When to Choose an Ultra-High-Power Laser
The throughput gains offered can be intoxicating. But is it for everyone?
Posted: April 18, 2023
THE CUTTING EDGE
Over the last couple of years, much of the sheet metal world seems to have been abuzz with the myriad promises of ultra-high-power fiber lasers; for sure, it’s hard not to be drawn to the potential gains in speeds, thickness threshold and part quality. Obviously, these ultra-high-power machines come with a larger price tag, so when deciding what to buy, the savvy consumer will want to consider whether bigger is indeed always better.
The first and most obvious question would be whether the machine is up to the task of safely and reliably accommodating such impressive levels of laser power. In the case of TRUMPF’s TruLaser 5000 series fiber with TruDisk 24001, the answer to that question is “yes.” Equipped with a potentiometer that scales speed with power output to an entirely unique optical chain (input coupling, beam delivery cable, cutting unit) the machine is certainly capable, so the question becomes one of practicality.
When laser power increases so does feed rate. That’s certainly an obvious statement that on the face of it is unworthy of further consideration. That is, at least, if you don’t look at two parallel factors: time and distance. When velocity increases, so does the time it takes to get to maximum velocity, and the distance required to do so. These two values (maximum velocity and distance, in particular) determine whether higher laser power actually equals (substantially) reduced run times. Let’s scratch out a bit of math to see for ourselves.
The calculation to determine time to maximum speed is:
In the case where we have a maximum cut speed of 1,500 in/min and an acceleration of 500 in/s2 the time it will take to achieve maximum cut speed is 0.05 seconds. In order for us to determine the distance required to achieve full speed, we use another formula:
Using the same values applied to determine time, we find that the required distance to achieve a full velocity of 1,500 in/min is 0.625”.
With that out of the way we can export some examples into a chart to have a nice, clean visual representation of the time and distance required to achieve full velocity when comparing a base line laser power with a laser producing double the amount of power.
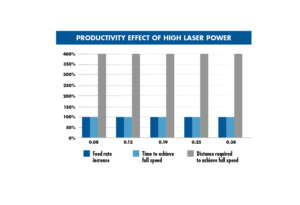
Figure 1 shows us is that using these nice, round (and incidentally, totally generic) numbers, we have an increase in time that perfectly parallels the increase in velocity between a laser of a certain size, and a laser that has twice the amount of power; 100% more power equals 100% more cut speed, which equals 100% more time to achieve full cut speed. The real standout is the gray column, which depicts the required distance to achieve full velocity. Here we’re seeing not a 100% increase like velocity and time, but a 400% increase. What’s the takeaway? The parts that you’re cutting either must have large enough contours and/or be thick enough to be able to achieve the speed increases of the higher power laser.
To move the conversation from the hypothetical to real world, Figure 2 is a comparison of sample parts ranging from thin to thick. The parts will feature varying complexities and sizes.
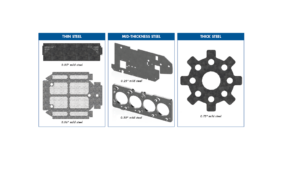
All the parts shown are made of steel and represent a nice cross section of the thickness ranges common to laser cutting. There are two things to consider when determining whether an ultra-high-power laser is appropriate to parts such as these, which range from 0.05”-to-0.75” mild steel. The first is total run time. To determine total run time in this case, I used a TruLaser 5030 fiber with 24 kW of power and compared it to a TruLaser 5030 fiber with 12 kW of power. After running all five parts, we see a result that is, once again, as expected (see Figure 3).
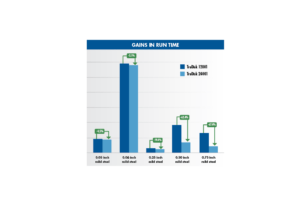
The gains were modest in the thinnest materials, particularly in the part example with the most (very small) interior contours. Quite simply, such tiny contours do not give the laser adequate time to achieve its increased feed rate. Only on the outside of the part can the laser really move. When you get into the mid-thick and thick material though, the story is quite different. On a dynamic machine like the TruLaser 5000 series fiber, it doesn’t take long to get to full trot on materials where maximum feed rate is ≤ 1,000 in/min. That leads to the next (and most important) calculation: actual part cost.
A laser with double the power is going to come with a greater price tag, so we have to calculate part cost with this increased overhead figured in. When the hourly rate of the machine goes up, the throughput needs to do likewise. Figure 4 shows us where that higher rate is offset by the higher level of throughput.
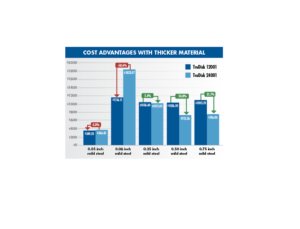
The thin parts didn’t show great enough throughput gains to offset a higher hourly rate. Not only would higher laser power not reduce the production cost of the part, but in fact, it makes it quite a lot more expensive. However, as with feed rate, job cost goes in the right direction as the material thickness climbs north. In contrast to thinner material, the gains in thicker material can be substantial.
The thing to keep in mind is that the charts shown here illustrate cost comparisons of a machine that 1.) is not yet paid off, so we have to calculate its hourly rate pre-completed ROI, and 2.) does not account for additional opportunity cost. The less time you spend cutting job “A,” the more time you can spend on other jobs, thus bringing in more revenue.
Is an ultra-high-power fiber laser for everyone? No, but the throughput gains offered can be intoxicating. Hopefully the information presented here helps you to sift through the numbers a bit and to see if you have a good fit for an ultra-high-power fiber laser, or if something more modest will actually create better profit.
Subscribe to learn the latest in manufacturing.