Nano-joints Offer Enormous Potential in Laser-Cutting Processes
Nano-joint technology allows fabricators to keep small parts securely attached to the nest without a hard tab that is difficult to break or requires clean up.
Posted: February 22, 2022
THE CUTTING EDGE
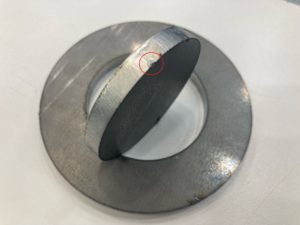
These days solid-state laser cutting machines have moved from the realm of “cutting-edge technology” to “bread and butter workhorse.” Since the introduction of the current generation of solid-state laser sources to cutting machines a little over a decade ago, this technology has proliferated to the point where most fabrication shops in the United States have at least one solid-state laser cutter on the floor. And because of the increased processing speeds that this technology brings when compared to older CO2 laser technology, most of these fabrication shops have found themselves with an increase in cutting capacity as a result.
For the most part this is a big benefit to factory productivity, but the increase in cutting throughput also creates challenges. Downstream operations like bending, welding, and finishing may suddenly become bottlenecked. Additionally, the pace of material handling and factory logistics needs to increase to support the added working speed of the laser.
One result of this situation is an increased investment in automation for material handling. Unlike in the past when the large majority of laser cutting machines were installed without any sort of automatic material handling, now the majority of new laser cutting systems are being purchased with loading and unloading automation included. The number of laser-cutting machines connected to material storage systems has also been steadily increasing as a result of the increase in cutting productivity of solid-state lasers. The upshot of this is that fabricators are gaining output in their cutting processes, but they also must learn how to work with automation efficiently if they haven’t done so before.
One of the biggest new tricks that fabricators must learn if they are adopting cutting automation for the first time is how to make that automatic unloading process for cut sheets reliable. Removing nests of cut metal parts with automation is obviously a bit different than doing it by hand. Whereas people are good at managing a little bit of randomness in their tasks, mechanical devices don’t have this flexibility and require things to happen in a consistent way.
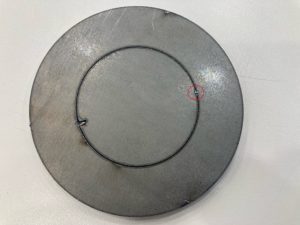
For example, problems with automatic unloading can arise when fabricators cut small parts, in the range of a few inches across or smaller. Due to the way laser-cutting machines operate, the worktable where the cutting process occurs needs to be minimal in terms of surface area so as not to interfere with the melting and ejection of metal during cutting. This is the reason that manufacturers of laser-cutting machines use steel slats to support the material being processed; these slats are easy to replace for fabricators as they become worn out, but more importantly the steel slats can support the parts and sheet being processed without needing much surface in contact with the bottom of the sheet. This minimal support structure of the worktable allows for rapid and high-quality cutting to occur but introduces a challenge for those small parts. Because there isn’t much support holding them up, small parts can tend to tip over and fall out of the nest, possibly getting hung-up in a vertical position.
Parts like these are a big problem for automatic unloading automation, which depends on the processed sheets coming out of the machine being relatively flat. When there are parts or sections of scrap sticking up or hanging down from the nest, this can cause a collision with the unloading device, potentially resulting in equipment downtime or scrapped parts. Clearly, if you want your laser machine running at full capacity, this isn’t something we can allow to happen!
The Advantages of Nano-joints
Fabricators accustomed to working with unloading automation know the standard technique for managing this issue: Leave the small parts connected to the scrap skeleton by a small amount of uncut material, called a “micro-tab” or “micro-joint,” which allows them to stay flat instead of tipping, and facilitates reliable automatic unloading. Even though this method enables automatic material handling, micro-joints come with some disadvantages. They add additional labor to the process of separating cut parts and scrap because now someone must break the micro-joints to free the part from the nest, instead of simply picking them up. The small tab also leaves a bit of excess material on the outer edge of the part; for most applications this is not acceptable, and this bit of extra material needs to be ground or filed away to make the part usable, adding more labor time and consumable cost (in the form of grinding media) to the production process.
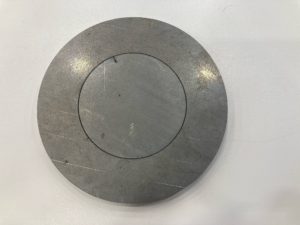
Fortunately, there is encouraging news that this problem might be alleviated through technology. A promising new laser cutting process, referred to as “nano-joint” technology, allows for the possibility of keeping those small parts securely attached to the nest without a hard tab that is difficult to break or requires clean up. Instead of stopping the cutting process completely and leaving a solid piece of material to hold the part in place, nano-joint technology works by ramping down the power output of the laser source on the fly during cutting to leave just a small amount of material connecting the part to the scrap skeleton along the bottom edge. A nano-joint tab leaves only about 30 percent of the material thickness on the bottom edge, and the top edge of the finished part is cut completely free.
This technique creates several advantages over conventional tabbing strategies. First, it makes removal of the tabbed parts much faster and easier, decreasing the labor requirement to get cut parts separated and sent on to downstream operations. It also leaves much less excess material on the cut edge, resulting in a reduction in the need for grinding and filing. Depending on the material type and application, the nano-joint may not require any clean up at all. Lastly, because making nano-joints does not interrupt the laser cutting process, a part can have multiple nano-joints to hold it in place without the need to stop the cut and pierce the material again. Nano-joints can even be used on a common-line cut edge between two finished parts, something that is impossible with conventional micro-joints, so it even has the potential to improve material yield in some cases.
For such a simple idea, nano-joints have enormous potential to make automated laser cutting much easier and more economical. Due to the nature of the process, this technique is currently limited to medium-thickness materials. Very thin materials are more difficult to nano-joint because of how quickly the material vaporizes during cutting. Nonetheless, for fabricators looking for ways to manage the increased cutting throughput of a new laser machine, this strategy makes it possible to improve speed and ease of use without any drawbacks.