Operational Differences Between Welding Positions
Whether welding in the flat and horizontal position or out of position, it’s important to follow the recommended parameters for the given welding wire to achieve optimal weld quality.
Posted: October 20, 2022
Semi-automatic welding applications vary in their complexity and the skill level necessary for the welding operator to complete the job correctly. Welding positions also differ, bringing with them specific considerations to gain the best weld quality and efficiencies.
Flat and horizontal welding and out-of-position welding have operational differences in their welding parameters, travel speeds, usable filler metals, transfer modes and more — all of which can impact overall costs and productivity. There are also industries that tend more toward one position or the other based on the advantages and limitations of each.
Flat and Horizontal Welding
Flat and horizontal welding (sometimes called in-position welding) is common in industries such as railcar fabrication and structural steel where the parts are large and the weldments long. In these applications, the parts are rotated so the welding operator can weld on a flat surface or on a surface with a roughly horizontal weld axis.
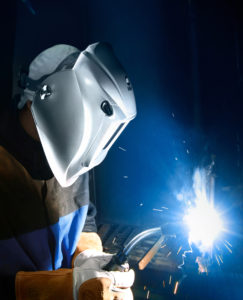
It is easier to train welding operators to weld in the flat and horizontal position. In addition to being faster than welding out of position, it’s often less expensive because it’s a more efficient and ergonomic use of labor; welding operators can spend less time positioning their bodies before welding begins. Many consider this welding position to be optimal, particularly regarding weld penetration and travel speeds, because the operator has more control over the weld pool, and it is more predictable. Gravity is working to their advantage, driving the molten filler metal into the joint quickly. With that comes increased deposition rates (the amount of metal deposited in the joint in a period of time) to improve productivity, and greater weld quality with flatter welds that tie in well at the toes.
Common joints for flat and horizontal welding include lap, butt, fillet and groove. Metal-cored, flux-cored and solid welding wires are all usable in these configurations. Metal-cored wire, in particular, offers increased benefits in these applications and is operated in the spray transfer mode at higher wire feed speeds, which increases travel speeds. This wire also offers a wider arc cone to bridge gaps more readily, high deposition rates (compared to solid wire) and low spatter levels to reduce post-weld cleaning. For an American Welding Society (AWS) E70C-6M H4 metal-cored wire in 0.045-inch diameter, operating parameters fall into the range of 200-to-400 amps and 23-to-30 volts.
Out-of-position Welding
Welding out of position typically refers to welding a joint vertical up or vertical down. It can also
indicate overhead welding, although this is generally avoided if possible due to it being slow. Out-of-position welding is common when working in confined spaces or on parts that cannot be manipulated, such as in construction and shipyard applications, field work and pipe welding. While it requires more skill to weld out of position and is slower than flat and horizontal welding, there is a potential time savings opportunity when workpiece manipulation is not required.
Flux-cored wires can be operated out of position in the spray transfer mode with decreased wire feed speeds and amperages to lower heat input. These settings allow the weld pool to freeze so the molten filler metal doesn’t fall from the joint, and they provide the welding operator with greater control of the weld pool. Additionally, the slag produced during the welding process creates a “dam” that supports the molten weld puddle until it freezes. The lower wire feed speed, however, decreases deposition rates and the welding process can take longer as a result. Welding operators should lower voltages slightly to reduce weld pool size when welding out of position and may need to adjust the gun angle to be more perpendicular to the base material. Parameters for an AWS E71T-1C/M H8 0.045-inch wire range from 170-to-220 amps and 23-to-25 volts.
It is also possible to weld out of position with a solid wire in the short circuit mode, but this often requires heavy weaving techniques to achieve acceptable bead quality. Unless pulse-capable equipment is being used, metal-cored wires are generally not recommended for out-of-position welding because it is not possible to gain the same productivity benefits as using them in-position.
Ensuring Success
Whether welding in the flat and horizontal position or out of position, it’s important to follow the recommended parameters for the given welding wire to achieve optimal weld quality. Always consult the filler metal data sheet for voltage and amperage ranges as well as wire feed speed details. When in doubt as to the operation about a wire, contact a filler metal specialist for guidance. This is particularly helpful to gain an understanding of wires for out-of-position welding; for example, certain wires may be designed to only operate vertical up or vertical down. And as with any application, follow best practices for weld prep and safety to achieve the best results and protect the welding operator.
Subscribe to learn the latest in manufacturing.