Siemens: Totally Integrated Platforms Pave the Road Toward Digitalization
Siemens breaks barriers and offers platforms and tools to ensure machine builders and end users move forward with the digitalization of their facilities.
Posted: August 24, 2022
SUPPLIER PROFILE
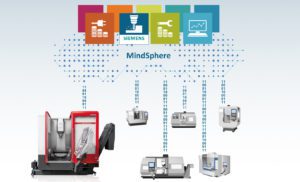
While there is so much uncertainty in the economy, not only in the United States but globally, one area that continues at a healthy rate of growth and implementation is the digitalization taking place in the manufacturing sector. For instance, orders of manufacturing technology dipped slightly in May 2022 to $441.2 million, according to a report by AMT – The Association For Manufacturing Technology; however, year-to-date orders reached $2.42 billion, a 20% increase above 2021’s orders through May.
Manufacturers continue to embrace the advantages and benefits of automating and digitizing their machines and processes, particularly in a tight labor market when workers are hard to find. Automation and digitalization leaders such as Siemens ensure customers have the all-encompassing platforms that enable them to integrate the physical and digital worlds so they can innovate and grow.
For Siemens, it’s Totally Integrated Automation (TIA) system, which has been around for decades, offers full seamlessly combined integration of hardware, software and services. It is a platform for both engineering and maintenance. According to the Siemens website, with TIA, information flows both horizontally and vertically. New technologies are integrated into TIA step by step. The result is added value, regardless of which phase of automation or which level of digitalization a company has achieved.
These tools enable manufacturers to create efficiencies and overcome machine tool builders’ and end users’ greatest challenges. “At the end of the day, the technology that we bring to market is really meant to increase manufacturing activity and accelerate a manufacturer’s business or business growth,” said John Meyer, marketing communications manager for Siemens Industry, Inc.
The Keyword is “Platform”
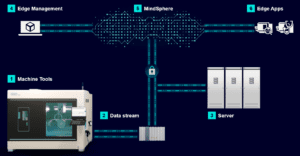
The Machine Tool Systems Business of Siemens offers an integrated platform with several products such as the SINUMERIK CNC platform. Other product lines include SINAMICS Drive Software to drive the motors, and SIMOTICS Motion Control Motors to move machines, as examples.
Siemens Machine Tool Systems offers two key products: the SINUMERIK CNC, which is the CNC controller; and software that enables engineers to build machines, as well as for end-users to monitor machines and collect data to optimize the machines, noted Tiansu Jing, product manager for Siemens’ SINUMERIK CNC Systems and Digitalization Solutions in the United States. The software can be utilized either through MindSphere, the Siemens’ cloud-based operating system, or from the SINUMERIK Integrate platform if users are unable to access the internet.
The SINUMERIK controller is for machine tools such as standard turning and milling machines, Jing said, as well as for fabrication customers such as those involved in laser, waterjet and plasma. “And, we also include those new machine types like robotic and additive, which can utilize our CNC capability in the motion control part,” Jing said.
Jing pointed out that some of the Siemens’ customers produce complicated solutions and need not only CNC, but also PLC and sensors in their processes. As such, a single platform for engineering saves machine builders from having to learn different products to achieve their goals. “It is the same for end-customers — they do not need to handle different solutions from different suppliers — it is just one [platform],” Jing said.
A Forward-Looking CNC
Jing said that through MindSphere, Siemens offers apps for end-users, not only those who use SINUMERIK, but also PLC controllers. “They can use the Siemens apps to monitor the machine to optimize their process,” Jing said. Siemens’ partners also offer apps in MindSphere to provide value-added services to customers.
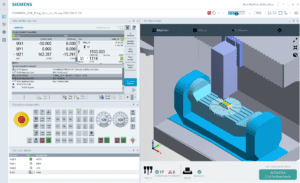
Digitalization is something “we can see and feel now,” Jing said. “Within the SINUMERIK CNC line, we talk about hardware, and we talk about software, and there is one important product connecting our hardware and software which can bring immediate benefit to machine builders and end-customers — and that is the digital twin.
From the Siemens’ point of view, the digital twin is not hardware or software,” Jing continued. A digital twin allows the simulation of machines prior to manufacturing, which saves time for both the machine builder and the end-user.
“A digital twin cannot work without a combination between hardware and software,” Jing said. What Siemens has done, specifically, for the digital twin, is in 2019 we released our first digital-native CNC called SINUMERIK ONE, which is the flagship of our CNC family in the market that is used for all machine tools, including fabrication machines.” SINUMERIK ONE is a forward-looking CNC, which is a driver in the digital transformation of the machine tool and manufacturing industry.
The controller works with software to create the machine controller and the associated digital twin from a single engineering system, totally integrating the hardware and software. With the seamless interaction between the virtual and real worlds, including the PLC, motor and drive hardware, SINUMERIK ONE has set new standards in productivity, performance and digitalization.
Jing said that together with SINUMERIK ONE, Siemens has created software, Create MyVirtual Machine for machine tool builders, and Run MyVirtual Machine for machine users. Create MyVirtual Machine runs the same NC kernel and PLC as the real SINUMERIK ONE control. “So, Create MyVirtual Machine itself is actually the CNC running in the PC or in the virtual world,” Jing said. It does not simulate the control, because from the point of view of both the machine builder and end –user, they require a digital twin of the machine, not the control.
Jing added that Create MyVirtual Machine connects the virtual CNC system and PLC, with a virtual 3D model of the machine, even with a virtual 3D model of the workpiece that a machine is cutting. It creates a 100 percent duplicate of whatever the user is building in the real world. The benefit of duplication is users can build a successful digital twin with all the good features and the bad features. Whatever fault they had in their hardware design is reflected in their virtual environment, which was not comparable in the past, Jing said.
So, for example, during a simulation of a tool path for a workpiece, in a virtual twin environment, users can see that perhaps they are making too aggressive of a path plan setting in the CNC, and without a real CNC kernel, the user cannot see the difference. Digital twins allow you to see potential collisions. This ensures machine builders can verify their designs and save time. What’s more, end-customers can reuse those designs to save time in repairing their work, Jing pointed out.
Connectivity Solutions
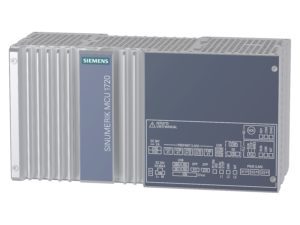
Among the Siemens’ industry leading initiatives are solutions regarding connectivity to support shop-floor management. Jing said there are three main applications: MindSphere, SINUMERIK Integrate and SINUMERIK Edge.
With the cloud-based MindSphere operating system, machine builders can easily connect machines, which can be utilized by end-customers and partners that offer apps to assist users in increasing their productivity by monitoring machines and analyzing the data collected.
When shops are unable to connect to the internet, they can access SINUMERIK Integrate and its series of apps in order to collect data from machines to manage the manufacturing process, for example, when managing a large number of tools. For those larger customers who have hundreds of machines producing hundreds of parts, which require numerous tool changes, communications between programmers and machine operators can be a challenge when it comes to developing production schedules.
“Siemens offers the solution for these kinds of customers that only the right part program will be pushed to the right machine with the right version,” Jing said, but “it also offers the flexibility for machine operators on the front end to optimize the machine and push this change back to the programmer and planner so they can evaluate and implement in future production. This is just an example. There are many other apps to serve these end-customers.”
Finally, with SINUMERIK Edge, customers have a unified solution to extend the productivity of their machines without impacting their current production. In SINUMERIK Edge, Jing said, there are many apps from Siemens and partners based on AI machine learning. “AI machine learning can only bring benefit to our customers by having the machines connected, by having the data of the machines collected,” Jing said.
An Edge box, placed on the side of a CNC machine, quickly collects and processes data. When the data is collected from a SINUMERIK CNC controller, the Edge device has an incomparable computing capability to process vast amounts of data before sending it back to the server, Jing said.
An example of a typical quality check “compares the tool paths and,” Jing said. “It is possible to have a comparable result in a quality check instead of having some laser or mechanical measure to measure the quality of the cutting piece.” In addition to process optimization, another useful application of SINUMERIK Edge regards the predictive maintenance of machines.
Secure Ecosystems and What’s Next?
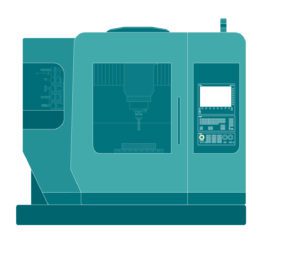
How has Siemens positioned itself in anticipation of industry changes, and what is next in terms of digitalization of the manufacturing sector? The company through its unified platform has enabled the capability and connectivity of machines, as well as the ability to collect and process massive amounts of data about those machines. With SINUMERIK Edge, Siemens is “offering an open and secure platform for end-users and our partners to innovate to introduce those technologies that we know of now, or those we do not know yet,” Jing said.
The data collected helps end-customers further improve productivity and/or reach areas they have not previously achieved. “What Siemens is doing in the short term is to break the barrier there and offer the platform for them,” Jing said.
Whether it is Siemens or other players in the market, companies need to push their latest technologies out to customers so they can implement them. Jing said the key is having the machines connected, having the data collected and utilizing a secure, well-designed platform.
“In the end, the key is this ecosystem from not only Siemens, but also others to offer this benefit to our customers,” Jing said.
Siemens to Present the Digital Machine Shop at IMTS 2022
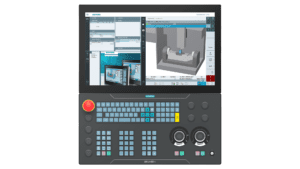
During this year’s International Manufacturing Technology Show (IMTS) in Chicago, September 12-17, Siemens will present its hardware automation and software technology portfolio, highlighted by the first-ever, digital-native CNC platform, SINUMERIK ONE, for machine tool applications. In addition, Siemens will present its solutions and services for the industrialization of additive manufacturing.
The company will be Booths E-133346 (Controls & CAD-CAM Pavilion) and W-433028 (Additive Manufacturing Pavilion), where its experts will highlight how machine users can quickly and easily embark on their digitalization journeys — from part concept to design, digital twin to simulation, part and machine production, as well as total integration of these processes into the digital enterprise for job shops and production departments alike.
Siemens will also highlight Create MyVirtual Machine for machine tool builders and Run MyVirtual Machine for machine users.
Siemens Extends its Portfolio to Fabrication and Additive Manufacturing Industries
The Siemens portfolio of machine control hardware, software and cloud-based services is now available to the fabrication industry. A highlight of the portfolio is the new Siemens SINUMERIK Motion Control (MC) system, an open, industrial PC-based controller with embedded CNC and PLC in a Windows 10 environment. SINUMERIK MC offers machine builders a customizable user interface and powerful motion control for fabrication applications.
In addition, also included in the portfolio are end-to-end solutions for additive manufacturing and digitalization, as well as the SINUMERIK 840D sl CNC for robotic applications.
The company’s Manage MyMachines application, which runs on the cloud-based MindSphere, remotely connects machine builders and end-users as well as Siemens Technical Application Centers. Users can increase the productivity, reliability, and availability of the machines. Connections are easily configured, and machine status, operating mode and program status can be quickly ascertained — no matter where in the world the machine is located.
Regarding the newest developments with the SINUMERIK 840D sl CNC and its Virtual NC Kernel (VNCK), with the SINUMERIK Run MyVNCK, users create their own control-specific virtual world by embedding their original CNC kernel into a virtual machine and then seamlessly integrate it into their normal product development process to optimize their production. In this virtual environment, users can plan, verify and optimize production and avoid programming errors and collisions. The technology can be applied towards OEM applications in laser cutting, waterjet, deburring, bending and more.
www.usa.siemens.com/sinumerik-edge
Subscribe to learn the latest in manufacturing.