Advances Revolutionize Grinding and Polishing Solutions
Better cycle times and performances result in the production of high-quality products.
Posted: December 27, 2022
METAL CUTTING
Increased versatility and a surge in automation capabilities ensures grinding and polishing machines are durable and provide consistent long-term results for a wide range of grinding applications.
Grinding Machine Offers the Highest Quality from Every Angle
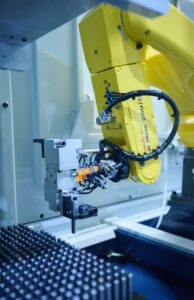
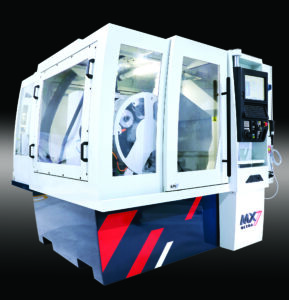
ANCA (Wixom, MI), a market leading manufacturer of CNC grinding machines, offers the MX7 ULTRA, which manufactures large volumes of endmills and other cutting tools with high accuracy and quality. The minute size of a micron is beyond the human eye, but in becoming even more precise and moving from micrometers to nanometers, ANCA will offer the highest accuracy and quality in the cutting tool in the market. New software, hardware and design features are combined to make advances in surface finish, accuracy, and controlled runout, to deliver batch consistency from the first ground tool to the thousandth.
The MX7 ULTRA includes:
- nanometer control system
- new servo control algorithm for smooth motion
- system and mechanical upgrades that enhance stiffness and rigidity
- in-process measuring, balancing and runout compensation for consistent accuracy
- Motor Temperature Control – compensation for thermal expansion on the grinding spindle
- specialist training support in how to grind industry leading cutting tools
Pat Boland, ANCA co-founder said: “The MX7 ULTRA is a significant development in precision machine design and will change the industry expectations for accuracy and tool life. Achieving these outstanding results has only been possible because of our extensive experience working with customers to manufacture the highest quality cutting tools over many years.”
Unlike its competitors, ANCA’s vertical integration means its teams can develop and manufacture their own machines from base to canopy — including controls and drive systems, design and simulation software and even machine monitoring software. Owning all the technology means engineers and designers can consider the entire machine as a single system when developing new solutions.
Internal Grinding Machine Perfect for the Entry-Level Segment
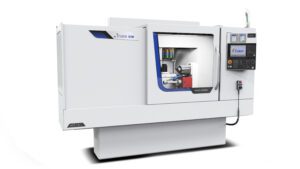
With the S100, STUDER (a member of the United Grinding Group, Miamisburg, OH) offers a universal internal cylindrical grinding machine for the entry-level segment. Its price-performance ratio makes it the perfect machine for a wide range of internal grinding applications. Like all STUDER cylindrical grinding machines, the S100 also has a machine bed made of Granitan®. Its dampening and thermal characteristics ensure consistently good grinding results and precision. During the development, special attention was given to a simple and efficient design of the components, making operation and maintenance easier for the operator. The equipment of the S100 also makes it suitable for grinding a universal spectrum of parts comprising of geometrically defined basic forms and contours, which can be generated with interpolating axes.
The machine can be equipped with up to two internal grinding spindles or one internal and one external spindle. In addition to a fixed wheelhead, it can be equipped with a manual with a 2.5° Hirth and, also with an automatic wheelhead with 1° Hirth. A further advantage of the S100 is the automation option that features a loading interface and an automatic sliding door, enabling automatic operation and the production of large series.
Typical workpieces for this machine include collets for toolmaking, bearing rings, ball bearings and cylinders, as well as hydraulic control valves in small series. External and internal machining of flange parts or grinding of threads or non-circular forms is also possible.
New Sharpening Duo for Carbide-Tipped Circular Saws
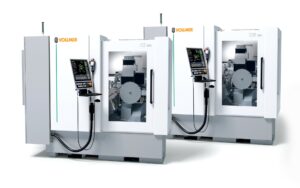
The Vollmer Group’s (Pittsburgh, PA) duo of grinding machines designed for machining carbide-tipped circular saw blades consists of the CS 860 and CSF 860. Thanks to simple control and programing via the touchscreen or keyboard, users can learn how to use the machine in no time. Innovative measuring equipment, handling systems for unmanned machining, as well as the networked data exchange via a standard IoT gateway, automate the production processes for carbide-tipped circular saw blades with various tooth geometries.
The CS 860 is suitable for grinding tooth faces and tooth tops on carbide-tipped saw teeth. The CSF 860 is designed for grinding of the tooth sides on circular saw blades. Users can control and program both machines intuitively via the touchscreen or keyboard. Since they have identical grinding wheel management, once the grinding wheels have been initially measured, they do not have to be measured again after they are changed. The machine automatically detects the newly inserted saw teeth and machines them to size in an oscillating manner. The feed pawl registers broken teeth to prevent the grinding wheels from breaking and determines the tooth pitch. It is not necessary to enter this manually, therefore preventing operator errors.
Automations for round-the-clock unmanned machining can be implemented using various VOLLMER handling systems from the ND series. Customers can combine up to three grinding machines with the ND robotic systems and depending on the equipment, they can be equipped with up to 650 circular saw blades.
Tool manufacturers can use these machines to automate the production of large volumes and sharpening services to flexibly machine circular saws from different manufacturers and types.
Machine for SiC Grinding can be Configured with Many Options
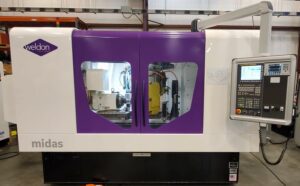
Weldon Solutions’ (York, PA) Midas series model is an ideal machine for silicon carbide (SiC) grinding technology as it can be configured with many options. It was designed for long-term performance in harsh environments with challenging materials.
The Midas series features a rotating turret, including angled and straight wheels for the boule face and diameter. The programmable C-axis option allows users to grind the primary and secondary location flats based on the X-rayed grain angle of the boule. Also, the onboard Renishaw probe provides angular and dimensional verification. With a vertical spindle option, the Midas series can create a horizontal notch required in some SiC boule applications.
Throughout its history, Weldon has collaborated closely with its customers in all industries to provide a solution for manufacturing SiC microchips. Recently, a leader in SiC wafer technology once again reached out to Weldon for solutions to their unique SiC boule (ingot) grinding requirements. In this application, Weldon’s multi-spindle, turret based wheelhead design on the Midas platform allows for OD, Face, Flat, Notching, and Angled-Plane End Face grinding all in the same cycle. The results for this customer are increased productivity, lower SiC wafer production cost, and consistent high quality.
Gear Inspection and Gear Grinder Companies Form Technical Partnership
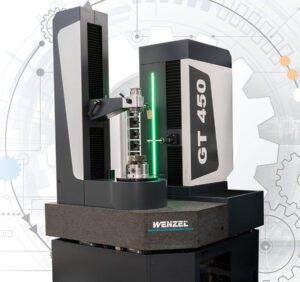
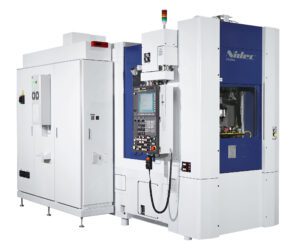
WENZEL America (Wixom, MI) and Nidec Machine Tool America (Wixom, MI) announced their technical partnership at IMTS 2022. WENZEL America and Nidec’s collaboration started with the mutual drive for serving their customers with excellence through data management. WENZEL’s metrology systems easily integrate into any production process, including the gear industry’s processes. “Collaborations like this are a way we bring innovation to our customers,” said Drew Shemenski, president of WENZEL America.
The successes achieved in the field of measurement technology solutions based on closed-loop processes are pushing the boundaries on throughput and delivery. Because of this, forming a technical collaboration between Nidec and WENZEL was an easy decision. “Both Nidec and WENZEL are able to utilize the international VDI/VDE gear data exchange format,” said Scott Knoy, vice president of sales at Nidec Machine Tool America. “Our joint effort with WENZEL offers gear manufacturers the ability to automatically make corrections to the process based on inspection data.” The process was demonstrated at IMTS on Nidec’s internal gear generating grinder, the ZI20A-G.
www.nidec-machinetoolamerica.com
Compact, Capable, Consistent 5-Axis Tool Grinder
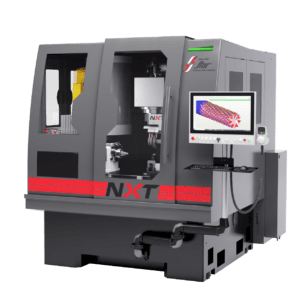
Star Cutter Co.’s (Farmington Hills, MI) NXT is a versatile CNC 5-axis tool grinder with a smaller footprint of only two meters wide with a large grind zone, providing benefits that include greater diversity, increased capability, flexibility, durability and added value.
The NXT wheel pack and coolant manifold is configurable per application with up to five stations, offering the flexibility to handle everything from high mix/low volume production through low mix/high volume applications. It also has two spindle options – a 28 kW, 20,000 rpm auto HSK for general manufacturing or a 15kW, 24,000 rpm auto HSK for manufacturing, regrinding and high rpm applications.
Featuring FANUC robot automation with 0.196”-to- 1.250” gripper assembly, other options for process enhancement include a clearance-optimized flip-up, air-actuated tailstock and other various workholding solutions.
With the NXT, preventative maintenance is improved through real-time tracking of temperatures, spindle hours and bearing travel distances. Key to the system’s functionality is the control software, featuring the latest Flexium Tools with NUMROTO 4.3.0, as well as an ESPRIT CAD/CAM for freeform grinding with 3D simulation and special capability for medical components.
The NXT is designed, manufactured and serviced in the USA with application support available to train operators in the manufacture of complex tools.
www.starcutter.com/tool-grinders/
Subscribe to learn the latest in manufacturing.