Help in Managing Your Additive Manufacturing Builds
Fabrisonic’s new SmartPlate™ includes embedded sensors made to a customer’s specifications. Extract data from the sensors for real-time or post-processing analysis.
Posted: February 21, 2023
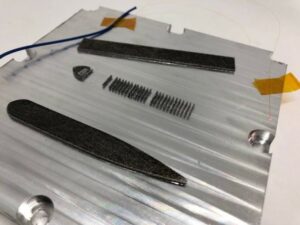
Are You Encountering?
- Parts that debond or delaminate during printing?
- Distortion of parts due to build-up residual stress?
- Bolts that detach from a build plate from accumulated stress during an AM build?
Would You Like?
- To see how stress accumulates during an AM build in real-time?
- Identify the track (stress layer) that leads to distorted or unusable parts?
Would You Like In-Process Quality Monitoring?
- Compare in-process data to previous (successful) product builds?
- Provider skilled operators the data they need to abort prototype or low-volume builds?
- Evaluate the risk of a single part that is part of a larger structure?
Does Visibility into Your AM Build Interest You?
- Early detection of a failure in AM manufacturing cycle.
- Develop a faster and more efficient build cycle.
- Reduce waste through early detection of failure.
- Extract more information within the manufacturing process.
- Verify and refine the analytical models used to predict the outcome of the build.
A Platform is Available to Provide Solutions
The SmartPlate is a build plate with sensors embedded into it that is made to your specifications. It can extract data from the sensors for real-time or post-processing analysis.
Want To See One
Fabrisonic has built a SmartPlate for several customers customized to collect the data they need.
The SmartPlate has optical strain gauges and thermal sensors built into the metal. The printed geometry on top was built using Powder Bed Fusion while simultaneously recording strain/time and temperature/time data. Click here to watch the real-time data that displays the temperature and surface strain video.
How do We do It?
Fabrisonic starts with a billet build plate and mills channels in locations where sensors are to be embedded. Sensors are placed in the milled cavities, and Ultrasonic Additive Manufacturing is used to print solid metal over the sensor. The low-temperature process does not harm the sensors; thus, the metal has continuous, contiguous, and direct contact with these sensors. When the product is completed, the customer has a fully consolidated metal plate with integral sensors buried within it.
Welding Metals Without Metaling?
Ultrasonic metal welding has been around since the 1950s with modern applications in everyday welding of battery tabs, thin foil packaging, and even electronic wires. An ultrasonic weld operation begins by pressing a thin metal foil onto another metal component (foil or baseplate). While under a constant force, ultrasonic vibrations are applied to cause scrubbing of the mating faces. This shearing motion cleans off surface oxides through friction to allow direct contact of pure metal on pure metal. For all metals, the bonding temperature is significantly below their respective melting temperature. The result is an atomic bond between the two metals with minimal heating, leaving the metals in a solid state. The heat and plastic deformation promote diffusion and recrystallization at the interface of the two metals. This process results in a true metallurgical bond. Ultrasonic welding can be accomplished at very low temperatures and without special environments. In using aluminum, for example, this peak temperature is always below 250°F. If you are interested in more information, please read the article Ultrasonic Additive Manufacturing.
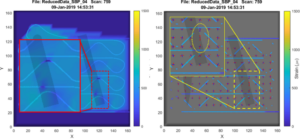
Where did the Idea of A Smart Build Plate Come From?
One of our close collaborators at EWI posed a challenge to Fabrisonic. “How can we measure the loads going through the build plate during an AM process?” Fabrisonic had built a reservoir of knowledge in embedding sensors and was working on embedding strain sensors in aerospace parts. We suggested we build a build plate using our UAM 3D printing technology and incorporating embedded sensors. Fabrisonic proposed collaborating with EWI (PBF research) and Luna Innovations (Fiber Optic Sensors) to design and build an instrumented PBF build plate. The challenge was accepted and then solved!
To test the concept, the team put the SmartPlate in EWI’s PBF machine and began a PBF build that included “highly problematic features.” The team found that the device picked up significantly more information from this initial build than the bulk stress state. Among some of the additional data that was uncovered were:
The resolution and scan rate were high enough to discern the scan strategy of each layer.
Defects appeared as large compressive strains that formed early in the build at localized points.
Slow delamination of a specific feature was seen in the data even though the recoater blade never hit the build.
Show and Tell
This video shows actual strain-time plots resolved in the x-y plane (left) and the raw data along the length of the fiber (right). These colorful strain-time histories easily communicate what is happening in the build. Further data analysis can provide a deep understanding of the quality of the build by:
Analyzing individual ‘pixels’ for sudden vector changes provides tell-tale signs of many build issues.
Comparing time histories of adjacent pixels also highlights problems in the build.
Fabrisonic continues to evolve the concept of the SmartPlate by adding various sensors, including thermocouples and vibration sensors. The team recently upgraded an EOS M290 for further investigations for quality monitoring.
Subscribe to learn the latest in manufacturing.