Recycling Solvents In-House Saves Costs and Improves Efficiency
In-house recycling results in numerous process control benefits including significant cost savings, reduced maintenance time, decreased disposal costs and more.
Posted: October 19, 2022
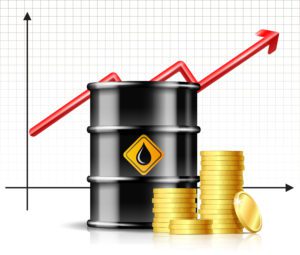
As the world continues adapting to environmental concerns, supply chain shortages, rising prices and lean business practices, it is important to work smarter, harder and more efficiently. Saving money while optimizing process control is a key aspect of success in manufacturing, especially when it comes to solvents and vapor degreasing. Reducing day-to-day costs for vapor degreasing while capturing every drop of solvent is important to keep operations running as smoothly and effectively as possible.
When it comes to process control, using a vapor degreaser to clean parts can be challenging. An efficient degreasing process requires a clean solvent, meaning that solvents must be used and replaced regularly, periodic maintenance is important, and hazardous waste must be disposed of safely. All of this adds up, increasing operational costs.
Using solvents presents its own set of challenges. Numerous traditional and older-generation solvents continue to be heavily restricted by internal environmental health and safety departments. Regulations are increasing and tightening due to reviews, rule changes and possible phaseout by the EPA and OSHA. While this is not surprising given the recent cost increases, it is a difficulty of which to be aware. Being “solvent conservative” means being environmentally responsible, which is necessary in today’s world.
Another issue is that solvent costs are rising, mainly due to the shortage of raw materials, logistics, environmental impact and raw material phaseouts. Many of the components used in blending solvents come from overseas. The global shortage of these raw materials makes it even more difficult to obtain and, therefore, more expensive to source and receive. When sending these parts and components from overseas, shipping, time and transport issues must be factored into the cost. Additionally, the environmental impact (TSCA) is extremely significant. Because of this, the EPA continuously formulates new rules and regulations concerning many of the older generation solvents, which will cause them to be phased out of use. Not only that, but the manufacturers of these solvents are slowly diminishing. For example, there are only one or two manufacturers in the United States that are still making TCE. Finally, because many of the raw materials used in solvents are being phased out, it is becoming more difficult to find materials, which makes the cost even more prohibitive.
Therefore, it is important not to waste any part of the solvent that can be reused. As parts are degreased, soil volume increases over time. To maintain solvent purity, the contaminants must be removed. Some users simply replace the bath with a new solvent when loaded. This is not efficient because it increases operational cost and interrupts the cleaning process.
Implement a Solvent Recycling System
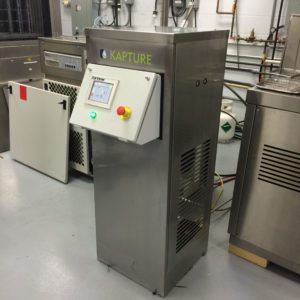
One solution to the shortage problem is using a solvent recycling system. Reduced cost and solvent consumption can be accomplished through in-house recycling. This type of program reduces the amount of new solvent purchases needed as well as maintenance downtime, hazardous waste disposal, process time (paperwork) and negative environmental impact from having to dispose of the waste. Solvent recycling systems also remove soils from the bath, which improves solvent purity to enhance parts’ cleanliness levels. Recycling also can extend bath lives and condense soil levels, reducing both operational costs and waste disposal. Recycling offsets the higher costs of today’s solvents.
The future use of solvent degreasing is viable and cost effective when using a solvent recycling system, such as KYZEN’s KAPTURE system. The KAPTURE is both efficient and easy to use. It connects to a standard degreaser. The dirty solvent is automatically transferred into the KAPTURE based on the system’s operation and ability to pull in the dirty solvent to be purified. The soils are separated from the solvent and retained in the KAPTURE vessel. The pure, clean solvent is boiled off, or vaporized, and returned to the degreaser for reuse again and again. The condensed waste is automatically discharged for periodic disposal. The system is programmed to dump the waste into an approved container, eliminating maintenance and the need for operators to touch the dirty solvent. The KAPTURE automatically separates soils from the process solvent on a continuous basis, creating a consistent solvent purity level.
Typically, solvent on a degreaser that is not equipped with a KAPTURE system must be dumped and replaced every six weeks. This equates to 12% soil loading. Heavier soil loading means less time between intervals. A standard KAPTURE system runs at approximately 98% efficiency, eliminating the need to dump and refill the machine because the soils are removed automatically and consolidated for waste disposal. Typically, when using the KAPTURE, a positive change in solvent cleanliness is seen in less than 24 hours of operation plus normal production. Additionally, no maintenance is necessary until the waste container inside the KAPTURE has reached the preset capacity of 80%. The machine will automatically contact maintenance personnel for cleaning, maintenance and to be placed back into service.
Reclaiming solvent makes sense in today’s world. It reduces the overall solvent usage/cost annually. The amount of good, reusable solvent that generally would be entrained in the contaminated solvent bath may range from 50-to-75% by volume. Companies can lower this entrained amount to expected levels of 5 percent or less by recycling the solvent in a KAPTURE system.
KYZEN’s KAPTURE system works on most brands of degreasers and provides a range of benefits. It is designed to connect to most popular brand open-top degreasers on the market today. Additionally, it can function with most commonly used degreasing solvents from low to medium boiling temperatures. However, it is not designed for use with flammables or some solvents that may easily chemically decompose. The KAPTURE is best suited for open-top degreasers that contain 50 gallons or less. If the degreaser holds a substantial volume of solvent, a larger size system will be required. While the average solvent recycle rate is 1.5 gph nominal, the recycle rate will decrease as the solvent soil loading increases.
Recycle, Reduce, Reuse is Imperative
Using a solvent recycling system allows users to reuse as much solvent as possible instead of disposing of it. This type of in-house recycling results in numerous process control benefits including significant cost savings, reduced maintenance time, decreased disposal cost, reduced hazardous waste transport cost and the reporting/taxes/permits involved with using solvent. Additionally, recycling separates and condenses waste volume, reduces “good” solvent disposal, reduces new solvent purchases, and lowers environmental impact. In today’s world, the “three Rs” (recycle, reduce, reuse) are imperative. Add in supply chain issues and price escalations, and it is more important than ever to capture and reuse every good drop of solvent.
Subscribe to learn the latest in manufacturing.