Precision Control and Automation Transform Forming and Fabricating
Discover what’s new with ironworkers, bending, plate rolling and punching equipment from leading suppliers.
Posted: December 23, 2022
METAL FORMING & FABRICATING
Metal fabricators are seeking ways to reduce cycle times and increase productivity in their operations. With ongoing labor challenges, companies require machinery that solves challenges efficiently, with precision and which generate less scrap, among other benefits and advantages.
Punch/Fiber Laser Combo Machine Equipped with Advanced Functions
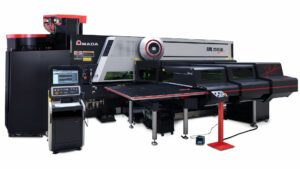
AMADA America Inc.’s (Schaumburg, IL) most popular combination machine, the EML 2515 AJ, combines a multi-purpose turret with the unlimited shape cutting flexibility of a fiber laser, providing the flexibility needed to create better part designs.
To maximize productivity, the EML is also equipped with an automated Punch and Die Changer, (EML 2515 AJ + PDC). The advanced punching and laser cutting functions achieve high-speed and high-quality processing with uninterrupted operation.
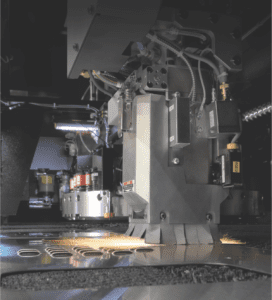
The EML-AJ Series combination machines come with all the punching functions inherent in single-function punching machines. Combined punches and dies are supplied with a Z-turret with different diameters of ø1010 mm upper and ø1200 mm lower or a high-capacity turret of ø1200 mm upper and lower. These machines include the same punching force of 300 kN as the EM Series turret punch presses. The EML-AJ Series also achieves a 25% improvement in stroke frequency (number of hits per minute) compared to conventional machines.
With the EML-AJ Series, AMADA has improved the quality of the laser beam with a 3kW fiber laser oscillator combining high oscillation efficiency with new optics. It employs assist gas rectifying technology for higher quality processing than conventional machines, while increasing cutting speed by a factor of three. The series also features an energy-saving operation, with power consumption reduced to one-third that of conventional machines.
The machines allow up to 24 hours of continuous operation by combining a wide range of optional automation solutions, such as automated Punch and Die Changer (PDC), nozzle changer, laser scrap unloading device, and a cleaning function for cutting plates.
Models equipped with a PDC have undergone an evolution to allow automatic replacement of tools in the processes of loading materials while laser cutting allowing high actual operation rates and further improvements in productivity. The model supports ID tooling and can manage individual tools, monitoring tool life to improve the quality of punch processing and prevent setup errors that can occur when manually changing tools.
All-Electric Tube Bender with Automated Loading
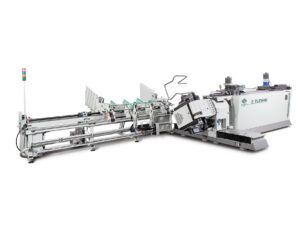
BLM Group’s (Novi, MI) E-TURN’s all-electric drive ensures precision control of the 15-axes movements, providing consistency, high accuracy, perfect quality bends and zero scrap. Tubes in most materials and section types — such as round, square, rectangle, flat sided, oval and elliptical — can be automatically loaded, bent and unloaded.
A key differentiator of the E-TURN is the VGP3D programming and 3D simulation software. By simply inputting the component bend coordinates, the complete bending program is graphically simulated, highlighting potential collision risks and producing the optimal working cycle. Component feasibility is checked virtually, eliminating the need for prototype tooling or physical testing on the machine. Unloading of the finished component is also automatically managed by VGP3D, with the 180-degree head rotation allowing the component to be unloaded in the position required.
Changeover times are significantly reduced, and machine setup simplified as all the critical settings for the machine tooling are managed automatically by the CNC, including clamps, pressure die, mandrel position, retraction, center line radius, etc. Additionally, the self-calibration feature enables true simultaneous axis movement with automatic adjustment of these settings.
The all-electric technology of the E-TURN offers reduced power consumption, typically offering 80% savings as compared to conventional hydraulic bending machines. Maintenance is also reduced due to simplified cabling and components.
The E-TURN is available in four sizes capable of handling maximum tube O.D. capacity ranging from 30 mm-x-2 mm (1.18-in.-x-0.079-in.) up to 50.8 mm-x-1.5-mm (2-in.-x-0.059-in.). Depending on the system, the E-TURN offers a minimum bending radius of 25-to-35 mm and a maximum bending radius of 150-to-165 mm.
Wide Range of Tooling Delivers Precise and Accurate Projects
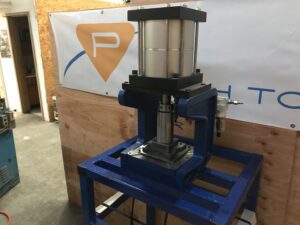
With PTI Punching Tools’ (Coquitlam, BC, Canada) Portapress you don’t need another CNC mill because the Portapress will solve your ills. The real benefit is the tooling that goes into the Portapress to punch primarily aluminum extrusions. It really shines in left/right corner notching applications that are common for window and door projects.
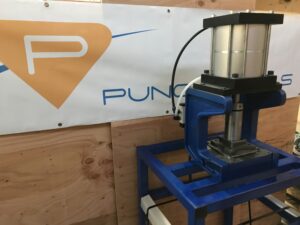
The Portapress can act as a dedicated production line workhorse. Many shops require multifunction machinery, so that is why PTI developed a two-minute quick change system, which allows many different processes to be done at the same punch station.
Punching holes in flat sheet is easy; Portapress tooling can do much more. Production floor managers look far and wide for productive and efficient solutions to band saw and drill press operations that the Portapress can solve quickly and easily.
The true benefits come from the wide range of tooling that fits in to the Portapress frame. Portapress tooling delivers a high level of precision and accuracy to projects to create a cost-effective solution. The precision and accuracy are borne out of the die sets used to guide the working components. Die sets are the backbone of the stamping industry and PTI has brought that to the bench top.
The die set provides precision guidance for punch and die mating. This foundation opens the door to many applications. Die set clearance is .0002” between pin and bushing. This backbone holds tolerance for punch and die clearances for thin materials.
www.punchtools.com www.portapress.com
50-Ton Ironworker with 3-Station Revolving Turret Features Quick Change
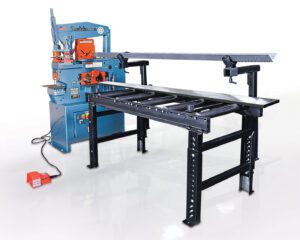
Scotchman Industries’ (Philip, S.D.) 5014-ET 50-Ton Ironworker features a three-station revolving turret that accepts up to three different punch sizes, changeable in seconds, reducing setup times and increasing productivity. For additional automation the 5014-ET Ironworker can be equipped with manual or semi-automatic feeding systems from Scotchman. These optional systems include a 5’-x-24” conveyor with angle iron to support higher production applications.
The 5014-ET hydraulic ironworker is a single operator design with seven total stations. It features 50 tons of pressure and can punch a 13/16″ hole in a 3/4″ plate. Comes standard with an angle shear capable of shearing 4″-x-4″-x-3/8″ angle iron, a flat bar shear that can shear 3/4″-x-4″ to 1/4″-x-14″, and rectangle notcher for notching up to 2-1/2″-x-3″ in 5/16″ material. Standard electric stroke control makes the 5014-ET machine very accurate for bending, punching, shearing and notching operations. A remote foot pedal and punch slug receptacle are additional standard features.
With its component tool table design, the 5014-ET can accept optional equipment, such as the 12″ press brake, rod shear, square tube shear, picket tools, pipe notcher, greatly expanding the 5014-ET’s fabricating capabilities. Custom tooling to meet unique sizes or shapes is also available.
The 5014-ET Ironworker is proudly made in the USA and is backed by Scotchman’s Best in the Business three-year warranty. Scotchman offers a complete line of American-made ironworkers ranging from 45-to- 150 tons of hydraulic pressure — quality, power, & versatility you can count on.
To schedule an on-site machine demonstration, visit Scotchman online or call. Scotchman Industries has 16 mobile demonstration vehicles located throughout the lower 48 U.S. states.
New Gripper Boosts Productivity for Automated Bending Processes
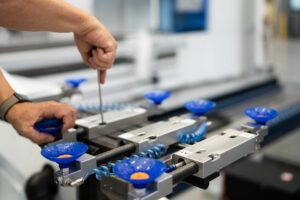
TRUMPF offers an innovative and versatile vacuum gripper.
Image courtesy of TRUMPF.
TRUMPF (Farmington, CT) has introduced a new and versatile multigripper that delivers greater productivity for automated bending processes. The innovative vacuum gripper is used with TRUMPF’s TruBend Cell 5000 and is fitted to the TRUMPF BendMaster robotic arm. Up to 12 grippers can be positioned in this way. Using these grippers, the BendMaster can remove a workpiece from the stack, move it reliably and efficiently within the bending cell, and then place it on the stack for finished parts.
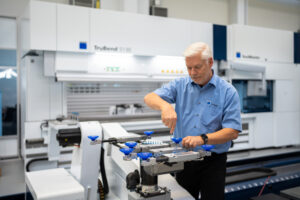
Image courtesy of TRUMPF.
The multigripper makes it economic to use automated bending processes, even for smaller batch sizes. It can be adjusted to handle a new workpiece in a matter of minutes. With the medium-sized variant (M-variant), each of the eight suction cups can be adjusted and replaced by means of a hex key. Minimal expertise is required to perform this operation. As a result, it is much quicker and easier to set up the new gripper than conventional vacuum grippers. All necessary adjustments for the new multigripper can be made at the system level, which reduces the time needed to set up the bending cell. Moreover, with the M-variant, each of the suction cups can be individually activated. This is useful when handling workpieces with complex geometries.
The multigripper also offers highly efficient and versatile handling of workpieces within the bending cell. The smaller-sized variant (S-variant) features a swivel joint that rotates through 180°. This means that the multigripper can turn over workpieces without having to put them down — something which conventional gripper systems are unable to do. This reduces cycle time and makes the multigripper ideal for companies with a bending cell and looking to boost their productivity. Job shops are likely to profit from this solution since they must undertake frequent gripper modifications to bend new workpieces.
Subscribe to learn the latest in manufacturing.