The Role of Assist Gases in Laser-Cutting Applications
There are variables that impact your assist gas choice. As the use of compressed air as an assist gas in laser cutting continues to increase, fabricators need to understand which gas is best for which application.
Posted: February 23, 2022
Over the past years, the laser-cutting market has continued to evolve with higher power lasers capable of faster cutting speeds. As these laser powers go up, so does the gas consumption required to accommodate the increased feed rate. Luckily, there have been significant improvements in both the speed and quality of laser cutting using high pressure, zero grade air (also known as compressed air), which is a blend of other gases, including nitrogen and oxygen.
As the use of compressed air as an assist gas in laser cutting continues to grow, it’s important that fabricators understand which gas is best suited to each application in order to optimize productivity and quality. Deciding on which type of gas to use requires balancing processing speed, edge requirements and cost of operation. Below are some basic guidelines.
Which Gas for Which Application?
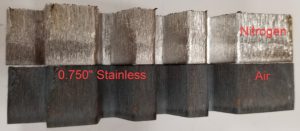
Power level is the biggest determinator of which gas should be used with different material types.
Aluminum: For fabricators processing aluminum parts, compressed air should absolutely be a consideration. In aluminum applications, air greatly reduces burr on the material, results in a smoother edge quality and delivers up to a 150% increase in speed (on 1/8” thick AL).
Oxygen or nitrogen can also be used with aluminum, but both are prone to produce more dross or edge oxidation. Additionally, nitrogen comes at a higher cost while offering no speed advantage.
Stainless: With stainless materials, nitrogen continues to be the best processing method with the purity of the gas dictating the edge quality. Though compressed air will cut stainless, it leaves a blackened edge due to the 21% oxygen content contained in air, so the use of air depends on the desired end result.
Mild Steel: As for mild steel, this is where there is the most variety of assist gas choice depending upon the laser power level. Air is the lowest cost and provides comparable cutting speeds to nitrogen. However, power levels will limit the thickness at which air can be used (up to 1/8” at 3kW or ¼” at 6kW and above). Additionally, air leaves an impregnated oxygen layer in the material that may affect some powder coating treatments. On the other hand, it’s less likely than oxygen to affect the painting process.
Oxygen is low cost and can be used on virtually any thickness level your laser power dictates (up to ¾” thick at 3kW and 1” at 4kW and higher). Unfortunately, the exothermic reaction of oxygen results in much slower speeds than nitrogen on thinner materials (up to ¼” at 3kW and 3/8” 6kW and higher).
Additionally, all oxygen cuts leave an oxidized edge that normally needs cleaning off before powder coating to prevent paint chipping. Nitrogen is used for faster speeds in ¼” and under and leaves a completely clean edge that shows no reaction to paint or powder coating, making it the universal “best case” gas to use for gage materials.
Troubleshooting Assist Gas Usage
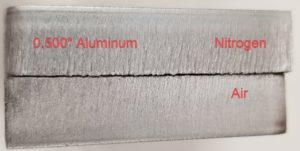
The biggest influencers on cutting performance with air or nitrogen include focus, gas delivery and speed. Gas can affect the cut in that too little gas will not push the molten material out of the cut, so the cut does not go all the way through the material (or possibly refills the bottom of the cut with oxygen). On the other hand, too much gas can cause excess dross (slag) to reconnect to the material as the process will then cool too fast (before the molten material can separate from the cut) or will cause excessive gouging in the cut surface (in the case of oxygen).
Additionally, the purity of the gas is critical to the cutting process. This responsibility lies with the supplier and/or facilities management to ensure the gases are at the high purity levels required for quality cutting. Using lower than recommended purity of gases will lead to darkened edges (in stainless cutting), an inability to cut thick materials (with oxygen assist gas) and/or the inability to reach listed speeds, regardless of the gas.
In addition to the factors discussed here, there can be numerous other variables that affect your assist gas choice. When in doubt, fabricators should consult with the equipment manufacturer for further direction.