Four Ways More Creative 5-axis Machining is More Productive
Prepare for the changes the addition of a 5-axis machine will bring to your business with the right workholding and tool holder solutions.
Posted: February 12, 2023
MACHINING MATTERS
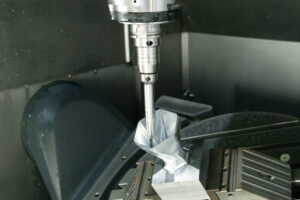
BIG DAISHOWA’s Super Slim Hydraulic Chucks are ideal tool holders for precision finishing processes in confined areas. The slim design eliminates interference.
Prepare for the changes the addition of a 5-axis machine will bring to your business with the right workholding and tool holder solutions.
The addition of a 5-axis machine tool is a significant investment and enhancement for any shop. That said, you can’t assume the new machine will make up for every other up or downstream inefficiency. It’s also important not to rely solely on the machining principles of more-common machines with fewer axes — tool and toolpath considerations can be completely rethought.
Whether you’re simultaneous or 2+3 machining, the added opportunity for movement brings angles and forces into play that may not even be physically possible on a vertical mill or 3-axis machine. Tilting parts or tools reduces the need for extreme tool stick-outs, but the near-limitless angles more axes allow, and extreme part complexities still introduce the risk of costly interference or collision.
In addition to dramatic differences in cutting considerations, efficient part changeover should be top of mind during any process or workflow design. A 5-axis spindle — especially a newly added one — is simply too valuable of an asset to sit idle unnecessarily. The right workholding arrangement plays a major role here — fast, easy and precise clamping can eliminate big chunks of idle time.
Oftentimes in the world of 5-axis, more creative solutions are more productive solutions. With this understanding, there are four areas we can think about a little differently.
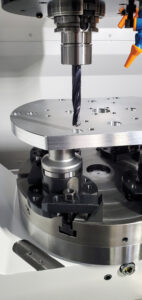
Part Changeover
Most 5-axis machines come with a round, square, or rectangular table or plate. They don’t, however, come standard with quick-change workholding ready to go. There are different bolt hole patterns and pins used to locate and stabilize the workpiece. Having to match these locations with each different workpiece adds another cumbersome step in a process that needs to be closely controlled — before cutting even starts.
Add the fact that 5-axis machining is rarely used for processing the same part over and over, and the right workholding can be a difference maker. The ability to use a zero-point system, like our UNILOCK, as a primary datum locator for all workholding, regardless of if it’s a vise, magnetic clamping or a dedicated fixture, is indispensable for optimizing spindle time.
Looking for a changeover solution that’s even more inventive? Let’s turn to angle heads. We all know angle heads effectively unlock approach angles, but they open possibilities beyond. If you’ve ever had to flip a large part, you know how difficult and time consuming it can be — not an economically efficient move on an idled 5-axis table. Instead of involving a crane, clamping and unclamping, with an angle head you may be able to simply flip the tool instead of the entire workpiece.
Tool Holder Bodies
The extra layers of complexity make it more difficult to adhere to one of the cardinal rules of tooling: keep assemblies as short as possible. Instead of adding extensions or trying to squeeze a wide-nosed holder into a deep pocket, use tooling that’s shaped and built for the job. Of the more-standard holder types out there, the best choice is commonly a hydraulic chuck or shrink-fit holder thanks to their narrow bodies.
Compared to collet chucks, shrink-fit holders and hydraulic chucks have a smaller nose diameter relative to the tools they hold. This allows a further reach into a mold cavity, for instance, or other tricky work envelopes without interference or homespun extensions.
Modular tooling systems offer versatile options for unlocking your creativity too. For one, thread-on style cutting tools with tapered-body designs, like our Contact Grip, are ideal for 5-axis work. Its narrow body is more supported near the flange making it more resistant to the dynamic radial, axial and tangential forces involved with complex 5-axis movements.
Instead of complicating a setup, the Contact Grip can be used as a stabilizing extension that can handle the side load involved with milling and perform movements like spiraling to get cleaner, faster cuts inside complex parts. It also opens the possibility to use several different cutter types more effectively, including chamfers, indexable end, ball nose and radius mills.
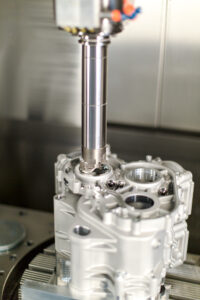
The BIG DAISHOWA Smart Damper dampens vibrations and reduces chatter in deep-hole finish boring and extended-reach applications — thus achieving better surface finishes and improved metal removal rates.
Part Setups
As mentioned, the goal is always to have the shortest tool assembly possible. That doesn’t always mean adapting the holder is the right move. It’s often better to move the part instead of building up a holder.
While zero-point workholding was initially developed and has long been used for setup-time reduction, the system has had great success in 5-axis machining for another distinct reason: access. A standard vise will block the sides of a part and low-profile vises leave sides more open, but grips only along the part’s lower edge.
Alternatively, the option to use a zero-point system to clamp exclusively on the underside of the part leaves the workholding hidden — concealed from all these interferences by the workpiece itself — for a freer state of machining. Pulling a part down is also better than squeezing it, because the squeezing process puts stress on the raw material and the material removal process can compound the negative effects of this stress. What’s more, the closer the part is to the table, the higher the risk of collision with the tool or tool body. Solutions include using a longer holder, which only tickles the part, or raising the part off the table.
Five-axis table adapters, for example, allow 5-axis base chucks to be mounted anywhere they are needed to access the table T-slots or grid holes, all while providing a strong foundation. The modular system allows various combinations of bases, extensions and reductions to be stacked. This can be fully within the part’s footprint, allowing full access to exposed faces and some of the bottom edges.
Hole Making
One of the most common approaches to hole making, helical interpolation, is painfully inefficient. That’s where an under-utilized tooling combination comes in.
Damped toolholders and modular extensions are often used to ensure finishes and tolerance, but when paired with a twin cutting boring head, allows for much heavier depths of cut. The integrated damping of something like our Smart Damper, along with the more efficient linear tool path saves dramatic time.
Similarly, while the use of high-efficiency, large-diameter drills are commonplace when 3- and 4-axis machining large parts, they aren’t as much with 5-axis. However, as more 5-axis machines are equipped with BIG-PLUS® dual-contact spindles and/or higher horsepower, there’s more of an opportunity to use larger drills. Something like the Series 336 IC drill can remove the same amount of material as a mill in a fraction of the time — a two-inch hole can be drilled in seconds instead of taking minutes to mill.
The addition of a 5-axis machine will have ripple effects across your business. You can be prepared for the changes with the right workholding and tool holders. You will also have to think a little differently. Seeking out the inventive solutions, designed uniquely for 5-axis work or not, accelerates all-important ROI. Plus, having the right equipment to support the machining center will unleash your team’s full talents, empower them to succeed and unleash the full capabilities of your business.
Subscribe to learn the latest in manufacturing.