Mitigating Hazards with Robots
Embrace robots to enhance worker safety and increase worker satisfaction in order to achieve greater overall productivity, boosting return on investment.
Posted: June 15, 2022

Meeting lean manufacturing initiatives, takt time requirements and more, manufacturers are realizing the benefits that high-performance robots can bring to current production spaces, and a wide range of tasks are being achieved with greater ease, efficiency and safety. While the ability to complete dull, dirty and difficult tasks for greater ease and product throughput may be an occupational preference, performing jobs via robots to mitigate the safety risks from dangerous applications is a necessity that should not be overlooked.
With ever-improving arm flexibility, axis speeds, device connectivity, interface usability, computational power and more, robots are equipped to tackle more risk-intensive tasks than ever. This is good news – as most industries are facing labor shortages and workers are being pushed to be more productive, causing fatigue and contributing to U.S. businesses spending more than $56 billion a year on serious, nonfatal workplace injuries, including:
Overexertion Risks
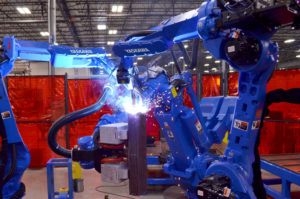
Often induced by the strenuous handling of heavy objects without proper equipment or sufficient breaks, overexertion can involve conditions such as strains, sprains and tendonitis. Accounting for a total cost of $13.30 billion annually, these ailments can be significantly alleviated with robotic automation. For example, many serious workplace injuries of this nature take place during heavy-duty palletizing, component assembly, press tending, warehouse picking and other pick and place tasks. These are all applications that robots excel at completing, and their use is strongly suggested to protect workers and optimize productivity.
Heavy-duty palletizing for end-of-line or distribution operations is back-breaking work. Ideal for moving large, unbalanced loads — including bags, boxes and containers to fully load pallets — performance-driven robots that offer a large work envelope, parallel-link construction, heavy-duty bearings and high moment of inertia ratings are exceptionally suited for this task. Where frequent yet safe human-robot interaction is needed, higher payload and longer reach collaborative robots made with cast aluminum construction for industrial durability may be used. Based on the outcome of a thorough risk assessment, cobots featuring Power and Force Limiting (PFL) can protect workers from potentially harmful contact situations, while facilitating smooth production.
Component assembly demands extreme speed and precision to perform tasks like nailing, screwing and stacking. Unfortunately for human workers, this type of repetitive work is not only very dull and tedious, but it can cause stress injuries on ligaments, muscles and more. Helping manufacturers across various industries to prevent common ailments like carpal tunnel, extremely fast yet compact robots like SCARA (Selective Compliance Articulated Robot Arm) robots are being used. Easily placed next to or inside machine assemblies these robots, as well as other small footprint slim-body models, are optimizing operations while protecting workers.
Press tending is a fast application that fosters an inherently dangerous environment for even well-trained employees. Even small presses can cause immediate and serious injury. Outside of injury by the press itself, high throughput demands put human workers at risk for repetitive injury, and the presence of metal parts with sharp edges presents other serious risks. A wide range of robot models, various mounting configurations and versatile options provide the flexibility needed to accommodate exact press tending requirements, including die changes. Paramount for press tending success is a durable handling robot with higher vibration ratings that can tolerate tough conditions for high duty cycles.
Warehouse picking can make or break production operations. As consumers demand faster, more accurate order fulfillment, manufacturers that heavily rely on human workers are struggling to keep pace — as this labor-intensive task is highly repetitive and taxing as workers strive to reach aggressive productivity targets to meet demand. Sophisticated vision and sensor technology combined with advances in artificial intelligence (AI) and machine learning continue to revolutionize this application, freeing workers to complete higher value-added tasks. From flexible industrial robots to highly adaptable and portable autonomous mobile robots (AMRs), a range of solutions exist to accommodate various budgets and requirements.
Pick and place tasks are frequently met head-on via robotic automation across the industrial landscape to move a part or product from one location to another with pinpoint accuracy. Typically relegated to repetitive and monotonous tasks that have the potential to cause ergonomic issues, the use of high-speed pick and place robots can eliminate worker fatigue and alleviate workflow interruptions. From 4-axis SCARA robots to 6-axis handling robots, a variety of options exists to suit application needs.
Falling Hazards
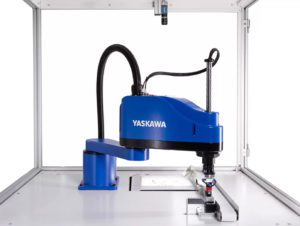
Ranking second and third, respectively, for the most disabling workplace injuries are falls on the same level and falls to a lower level — with the former accounting for $10.58 billion (18.1%) annually and the latter costing $6.26 billion a year (10.7%). Often causing sprains, broken bones, as well as knee, hip and spinal injuries caused by tripping on cables, tracks, parts and slippery surfaces, falls on the same level can occur with dirty tasks such as welding and painting. Bad production workflow may also contribute. Similarly, falls to a lower level are frequently responsible for serious sprains, broken bones, concussions and paralysis, which can result from falling off stairwells, balconies, ladders or other machinery during multiple activities, including part changeover. Thankfully, robots can help mitigate hazards for these applications, while optimizing factory floorspace.
Welding risks are usually associated with UV exposure or toxic fumes. However, they frequently include stumbling over heavy parts, falling from ladders or low risers, as well as tripping on cables. Whether spot welding or arc welding, the proper 6- or 7-axis robot with the right reach, payload and mix of peripherals offers tangible benefits. A robot cell with cable management is suggested to reduce tripping, while the use of robots with safeguarding, in general, can protect workers from other harmful situations like weld fumes and spatter.
Painting and coating are applications that demand extreme precision. Whether a stationary part or a workpiece moving quickly via a conveyor, achieving a smooth, consistent finish with the utmost safety is paramount. Large hollow-wrist robots prevent utility interference and tripping hazards, and Factory Mutual approved (FM-approved) robots for use in Class I, Division 1 hazardous environments with intrinsically safe programming pendants enable safe working environments. Similarly, robot usage eliminates ergonomic strain on workers from repetitive motion, and it removes workers from being exposed to dangerous fumes.
Changeover for large parts can be streamlined with handling robots, eliminating multiple dangerous scenarios such as employees falling from ladders or heavy workpieces falling from cranes. Extended reach, heavy-payload robots are especially ideal for jigless applications, where a robot positions a part for processing by other robots or two robots handle a single part.
Other Factors
Rounding out the top five nonfatal workplace injuries are being hit by objects, accounting for $5.61 billion a year (9.6%), followed by other exertions or body reactions at $4.7 billion annually. From bruises and breaks to concussions, spinal injuries and more, these conditions are most common in factories and on construction sites.
Next Steps
Proactive companies that embrace robotic technology to enhance worker safety for risk mitigation will most likely experience increased worker satisfaction for greater overall productivity, boosting return on investment. Decision makers looking to implement robots should contact an experienced robot supplier or integrator to perform a thorough plant audit and only accept equipment with a risk assessment. This will help answer any questions relating to OSHA, ISO or other relevant standards that must be met to deem an application as “safe,” and it will also address potential workflow bottlenecks, allowing for steadier part flow.
Subscribe to learn the latest in manufacturing.