As the Mills Turn
Easy-to-learn CNC turning solutions are available for entry-level machines.
Posted: December 20, 2022
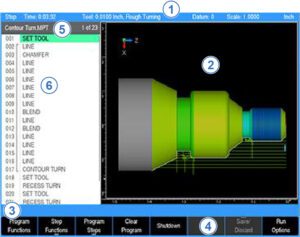
display window of graphical simulation; 3) operator intervention message (OIM); 4) soft keys display area; 5) program name; and, 6) program steps.
It’s not that long ago that milling machines were all manual, and machinists had to meticulously labor over making parts, each taking hours and sometimes days. The job of turning the part within the manufacturing or production setting could be even more laborious.
It is documented that the first lathe was an all-metal slide rest lathe invented by Jacques de Vaucanson around 1751. This lathe allowed for fixing the cutting tool to sliding rails. Then by moving the tool smoothly along the length of the lathe, cuts could manually be made evenly. Early machines were used to standardize the size of screw threads; in turn, that allowed screws to be mass-produced and used interchangeably. As manual turning machines became more widely used, operators began to use mechanical dials or measuring devices to check for part dimensional accuracies of the workpiece. Early parts made with them most likely included items like flat wooden dishes, decorative turned parts, tools and weapons.
Then when digital readouts (DRO) were invented (consisting of a linear glass scale axis-position encoders and a numeric display), manually operated lathes became much simpler to use given the precise positioning accuracy and direct feedback of the tool position. Followed by the invention of CNC turning controls in the 1940s, the capabilities of even entry-level milling and turning machines became incredible.
What’s Now Possible with Turning CNCs?
A long-time manufacturer of machine tool accessories that are used to assist manual machine owners and educators, ACU-RITE has been active in creating advancements in the machining sector. This includes participating in programs that promote machining basics where apprentices learn skills to use manual machines such as mills and lathes, specifically understanding turning functions and features that cover threading and taper turning. This is an opportunity for these apprentices not only to learn and understand the fundamentals of machining with intuitive user-friendly digital readout systems, but also allows them to train on entry-level CNCs. CNCs for milling and turning applications make tedious work much simpler.
Many entry-level CNCs are equipped with manual and conversational modes which make it ideal for production or one-off jobs. As part of the HEIDENHAIN Group, the ACU-RITE TURNPWR was recently introduced for lathes as an entry-level CNC. Although TURNPWR has many intuitive conversational features to support CNC lathe application, users can also import .dxf files and g-code programs. These machines also make it convenient for educational purposes where instructors can use the functionality both in manual and automated mode.
The TURNPWR is designed for turning machine tools with up to two axes plus controlled spindle. Long gone are the days of a machinist’s only option of a manual lathe because current lathe CNC controls are equipped with a user-friendly control screen, and automated machining options available at a touch of a few buttons.
Entry-level CNCs for Lathes
Today’s CNC-controlled lathes can produce a myriad of parts faster than ever before. Even entry-level machines have been known to output parts such as for the aerospace, automotive and engineering industries with materials such as steel, aluminum, brass, acrylic and even electronic components. To do so, users simply choose parameters and/or programs on the control display. For example, the TURNPWR offers both a DRO mode and a PGM (program) mode display.
In the DRO mode, the current position of each axis relative to current datum is displayed. Here, manual machining and Single Cycles can be performed. Tool selection, units, along with most setup features can also be accessed.
The PGM mode displays the list of program steps and part view graphics. New programs can be created as well as editing existing programs. Programs, new or existing, can be saved, deleted, or copied using program functions.
Although a user can import a .dxf file or g-code program in TURNPWR’s PGM mode, the control is very simple to program conversationally using the turning functions. Simple fill-in-the-blank forms allow the operator to quickly define the part program geometry and graphically see the program being created all while verifying the program even before starting to cut material. Before machining a part, users can test the program for things like correct tool path, count direction, feed rate and sequence of operations. The control provides several run-time choices to assist doing this.
Choosing the tool that will be used can be done by entering the data for the tool and establishing its offset or by selecting a tool from the tool library. Lines and arcs are defined by their from point (the point where they begin) and to point (the point where they end).
So, no matter the turning job, machinists can make a simple or complex job with part graphic verification using the turning features and conversational programming within TURNPWR.
The Option of Offline Programming
Another great benefit to many of these entry-level CNC machines is the capability to use some sort of offline programing station. This type of tool allows the operator to program conversational, import .dxf or g-code program while not having to be directly in front of the control. This programing capability usually runs on a standalone demo unit or software that can be loaded onto a desktop PC.
In most cases, the features of the programming station mirror that of the control itself. The option of this simulator software is one of the added benefits to ACU-RITE’s MILLPWR or TURNPWR controls. The control simulation software provides a convenient way to write part programs and simulate machine behavior using a standard Windows computer. Features and functionality are virtually identical to that of the control itself.
The advantages of CNC machining are well known, which includes improved accuracy, productivity, efficiency and safety. Human interaction is significantly decreased when using a CNC machine, and as a result, the number of errors is lower. CNC lathes provide uniform results, allowing companies to produce more parts in a shorter amount of time, cost effectively and safely.
Subscribe to learn the latest in manufacturing.