3D Printed Metals are Boosting Sustainability at Scale
Look across the lifecycle of a product to determine where the design fits into the bigger picture of making resilient products and moving towards a circular economy.
Posted: July 21, 2023
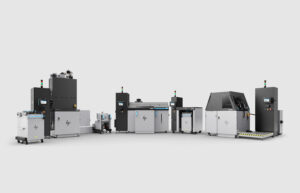
Manufacturers are under increasing pressure to produce and distribute products more sustainably and so are looking at ways to bring down the carbon emissions of the supply chain. With recent climate summits such as Cop26 and Cop27, and the ongoing Paris Agreement providing the framework for ambitious climate goals, manufacturers are also accepting responsibility and placing increased emphasis on the importance of reducing their carbon emissions. More than ever, sustainability must be incorporated from the design stage. New innovative processes such as metal 3D printing — which reduces environmental impact by minimizing waste — are now available and commercially viable. With new approaches to design and digital manufacturing, businesses can seek dramatic improvements, rather than incremental savings.
Currently, companies are already seeking to make an impact by replacing original material with recycled materials, reducing waste through lean manufacturing processes, and adopting renewable energy, which in and of themselves can make inroads to reducing emissions. In addition, there’s scope for advancements in product innovation, whereby companies can transform the way they approach sustainability and introduce new levels of flexibility to their production lines. 3D printing can provide solutions for both sustainability and innovation, and it’s being used with more materials than ever.
Metal 3D Printing: A New Opportunity for Sustainable Manufacturing
By now, no one is a stranger to the benefits of additive manufacturing such as promoting a circular economy and reducing the materials used. 3D printing can help produce personalized, more localized, on-demand 3D printed parts that enable companies to use less material, while expanding product life through increased availability of spare parts. Using on-demand strategies to match production and demand, combining parts to reduce part counts, and printing spares and service parts, means we could reduce our inventories and reliance on warehouses around the world.
The metals applications are now the fastest growing segment of the traditional 3D printing market, and as such, it’s an opportune time for more industries to benefit from it. Industries including automotive, consumer and industrial, want to leverage innovative additive manufacturing technology to address their end-to-end needs for materials, software, sintering and post-processing. Companies across sectors are looking broadly at two objectives: becoming more efficient and safeguarding against instability in the global supply chain. With the increased use of additive manufacturing with metals, being able to produce parts and products in the same part of the world where they will be consumed achieves both objectives.
3D Printing Metals for Mass Production
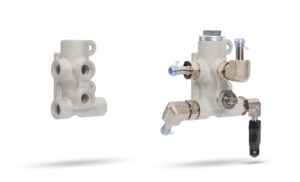
But there was still one major issue with 3D printed metals and that was its inability to scale to mass production. This was addressed by HP with the recent launch of the Metal Jet S100 Solution, which shows a major step in helping businesses to produce 3D printed metal parts in a wide range of applications at scale and with the right economics. The Metal Jet S100 Solution is a modular system that enables build units to travel between four different stations, meaning users can continually run production at high quantities. It provides industrial production capabilities, integrated workflow, subscription and service offerings — all with the aim of helping companies achieve their goals for business transformation.
With the additive manufacturing of metals now available and feasible at the highest capacities, there are now more options open for businesses to innovate. When compared with traditional production methods, 3D metal printing can eliminate the need for molds or tools, thus making it more efficient to produce specialized parts. Additionally, it can help in the creation of new designs and geometries that can lead to parts being lighter, which could lead to other sustainability improvements depending on the application the parts are used in.
Agricultural and construction equipment firm John Deere is an example of a company that has already taken advantage of metal 3D printing and has unlocked environmental and productivity benefits as a result. Together with GKN Additive, John Deere is now using the Metal Jet S100 Solution to create 3D printed metal valves for its agricultural machinery. The company is also using 3D printed prototypes to test and fine tune components and parts such as windshield holders, reducing pre-assembly from 30 days to 10 days, delivery times by up to 10 weeks, and overall production costs by between 20%-to-25%.
Sustainable Design from the Outset
Metal 3D printing is an invaluable step in unlocking the drastic changes we will need to see to become more sustainable right from the design stage. But the goal shouldn’t be to use additive printing, it shouldn’t even be to use digital manufacturing. The priority is to look right across the lifecycle of the product and see where the design fits into the bigger picture of making resilient products and moving towards a circular economy. To succeed, we can’t see manufacturing efforts happen in a vacuum. There should be a unified, organizational approach to sustainable impact, and for that we need buy-in and investment from the top-down to impart meaningful and lasting change.
Businesses can now design with the benefits of additive manufacturing top of mind and incorporate sustainability into the brand’s identity. A key part of maximizing the benefits of 3D printing is to make sure you can track the benefits in the first place. It’s vital, therefore, to set clear targets and goals to help measure the desired level of impact and to maintain organizational accountability in the journey to circularity.
The use of 3D metal printing technology has been steadily growing in recent years, but there is still room for organizations to explore its full potential. While some companies have already started to design products with large-scale metal additive processes, many are still in the early stages of adoption. That is a reason to be excited about the future of 3D printing. We’re only just scratching the surface of what’s possible and as more companies come on board and roll out 3D printed metal for new use cases, we’ll see bigger improvements to the way we make things in the future. The market is learning more about the benefits of 3D printing all the time and as such, we will see bigger investment in the technology in the coming months.
Metal 3D printing is revolutionizing manufacturing, and providing new ways to reach sustainability goals, and as such, the direction of travel can only go one way. It’s now time for the mass production of metals to enter a new dimension and reap the benefits of doing so.
Subscribe to learn the latest in manufacturing.