How Advances in Aluminum Component Machining Support the Shift to EVs
Commentary from Sandvik Coromant notes how selecting tools made from advanced materials better assists in machining aluminum.
Posted: May 2, 2022
According to a report by the International Transport Forum, global transport activity is expected to double by 2050 compared to 2015 levels. With climate change a global concern, it’s important that we produce more efficient vehicles that run on greener fuels. Material choice and innovations in metal cutting are supporting the transition to more environmentally friendly vehicles.
While COVID-19 caused a short-term reduction in transport activity, vehicle use is still set to rise over the coming decades as the global population increases and economic development continues. Producing more vehicles to meet increasing demand is inevitable — the real challenge is making them greener. The International Energy Agency (IEA) reports that transport already accounts for 24% of direct CO2 emissions from fuel combustion, with road vehicles accounting for nearly three-quarters of this figure.
The United Nations Framework Convention on Climate Change (UNFCCC) recognizes the importance of lowering the transport sector’s emissions and thus released its Climate Action Pathway for transport earlier in 2021. The UNFCCC’s vision is that, by 2050, passenger and freight transport will be completely decarbonized following a shift to more sustainable vehicle technologies. This shift is broken down into transitioning to zero-emission modes of transport and increasing vehicle efficiency.
The EV evolution
Among zero-emission modes of transport are electric vehicles (EVs), which executive director at the IEA, Fatih Birol, says, “have an indispensable role to play in reaching net-zero emissions worldwide.” By using electricity, specially from sustainable sources, from the grid to recharge batteries that power an electric motor, EVs produce zero tailpipe emissions and are thus a more environmentally friendly option than internal combustion engine (ICE) vehicles.
According to the IEA’s Global EV Outlook 2021 report, there were ten million electric cars on the world’s roads at the end of 2020, and EV registrations increased by 41% that year. While EVs are clearly on the rise, their adoption can be accelerated further by overcoming range anxiety, the fear that the vehicle has insufficient range to reach its destination.
And range is not just the responsibility of the battery. In addition to a more robust charging infrastructure and improvements to EV battery design, every element of a vehicle needs to be made lighter. An EV with a lower weight requires less energy to travel a given distance and can therefore go further on a single charge, increasing its range.
Aluminum plays a large role in the light-weighting of EVs, weighing just a fraction of the more traditional automotive materials of choice — steel or cast irons. In fact, aluminum is now commonly selected for a range of vehicle parts, such as the chassis, internal panels, motor housing and battery enclosures. According to the Aluminum Transport Group (ATG), using aluminum to reduce an EV’s weight can result in range gains of approximately the same proportion. For instance, if the vehicle weight is reduced by 20%, the vehicle should be able to travel around 20% further on the same charge.
Mastering machining
However, components made from aluminum are notoriously more difficult to machine. Aluminum is softer than most metals, which can make it challenging to work with. What’s more, the melting point of stainless steel is 1510 degrees Celsius, whereas for aluminum it’s 660 degrees Celsius. When machining the metal, the lower melting temperature of aluminum means that chips can build up from the heat of friction at high speeds and adhere to the tool. This chip accumulation can dull the tool, making it difficult to cut through the billet. In addition, manufacturers can face issues such as time-consuming tool setups, inconsistent tool wear, burr formation and inferior surface finishes. The need for high speeds is also a struggle.
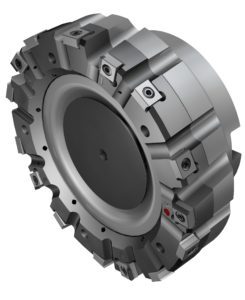
Fortunately, these challenges can be overcome by selecting a tool with an optimized design that’s made from advanced materials. For instance, the Sandvik Coromant M5C90 face milling tool, part of its M5 cutter series, was designed for solid aluminum parts with long milling operations, as well as for roughing and finishing cylinder heads, blocks and electric car components. In just one efficient operation, the M5C90 can perform the entire machining process, from roughing to finishing. In many cases, this can be with a depth of cut of up to four millimeters. This tool can increase tool life by fivefold and reduce cycle time by up to 200%.
In addition, the M5 cutter series features step technology, where its extremely hard-wearing polycrystalline diamond (PCD) inserts are arranged in a spiral and staggered vertically to remove material from the workpiece, both axially and radially. Furthermore, the last tooth has wiper geometry to further ensure a high-quality, flat-surface finish. The wiper cutting edge remains in a fixed position, which eliminates the need for time-consuming setups. Other tools in the M5 series include the M5B90 face milling cutter concept for fine finishing and the M5F90 combination milling cutter for roughing and finishing in smaller dimensions.
The transition to EVs will lower transport emissions, and adoption can be accelerated by increasing their efficiency. EVs that take advantage of aluminum components can travel further per charge, helping to overcome range anxiety. Automotive manufacturers who select machining tools optimized for aluminum will be able to produce high-quality aluminum EV components ― helping to support the shift to greener travel.