MIG Welding FAQ: Best Practices for MIG Success
Tips to troubleshooting a few common MIG welding issues will help operations improve productivity and quality, as well as reduce downtime.
Posted: July 22, 2023
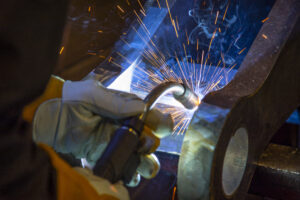
MIG is the most frequently used welding process in general manufacturing and fabrication, thanks to its ease of use, versatility and productivity benefits.
While MIG is widely used, some operations may still run into issues that require troubleshooting. Understanding the basics of MIG welding and following best practices for operator technique as well as gas and consumable selection can help optimize results with the process.
Below are common troubleshooting questions and answers.
Question: What are the main advantages of MIG welding?
Answer: MIG offers productivity benefits when compared to other welding processes such as TIG and stick, thanks to MIG’s higher travel speeds and deposition rates. MIG is also considered easier for new welders to learn, so it can be a good option for operations that struggle to find skilled welders.
MIG can be used with either solid filler wires or tubular wires such as metal-cored wires. When used with flux-cored wires, it is referred to as flux-cored welding. In general, tubular wires can be run at higher speeds and deposit more weld metal, so they offer even higher productivity gains than solid wires.
Question: What are the differences between MIG and TIG welding?
Answer: There are many factors to consider when choosing the right welding process for your application. These include base material type and thickness, weld appearance requirements, productivity requirements, the welding environment and available skilled labor.
TIG welding is generally used in niche applications, such as those that require high-precision welds or extremely high aesthetic quality. TIG is frequently used with special-grade materials like titanium or stainless steel. In comparison, MIG can be used in higher production applications where increased throughput is important, and it’s a good option for a wide variety of metals.
A typical travel speed in TIG welding is 4”-to-6”per minute. With MIG welding, travel speeds are much higher; 6” per minute is considered slow, and 15”-to-20” per minute is common. Deposition rates are also much higher with MIG welding.
Regarding training, TIG is considered the most difficult welding process to learn and master since it uses both hands. It may take a few months for an operator to become proficient in TIG, while a new welder could be proficient in MIG within a week or two.
Question: What is the right shielding gas for MIG welding?
Answer: Shielding gas plays an important role in determining weld penetration profiles, arc stability, mechanical properties of the finished weld, the transfer process you use and more.
The filler metal manufacturer often provides shielding gas recommendations for the type of wire being used, so it’s a good idea to first consult the wire specification sheet.
When using flux-cored wire, common choices are 100% carbon dioxide or an 80/20 argon/CO2 mix. When it comes to solid wire or metal-cored wire, the gas selection is dependent on the transfer mode being used. A short-circuit transfer mode works with 100% CO2 gas in most cases but it can still run on mixed gas. While using a pulse or spray transfer, a higher argon content is needed and an 80/20 argon/CO2 mix is the right choice.
The base material also plays a role in choosing the right gas. Aluminum requires 100% argon, while stainless steel requires at least 98% argon.
Question: Which is better: a push or a pull technique?
Answer: The technique choice may come down to operator preference in most cases, but there are some best practices to help optimize results. For example, when welding aluminum, a push angle is generally better because it helps the cleaning action of the oxidation layer on aluminum while also helping visibility and penetration. Conversely, when using flux-cored wire to weld carbon steel, a pull angle works better because it gives enough time to the slag so it’s not entrapped in the weld metal.
Question: What is the proper wire stickout?
Answer: Maintaining a proper stickout is important to achieving the best results in MIG welding; a too-long or a too-short stickout will affect the weld quality and appearance. A 3/8” stickout is a good starting point, but operators can deviate from that based on preference, wire diameter and accessibility to the weld.
Question: What amperage MIG welding gun is needed?
Answer: To choose the right MIG welding gun, consider the specifics of the application. The wire feed speed and wire diameter are two of the most important factors in determining proper gun amperage. Are you welding heavy-wall materials, like heavy equipment or heavy steel structures? Those jobs will likely require a high deposition and therefore a high-amperage welding gun, such as an air-cooled 400-amp gun with at least a 60%-to-80% duty cycle or more, or in some cases a water-cooled gun. If you weld lighter walls and shorter beads, you may consider a 200-to-300-amp gun.
The most common amperage choice in the industry is a 300-to-400-amp, air-cooled MIG gun. This gun can address the majority of MIG welding applications and can run the most common wire sizes, including 0.045” and 0.052”.
A good starting point is also the welding procedure that’s in place that specifies the amperage needed for the weld, which helps in choosing proper gun amperage. Another easy way is to match the welding machine amperage output — a 400-amp welder would run well with a 400-amp gun in most cases — but this might not be the most effective way to select the right amperage gun when compared to the other methods mentioned above.
Question: How can an operation make consumables last longer?
Answer: Using the OEM consumables designed to be used with a specific MIG gun and welding system is important because these consumables are machined to very tight tolerances and go through strict quality measures, which in turn translate into higher quality welds and longer consumable life.
Be sure to choose a contact tip that is the appropriate size for the wire diameter. An oversized or undersized contact tip will wear faster and result in poor performance. In addition, follow the gun manufacturer’s recommendations for consumable installation and changeover; check connections regularly; install and trim liners to the right length; select the right nozzle material, size and recess/extension; and clean consumables regularly and change them when needed.
Knowing how to choose the proper gun and consumables, using the right welding parameters for the application, and knowing how to troubleshoot a few common MIG welding issues can help operations improve productivity and quality and reduce downtime.
Subscribe to learn the latest in manufacturing.