Drilling and Milling Solutions Turn Cutting Machines into Multi-Functional Production Centers
Fabricators throughout North America have wider access to some of the industry’s most sought-after cutting equipment.
Posted: October 20, 2022

Fabricators throughout North America have wider access to some of the industry’s most sought-after cutting equipment.
Fabrication processes often require high-precision holes, threads, or countersinks. Whether its flanges, end plates, heat exchanger tube sheets or generally any stress-exposed bolted joints, there are many applications where it is technologically necessary to create the holes by drilling. While there are jobs – especially those with large quantities of holes in a single workpiece or assembly – where using a dedicated boring machine is most efficient, there are also many parts that require just a few holes and perhaps some threads.
Ideally, these parts would be manufactured with a single machining center including cut contours, markings, and machined holes. But, lacking this option, this work is usually done manually, or via a separate mechanized drilling process adding time and cost to the job.
Automating Operations
Integrating technologies into a single multi-functional gantry automates the processes with a single NC program — be it plate, profile, beam, or a pre-welded assembly. This not only includes automated tool exchange, but automatic switching between the technologies. This sets the sequence of operations for each part in advance while considering thermal expansion of material and the ability to set the most efficient process for producing parts with the desired accuracy.
“Input here is the raw semi-product, such as a metal plate loaded on the cutting table,” explained Michal Kováč, MicroStep’s Marketing Manager. “The output is finished parts that can have contours cut with straight edges up to complex bevels [without dross] drilled and countersunk holes, cut threads and laser marked data matrix codes for identification. The parts can then go straight to welding, blasting, or whatever the production process requires next.”
Reducing secondary operations (e.g., no need for deburring or manual grinding of cut holes), eliminates transfer of parts to different workstations streamlines the process saving labor and time. What’s more, investing in one multi-functional machine requires less floor space and eliminates the need to purchase multiple machines to perform the operations.
Drilling, Tapping, Countersinking – Well Tuned and Field Tested
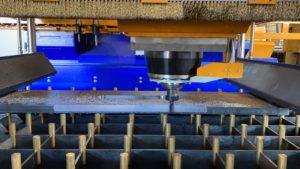
During the past two decades, MicroStep has supplied manufacturers with hundreds of multi-functional machines with drilling capabilities, combining mostly plasma bevel and oxyfuel cutting with machining operations. The solutions include small drills up to Ø 0.50-inch as well as more rigid units with spindle powers 11 kW – 55 kW that cover drill diameters up to Ø 1.18-inch, Ø 1.57-inch and Ø 2.36-inch for drilling up to 3.94-inch-thick plates. Pre-drilling units Ø 0.47-inch for thick oxyfuel piercing up to a 11.81-inch plate thickness are also available. The company’s most popular choice is a 26-kW drill with diameter range Ø 0.16-inch – Ø 1.57-inch, countersinking and tapping up to M33.
The drills come with automatic tool exchange and internal and external cooling of drill bits as well as with damage protection in case of tool breakage. Two incremental sensors in the pressure retainer measure the distance between the plate and the drill to ensure high precision countersinking. The equipment includes automatic drill length calibration (ACDB technology) and supports various drilling cycle types including peck drilling.
Kováč says that MicroStep’s plate processing DS series is a popular solution for heavy-duty drilling operations of flanges, gussets, and end plates. This machine can be equipped for automated operation of loading and unloading, drill chip removal, and brush cleaning of work area.
Milling and Heavy-duty Drilling up to Ø 2.76-inch
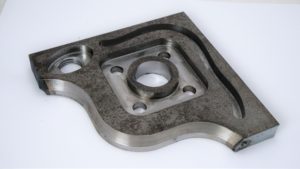
MicroStep’s flagship in machining operations is DRM Max — a heavy-duty CNC cutting, drilling and milling machine with key applications in offshore, wind tower, heavy vessels, columns, reactors, and heavy-duty machinery applications. Its gantry has a rigid double-beam structure with an independent sub-gantry carrying a 55-kW spindle and two powerful retainers that clamp down with 5,395 pound-force each, over a 29.53-inch-wide drilling and milling area.
This robust machine design enables drilling up to Ø 2.76-inch and a variety of milling operations such as large hole milling, face milling, pocket & slot milling, chamfer milling, thread milling or counter boring.
Lasers with Drilling
It’s not only plasma and oxyfuel machines that bring the advantage of multi-functional design, but also MicroStep’s waterjet and fiber laser machines. For the latter, a turret head with 6 tools and automatic drill bit calibration provides drilling up to Ø 0.78-inch, tapping up to M16 and countersinking capabilities while a stronger drill up to Ø 1.18-inch is available for MSF Max laser machines with steady cutting tables (without pallet changers).
The Bottom Line
MicroStep machine tools are represented throughout the North America by United Precision Services (Cincinnati, OH). The company’s national sales manager, John Prevish, said that streamlining and accelerating operations will generate a measurable and sustained return on investment.
“These tools deliver a comprehensive line of drilling, tapping, countersinking, and milling solutions that can be integrated within the same CNC machine, and in many cases even on a single gantry,” said Prevish. “By upgrading to MicroStep, fabricators are making an investment – not just a purchase. Over the past 30 years, the company has developed a wide range of innovative cutting technologies while continually building upon a well-earned reputation for quality and performance. While we’re happy to be partnering with a company like MicroStep, the true beneficiaries are fabricators throughout North America who will now have wider access to some of the industry’s most sought-after cutting equipment.”
www.unitedprecisionservices.com
Subscribe to learn the latest in manufacturing.