Copper Alloys Find an Ideal Niche in Metal AM
Its thermal conductivity is desirable in rocketry and industrial applications such as electronics, where heat exchange is critical. But 3D printing these advanced materials poses distinct challenges.
Posted: June 5, 2023
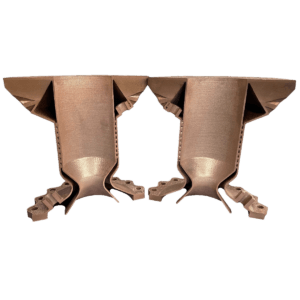
Copper is one of the “hottest” metals attracting attention in the additive-manufacturing world these days. This is in large part due to its superior thermal conductivity, which is desirable in rocketry and industrial applications such as electronics, where heat exchange is critical. That capability stems from the copper atom’s single, free electron in its outer shell that can transfer a high level of energy over a distance with little-to-no resistance. Small amounts of copper can be found in nugget form, but most of what’s used today is smelted out of mined ore.
Second only to silver among metals in its ability to conduct heat, copper is also pound-for-pound significantly less expensive, which is attractive to rocket developers. In its pure form copper is relatively soft; for the more advanced 3D-printing purposes it’s usually mixed with other metals into alloys that provide enhanced mechanical properties along with that valuable conductivity. Common copper alloys for AM include GRCop-42 and GRCop-84 (both are copper chromium niobium), C18150 (copper, chromium, zirconium), C18200 (copper chromium), and GlidCop (copper and alumina). The color of copper alloy powders is a soft pink, with finished AM parts displaying that classic, copper-color glow.
NASA Takes an Early R&D Lead
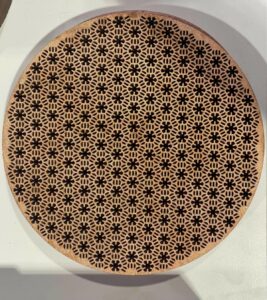
While NASA pioneered the usage of copper alloys in the 1970s on the Space Shuttle Main Engine, that use was at first limited to forged components. GRCop powder metal was developed by NASA metallurgist David Ellis as an improvement on the earlier forged alloys and used with vacuum plasma spraying, a form of Direct Energy Deposition (DED) additive-manufacturing process that produces relatively simple, large structures.
But it wasn’t until LPBF became available—and with enough laser power to work with copper— that copper powder found its ideal match in advanced AM technology. Carried out in an airtight build chamber, LPBF is the manufacturing process that can deliver the extremely complex internal geometries being developed for the latest rocket combustion-chamber designs, or for cold-plate applications in electronics.
These AM-enabled complex geometries are of particular interest to engineers designing lighter-weight rockets with novel propulsion configurations for launch vehicles, hypersonics, and other applications. A rocket’s thrust chamber needs to have material properties that can withstand the thermal and pressure extremes of ignition. But because it is essentially functioning as a heat exchanger, the chamber must also withstand a surrounding flow of super-chilled rocket propellant. Such a fluctuating environment can be balanced with extreme precision by 3D printing intricate cooling channels in the surrounding walls of the thruster—with geometries that cannot be achieved via any other type of manufacturing. The best material for this kind of system? Copper, of course, lining the combustion chamber.
Material Considerations
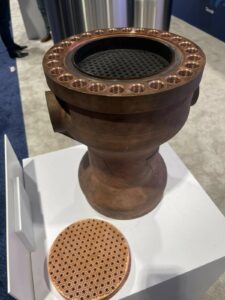
The road to high-value parts always begins with the quality of the materials employed and it’s been no easy task combining copper with other metals into the alloys that are essential for 3D printing high-value parts. Most AM system makers do not also atomize powders; they are dependent on independent materials suppliers to deliver the raw-material ingredients their machines require for optimum results.
Those materials suppliers have been challenged by copper’s relative softness and stickiness, which make it difficult to combine with other ingredients. Some copper alloys rely on dispersion strengthening for enhanced mechanical properties. With GRCop-42, for example, a crucible containing copper, chromium, and niobium is superheated until the chromium and niobium dissolve into the liquid copper. When the alloy is atomized via flash-freezing into a very fine powder, the chromium and niobium combine into what’s called an intermetallic. The smaller the intermetallic dispersed within a powder particle, the higher the mechanical properties (strength, fatigue- and creep-resistance, etc.) of the material—that help mitigate the heat-flux (very hot on one side, very cold on the other) in the liner of a rocket thrust chamber.
According to Jamie Cleland, a materials expert with decades of R&D work in rocketry who’s now a California-based consultant, “You can’t get that key intermetallic formation of copper in an ingot; GrCop is only able to be manufactured as a powder. It was essentially a powder looking for a process, for years—before it found its niche in 3D printing.” Cleland notes that Paul Gradl, a principal engineer at NASA’s Marshall Space Flight Center, is widely credited for taking the lead on the use of powdered copper alloys for AM.
Starting in 2014, NASA began developing GRCop-84 for printing rocket combustion chambers. They then moved to GRCop-42, which had improved conductivity, important in those extreme heat-flux environments, as well as higher build speeds—the latter a metric always in demand in additive.
Gradl reported that, in some cases, the move from conventional manufacturing to AM resulted in cost reductions of more than 50 percent and lead time reduced by up to 10X. Convinced of the value of copper for rockets, NASA stayed the course with GRCop-42, and now, after admittedly quite some time in R&D partnerships, achieved its goal; GRCop-42 has been certified by several of the more advanced laser powder-bed fusion (LPBF) system providers, as has the newer C-18150. Other copper alloys are undergoing certification trials.
Not That Easy to Work With
Now that “new space” startups have begun seriously working with NASA to launch rockets, deliver satellites, and develop hypersonic aircraft, the rush is on to secure powder stock and harness the capabilities of the latest copper alloys. Progress has been somewhat uneven, due to lingering manufacturing issues on the part of materials providers (striking the correct balance between best mechanical properties versus yield and cost of manufacturing powder to meet chemical composition specifications).
“The powder-atomization industry was definitely having challenges just making copper alloy powders,” says Cleland. “As a result, there was more variability in those powders than other more mature ones like Inconel.”
There were also fairly steep learning curves for both AM machine makers and operators (small contract manufacturers with limited experience were particularly challenged when working with copper). Issues continued with print accuracy and product integrity.
Things have improved significantly in recent years. As AM systems continued to evolve their processes and controls, the materials industry began working to better-standardize powder manufacture and sourcing. Nevertheless, supply chain issues were exacerbated by the global pandemic and linger still. Recently, some AM system providers have been working more closely with leading materials makers to secure contracts providing a reliable supply of highest-quality powders for their customers. The larger 3D-printing systems now on the market are also a better size-match to rocket-engine requirements.
As the sophistication of AM systems rises to match the variety of challenges of working with copper, successes are beginning to be realized. These are some of the obstacles being overcome:
- High reflectivity—Most LPBF systems use a fiber laser that operates at near-infrared wavelengths, generally around 1070 nanometers. It turns out that copper alloys are extremely reflective at these wavelengths, with up to 95% of the laser energy directed at the material bouncing off of the metal and into the walls of the build chamber. This means that these systems require even higher power lasers, e.g., in the 1kW range, in order to initiate the melting process—and you need an extremely effective cooling system in the walls of a copper-qualified printer.
Interestingly, once enough directed laser-power has hit the material so that melting has begun, copper transitions from reflecting to absorbing energy. At this point, copper’s innate conductivity comes into play, changing the dynamics of the meltpool as it sucks energy away from the center more quickly than other materials would. The AM system and processing parameters then have to balance these two different modes of the meltpool, conductive (broader, shallower) and keyhole (deeper, light-trapping) in order to ensure that control is maintained and successive layers cohere properly.
- Stickiness. Copper alloys are relatively soft and gummy compared to other materials commonly used in AM. This can create issues in sieving, powder-conveyance, and leftover-powder removal after manufacturing. CT scanning can be used for analyzing powder composition and density, as well as verifying proper de-powdering after a print.
The layer-by-layer process of LPBF is also more of a challenge with copper alloys because their stickiness can make it difficult to achieve even recoats of powder over the build-bed. A non-contact recoater is a distinct advantage here because it never touches the bed or the growing part within it.
- Oxygen sensitivity. Paul Gradl’s work on GrCop demonstrated that the thermal conductivity of the alloy is highly dependent on, and inversely proportional to, the oxygen content of the printed material. Any oxygen that gets incorporated into the microstructure of the alloy will keep it from conducting as well as it should. Particularly in the larger build chambers now available, the importance of maintaining a very low oxygen level in the chamber is paramount. Inert Argon gas is the preferred build-chamber medium when working with copper.
Control and Compete
“Once you know the tradeoffs of copper material, process control is clearly the key to success with printing with it,” says Cleland. “Layer-by-layer quality assurance checks that monitor an hours- or days-long print are critical.” Data collected from sensors during a build informs process development teams at the major AM system providers as they fine-tune parameters for working with more challenging materials like copper.
Meanwhile, NASA is continuing to advance the technology for AM using copper alloys for combustion chambers. Several U.S. vendors have been established to provide these designs as a commercial printing service, and NASA is using vendor-supplied chambers as part of development testing under various programs.
The democratization of AM continues, with even smaller rocket companies now able to buy, lease or access 3D printing (through a contract manufacturing network). The opportunity is ripe to take advantage of the now-being-realized potential of a more mature technology, along with performance-enhanced materials, and enter the competition on an increasingly level playing field.
Subscribe to learn the latest in manufacturing.