach, Validate and Tune.
The welder first helps the robot develop a good model of the part by simply pushing the Scan button. The robot then moves over the weld area with its 3D camera open and automatically creates a model of the part. The welder does not need to have any CAD of the part or even knowledge of how to use CAD. The welder then teaches the robot where he/she wants the welds by pointing the handheld teaching stylus where they want the approach, weld path and depart points. The user then makes sure the robot can reach all the points by pushing the Validate button on the interface. The welder can choose whether they want to make any changes to the automatically generated program, and once they are happy with the path and torch angles, they send the program to the real robot.
Any robot programming process requires some fine tuning to make the path perfect. With arc welding, the generally accepted rule-of-thumb is that the weld wire tip must be within half of a wire width of the ideal path of the seam to be welded. The Scalable system makes that easy with its Auto Tuning feature. Because the system knows the geometry of the part and where the weld is, it can automatically create search paths that use touch sense with the weld wire to accurately locate the part surfaces. It then places the torch tip in the ideal position for that weld type, and then gives the welder an opportunity to make any changes if needed based on experience.
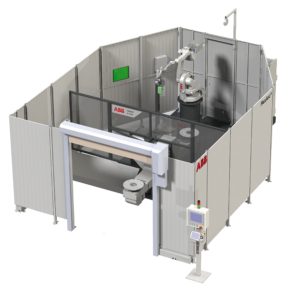
Often a weld path will have some uniqueness, for example, one side of the metal may be thicker than the other, which would require the path to be biased slightly toward the thicker metal to even out the heat and ensure good penetration. In the Scalable interface on the robot teach pendant, the welder can make all the necessary adjustments in an intuitive way without knowledge of robot coordinate systems, just by tapping buttons with simple labels like ‘left’ and ‘right’ to adjust a point in the weld seam.
The welder can then repeat the teach, validate, and tune steps to create as many weld seams as needed to finish the part and make a whole part program. And if repeatable fixturing is being used, the system is now ready to run production. If the fixturing is not repeatable, Scalable’s system can be configured to automatically adapt to variations.
Solutions for the three last barriers of entry into robotic welding
The advantages of the Scalable Robotics programming system are:
- For welders, training time goes from weeks to hours, and no new skills are needed.
- For part programming, the time is reduced from days to minutes and no CAD is ever needed.
- For fixturing, in cases where increased part tolerance is acceptable, the system can do a production time tune, and detect where the seam actually is before welding it, thus allowing for lower cost, more adaptable fixtures.
- Additionally, compared to other systems, the much lower complexity, lower cost, and additional flexibility of a Scalable Robotics system is clear. The single, low cost, well protected 3D vision sensor coupled with robot motion generates a 3D model that lets the robot understand the geometry of the part. By using the welder to show the robot where to weld, the system captures the welder’s knowledge and experience with the parts they normally hand weld, thus ensuring a good outcome at a lower cost. www.scalablerobotics.ai