Monitor and Inspect with Confidence
Tool condition monitoring and inspection systems assist in establishing repeatability and reducing machine tool downtime, among other benefits.
Posted: December 20, 2022
Maximize your shop’s productivity and ability to detect tool breakage and perform preventative and predictive maintenance with these time and money saving solutions.
Tool Holders Reduce Machine Tool Downtime by Enabling Predictive Maintenance
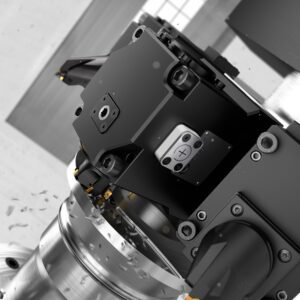
Part of Sandvik Coromant’s (Mebane, N.C.) CoroPlus® digital machining offer, the Coromant Capto® DTH Plus solution minimizes costly dTool Breakage Detector, Heidenhainowntime due to breakages by alerting operators to the need to service an individual driven tool holder. This allows manufacturers to achieve maximum machine tool productivity and output through predictive maintenance and offers fast tool changes in applications using driven tools.
Developed to complement the Coromant Capto quick-change tooling concept from Sandvik Coromant, the driven tool holder solution uses sensors to gather data, which it transmits via Bluetooth, enabling predictive maintenance of the holder. Thanks to the quick-change functionality, the time an operator spends on measuring, setup and tool change is kept to a minimum. Also, because these driven tool holders are equipped with Coromant Capto couplings, the solution makes an extensive range of high-performance cutting tools available to operators.
The software application included provides operators with real-time information, such as the vibration level of the holder, allowing for live monitoring of the spindle as well as monitoring of the temperature within the tool holder. Other data delivered through the sensors include rpm and direction of rotation, which minimizes chances of exceeding the driven tool holder’s limits, along with current and historical information about a particular tool. Also provided are data on the location of a driven tool holder, including the specific factory, machine name, turret and station number.
By providing real-time data, the Coromant Capto DTH Plus offer makes it possible to make the correct decision regarding when to schedule a maintenance stop, ensuring service is carried out with true need and not simply through interval planning. As a result, manufacturers can be confident that their driven tool holders are always in good condition and that their machine shop is operating at very high efficiency levels.
Establish a Controlled Process to Maintain Tool Life
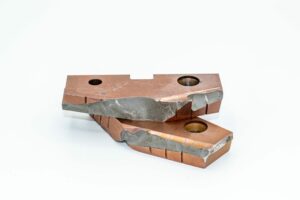
Tool life is often a top priority when working in a high production environment. To some degree, it does not matter if you have the fastest or the best tool; it is more important to have a tool that fails consistently in the exact same way, but the question then becomes how do you achieve this? How can you proactively plan for predictable tool failure?
Allied Machine & Engineering (Dover, OH), a leading manufacturer of hole making and finishing tooling systems, said there are many factors that contribute to failing consistently from the tools themselves to outside factors like coolant, machine maintenance, material hardness, etc. While it is unrealistic to hit 100% repeatability, it is key to keep as many factors as you can the same from job to job and part to part. Establishing repeatability makes it easier to prevent catastrophic failure that will damage the workpiece and tooling, which becomes much more expensive than just taking the tool out early even if that is before it is completely worn out. Therefore, cost savings is one of the biggest benefits of consistent tool life. It is better to change an insert out ahead of time instead of pushing it to max life and potentially damaging components of the tool or components of the machine — causing more setup time and more machine downtime.
Tips to help achieve a controlled process include:
- Proper coolant maintenance and filtration
- Perform preventative maintenance
- Source materials from consistent vendors
- Focus on tool holders
- Consistent tooling means consistent results
Regarding the last bullet point, to do this, it is key to source tools from manufacturers that have good quality systems to produce parts of the same quality every time. If there is a switch in manufacturers, processes will be affected even if the tools are dimensionally the same because quality and performance standards will vary depending on the manufacturer.
Aside from these top factors to consider when planning for predictive tool failure, you
can also work to baseline your tools. Whenever you are running off a project, for the first couple of tools you are putting into the part, you need to ensure that speeds and feeds are optimized, and that repeatability is established. If it repeats after a couple of tools, that is your baseline; you can reach “x” amount of parts per tool.
Being more knowledgeable about an application — whether that is through data collection or proper training — allows you to better establish the desired repeatability.
Machine Tool Break Detection Without Breaking the Bank
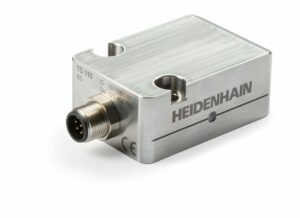
Specially designed for quickly sensing tool breakage during use within a machine tool, the HEIDENHAIN CORP. (Schaumburg, IL) introduces the new TD 110 Tool Breakage Detector. Providing contact-free inspection of drill bits and end mills, it can determine whether a tool is broken off by more than 2 mm as it passes within a machine tool, yielding significant time and money savings.
The TD 110 tool breakage sensor can be placed in the work envelope so that it is fast and easy to reach during the tool change. The inductive sensor can detect tools as they pass by while they are spinning at their operational speed. Thanks to its rapid scanning technology, even very small tools made of HSS steel and carbide are detected.
The breakage sensor can then generate either a floating or an HTL switching signal and the machine control can evaluate it via standard instruction sets. These signals/outputs can be used to connect to a HEIDENHAIN TNC control or a PLC or to any other IOs of nearly every CNC control manufacturer. In addition, an LED signals whether a tool has been flagged.
Overall benefits of HEIDENHAIN’s new TD 110 tool breakage detector include:
- Maintenance-free sensor for reducing non-productive time for breakage inspection
- Cooling lubricant and lightly contaminated tools are tolerated
- Universally retrofittable thanks to standard interfaces for tool touch probes
New Rapid Tool Breakage Detection System
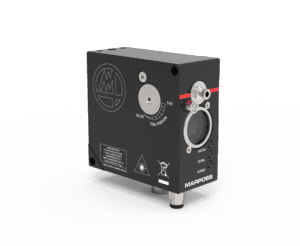
Marposs’ (Auburn Hills, MI) Tool Breakage Detection (TBD) system is a non-contact system well-suited for mass production environments with short machining times, taking less than 1 second to check for breakage on solid body concentric tools such as drill bits, tapping tools, flat and ball end milling cutters. The system helps to reduce part rejects as well as allowing unmanned production.
The TBD is a contactless system using laser reflection technology. The laser beam is projected onto the tool surface, which reflects it onto a high sensitivity photodiode. The signal received is processed to allow tool identification, filtering any interruptions caused by droplets of coolant. A broken tool does not send any reflection signal to the TBD, which remains ready for subsequent checks.
The TBD checks tool integrity before a change-over or after the same operation has been repeated many times, achieving top performance when the machine spindle moves in a single direction. Normally used to detect axial breakage on rotating tools, the TBD has a special operating mode allowing it to detect “passing” tools, whether they are rotating or not, so that the spindle does not have to be stopped in the check position.
The system has an operating range of between 200 and 5,000 rpm, making it well-suited for most standard applications on machining centers, drilling and tapping machines and where unmanned production is required. Additionally, a high-speed version is available for application of 1,000-to-80,000 rpm.
It is a single device with an integrated electronic interface that is easy to install and wire. For optimum performance, the TBD comes complete with software designed for the most widely used CNCs.
Subscribe to learn the latest in manufacturing.