FABTECH 2022: Where Innovation Meets Opportunities
FABTECH to Take Place at the Georgia World Congress Center in Atlanta from November 8-10!
Posted: October 1, 2022
Don’t miss the chance to be inspired by industry experts, suppliers and your peers in the metal forming, fabricating, welding and finishing sectors at FABTECH 2022. Attendees can view the latest product and machinery demonstrations, participate in conference sessions — and more — in this all-encompassing event.
FABTECH is North America’s largest metal forming, fabricating, welding and finishing event. At this annual gathering attendees can view the latest machinery and software innovations and find the tools and new solutions that will assist them in improving productivity and increasing profits. Many exhibitors will unveil new or updated machinery or products and services at this event.
FABTECH gives you the tools, technology, and thought leadership to stay ahead of the competition. FABTECH’s leadership expects more than 1,100 exhibitors, and more than 150 conference sessions that include technical, operational, economic and managerial sessions. All sessions are 90 minutes long and are offered in basic, intermediate and advanced levels. Sessions with Tech Tours combine classroom instruction with expert-led guided tours on the show floor to see technology operating in designated booths. The American Welding Society’s programs focus on best practices and new commercial developments in welding and thermal spray.
Fabricating & Metalworking is proud to present the FABTECH 2022 Product Showcase, which is an invaluable guide to navigating the trade show floor at the Georgia World Congress Center this November. The following pages outline products and demonstrations expected to be on display by world-class suppliers in four halls. Pavilions are dedicated to 3D/additive manufacturing; finishing; forming & fabricating; METALFORM; robotics & industrial automation; tube & pipe; welding; and welding automation.
Don’t miss this year’s FABTECH, the only event where you can take in a range of industry activities all in one place.
Venue Information
Georgia World Congress Center
285 Andrew Young International Blvd. NW
Atlanta, GA 30313
Expo Hours
Tuesday, Nov. 8 10 a.m. — 6 p.m.
Wednesday, Nov. 9 9 a.m. — 5 p.m.
Thursday, Nov. 10 9 a.m. — 4 p.m.
Admission
Show floor admission is complimentary if you register before November 4, 2022. After this date and onsite, there is a $50 registration fee.
FORMING & FABRICATING, METALFORM, FINISHING
AMADA Will Pair the REGIUS 3015 AJ 12kW Fiber Laser with the AMS 3015 LL
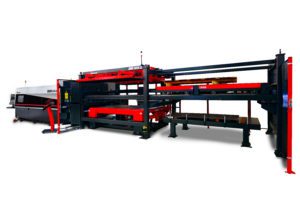
AMADA AMERICA’s (Buena Park, CA) REGIUS 3015 AJ 12kW fiber laser will be paired with AMS 3015 LL (linear loading) automation in Booth B7109. This system combines the world’s fastest 3-axis linear drive system and a variety of autonomous features with the efficient design of the AMS LL.
REGIUS Series Fiber Lasers:
AMADA’s REGIUS Series fiber lasers combine the world’s fastest 3-axis linear drive system with a variety of autonomous features to ensure high-speed, continuous operation. The Laser Integration System (LIS) in the REGIUS consists of a variety of features to significantly reduce setup time and maximize quality. By autonomously monitoring for nozzle condition, pierce penetration, tip ups, and debris on the protection glass, the REGIUS can seamlessly navigate around production issues that may disrupt laser cutting.
This innovative fiber laser series utilizes AMADA’s patented ENSIS technology that’s engineered specifically for manufacturers that laser cut thin-to-thick materials. The lineup for the REGIUS series consists of the 6kW with two 3kW modules, 9kW with three 3kW modules, and 12kW with three 4kW modules.
AMS 3015 LL Automation System:
The AMS 3015 LL is designed for shops requiring a narrower footprint. If your ability to add automation to your laser is limited due to walls, aisle ways, or other equipment, the AMS LL can be a solution by keeping the system roughly the same width as the laser itself. Like all of the AMS systems, the AMS LL is designed and built in the USA and utilizes many of the same components as the other configurations. The simple and efficient design of the AMS LL can greatly increase the overall productivity of your laser without the need for more floor space.
Booth B7109
The HBE-320/523GA at the Leading Edge of Sawing
Behringer Saws (Morgantown, PA) is excited to be presenting the HBE-320/523GA, fully automatic miter saw in Booth B7817. The HBE-320/523GA is a state-of-the-art, dual-column, horizontal band saw. With its standard industrial PC operator’s control, it automatically positions both the material length and required miter rotation with high precision. The PC controls also allow for a wide range of programming, functionality, customer information, and virtually unlimited program storage. With its heavy duty dual-column design and ball screw servo driven technology, the 320/523GA delivers the industry benchmark regarding both length and miter angle tolerances, and repeatability. Length tolerances are +/- .005” or better, and with a miter accuracy of 1/10th of 1 degree, it is truly a precision sawing operation.
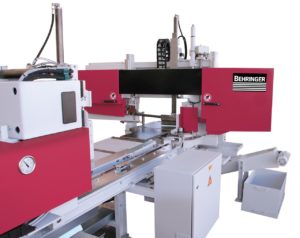
Built with Behringer’s renowned cast iron construction, this machine is very rigid, assuring square and fast cutting performance. The inherent vibration dampening characteristics of the cast iron components also ensures a high-quality finish and long blade life. The independently powered chip brush, precise blade lubricant application, and high blade tension, due to the dual-column design, help the 320/523GA generate excellent chip evacuation, cut quality and squareness.
The HBE-320/523GA has cutting capacities of 20.4” (520 mm) wide by 12.6” (320 mm) high, and miter capacity of 45 degrees right and 60 degrees left (105 degrees total rotation). It also has special miter cutting capabilities such as the ability to do double miter cuts on each end. The standard automatic down feed pressure regulator ensures the optimal in blade chip load, and by self-monitoring the feed rate it delivers long blade life and precision.
Behringer Saws also supplements our machines with any material handling requirements you may have, including non-powered or powered roller conveyors, loading magazines, output sorting units, and many other optional components. Our ability to automate saw operations allows for the greatest possible efficiency and even “lights out” operation.
Finally, like all Behringer Saws, the 320/523GA is supported with outstanding post sale support, including initial machine start up and training, by our team of factory trained field service engineers. In addition, our parts department in Morgantown, Pa., is well positioned with inventory to supply your consumable and replacement part needs over the long lifetime of the saw. Powerful, accurate, and reliable, the HBE-320/523GA is well positioned to be your high premier, high-production fabrication saw.
Booth B7817
BLM Group to Demonstrate the LT7 With Insertion Unit
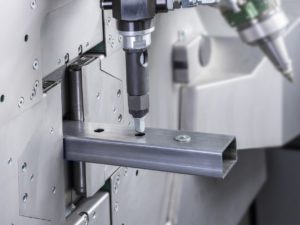
In Booth B7513, BLM GROUP USA (Novi, MI) will be demonstrating its LT7 lasertube with a new thread insert unit, which automatically installs thread inserts into laser cut/drilled holes using press fitting. A simple and widely relied upon joining technique, press fitting relies upon force and friction to hold two components together. A patent-pending technology exclusive to BLM GROUP, this inserter unit simplifies and shortens the processing time required for mating an insert with a tubular component.
The thread insert is an ideal solution for thin wall tubes, which are not sufficient for standard threads, and an ideal partner with the BLM GROUP LT7 machine. The system is capable of handling threaded hexagonal inserts from M4 to M12 with automatic checks to ensure proper insertion. Post-laser cutting, the time to install inserts is only nine-to-11 seconds/insert.
BLM Group’s Artube software makes for easy offline programming accommodation for the insertion process inside the same software for all other part programming. Programming on the machine then takes place automatically, while allowing the operator to maximize production.
Booth B7513
SigmaNEST Will Showcase SigmaSUITE 23
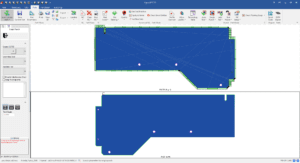
SigmaNEST (Cincinnati, OH), the SMART CAD/CAM nesting software for fast, efficient cutting, routing, punch, and bending will showcase SigmaSUITE 23 in Booth B8621. Visitors to the booth can view the software’s powerful new advances for CAD/CAM nesting automation, new enterprise and ERP functionality, and a full lineup of Connected Shop integrations for streamlined manufacturing.
The SigmaNEST booth will also feature a “Connected Shop Wall” to show the automation of a job as it progresses throughout the shop from quote to invoice, with a seamless closed loop of integrated communication empowering each station and team member. The modular Connected Shop platform includes scheduling, logistics, and ERP/MRP connection informed by nesting intelligence. Managing an efficient workflow is simplified with enhanced SigmaSCHEDULE for nested operations and Load Manager 23 to control production, and with integrated Shop Manager apps for remote control of incoming and outgoing resources.
Debuting in v.23 are three new Connected Shop products – Shop Clock for time keeping, Data Hub for accessing job-related documents, and Quality Manager for maintaining manufacturing excellence. Network security is further enhanced with support for Transport Layer Security 1.2 protocol to authenticate and encrypt data between endpoint devices and applications.
The SimTrans program works more powerfully than ever to allow enterprise control of distributive manufacturing between separate locations. SimTrans now supports Drag and Drop to convert individual CAD files for flexible job management. In addition, an improved diagnostics system makes SimTrans easier to setup and maintain.
Numerous UX enhancements help to simplify CAD/CAM including a new Multiview for Part Mode to split the view into two-to-12 separate windows for programming parts side by side. Further developments for each CAD/CAM software help to elevate nesting for sheet, tube, beams, bending and HVAC components. SigmaCTL cut-to-length software is now fully integrated to allow ERP control to build the order list of parts.
Part of the Sandvik Design and Planning Automation division, SigmaNEST empowers customers in major industry sectors with a machine-agnostic approach, integrated platform, and a worldwide team of product experts.
Booth B8621
Fully Automatic Vertical Tilt-Frame Band Saw is Market Leader
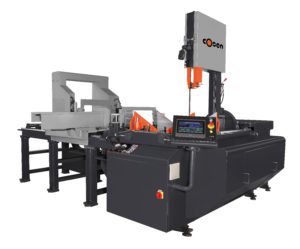
Cosen Saws North America’s (Charlotte, NC) AV-2026NC band saw is one of the best automatic vertical saws on the market right now. Cosen will be in Booth B8629. The AV-2026NC is the perfect saw if you are looking to further integrate automation in your structural steel fabrication business. The AV-2026NC consists of Cosen’s reliable vertical tilt frame saw with an automated feeder. This saw exceeds many of the standard requirements that operators look for in a band saw machine. This makes the AV-2026NC a technologically advanced saw that provides the convenience of allowing operators to push a button and walk away until the job is completed and can run all day long without any issues. With its rigid construction and superior features, Cosen’s AV-2026NC offers precision, efficiency in operation, lower cost per cut, and durability in demanding production environments.
The AV-2026NC features a 20″ x 26″ capacity with an adjustable head cant from 0°-to-5°. Equipped with a 7.5 hp saw blade motor and 1 hp hydraulic motor, the saw is ready to cut through any challenge. The hydraulic tilt-frame head along with 60° left- and right-hand vises makes cutting angles anywhere from 0°-to-60° a breeze. Additional benefits and features of the AV-2026NC include:
- Gearbox designed to accept high lateral pressure with no thermal distortion
- Inverter blade drive system which allows for infinitely variable speeds
- 10″ HMI touchscreen display
- Adjustable flood coolant system
- Motor driven, synchronized wire blade brush
- Carbide blade guides and bearings provide additional blade support
- Rigid cast-iron guide arm
- Hydraulic blade tensioning device
- Cast-iron hydraulic vise
- Save-a-Blade feature
- Computer controlled indexing up to 999″
Booth B8629
New Interactive and Advanced Graphical Display Control for Press Feed Lines
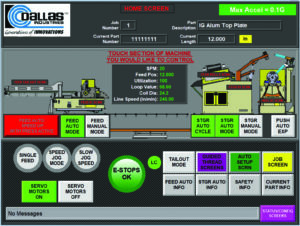
Dallas Industries (Troy, MI) a leading manufacturer of press feeding equipment and controls for the stamping industry will feature a compact feed line and its new interactive and advanced graphical display control for press feed lines in Booth B6007. In a shared booth with AIDA-America, Dallas Industries will exhibit a servo feed, with piloting pull through straightener and powered reel. The feed line will be running material into a fully operational AIDA servo press for a live stamping demonstration.
The 15-inch graphical display is designed to maximize productivity during start up and into production by providing an HMI touch and diagnostic screen for the entire feed line process. The new design features an intuitive and easy to follow graphical format that duplicates the machine in operation. This graphical display can reduce launch and setup time, minimize changeover time and assist production by providing real time diagnostics for the entire machine.
As it relates to the compact feed line, personnel will be on hand to discuss ways to achieve smoother feed motion through ProfileSelect™ software which uses a sinusoidal profile (cam motion), that puts less stress on the material and mechanics. And SyncLoop™ controls that synchronize the feeder/straightener and reel speeds dramatically enhancing the loop’s stability and control to provide for a smoother loop handling.
Dallas Industries’ full line of products includes press feed lines in both conventional and SpaceSaver styles. Also offered are a wide range of sizes and capacities of servo feed, heavy-duty straighteners and coil handling equipment.
Booth B6007
Expand Your Cutting Capabilities with the LC 3 Fiber Laser
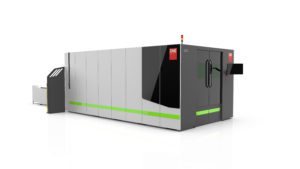
DNE Global (Hoffman Estates, IL) stands for performance laser cutting at an exceptional value. The innovative LC 3 fiber laser cutting machine combines efficiency, speed, and ease of operation with Swiss engineering and state-of-the-art laser cutting technology to deliver all the performance you will need to succeed in the sheet metal processing business at a low investment cost. In addition, with a lower cost per part, job shops can realize increased competitiveness and the ability to expand their services to other markets. DNE Global will be in Booth B8441.
Benefits include:
- Easy to operate and program
- Fast and reliable laser cutting for more profit per part
- Local service support and parts availability – fast response time; proven components
- Attractive price-performance ratio
- State-of-the-art technology based on Swiss expertise
- Powerful laser output of 2kW, 3kW, 4kW and NEW 6kW
The innovative LC 3 fiber laser cutter opens up a broad spectrum of cutting applications for industries ranging from construction and agriculture machinery to mechanical and electrical engineering, shipbuilding, automotive and aerospace. An established sales and service network with local parts sourcing ensures customer satisfaction. Whatever your sheet metal processing needs, we have a solution for you.
Booth B8441
Chip and Parts Conveyors in Variety of Models and Slider Bed Widths
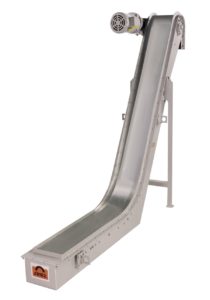
Permanent Magnetic Chip and Parts Conveyors from Eriez® (Erie, PA) safely and reliably move and elevate ferrous materials such as chips, turnings, small parts and stampings. Eriez will be in Booth B7741.
These units are practically maintenance free and innovatively designed to ensure the highest level of operator safety. Four frame sizes are available with four to five standard slider bed widths. For restricted areas under smaller machines, or where a relatively small volume of material is to be moved, the Model 6 — only 6-¼ inches (159 mm) deep — is ideal. For larger areas and greater volumes, the Model 9 conveyor — 9-¼ inches (235 mm) deep — is recommended.
The Model 12, which is 12-¼ inches (311 mm) deep, provides the magnet power and large surface area to continuously remove large quantities of ferrous materials. Where exceptionally large quantities of chips are involved — up to 10 tons per hour — the 21-¼ inch (540 mm) deep Model 21 is the best choice.
Eriez’ Tuf-Trac™ drive system is featured on conveyor models 6, 9 and 12. The drive chain rides in an oil impregnated Ultra High Molecular Weight track, designed to operate quietly and maximize conveyor life. Tuf-Trac eliminates the need for oil inside the conveyor housing.
Besides an externally mounted drive motor, Eriez’ Chip and Parts Conveyors are self-contained, with a conveyor mechanism that is completely enclosed. With a broad assortment of shapes, sizes and options, Eriez’ Chip and Parts Conveyors provide a solution for virtually all application needs and requirements.
Established in 1942, Eriez is a global leader in separation technologies. Our commitment to innovation has positioned us as a driving market force in several key technology areas, including magnetic separation, flotation, metal detection and material handling equipment.
Booth B7741
Form Your Own Inserts
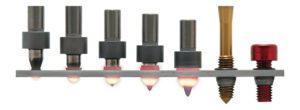
Friction drilling by Formdrill USA (Rolling Meadows, IL) is an easy and cost-effective application to join thin-walled materials and avoid costly weld nuts or inserts. Our drill bits are used to make a hole and create a bushing out of the parent material which increases the area available for tapping. Formdrill USA will be in Booth B8973.
Our tools work with standard equipment like drill presses, milling machines or CNCs. This process is usable in most malleable materials such as mild and stainless steel, aluminum, copper, brass and other high strength alloys. Although this may look like new science, it is a proven technology that has been around for more than 40 years and is used throughout the automotive, furniture, HVAC and other manufacturing industries.
Booth B8973
New Controls for CLOMEA’s Line of Benders
J&S Machine Inc. (Ellsworth, WI) will display the CLOMEA CRMX70 roll bender in Booth B7807. This roll bender features three independently driven drive rolls with five position adjusted shaft distances for bending up to 5-1/2” tube, 2-1/2’ square bars or 3” solid round bar. Adjustable distances between lower roller shafts are from 11-to-37 inches for the best positioning of the rolls for the material type and radius required.
CLOMEA is introducing the newest of controls for the CRMX70 and their line of benders. The machines can be equipped with different controls, from manual to highly technical CNC. One bender can be powered by six different control models allowing a company to purchase a manual control and upgrade to a more powerful control as their needs and capability requirements grow. This allows two models of benders — one pyramid and one double pinch — to use the same control for investment savings.
KAAST to Present Wide Lineup of Fabrication Equipment
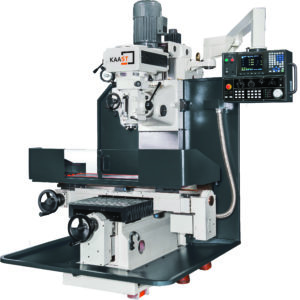
KAAST Machine Tools, Inc. (Aldan, PA) will be bringing at least six different fabrication and forming machine tools to FABTECH. Booth B9329 will feature a PS 65 DP 70-ton Ironworker; HPA-P 100/40 100t x 40” Simple Press Brake; RBD-3M 15/7 5’x0.25” Plate Roller; DMV 230 VS Knee Mill with a 9×49” table; HBS A 230 9” Fully Automatic Band Saw; HBS 360 DGH Dual Mitering 14” Band Saw; and a PBH 65 NC Angle Roller strong enough to bend 1.25” square bar to a 16” diameter circle. Customers are invited to stop by and see these impressive machines in person while at the show.
Booth B9329
New K5200xmc Saves Time on Plasma Cutting, Milling and Drilling
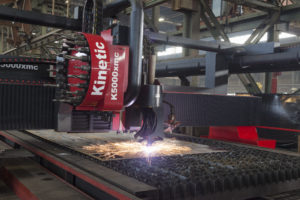
Many fabrication shops and OEMs are forced to maximize every dollar — and every minute — in today’s fast-paced economy. That’s why it is important to invest in a machine that does more than just cut plate.
Kinetic Cutting Systems Inc.’s (West Burlington, IA) K5200xmc all-in-one CNC plasma cutting systems are designed to help businesses maximize profitability and productivity by helping them find ways to boost output, save time and save money. You can see this innovative machine first-hand in Booth B8467.
By combining plasma and oxy-cutting technology with vertical machining functions, this machine can perform multiple processes in a single setup, eliminate moving WIP between stations and reduce labor needs. In fact, these machines can save time from start to finish — and they just might mean the difference between keeping up and getting ahead.
Shops can work faster with multiple processes in a single setup. Kinetic’s K5200xmc with integrated cutting, milling and drilling capabilities eliminates the need to move workpieces from station to station, allowing fabricators to drastically reduce the amount of time and handling it takes to complete a run of parts. In fact, engineering time studies have shown a 95% reduction in time to fabricate a part on Kinetic’s combination machines.
Busy fabricators and OEMs benefit from plasma cutting systems that save time by processing plate faster. With automated part unloading, the Kinetic K5200xmc can unload and organize parts based on a specific part number or work order number. It can also select individual parts from a group nested in a single sheet – and then sort them onto pallets based on different criteria. This automation allows Kinetic plasma cutting systems to cut at one end of the table while unloading the other and produce parts with minimal downtime.
With part marking, cutting, milling, drilling, tapping and more, the K5200xmc can perform multiple fabrication processes in one step and save businesses time and labor. Not only can this machine eliminate or reduce the time and labor needed to move parts for downstream processes, but it can also reduce the manpower needed to clean and service machines, thanks to Kinetic’s automatic chip, dross and waste collection and coolant recycling.
Booth B8467
Tooling Solutions for Punching, Bending and Laser Fabricating
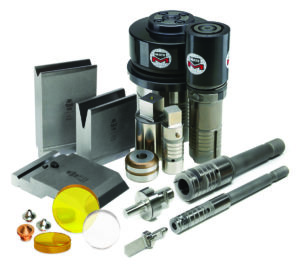
The latest Mate Precision Technologies (Anoka, MN) tooling solutions will be in Booth B7747. Mate sales engineers will demonstrate features and benefits of the full line of solutions from tooling for punching, bending and laser consumables.
Mate American Precision Style press brake tooling offers a full line of precision ground punches and dies featuring the patented Maglock® magnetic safety system.* Attach and seat the punch to the holder with no separation between the surfaces, ideal for front loading of tooling. Purchase by the inch to buy the length required by the part design.
Mate QCT™ thick turret tooling takes insert-style punching systems to a whole new level. The tool-less punch retention mechanism makes changing the punch insert a breeze: flip the durable latch to remove and snap the new insert into place. It’s that easy. No tools to use, break or lose to change the punch insert. QCT’s durable design is designed to minimize effort and maximize uptime.
What’s more, Mate has added new laser accessory products reaffirming its commitment to the rapidly growing fiber and CO2 laser market. Newly included are fiber lenses, fiber windows, nozzles and accessories for Eagle, IPG, Phoenix, Piranha and other lasers.
*The Maglock press brake tool retention system is protected under U.S. patent 11,383,284.
Booth B7747
Laser Cutting Machine Offers High Power and Maximum Control
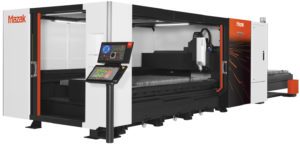
Mazak Optonics Corp. (Elgin, IL) has released the next generation of laser-cutting machines, the OPTIPLEX 3015 NEO 15kW which is equipped with technology that allows increased control of beam shape and beam diameter. Mazak Optonics will be in Booth B7541.
The machine automatically adjusts beam diameter to optimally cut various materials and beam shape to control the concentration and power density of the laser beam. The result is improved cut speed and cut quality for a wide range of materials. Equipped with large front and side access doors, the OPTIPLEX 3015 NEO offers accessibility and ease of operation. Minimized work area restrictions make loading material onto the machine and unloading finished parts easier.
The new MAZATROL SmoothLx CNC control features a large 21.5” screen and touch panel. Dual monitors allow multiple applications to run simultaneously. Additionally, the CNC control rotates giving operators the flexibility to work at the front or side of the machine.
The OPTIPLEX 3015 NEO is equipped with a nozzle changer, nozzle centering camera, camera assisted part nesting, and many other intelligent functions. The nozzle centering camera provides visibility of nozzle location while adjustments are made on the torch. Camera assisted part nesting automatically determines arrangement of parts for cutting on remnant material. The intelligent setup, monitoring, and cutting functions support optimal laser-cutting performance.
Booth B7541
New Machines, Solutions, and After Sales from Messser
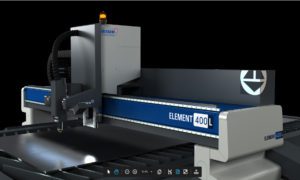
At this year’s FABTECH Messer Cutting Systems (Menomonee Falls, WI) will focus on the new and innovative compact footprint Element 400L Unitized, the versatile Element 400 gantry cutting machines. Messer Cutting Systems will be in Booth B8729.
This U.S.-manufactured cutting machine has acceleration and speeds that can support multiple laser or plasma heads with no loss of performance. These cutting machines have the flexibility to be equipped with many customized options such as plasma beveling, laser beveling, oxyfuel cutting and marking. Both machines at the show will be equipped with the plasma Bevel-S with a C-axis rotation of ± 540° for maximum efficiency. This beveller has scored well in the market for its excellent dynamic behavior.
Our applications engineers will be providing live cutting demonstrations on both machines to showcase the latest in plasma bevel cutting and oxyfuel cutting techniques. Another central focus to this machine is the Global Connect Control and the OmniFab software suite. This software is taking the industry by storm due to advanced digital optimization for plate processing with a focus on Industry 4.0, and IoT with material handling solutions.
Messer is also creating solutions beyond machines and improving productivity through the entire workflow of the thermal cutting process, with a focus on taking a holistic approach. There are many pieces to the manufacturing puzzle of the cutting process and one of the pieces is production software. Messer’s IT professionals will be demonstrating the latest OmniFab production software. This is a tailor-made solution for order-related production to increase efficiency. It integrates Messer engineering technology into a customer’s workflow from the office to production on the factory floor, typically used in conjunction with material handling.
Messer also offers strong after sales and service capabilities and its service teams will be on hand to discuss the service and maintenance packages offered with a purchase of a new machine. The service department will be providing live demonstrations of Messer’s remote Visual and Virtual Services. These are advanced tools that truly offer an “over-the-shoulder” support experience for the customer. For maintenance and errors, the benefit to end users is a much quicker return to production when an issue occurs and a higher “first-time fix rate.” Rapid resolutions using remote tools eliminate the lost time waiting for a technician to arrive on site and the costs for that onsite visit.
Booth B8729
New Small Enclosure CO2 and Fiber Galvo Lasers
Radian Laser Systems (Anaheim, CA) will be featuring their latest 3D fiber and CO2 galvo lasers in Booth A1816. Radian specializes in providing fast and precise 2D and 3D laser marking and engraving solutions for a wide variety of material types. This year they will be featuring their newly released small enclosure CO2 and fiber galvo lasers. Radian’s 3-axis (3D) solutions have proven to be a great addition to shops looking for speed and precision advantages over traditional solutions. Accessories will be on display which will help highlight the flexibility and adaptability that these machines have. Additionally, Radian will be offering visitors customized giveaways so visitors can see the machines in action and have something useful to take home after the show.
Radian manufactures, sells, and services a complete line of both flatbed and galvanometer CO2 and fiber cutting, marking, and engraving solutions that meet the demanding needs of industrial customers. The 3D systems allow for marking on curved surfaces without rotating the workpiece, as well as performing true 3D relief engraving. Advanced software allows for unlimited configuration and precise control to meet the most exacting demands.
Booth A1816
NEW SOLUTION FOR ENTRY LEVEL AUTOMATED LASER WELDING
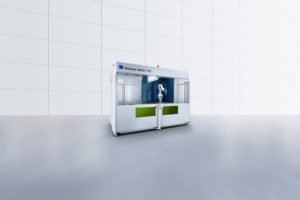
In Booth B6309, TRUMPF (Farmington, CT) will unveil a new solution to help sheet metal fabricators get started in automated laser welding. Fabricators no longer must choose between costly and time-consuming manual welding or large, automated systems that are expensive and complicated to operate. Enter the TruLaser Weld 1000, an entry level solution from TRUMPF which offers smaller companies the benefits of automated laser welding, boosting the productivity of their production processes to provide a real competitive edge. The new system is particularly suitable for job shops that weld products such as electrical cabinets, sheet-metal boxes and covers.
The TruLaser Weld 1000 makes programming quick and easy. Unlike most commercial systems that require several days of training, the information needed to run the TruLaser Weld 1000 can be obtained through e-learning. The system incorporates a robot whose operation is based on the concept of a collaborative robot, or cobot. However, its 6-axis articulated arm enables it to move much faster and more precisely than a standard cobot, resulting in higher-quality weld seams and less non-productive time. The operator manually guides the robot over the seams on the part to be welded and presses a button to mark the relevant waypoints. Then, the software creates the weld program.
“Depending on the part, this style of programming — where you simply guide the robot along the seam — takes a matter of minutes,” said Masoud Harooni, head of the welding technology product group at the TRUMPF Inc. Smart Factory. “So, it’s also a good choice for small-batch production.” With a compact format and dimensions of 17 by 7 by 9 feet, the system fits most manufacturing facilities and can typically be installed and commissioned within a single day.
Double the Work Area at the Touch of a Button
Efficiency is a key advantage of the TruLaser Weld 1000. The work area is divided into two sections with a partition. While the robot welds a part on one side of the partition, the operator can load and unload on the other. Once the welding process is finished, the robot automatically switches to the other side along a linear axis and starts work on the next part. This design saves time and boosts productivity. If the operator wants to weld larger parts, the partition can be raised automatically to provide a work area that is double the size. To maximize safety, TRUMPF developers installed a wall behind the robot to ensure that no laser light can escape during welding. This keeps employees safe when they are working right next to the robot.
High-quality Welding of Thin Sheets
TRUMPF uses a 3kW solid-state laser as the system’s beam source. The high-power laser energy rapidly penetrates the sheet when and where it is needed, making it easier to weld thinner sheets without distortion. In most cases, no post-processing is required, so companies can save time and cut costs. The TRUMPF laser system is also a great choice for processing thicker sheets.
Booth B6309
AIDA-America’s Single Point, Direct-Drive Gap Frame Servo Press, DSF-C1-A Series
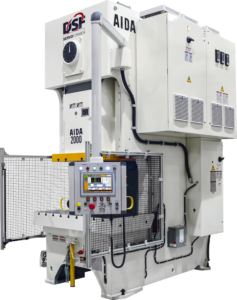
AIDA-America’s (Dayton, OH) A-Series single point, direct-drive gap frame servo press showcases the company’s exclusive Allen-Bradley control, featuring an ergonomically designed 12-inch swing-arm mounted color touch screen HMI with optical run buttons to provide the highest level of safety while helping to reduce operator fatigue. AIDA-America will be in Booth B6007.
Other control highlights are an Allen-Bradley servo motion controller on ControlLogix® platform, 150 job recipe storage, integrated tonnage monitor (peak only), step-feed (CNC handwheel) slide motion control for ease of die setup, eight PLS cams, eight channel die protection with PNP/NPN signals, and display of actual and virtual crank angles. Additional DSF-C1-A Series features are a next generation servo motor with 5-to-10% higher speeds than AIDA’s previous generation gap frame servo presses, a capacitor-based Energy Conservation and Optimization system that reduces peak energy draw, and a state-of-the-art Electronic Overload Protection system that monitors applied torque throughout the stroke to prevent overloading. The DSF-C1-A Series product line is offered in a range of tonnages from 80 to 250. AIDA-America will demonstrate a 150-ton DSF-C1-A gap frame servo press in its booth, blanking parts with AIDA’s optimized servo silent blanking motion profile, which can only be achieved on a servo press.
Booth B6007
New Era of Press Tech Without Hydraulic or Mechanical Flywheel Systems
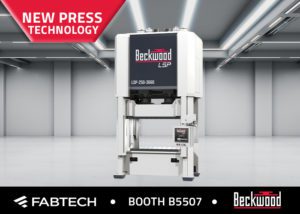
Beckwood Press Co. (Fenton, MO) will unveil their new product line, Beckwood LSP™, at FABTECH. Visitors to Booth B5507 will see first-hand the new era of press technology that achieves both high tonnages and production level speeds, without the use of hydraulic or mechanical flywheel systems.
New to the press industry, this line is unmatched in terms of forming flexibility, production throughput, precision, and uptime. The Linear Servo Press product line (patent pending) combines the flexibility of hydraulic presses with the performance of servo-mechanical presses. LSP is ideal for modern manufacturers in industries ranging from compression molding to advanced steel forming and is available at a competitive acquisition cost. Without hydraulic power units or mechanical flywheels and crankshafts, users experience a design with fewer moving components which allows for easy setup, troubleshooting and virtually no maintenance for millions of cycles.
Booth B5507
Latest in Plate Roll Bending, Tube and Pipe and Section and Profile Bending
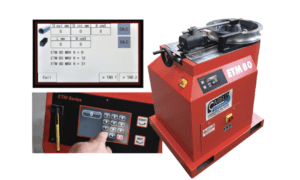
In Booth B9041, Carell Corp. (Stapleton, AL) will display the latest fabricating technology in plate roll bending, tube and pipe, section and profile bending systems. On display will be the ETM-80HD which is the company’s latest generation of tube and pipe benders. Built solid for high-performance bending of large diameter tubes on right or left sides with an easy-to-use programmable touchscreen that delivers years of reliable performance. A powerful and precise non-mandrel counter-matrix system allows for less mechanical effort for faster cycle times than machines in the same category, providing excellent finishes. Manufactured from solid steel, its Digital Bend Programming system features a 100MB hard drive with an easy-to-use 7” Touchscreen that offers 99 programs of five bends each, automatic spring back compensation, limit warnings and alarm diagnosis, maximum capacity and minimum radius calculators and maintenance notice screens. Capacities range from 1/2 inch-to-2-1/2 inch Scd. 40 Pipe & 3” OD Tube, Bending Radii: 2” to 16”, as tube sizes permit and can be fitted with optional mandrels and mandrel arms. The powerful drive arbor accepts a variety of tool sizes with quick change tooling for rapid conversion. The keyless arbor’s unique safety drive pin ensures correct mounting of the former every time, making it an excellent choice for any fabricator.
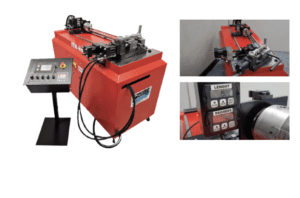
Also from Carell is the ETM-H range of semi-automatic hybrid tube benders, which is ideal for the machining of thin tubes without deformation. In the ETM-H series, the bending function is performed automatically, while the feeding and rotation of the tube between the curves must be performed manually. Simplicity, sturdiness and precision are the key features of this particularly cost-effective line. They are designed for medium-to-small sized production work and adaptation for mobile bending on site. When machining multiple curves, the manual positioner facilitates the work and allows the exact fixing of the length and rotation positions between curves. The hydraulic mandrel extractor, hydraulic clamp die, and pressure die come standard, ensuring a quality finish.
The Digital Bend Programming Touchscreen is easy-to-use with up to 99 programs of five bends each including automatic spring back compensation. Your realized projects can also be stored as repeatable programs. Capacities are diameters up to 3” with a minimum bending radius of 1.5 x the tube diameter.
Booth B9041
“COE EXPERIENCE” Technology Hubs
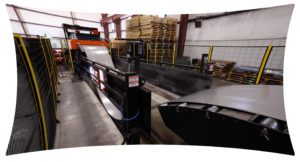
COE Press Equipment (Sterling Heights, MI) will feature a group of technology hubs that together create the COE EXPERIENCE. Visitors to Booth B5729 can partake in a Virtual Reality (VR) demonstration, visit the Smart Manufacturing Decisions station, or participate in other demonstrations that illustrate COE’s equipment and service differentiators.
At the VR hub, visitors will be virtually transported to a fabrication facility to experience an operating COE 72” Cut-to-Length line. At another station, COE team members will take specifications from visitors and run data through the company’s proprietary Science Behind the Solution™ calculators, assisting in better decision-making regarding equipment needs and performance optimization. For example, COE’s Coil Calculator analyzes coil weight based on width/ID/OD, as well as providing coil run time and parts/coil, allowing customers to better plan production and quote new work. The COE EXPERIENCE is intended to help customers make the best coil processing equipment decision for their needs.
Booth B5729
View the Latest Section and Profile Bending Systems
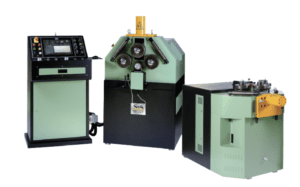
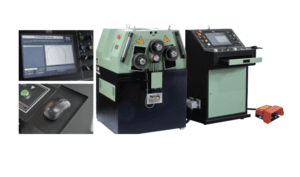
For more than 28 years, Eagle Bending Machines Inc. (Stapleton, AL) has proudly maintained its goals to provide high quality section and profile benders, tube and pipe bending machines, ornamental bending machines, custom tooling options, and CNC controls to fabricators worldwide. Eagle Bending Machines will be in Booth B9041.
Products include the BA-40 and the BA-55, which both feature three driven rolls, hydraulic positioning and CNC controls, and which feature automatic cycle with direct insertion of the radius and bending data to obtain most any shape. The Eagle Probending CNC Controls offer a rapid one pass production rolling or coiling with maximum precision and repeatability. Eagle is 100% American owned and has placed more than 7,500 machines in North America.
Booth B9041
Innovative Hydraulic Press Solutions Include Automation, Custom Applications
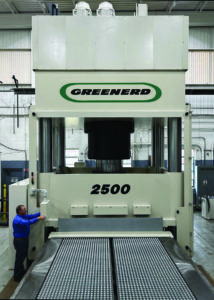
Greenerd Press & Machine Co. (Nashua, N.H.) will be highlighting the company’s extensive hydraulic press and automation capabilities in Booth B5441. Application experts and design engineers from Greenerd will be available to discuss specific user applications and press requirements.
Greenerd offers unique hydraulic press application solutions for a range of industries. One example that demonstrates this versatility is a very large 2500 Ton Hot Forming Press that Greenerd will discuss at FABTECH. Greenerd has designed and engineered this 2500-ton press and is currently building it in their main facility as part of a seven-press order. The press features an innovative mold transfer system which significantly improves the ergonomic and safety dynamics for operators and reduces the press idle time between cycles.
“To meet the demands of today’s challenging applications, we are providing manufacturers with press solutions that are flexible, productive and reliable as well as often being quite large and complex,” commented Greenerd Press & Machine Co.’s CEO Jerry Letendre. “For even greater manufacturing efficiency, we are able to provide our hydraulic press customers with turnkey, state-of-the-art robotic and other product handling solutions.”
Greenerd is a Tier 1 Industrial Authorized Robot System Integrator of FANUC America Corp., the industry’s leader in automated manufacturing equipment. The partnership gives Greenerd full access to the comprehensive offerings of FANUC Robots including all models, training and support, providing state-of-the-art automation solutions in short time frames. Complete, fully integrated production systems can be provided including simple raw material feeding systems, and robotic solutions including loading/unloading the press, the ability to perform an optional secondary part manipulation or process, automated inspection of parts and stacking finished products for downstream processes. The scope of automation can also encompass part inspection systems, ranging from small sensors to complex camera inspections, and temperature monitoring/control of press and non-press related systems. Streaming critical production data to and from the press is also offered.
Greenerd’s extensive line of hydraulic presses are available in a variety of styles ranging from gap frame and straight-side to die-spotting and forging presses, with unlimited size and tonnage capabilities. Greenerd has a long tradition of designing, engineering and manufacturing customized hydraulic presses with product handling solutions.
B5441
New Electronic Control for MQL Systems
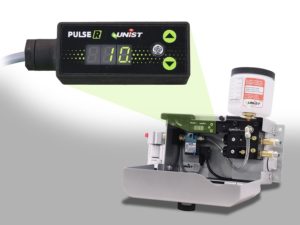
From Booth B5728, Unist Inc. (Grand Rapids, MI) will showcase the new Pulse R™ electronic control, which gives users expanded control of their Unist MQL systems. Backwards compatible, the Pulse R works with new and existing Unist Coolubricator™, Saw Blade Lube, and Serv-O-Spray™ systems. The Pulse R ties into the system control solenoid valve and takes the place of the pneumatic pulse generator timer or logic block. Equipped with fault monitoring and visual feedback of output and input status, Pulse R gives users confidence that their system is working as it should. The Pulse R features flexible operating modes allowing for either constant fluid delivery or intermittent fluid delivery with a user-specified quantity of shots and actuation control with either an input trigger signal or when powered on. The Pulse R requires a 24VDC power supply and input signal, can produce a maximum cycle rate of 250 cycles per minute in continuous operation modes and can deliver a maximum of 99 shots in intermittent modes.
Booth B5728
Press Automation Controller and OEE/Data Collection Software Includes New Features
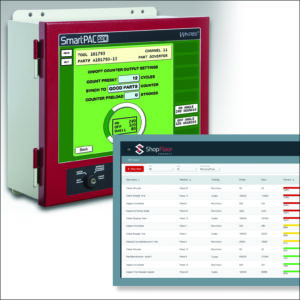
Wintriss Controls Group (Acton, MA) will be demonstrating new, advanced features in its SmartPAC PRO Press Automation Controller and its ShopFloorConnect® OEE and Data Collection Software in Booth B5716. For a connection to a smarter factory, including when remote monitoring is required, the latest functionality in the software gives fabricators and metal formers efficient and easy-to-use tools.
Wintriss reports it has developed the world’s most advanced Programmable Limit Switch (PLS) — new ProCamPAC PRO, for its flagship SmartPAC PRO Press Automation Controller. FABTECH attendees can see this new PLS which includes counter driven outputs that operate only on specified strokes to precisely control gagging operations, new asymmetrical toggle outputs for controlling complex configurable tooling, and additional timed outputs for even greater versatility.
A new Toggle Cam Output performs an asymmetrical toggle function, turning an output off or on for different stroke amounts. The output can be used to operate diverter gates and to control complex gagging operations. The new On/Off Counter Cam Output precisely controls functions that need to operate at a preset interval instead of on every machine cycle. Operating similarly, a new Pulsed Counter Cam Output is programmed with an “on angle” and a dwell time instead of an on-off output.
Useful when running configurable tooling, a new Channel Always On Cam Output will simply turn on and stay on until a new tool is loaded. The ProCamPAC PRO PLS also features a unique Triggered Cam Output which actuates a precision one-time cam timing signal based on a preset trigger such as an external input from ancillary equipment, an extended period of machine idle time, or a job change. This output type is ideal for diverting parts during a warm-up period, QC checks, or when bad parts are determined by an outside measuring system.
Attendees can also see new Advanced DiProPAC available on the SmartPAC PRO Press Automation Controller, which boasts more than 10 new capabilities for even greater die protection for presses. In addition, Wintriss has expanded the static sensor monitoring capabilities in DiProPAC with auto-reset, programmable bypass angles, and minimum actuation time settings.
Also, to be highlighted at FABTECH, Advanced ShopFloorConnect® OEE and Data Collection Software collects downtime and production efficiency data from every machine, ranging from CNC machines to presses, fabricating machines and more, in all areas of discrete manufacturing. The new ShopFloorConnect PM Tracker enables users to track important machine preventative maintenance (PM) items by run hours or machine cycles, issues targeted alerts when an item requires PM, and tracks the maintenance work history for all machines. ShopFloorConnect 6.0 also features a new Universal Interactive Application Program Interface that enables users to quickly set up two-way data sharing with any ERP or MES software.
Booth B5716
CCAI’s Finishing Pavilion and FAB to FINISH Experience
The FABTECH 2022 exhibition floor will showcase the newest innovations the finishing industry has to offer, from liquid and powder coatings to pretreatment technologies, auxiliary equipment and more. The Chemical Coaters Association International (Lakewood Ranch, FL) will host its 13th Finishing Pavilion at FABTECH. “The growth of the pavilion and conference program for those interested in finishing allows attendees to see the latest in industrial finishing technology alongside valuable educational sessions,” said Anne Goyer, CCAI’s executive director. FABTECH is the place where industrial finishers gather every fall.” CCAI will be in Booth B4600.
FABTECH’s educational programming offers the perfect opportunity to learn more about the technologies you see on the show floor. The FINISHING Conference program features 19, 90-minute sessions, comprised of nearly 40 presentations, offering a wide range of technical education – from basic to advanced – on topics for everyone involved in finishing technologies.
This year also marks the fifth edition of CCAI’s FAB to FINISH Production Experience. Providing show attendees the opportunity to see a part produced from fabrication to finishing, FAB to FINISH participants can experience each production step first-hand. Attendees pick up a laser cut souvenir part and a production route card from fabrication partner, Mazak, in Booth B7541. The production route card takes participants to CCAI Corporate Member exhibitors in the FINISHING Pavilion for the pretreat, powder coating and curing processes.
Booth B4600
Dynamic Contour Detection Laser Scanner Demonstrations
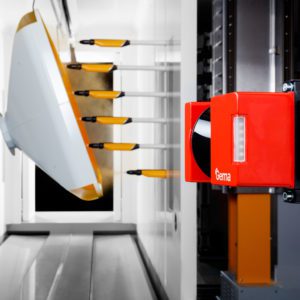
Gema USA Inc. (Indianapolis, IN) will be conducting demonstrations of the Dynamic Contour Detection laser scanner in Booth B5131. The scanner is designed to detect object geometries, aligning each gun to the correct position to coat the most complex components.
Also on display will be Gema’s cloud-based digital intelligence tool, GemaConnect®, which provides data on performance and operational status, as well as maintenance and system health information.
Try out first-hand the OptiFlex® Pro manual spray unit, featuring the highest charging power in the industry at 110,000 V /110 µA. Visit Gema and find out about the latest developments in automatic and manual powder spray guns, booths and powder management technology.
Booth B5131
Alkaline Cleaners with Corrosion Inhibitors Built In
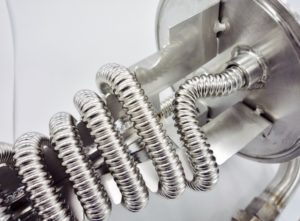
KYZEN (Nashville, TN), the global leader in innovative environmentally friendly cleaning chemistries, will highlight METALNOX M6314CP and METALNOX M6324CP in Booth B5017.
Cleaning and then protecting metal parts is traditionally done in two stages with two different chemistries; however, there are products with the corrosion inhibitor built in to simplify the process while providing pristine parts. Visit KYZEN at FABTECH to learn how its product offerings for clean, rust-free parts can save both time and money.
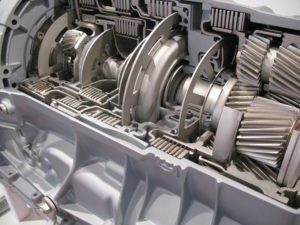
METALNOX M6314CP is an aluminum-safe alkaline parts cleaner formulated to remove numerous manufacturing oils used in a range of machining, stamping and deep draw operations. M6314CP is built with effective steel corrosion inhibitors to provide long-term protection for both mild and cast steel. With its advanced formula, this product successfully prevents flash rusting common in aqueous processing of ferrous metals. M6314CP also is suitable for use on non-ferrous metals, stainless steel, chrome steel, aluminum, magnesium and HSS-parts.
Also on display, METALNOX M6324CP is formulated to remove chlorinated, paraffinic oils used in a various machining, stamping and deep draw operations. It is built with effective steel corrosion inhibitors to provide long-term protection from rust. M6324CP can be added to both the wash and rinse stages of multi-stage cleaning systems and is excellent at removing difficult soils including carbon smut and chlorinated oils. Low foaming with a very low VOC, M6324CP is easy to use and environmentally friendly. The solution provides effective steel corrosion protection for up to 90-days of indoor protection and has an oil splitting formula to allow efficient oil removal.
Since its founding in 1990, KYZEN’s innovative cleaning technologies, scientific expertise and customer support have been repeatedly recognized with the industry’s most prestigious awards.
Booth B5017
Subscribe to learn the latest in manufacturing.