Get Answers to More Advanced Questions About Aluminum Welding
Getting the best results when you’re welding aluminum requires attention to a lot of details.
Posted: October 20, 2022
In a column printed in the August 2021 issue, I talked about how aluminum doesn’t have to be more difficult to weld than other materials — but it is different than other materials.
Even as you gain experience with welding aluminum, you may still run into occasional issues and challenges when dealing with the material. Here are answers to eight questions we get from welders who work more frequently with aluminum.
Q1: What welding parameters should I use?
A: Setting proper parameters for welding aluminum depends on several variables, including the welding process, weld position, joint design, wire diameter, and base material type and thickness. First, check to see if the filler metal data sheet has any recommended parameters for the welding process and weld type you’re using. You can also test whether you have proper parameters by welding a coupon with those settings and then conducting destructive testing to inspect the weld for proper root fusion.
Q2: What is the best filler metal for aluminum?
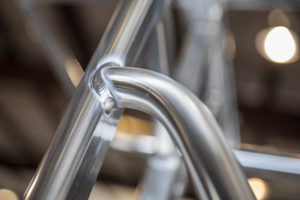
A: Choosing the right filler metal for the job is a key part of creating high-quality aluminum welds. Two of the most common aluminum filler metals are 4043 and 5356. If your welds will be exposed to long-term elevated temperatures (more than 150 degrees Fahrenheit), if they require reduced risk of shrinkage cracking, if you want to minimize the chance of distortion, or if aesthetics is important, a 4043 filler metal is a good option. If you are welding on 5xxx or 6xxx series aluminum that requires anodized color matching or where strength is a consideration, or on welds that require high ductility and toughness (such as those subject to dynamic loading), then a 5356 filler metal is a good choice. Consult a filler metal selection guide if you have additional questions. Also, no matter what filler metal you choose for MIG or TIG welding, be sure to use the right size filler metal. When selecting a size, consider the volume of filler metal compared to the surface area to be filled. There is often a tendency to undersize the welding wire or rod, which can cause problems and result in poor weld quality.
Q3: How do I prevent porosity in aluminum welds?
A: There are many possible culprits of porosity, so it can be difficult to pinpoint the exact cause. The first step is to make sure your base material is properly prepped and cleaned, which is crucial to making a good aluminum weld. Clean the base material with solvent cleaner or etching, then brush it with a stainless-steel wire brush before assembling the weld joint to remove impurities and the oxide layer. If you’re using a solvent, make sure to choose one that will completely evaporate before you weld. Another possible cause of porosity is the shielding gas. Check for any leaks in the gas delivery system and inspect the O-rings on the welding gun. Also, if the base material and filler metal are wet with condensation (if they were brought into a warmer shop from colder storage, for example), this can be a cause of porosity.
Q4: How do I control heat input on aluminum?
A: The weld is often not the weakest point when working with many aluminum alloys. Instead, the heat-affected zone (HAZ) around the weld will be the weakest point. This comes into play when welding with high heat and slow travel speeds. It’s also important when the weld is ground out and redone or when the job requires multiple weld passes, since these factors put more heat into the HAZ and surrounding material. In those cases, you can end up with a very strong weld but a weak HAZ. Be sure to take this into account when designing the weld joint and planning heat input. The loss of tensile strength in heat treatable alloys may continue in the HAZ as heat input increases. Meanwhile, 5XXX base alloys will drop their tensile strength to the annealed condition regardless of high heat input conditions.
Q5: What is the best tungsten for aluminum TIG welding?
A: Previously, it was common to weld with pure tungsten (green tungsten) when using a transformer-based power source. However, a 2% ceriated tungsten (gray tungsten) is a good choice for today’s inverter-based and transformer-based machines. Gray is a good all-purpose tungsten for both AC and DC welding on steel, stainless steel and aluminum. With gray, operators don’t have to guess which tungsten to use for AC or DC welding. The added elements in the 2% ceriated tungsten can help promote the emission of electrons and prevent tungsten erosion better than pure tungsten. Gray tungsten also has a higher melting temperature than green tungsten, so there is less of a balling effect. The technology in a modern inverter-based TIG welder can result in lack of arc starting or poor arc starting characteristics when using green tungsten. Beyond green and gray offerings (which will cover about 90% of industrial welding applications), other options include 2% lanthanated (blue) tungsten and tri-mixed tungsten. These can offer more precision for very specific applications.
Q6: What can I do with advanced machine features when TIG welding aluminum?
A: If your welding power source offers features such as independent amperage control, balance control and frequency adjustment, you can get ultimate versatility in welding performance for aluminum. Today’s inverter-based power sources have the ability to pair features that help welders of all skill levels produce quality welds. For example, functions like independent amperage control and wave shaping help reduce the heat input on thin materials and get more penetration with the electrode.
Q7: How can I best weld anodized aluminum?
A: Anodizing is a process that converts the metal surface into a durable, corrosion-resistant oxide finish. Different operations often have different methods for welding anodized aluminum. One common way is to use “bump welding,” where operators don’t mechanically clean the anodized layer off the metal. Instead, they use a very high amperage to TIG weld it, which provides a lot of arc pressure to push the oxides to the side. The operator dips the filler rod and turns the arc off, causing the oxides to flow back over the top of the weld pool. This keeps a consistent material appearance.
Q8: Should I use pulsed MIG on aluminum?
A: Pulsed MIG can provide several benefits for welding aluminum. The process maintains a clean droplet transfer through the entire wire feed speed range of the electrode, so there are no short-circuit or globular transfer regions. This reduces weld defects and post-weld rework. Also, pulsed MIG typically welds at lower average voltages and amperages compared to CV MIG when used at the same stickouts and wire feed speeds. This difference allows pulsed MIG wire speed to be increased beyond that seen in CV MIG — to match the same amperage seen in CV MIG. As a result, you get increased deposition rates and faster travel speeds, which lowers heat input. Some welding power sources capable of pulsed MIG have additional features, such as arc control, to help you fine-tune arc characteristics to produce higher-quality welds.
Tips for Aluminum Welding
Getting the best results when you’re welding aluminum requires attention to a lot of details. Material preparation and cleaning, proper heat input, and selecting the right welding process and filler metal for the application are all crucial factors when you work with aluminum.
Subscribe to learn the latest in manufacturing.