Non-woven Abrasives Optimize Finishing while Reducing Grinding Steps, Increasing Productivity
Modern abrasive grains and stronger bonding methods found in the latest non-woven abrasives enable shops to quickly achieve desired surface quality.
Posted: August 24, 2022
SURFACE CONDITIONING
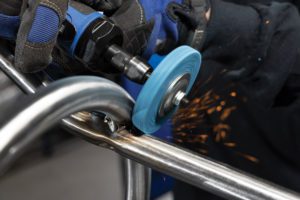
When improving the finish of welded fabricated parts, or blending the forging lines of casted components, both of these processes almost always require multiple steps. First, it is important to identify the surface finish requirement. Some parts will only require a visual inspection, but because there is subjectivity in this type of inspection it is best to perform finish inspections using a device called a profilometer. A profilometer measures the depth of a scratch within the material. A higher Ra means there is a deeper scratch or worse finish. A lower Ra means a smaller scratch, and therefore a better finish. A welded component may have an Ra as high as 100, whereas a forged or molded part can be lower. But typically, most customers want an Ra somewhere in the range of 5 (almost mirror image) to about 20. Improving the finish from 100 to 20 consists of using a finishing sequence of abrasive products starting with coarser (larger abrasive sizes) to finer (smaller abrasive sizes) grit sizes.
The first abrasives application step is the most critical, as it will determine how much work is required to reach the required finish on a weld or when blending a mold line. Historically, manufacturers have used a grinding wheel for this first step. In doing so, excessive scratches on the part may result, requiring additional steps to improve the finish. Having the skills and experience to apply the grinding wheel optimally as well as selecting the best one for the application at hand will certainly maximize results. However, using a grinding wheel that is too coarse when removing parting lines on castings, or during blending and finishing operations on welded products can change the part geometry or size, or result in having to scrap the workpiece for being out of dimensional tolerance. To reduce this risk, select a softer, finer wheel such as the new Norton non-woven Vortex coarse grit wheel.
Non-Woven Abrasives Advantages
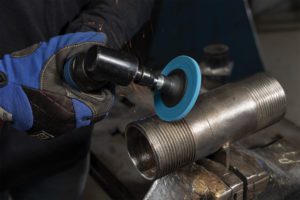
Improving the finish of welded, machined and casted materials has now become easier with the development of new non-woven Vortex coarse grit abrasives technology that reduces finishing steps and saves time and costs, while improving quality and reducing scrap rates. The conformable fiber matrix of non-woven products allows the abrasive particles to uniformly contact and “polish” the workpiece surface, which eliminates heavy cutting which can lead to damage. For example, the relatively non-aggressive nature of a non-woven product combined with the Vortex patented grain results in a good cut rate, while improving surface finish in one step. This technology also helps eliminate inconsistent part quality that can occur from one operator to another. Having measurable CTQ (Critical To Quality) steps, such as Ra requirements and dimensional tolerance that can easily be repeated and maintained when using non-woven abrasives, helps improve efficiency and reduces manufacturing time.
Traditionally, non–woven abrasives were only thought of as a fine grit finishing product, but new more capable and productive abrasives have come on the scene. With new Vortex coarse grit offerings, the advantages of a higher cut rate and improved finishes are achieved at the same time. By using modern abrasive grains and stronger bonding methods found in the latest non-woven abrasives, shops can often reduce the number of steps needed to achieve the desired surface quality. This helps cut labor time, abrasives inventory, and especially reduces operator fatigue when right angle grinding.
For example, the non-woven abrasive coarse grit technology can remove a weld or parting line that is 100 Ra down to 70 in one step. This non-woven abrasive has two significant advantages — it is more likely to maintain the part’s dimensional tolerance, and it will not create a deep scratch that will require additional steps to improve. The second step in this example is a Vortex medium grit which can improve the Ra from 70 to 30. With just two steps, you have completed what historically would have taken five or six operations. If a better finish than 30 Ra is required, the Norton Rapid Blend NEX wheel can be applied. Finally, if a mirror (5 Ra) finish is the goal, use a fourth step with the Norton Rapid Polish felt disc. Some customers use a compound stick with the Rapid Polish wheel in order to decrease the heat and assist in polishing to a bright sheen.
Refer to this video1 to see an example of the Vortex technology. The video illustrates how to deburr and finish in one step with Rapid Blend non-woven depressed center discs, helping to finish the job faster.
Steps may vary slightly by operator experience and/or the condition of the equipment. To minimize steps and improve repeatability of quality, an automated process can be applied.
Automate
Offhand grinding is a term used for decades. Some refer to it as RAG (right angle grinding) but in lay terms it is simply applying a portable grinding machine to a workpiece to improve finish. A portable grinder can be operator applied but can also be used in robotic applications. Saint-Gobain Abrasives has recently introduced the Norton Abrasive Process Solutions (APS) Program, designed to educate customers on how to transform manual operations to robotic. APS services encompass the testing and optimization of new abrasives, improving quality and/or throughput, and trying entirely new and customized processes. The overall customer experience can expect an array of services, ranging from determining optimal grinding or finishing solution, off-hand or automated, and for metal fabrication, production grinding and virtually any abrasives operation. For more information visit nortonsga.us/aps.
End Note: 1“How To Deburr & Finish in One Step with Norton Vortex Rapid Blend” – YouTube
Subscribe to learn the latest in manufacturing.