Implement People, Process and Technology to Cure Labor Shortage Woes
Technology is attractive to the new generation of workers who are digitally fluent and expect to use digital tools on the job.
Posted: June 15, 2023
WORKFORCE MATTERS
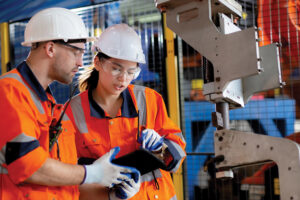
Over the last decade, manufacturing has been on the losing end when it comes to finding and retaining employees, and it is projected that by 2025 the industry will have 2-to-3.5 million unoccupied manufacturing positions. We are witnessing the double whammy effect of an entire skilled generation entering retirement, and, more importantly, the next generation is not lining up to fill in the gaps they left behind.
While attracting and retaining workers is a concern for any business, metal fabricators face some unique challenges. The industry requires specialized skills, can be physically demanding and the work often involves mastering heavy machinery and working with hazardous materials, all of which can add to the current shortage. Metal fabrication shops also claim they have a higher turnover rate as workers leave for other opportunities or pursue other careers outside of manufacturing, which makes it difficult to maintain a stable workforce and ensure continuity of operations.
Unfortunately, there is no perfect solution to this pressing issue. It will demand a holistic approach — one part industry rebranding effort but perhaps most importantly a clear path to career advancement. Which is why now more than ever the industry needs to showcase the powerful role of technology in the workshop.
Keep Your People at the Heart of Your Technology Decisions
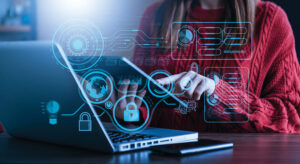
While technology and automation can perform many routine tasks, it is not always able to replicate the creativity and problem-solving skills of human workers. On the shop floor, workers often need to find innovative solutions to problems on the fly, and this requires human intuition and creativity. Case in point, Rainier Industries, a 126-year-old Seattle, Wash.-based manufacturing company, describes itself as an early adopter in certain areas of its digital transformation journey. The company made early investments in CNC plasma tables, plasma pipe tube cutters and robotic welders in its metal shop. In other areas it considers itself perhaps in the middle majority, such as when it comes to the implementation of software applications. In short, digital transformation is not an all or nothing journey. A business needs to ask itself the hard questions about what investments need to be prioritized based on the challenges the business is attempting to solve.
An effective place to start is to ask: What positive impact does this technology investment have on our people? Decision makers should look at that investment not just from the standpoint of immediate ROI, but also how it will create a forward trajectory for employees, such as what upskilling opportunities it presents. Rainier CEO Chris Inverso commented: “Rather than asking our teammates to adopt all the latest and greatest technology, we continue to selectively deploy digital technology only when it gives us a strategic, competitive advantage and when it allows for the highest and best use of our teammates’ talents and abilities.”
He also cautioned: “Employee development is a critical byproduct of our digital transformation journey. Our investments are strategically made to free up our existing talent and move them onto higher and better applications. It is a love triangle of sorts between people, process and technology.” Inverso pointed out how young employees have joined the company as laborers to end up as skilled craftspeople in the metal, fabric, or wood shop because of the powerful marriage of software and machinery that has empowered them to do new things.
Technology as a Hiring Perk
Adopting software solutions such as a manufacturing-specific ERP solution can be the backbone to bolster businesses’ competitive edge when it comes to hiring. As skill gaps and labor shortages continue, positioning your business as a forward-thinking organization with tools in place to make potential hire’s job easier can be a deciding factor. Technology is particularly attractive to the new generation of workers who are already digitally fluent and expect to use digital tools on the job. Given a choice between multiple job offers, 91% of Gen Z candidates say the technology offered by an employer would be a factor in their decision. Today’s high-value candidates are looking for places to work that are rich with technology that is new and intuitive. Enterprise software implementation combined with automation are the technology building blocks fabricators can put in place to maintain and improve bottom lines and improve workforce morale.
Addressing the Misconceptions: The Robots Will Take Over
A common misconception about technology being used to address workforce shortages is that implementing software like ERP to automate business operations will eliminate and replace workers in the long term. Many times, employers ask, “If I automate these tasks, can I eliminate these three positions on the shop floor?” The truth is that automation technology affords workers the skills and tools they need to be more efficient and productive at their jobs, as well as data and analytics to make more informed business decisions. The reality is that with solutions embedded with automation capabilities, workers can be retrained and utilized for more skilled work that contributes to the broader growth goals of the business.
Automation doesn’t replace jobs; automation helps improve efficiency and eliminate repetitive tasks that are more prone to mistakes. For example, if businesses are relying on people to manually input data into a system, there is a greater chance for inaccuracies. Automation helps to remove those errors and ensure greater accuracy in the data, which is invaluable to everyday decision making. It also eliminates the time needed for workers to manually correct mistakes.
Why is Training so Important?
Training with automation software is extremely important because with the ongoing skills gap and the growing use of technology in manufacturing, the incoming generation of manufacturing workers must know how to use the technology and software to perform their jobs most efficiently. It also ensures a business is receiving the utmost return from investment in this technology. This is both the responsibility of businesses, educators, and the software vendors themselves.
While manufacturing businesses should be investing in retraining and upskilling their workforce, it’s integral that the chosen vendor provides customers with training materials that are intuitive and digestible for the end-users. At Epicor our focus is on making our training content available on demand and integrated within the product itself. It is essential that the enterprise software industry plays its part in alleviating the skills gap by developing intuitive training that eliminates learning curves so staff can perform at their full potential.
What’s on the Horizon?
There is a lot to be excited about when it comes to the future of industrial labor. With the growth of automation comes the upskilling of the labor workforce. It will be exciting to see the snowball effects and results of what a more tech-forward manufacturing workforce will be able to innovate and create. Additionally, the rise of low-code/no-code platforms is breeding a whole new era of DIY developers allowing manufacturers to adopt some of the latest technologies quickly and cost effectively, with little to no IT resources. This technology will help manufacturers not only do even more tasks with the resources they have — which will prove to be especially beneficial to small-to-midsize businesses — but more importantly will empower employees to address real workshop challenges with customized solutions.
{Sidebar}
Given a choice between multiple job offers, 91% of Gen Z candidates say the technology offered by an employer would be a factor in their decision. Today’s high-value candidates are looking for places to work that are rich with technology that is new and intuitive.
Subscribe to learn the latest in manufacturing.