Formidable, Powerful Workholders Provide Optimal Clamping Force
Secure your workpieces with robust clamping forces, innovative designs and quicker setups.
Posted: October 20, 2022
Clamps, vises and positioners are a vital component of workholding systems. Machine shops are looking for reliable solutions in order to avoid disruptions — and surprises. Learn about the latest products that will enable your shop to get the most out of your investment.
New 82L-3E Series of Power Clamps
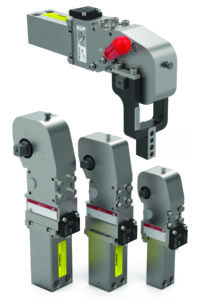
Destaco’s (Auburn Hills, MI) 82L-3E Series Power Clamps feature lightweight, enclosed aluminum housing and optimized mechanics that are more precise and significantly longer-lasting than previous power-clamp designs. The 82L-3E power clamps are a perfect complement to the 82M-3E models and are available in three versions with a holding torque range of 75 Nm to 380 Nm, and clamping torques of 25 Nm up to 120 Nm at 5 bar.
In the event of a compressed-air outage during the 82L-3E’s operation, the clamp can be unlocked manually. Additional flexibility is provided by an optional hand lever, which can be mounted on the clamp’s left or right side. Multiple mounting surfaces also offer improved mounting and installation flexibility. The 82L-3E’s modular structure simplifies the procurement of spare parts and reduces storage requirements, with the same clamp arms that are used with the 82L-2 Series Power Clamps also available as U, H and lateral versions. What’s more, the opening angle of the clamps can be quickly adjusted with just one tool, which helps guarantee maximum flexibility of use.
Innovative Clamping Systems for EV Applications of the Future
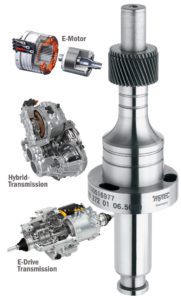
Euro-Tech Corp. (Menomonee Falls, WI), the exclusive North American distributor for Mytec, offers the Mytec Hydraclamp product line of high precision hydraulic and mechanical clamping tools, which are ideal for manufacturing e-motors, hybrids and e-drives.
The Hydra-expansion arbors and chucks are rupture-proof due to their seal-free design making them impervious to dirt. They offer a uniform expansion of the entire clamping range, very high concentricity and repeat accuracy of ≤ 0.003 mm. The Hydra-mechanical arbors and chucks are also seal free for excellent wear resistance. They offer high rigidity due to plane tightening of the workpiece, large loading and insertion clearance, high concentricity and repeat accuracies of ≤ 0.005 mm.
Workpieces include differential gears, stators, rotor shafts, gear shafts and differential housings. The gear grinding of pinion shafts, gear hobbing of pinion gears, gear honing of ring gears, balancing applications, double flank gear and noise checking and arbors for a torque test bench are typical applications.
To ensure superior manufacturing outcomes, Mytec Hydraclamp clamping tools may be incorporated in the assembly and production of the stator package, precision turning of the stator and the e-motor housing for the bearing seats, internal and external grinding of the main rotor shaft, gear hobbing of the transmission gears and shafts, gear grinding of the transmission gears and shafts, gear honing of the transmission gears and shafts, double flank gear checking machines, noise measurement machines, balancing machines and test machines.
Design Fixtures Successfully with Clamping Tools from Lenzkes
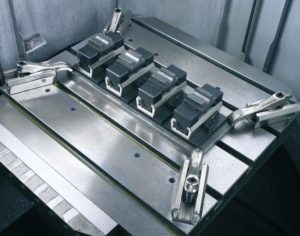
Lenzkes Clamping Tool’s (Christiansburg, VA) Self Centering Clamps can be mounted on sub plates in various numbers. Lenzkes Multi-Quick Tools can also be used to hold sub plates on the machine table. Sub plates with a lower profile can be fixed safely and quickly with Lenzkes Multi-Quick 60 and 100 Series 8 tools.
Features of Lenzkes Self Centering Clamps:
- Stepless adjustable
- Centering accuracy of 0.04 mm/~.0016 inch
- Interchangeable/replaceable faces
- Base plate with centered tapped hole
- Clamping force up to 25 kN/5,620 lbf
Multi-Quick 60 and 100 Series 8 Features:
- Protected trademark Multi-Quick
- Stepless vertically and horizontally adjustable
- MQ 100 Series 8 — greater horizontal adjustment due to the integrated sliding plate
- Strong clamping pressure for small clamping torque MQ 60 Series 8 — up to 24 kN/5,395 lbf clamping force
- MQ 100 Series 8 — up to 22 kN/4,945 lbf clamping force
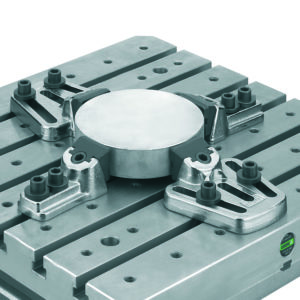
Lenzkes Side Clamps SK10/SKQ 10: Quick and safe workholding solution for free surface machining.
Because workholding fixtures for low profile workpieces and free surface machining are in demand, Lenzkes developed and designed SK10 and SKQ10 side clamps offering solutions for workpieces in different shapes and heights.
SK10/SKQ10 Features:
- Side clamps SK10 and SKQ10 made from drop forged alloy steel and available in different styles
- SK10 side clamps can be used and moved parallel to the t-slot
- SKQ 10 side clamps can be used and moved parallel and at any angle to the t-slot
- Clamping forces up to 14,600 lbf for the largest side clamp
Design of Vises Ideal for Machining Simple to Complicated Jobs
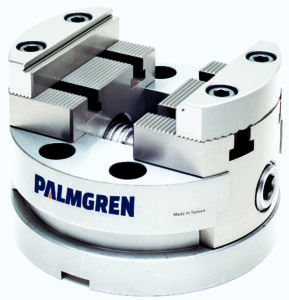
Palmgren’s (Naperville, IL) 5-Axis Machine Vises are specifically designed for multi-face machining. They are equipped with self-centering jaws that reduce clamping time and provide a workholding solution for a variety of workpieces including square, round or odd shaped parts. The design makes them the ideal solution for machining simple to complicated jobs. In addition, their unique round design allows for five-sided access to workpieces. The vises occupy less space and reduce the amount of vise interference. The 100-year-old Palmgren is a C.H. Hanson® brand.
Intelligent Positioner for Assembly, Arc Welding, and Post-weld Finishing
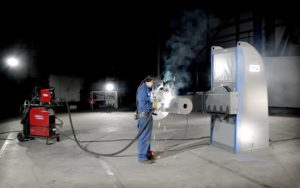
Pemamek Oy and Pemamek LLC (Mason, OH) offer the Skyhook Pro Intelligent Positioners, building upon their proven Skymaster Pro positioning technology. Controlled by a RC32H-wired remote control and intelligent software, the Skyhook Pro positioners can work with heavy loads up to 15 tons. The ability to pre-program and modify movements as needed has eliminated the need for clamping and increased productivity by 70%. They can be rotated +/-180 degrees for optimal positioning. Additionally, because the programs are generated ahead of time by more experienced welders, those new to the trade can continue operations for optimal working cycles using just the remote control and a pedal. This also provides for safer operation.
The Skyhook Pro positioners require virtually no installation, requiring just a few fasteners and cables. Inside an electrical cabinet on the backside of the positioner contains a proprietary communication system connected by Wi-Fi technology to mobile phones, tablets and laptops for programming, diagnostics, and maintenance schedules, providing a vehicle for importing or exporting work cycle information to other Skyhook machines. They are easily integrated with Pema Column and Booms and are ideal for assembly, arc-welding and post-weld finishing operations.
PGU 9800 Uses Holder’s Mechanical Properties Resulting in Tremendous Gripping Force
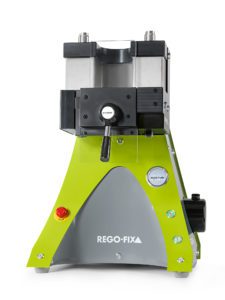
REGO-FIX (Whitestown, IN) offers the PGU 9800, an enhanced version of its proven PGU 9500 powRgrip automatic tool setter, with integrated touchscreen controls, a quieter motor and a status display. The touch-and-swipe LCD displays the size of the current PG insert along with technology cycle counts by tool size, analytics, diagnostic codes and the machine build date.
Like the PGU 9500, the PGU 9800 clamps a tool in less than 10 seconds with up to 9 tons of clamping pressure. For convenience, the unit runs on standard 110V AC power, handles tapers including CAT, HSK, BT, CAPTO, BIG +, TC and ISO, and clamps carbide or HSS in h6 tolerance, including Weldon flat and long shank tooling.
Unlike other clamping systems that rely on heat or hydraulics, the PGU 9800 uses the mechanical properties of the holder material to generate tremendous gripping force, with TIR of less than 0.0001 (≤3 µm) and length adjustment repeatability of less than 0.0004″ (10 µm). Tools are ready to use immediately, with no wait time, loss of accuracy or shortened tool life.
The touchscreen control panel also displays full information about a customer’s PGU 9800 unit. The display enumerates cycle statistics and provides an easy-to-use digital indicator of error conditions.
Pneumatic Clamping Vise for Entry into Automated Machine Tending
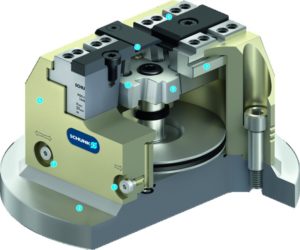
Collaborative robots and an abundance of integrators have made it easier than ever to implement automated machine tending. Many small- to medium-size manufacturers are making the investment into automation and seeing returns in less than six months.
The SCHUNK USA (Morrisville, NC) TANDEM PGS3 vise further supports this trend. Featuring reliable, quality construction, the TANDEM PGS3 reflects SCHUNK’s 75 years of experience at building quality components for the industrial automated manufacturing industry.
The pneumatically operated clamping force block TANDEM PGS3-LH 100 can be directly mounted on machine tables, dividing heads or VERO-S NSL 150 clamping stations of machining centers via an integrated flange. Its extremely compact design and square shape ensures optimum accessibility and enables a considerable stroke of 6 mm per jaw. With a clamping force of 4,500 N and a repeat accuracy of 0.02 mm, the low-maintenance TANDEM PGS3 is particularly suitable for basic applications in aluminum and plastics machining.
Special quality features are the chip-repellent design, the surface-treated components in the force flow and the long base jaw guides that prevent the chuck jaws from buckling under load. The vise can be equipped with all standard top jaws with tongue and groove (KTR, KTR-H) from the world’s largest range of chuck jaws from SCHUNK. With lateral air connections and built-in keyways on the bottom, the vise is prepared for immediate installation in any machine tool.
The PGS3 and VERO-S are a perfect combination to achieve automated workpiece clamping and quicker setup changeover. The quick-change system is the perfect base for your machine table and can reduce setup times to a matter of seconds. Additionally, by having VERO-S on multiple machines, workholding such as the PGS3 can quickly be moved to different processes across your entire production facility, enabling you to get the most out of the investment.
Subscribe to learn the latest in manufacturing.