State of the Industry: Creating a Sustainable Future
Learn all about the benefits of navigating the road to becoming a sustainable manufacturer.
Posted: December 20, 2022
The manufacturing industry, including the metalworking sector, is increasingly applying sustainable business practices as pressures such as regulations mount. A reduction in energy usage, lower carbon dioxide emissions, closed-loop recycling — and even customer demands regarding ethical material sourcing — are of critical importance in meeting goals.
Why the uptick in sustainability-related initiatives? Consider this point: research by a board member of the Manufacturing Leadership Council (MLC) found in 2003 there were nearly 2,000 regulations dealing with climate, environmental and other ESG issues1 around the world — by 2019 there were almost 22,000 such regulations. At this rate, the manufacturing sector can expect more regulations in the future.
Sustainable strategies ranging from digitalization (Industry 4.0) to net-zero carbon emissions to circularity are good for business. Not only because the initiatives provide numerous bottom-line advantages but also because they assist in attracting and retaining customers and employees, not to mention ensuring compliance.
A focus on sustainable practices was named as a priority issue in the December 2022 MLC report, Sustainability and the Circular Economy. The MLC is the 3,500+ member digital transformation arm of the National Association of Manufacturers. In fact, an overwhelming 90% of survey respondents believed the manufacturing sector has a special responsibility to become more sustainable in the future.
“And this is a sentiment of senior executives already in place,” said Paul Tate, MLC’s Co-Founding Executive Editor and Senior Content Director. “This is not just next generation, green attitudes. Today’s executives recognize there is a great deal of both opportunity and a few challenges along the way.”
Reputation and corporate values came out on top regarding motivating factors to establish sustainable practices. “This makes a big difference in today’s world because a lot of investors, customers, employees and partners all want to be associated with a company with a sustainable goal or at least a set of sustainable values, irrespective of what particular sector they are working in within the manufacturing industry,” Tate said.
Other motivators included increasing operational efficiencies, reducing waste and cost reduction. “There are some very hard business benefits to pursuing this course and compliance fits into this as well,” Tate noted. Additionally, sustainable practices implemented in the manufacturing of products is passed on to end users who can share that information with their customers.
The Road to Sustainability
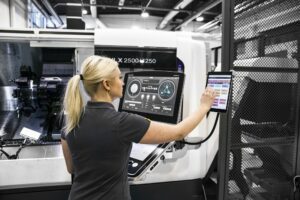
Yes, there are overhead costs associated with pursuing sustainable measures. Perhaps sustainable measures seem overwhelming. Where do you start? The goals do not need to be ambitious right out of the gate, but rather can be tactical. For instance, review your operation’s use of energy.
“All savings are worth money on the bottom line when it comes to energy usage,” Tate said. “If you can focus on renewable energies, I think that is a good step forward for the future and will make your energy supply, hopefully, more resilient. These are difficult times in the world in terms of the energy crisis so all we can do to gradually move toward a more renewable future is beneficial for the industry as well as the environment.”
Tate also pointed out it is important to create a level of understanding as to what your company’s sustainable values are so employees are on board. That way people on the front lines will want to share their ideas on how to improve and create future innovations in more sustainable ways.
So Many Strategies to Achieve Sustainability
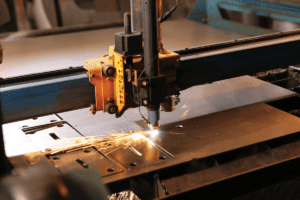
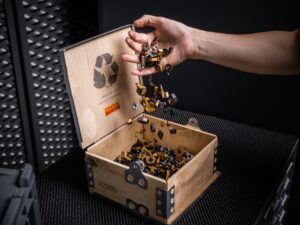
Novelis, Inc., a leading sustainable aluminum solutions provider and the world leader in aluminum rolling and recycling, is working towards achieving a fully circular economy, also known as circularity.
Novelis has partnered with its suppliers and its customers in the aerospace, automotive, beverage can and other industries on the road to being carbon neutral by 2050 — or sooner. Its efforts include closed-loop recycling programs, as well as sorting technologies that increase the quality of scrap to further reduce the company’s CO2 manufacturing footprint.
Naturally, there are costs associated with creating an ecosystem that delivers recycled materials back to Novelis so it can create new aluminum sheets. The partnerships formed in the development of this ecosystem are vital to success. Tate noted that agreements with major customers, particularly in the auto sector, include Novelis taking back waste material resulting from metal cutting. “So, there is a mutual beneficial relationship being established,” he said.
Recycling aluminum cans, for instance, is one thing, but what about reclaiming material from an electronics product, which has a variety of materials? Implementing a circular economic model from the design stage ensures products are easier to disassemble and be dropped off at proper recycling locations.
“There are some challenges in doing that, but it is about creating a mutually beneficial ecosystem and, in many ways, new businesses and new opportunities along that green value chain, which are open to metal formers and their partners,” Tate noted.
There are technologies that assist in the sustainable creation of products. For example, additive manufacturers are increasingly looking at metal fiber to create end products. “And if you think of how that changes the network, the production footprint, if you have smaller factories, in more regional or local areas, you can start to download designs,” Tate said. Producing additive manufacturing techniques locally reduces shipping costs. “And it reduces CO2,” Tate added.
That Industry 4.0 (digitalization) approach to implementing sustainable measures in the design process is sometimes overlooked as a tactic in achieving sustainability. Data, and knowing how to use it, identifies where industrial waste can be reduced, the most efficient use of materials, where reductions in energy and water usage can be achieved, among other factors.
Digital technologies can monitor emissions from a particular plant as well as your progress in reducing emissions. They also assist in streamlining the reporting process to governments regarding an organization’s environmental performance, which is important to compliance efforts, Tate said.
The value of digital technologies and real time data is immense when it comes to developing more sustainable production processes. As an example, connected machines on a shop floor can enhance the invaluable experiences of human workers in “transparency, optimized planning and streamlined production,” wrote Matilda Gynnerstedt, head of product management turning for Sandvik Coromant, in press materials.1
Data-led insights allow companies to pinpoint challenges to their productivity and to avoid unplanned downtime. “For instance, if a facility is experiencing premature tool wear, subpar surface finishes or high machine downtime, the data gathered through sensors can help operators make informed improvements to their machining process in ways that help reduce waste and increase energy efficiency,” Gynnerstedt wrote. Sandvik Coromant, a global leader in metal cutting, is one company that offers machine monitoring insights. The data collected in its CoroPlus Productivity Improvement Program, for example, provides an analysis of a complete production cell, down to the cutting tool. Even small changes prevent waste and reduce energy usage. These changes accumulate and create a positive impact on operational efficiency.
Metalworking Industry Steps Up
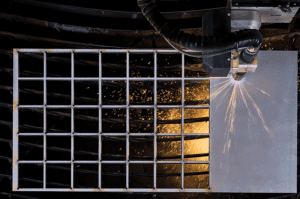
Sandvik Coromant, much like others in the metalworking industry, have developed ambitious sustainability goals. One of the company’s efforts is to establish a more circular business, where it recycles nearly 90% of its waste, and halves its carbon dioxide impact by 2030. It also aims to reduce its energy consumption by 2.5% each year.
For Hypertherm Associates, a U.S.-based manufacturer of industrial cutting products and software, the company continues to work toward four environmental goals set forth in a 2020 report. The goals include achieving carbon neutrality; eliminating 50% of the company’s waste; reducing its carbon impact by 50%; and creating a circular economy. The goals are designed to reduce the company’s use of resources and the carbon impact of its global operations, while also addressing the impact caused by the use of its products.
To that end, according to Hypertherm’s 2021 Corporate Culture and Social Responsibility Report, during 2021, the company integrated its OMAX waterjet business into its energy usage metrics for the first time. Despite the addition of an entire business, non-renewable fuel use decreased more than 7% while absolute electricity usage increased 3.3%. What’s more, both direct and indirect greenhouse gas emissions were lower. Hypertherm also introduced two new products with environmental benefits: a more efficient consumable cartridge; and PlateSaver, a technology that helps customers use fewer plates, which generates less scrap. It is available through Hypertherm’s ProNest and other authorized software for fabricators cutting mild steel on a CNC table using X-Definition plasma.
Yet another metalworking industry company, CERATIZIT Group, is determined to be the leader in sustainability for the hard metal and cutting tool industry by 2025. The company provides tooling solutions and services for the metalworking industry and is on the road to becoming a net-zero corporation by 2040 (which is 10 years ahead of the Kyoto protocol). Current initiatives include implementing green energy resources by switching to blue hydrogen, which results from hydrolysis. Furthermore, at press time, the company has signed contracts to secure green energy supply for all of its facilities in Europe and up to 95% of its facilities around the world.
CERATIZIT also aims to achieve 95% circularity in its processes, based on scrap recycling rates on sintered product. The company aims to reduce the use of virgin raw materials in its products by increasing the proportion of recycled carbide in its products. “It is an extremely high target, but it is a target we are already now working,” said Mirko Merlo, president of the Americas for CERATIZIT Group.
The 95% goal is important because natural resources are not infinite. Secondly, in the supply chain, removing virgin raw material from a mine generates large amounts of CO2. What’s more, it is not sensible to depend on one source or nation for a resource.
CERATIZIT’s green carbide is a world first technological breakthrough, and results from reclaimed material. Merlo said recycled material is often considered a secondary performing material. “In this case, the performance is even better than the typical premium produced with virgin material,” Merlo said. “With this product we were able to reduce by 80 percent the generation of CO2.”
The green carbide, the CT-GS20Y grade, was on exhibit at IMTS 2022 in Chicago. Visitors learned the lower CO2 footprint of the green carbide benefits end users because they will significantly reduce the CO2 generated in the manufacture of their tools. What’s more, due to the use of secondary raw materials for this grade of carbide, CERATIZIT can guarantee better price stability to counteract supply chain risks.
CERATIZIT is also underway with another initiative, a regrinding service, which gives a second life to worn tools by restoring surfaces so that companies can reuse the tools instead of buying new ones.
CERATIZIT also generates nearly 60% less CO2 by producing packaging made from recycled plastic.
Reaping the Benefits
For the foreseeable future, sustainability initiatives will continue to be an expenditure on the bottom line. Merlo encourages U.S. companies to implement sustainability goals. “I am sure if we go all together in this direction, we will really leave a better world behind us,” Merlo said. “This is not meant to be a slogan — I really believe we have a responsibility to leave a better and sustainable world to the next generations.”
Merlo already sees the pendulum swinging in the U.S. marketplace. While European companies have long sought to buy green and sustainable materials and products, they increasingly want to know how much CO2 is generated to make a product. A commonly held thought is that sustainability initiatives are not yet as high on the U.S. manufacturing agenda. To Merlo’s surprise, in visiting with attendees at IMTS, CERATIZIT’s officials found themselves overwhelmed by the number of sustainability-related questions — and ideas — from customers and attendees.
“It goes together with other trends you see in the market, not necessarily connected to our industry or our product,” Merlo noted. “It was a very positive reaction.”
Both Merlo and the MLC’s Tate encourage manufacturing companies to start on the road to sustainability if they haven’t already. “It doesn’t matter whether the targets are ambitious or not,” Merlo noted. “We need the contribution of each and every one if we want to get there. It is a dynamic journey.”
{sidebar} CERATIZIT’s Green Carbide Wins Best of Industry Award 2022 CERATIZIT’s green carbide grade CT-GS20Y recently won the Best of Industry Award in the Best Sustainability Project category, which was awarded by MM Maschinenmarkt.The CT-GS20Y combines the full performance of a premium grade with a focused sustainable production and consists of more than 99% high-quality secondary raw materials. CERATIZIT guarantees low-CO2 production through low-emission production processes and energy sources as well as consistently short transport routes throughout the process chain.As a result, an unprecedented low CO2 footprint of 2.6 kg CO2/kg carbide can be demonstrated for a premium carbide grade with maximum performance.
For further details, visit:
www.manufacturingleadershipcouncil.com
End Notes:
- Regulations included: Chemicals, Substances & Materials, Environment, Human Rights, Circular Economy, Extended Services & Repair, Carbon, Packaging, Product Registrations and Procurement, Waste, Bribery & Corruption-Manufacturing Leadership Council
- “Sustainable Metal Cutting for People, Planet and Profit.”- Gynnerstedt, Matilda, Sandvik Coromant
Subscribe to learn the latest in manufacturing.