An Impossible Engineering Feat Made Possible: Sandvik Coromant Develops Statue for the History Books
Made using AI modeling and cutting-edge manufacturing solutions, the Impossible Statue combines some of history’s most famous artists from a period spanning 500 years.
Posted: May 10, 2023
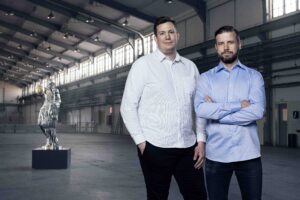
Crafting works of art from metal isn’t anything new. Many of us would instantly think of the Statue of Liberty or the Eiffel Tower, while those versed in contemporary art may think of the Chicago Picasso or Sir Antony Gormley’s Angel of the North. But how would one go about combining several famous works of art using stainless steel and artificial intelligence (AI) to create a new type of modern masterpiece? When Sandvik Coromant engineers Henrik Loikkanen and Jakob Pettersson were tasked with creating an AI-generated, stainless steel synthesis of some of history’s most famous works of art, their metal cutting expertise was put to the ultimate test.
In partnership with Sandvik Group, Sandvik Coromant has developed a statue for the history books. Made using AI modeling and cutting-edge manufacturing solutions, the sculpture combines the dynamic poses of Michelangelo’s work, the musculature craftmanship of Auguste Rodin, the somber tones of Käthe Kollwitz, Kotaro Takamura’s Japanese influence and Augusta Savage’s inspirational defiance to unite some of history’s most famous artists from a period spanning 500 years.
Weighing 500 kilograms and standing at 150 cm tall, the Impossible Statue was officially inaugurated at Tekniska Museet, Sweden’s National Museum of Science and Technology, in April 2023. Producing a statue in such a way has never been done before. So how did Loikkanen, Pettersson and the team craft this blend of art and science, past and future?
When AI Meets Art
AI has been around for some time, with intelligent machines tasked with performing activities that normally require human intelligence, such as visual perception, speech recognition, decision-making, language translation and problem-solving. Its concept dates back decades, with the earliest program written in 1951 by Christopher Strachey, later director of the Programming Research Group at the University of Oxford. But the emergence of new, conversational AI programs such as Google’s Bard and ChatGPT open up even more applications of the technology.
Today, the achievements of AI seem almost limitless — it can even create art. After establishing a 2D design that brought together the styles of the five artists, Sandvik began translating the model into a complete 3D image. Using depth estimators to build the 3D model, human pose estimators to refine the body, video game algorithms to generate realistic fabric and specialized AI to reintroduce fine details that were lost in previous steps, Sandvik was ready to turn the design into reality. Using Mastercam software, a design for a statue with over six million surfaces and complex details was converted.
There were some unique challenges involved in the statue’s design. “We needed a phenomenally precise digital simulation to help us machine the statue,” revealed Henrik Loikkanen, Technology Area Manager at Sandvik Coromant. “Digital manufacturing means we can prove out that whole complex machining process beforehand. The only time we spent on machines, therefore, is actual production time. It also meant we didn’t produce a single scrap component during the entire project.”
Machining the Impossible
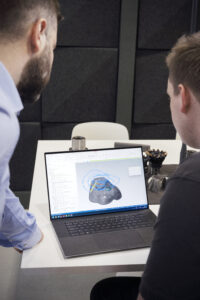
After finalizing the statue’s design with AI and virtually simulating optimal ways to manufacture the statue using digital twinning, it was time to commence machining. “We treated producing the statue as we’d treat machining highly specialized, complex parts like those found in the aerospace industry,” continued Loikkanen. “An additional challenge came from the statue’s chosen material — stainless steel from Alleima — as ISO M materials are notoriously difficult to machine. The material group is characterized by its high work hardening rates and poor chip breaking properties during machining. Careful attention, therefore, must be paid to the tools selected for machining the material.”
Sandvik Coromant chose several tools to help sculpt each intricate part of the statue. The Coromant Capto® tooling interface was used to connect the arm and head to the torso of the statue, solid round tools from the CoroMill® Plura and Dura families were responsible for finishing all the statue’s surfaces and features, and CoroMill MH20, a high-feed milling cutter launched in 2021, was used to machine the bulk of the stainless steel removed from the workpiece.
“We have more than 10,000 standard products covering drilling, milling, reaming and threading in our back catalogue,” explained Jakob Pettersson, CAM and Machining Specialist at Sandvik Coromant. “But we couldn’t select just any tool to create the Impossible Statue. To pull off such a manufacturing feat, we needed to be laser-focused in our selection.”
“We had to give the method and tooling selection extra thought in order to use as little tooling as possible and thereby limit waste. Rough machining of the statue was done with a mix of solid carbide end mills from the CoroMill Plura and Dura families. The rough profiling of the final shape had to be made with rather long tooling. Here, a combination of MH20 high-feed cutters mounted on heavy metal shanks was the perfect fit. The use of end mills from our solid round tools offering greatly sped up the process and therefore reduced energy consumption.”
The CoroMill MH20’s ability to machine at long overhangs typically makes it beneficial to the aerospace sector. It’s designed with difficult-to-machine components in mind and, in contrast to the conventional four-edge concept, the MH20 is designed with a two-edge insert. This is especially beneficial as it means the weakest section of the insert is far away from the main cutting zone, delivering greater reliability and protection against wear. It also means that machining against a corner or wall will not impact the next edge or leading corner, ensuring an equal performance per edge.
CoroMill Plura HD is Sandvik Coromant’s first choice solution for heavy-duty applications in steel and stainless steel, offering safe and efficient solid end milling. The tool now comes with an added benefit in the form of Zertivo™ 2.0 coating, developed by Sandvik Coromant’s R&D team to improve process security and productivity even further. CoroMill Dura is designed to be a one-for-all tooling solution. The end mills can be used in all processes needed to produce a component ― including roughing, finishing, semi-finishing and ramping.
A Manufacturing Masterpiece
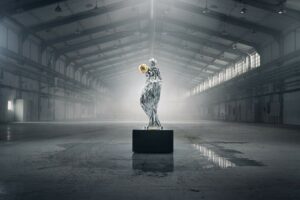
Naturally, machining the impossible isn’t without its challenges, and the team made several adaptations to its machining strategy. “The initial 3D model was not the type of model CAD/CAM systems can work with,” said Loikkanen. “It had to be converted from a 3D-mesh model, which is essentially a shell of surface polygons commonly used in 3D animation studios, to a solid 3D model with density, and that was a pretty challenging process. Once completed, the model was sectioned into 17 pieces, and all interfaces between them had to be modelled with a tight fit to make the intersections invisible when the parts were put together. It took time to get everything perfect.”
“We also had some challenges during rough machining due to the size of the component in relation to the machines,” added Pettersson. “This was solved by simulating NC-code and finding all the areas where we would reach the machine work envelope limit and by altering the CAM sequence.”
In the end, a statue that seamlessly blends the works of five artists was made possible. But developing a never-seen-before statue wasn’t the only accomplishment for Sandvik Coromant. “Along the way, we implemented several techniques that can be applied to future digital machining projects,” said Loikkanen. “Because of the pure amount of programming work, building the statue would have been impossible without a digital twin. All the testing was done digitally to save a huge amount of time that would otherwise be spent on trial-and-error testing. This is certainly something we can apply in future projects to save time and reduce the number of scrap components.”
“The programming and simulation process became faster and faster for each component,” added Pettersson. “Machining took about the same time throughout, mainly because the cutting data and tooling selection never changed that much. This point brought me to one conclusion: the extensive product data and recommendations we give are accurate and are easily attained either from our website, tool guide, Tool Library or even integrated directly in CAM systems themselves. Surely, this is of great value to our customers and addresses one of the more work-intensive tasks in closing the digital loop around CAM programming.”
Now on display for art and technophiles alike to admire, the statue serves as a reminder of the creativity both digital and physical manufacturing tools can accomplish. “I’m incredibly proud we’ve pulled this off,” concluded Loikkanen. “Hopefully those visiting Tekniska Museet, and anyone else who sees that statue, can appreciate that it’s an artwork like no other.”
“The techniques we used and the methods we employed really show what Sandvik Coromant can do,” added Pettersson. “We truly know metal cutting, even when tackling a challenge nobody’s ever seen before.”
To learn more about Sandvik’s Impossible Statue and to watch a video of the project in action, visit home.sandvik/statue.
Facebook; Twitter; LinkedIn; YouTube; RSS Feed
Sandvik Coromant
Part of global industrial engineering group Sandvik, Sandvik Coromant is at the forefront of manufacturing tools, machining solutions and knowledge that drive industry standards and innovations demanded by the metalworking industry now and into the next industrial era. Educational support, extensive R&D investment and strong customer partnerships ensure the development of machining technologies that change, lead and drive the future of manufacturing. Sandvik Coromant owns over 1,700 patents worldwide, employs over 7,700 staff, and is represented in 150 countries.
www.sandvik.coromant.com
Subscribe to learn the latest in manufacturing.