Improving the Approachability of Automation
Automation is more accessible than ever to manage labor shortages, process inconsistencies and more.
Posted: August 28, 2023
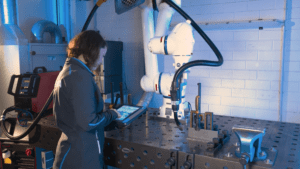
For many, the only concept of robotic automation that comes to mind is inspired from commercials showcasing expansive factory settings with dozens of large, fast-moving robot arms that are timed to conveyors. Throw in weld sparks flying, heavy metal guarding and flashing light beacons, and the overwhelming concepts of robotic automation can be quite intimidating.
While the combination of these robust machines and peripherals is often the most efficient option, the level of complexity and cost can be very high. This mingled with the resistance to change that companies sometimes deal with can also contribute to the hesitancy that many end users face where robotic implementation is concerned.
Automation Approachability
To help curb buyer reluctance, an ease of use revolution continues to permeate the industrial landscape, making automation more accessible than ever to manage labor shortages, process inconsistencies and more. A fresh mix of highly flexible, more affordable, user-friendly robots and tools — paired with intuitive technologies and feature-rich software platforms — is effectively shifting big picture ideas to real-world applications. Key among these are:
Collaborative Robots
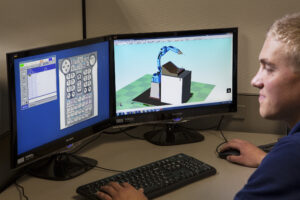
The ability to produce maximum quality parts quickly with minimal expense is paramount to keeping competitive for many small- to medium-sized enterprises. Thanks to a variety of technologies, including extremely portable and capable collaborative robots with industrial pedigrees, tackling tough issues quickly and more affordably is an attainable reality. Cobot designs with lead-to-teach capability, Power and Force Limiting (PFL) technology and IP67-ratings are enabling a range of tasks to be completed safely close to human workers. This includes arc welding without additional coverings or safeguarding (based on risk assessment). Ideal for supplemental manual welding or for rolling up to large heavy workpieces, cobots are also being installed in pre-engineered collaborative workcells. Extremely convenient, these portable workcells come complete with everything needed, such as arc flash protection and fume mitigation, to process small- to medium-volume runs.
Offline Programming
Integral for minimal downtime, the use of offline programming (OLP) brings programming to a virtual environment for the efficient deployment of a robot system. While the subject of programming a robot from a computer predates the machines themselves, new technology and applications have evolved. Utilizing a wealth of convenient and intuitive tools that allow many to forego the learning of a proprietary robot language, OLP provides a 3D representation of a robotic workcell that visually demonstrates the robot moving along its programmed path. Like CAD software, these PC-based platforms enable users to design, test and adjust a robot program before implementation on the shop floor. Tools have also been added to automate path generation with simple click-and-go inputs, automatically optimizing program sequence — with some suites modeling the look and feel of video games or editing software.
AI Systems
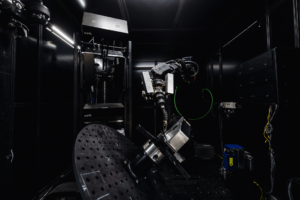
Giving robotic automation a huge boost are advances in artificial intelligence (AI), simulation and modular hardware for enhanced robot dexterity. While seemingly complex, AI-guided systems combine robot information and device data in real time to make informed decisions about how to change robot behavior, as needed. From robot speeds, pathing, tooling and external device characteristics, the computation power of AI can be used to analyze a wide variety of inputs to gain every bit of performance out of a robotic system. These can appear in basic forms for path manipulation, to more advanced forms that inspect product quality with complete path control using similar techniques to a skilled laborer and the human mind. In turn, this is facilitating a low- and no-code programming approach to robotics that reduces barriers to entry for many manufacturers looking to branch into robotics.
Intuitive Applications
Taking a page from the smart devices in our pockets, more companies and robot OEMs have been busy developing applications that run on tablets rather than a button-ridden teach pendant. These applications are also much like those on your mobile device, in which descriptive graphic icons and simple menu selections that guide you through a programming process. Some of these ease-of-use applications use other intuitive input devices that can mimic the tools used in skilled labor, recording positions for easy manipulation and execution from the robot tablet.
Robots-as-a-Service
Enabling highly efficient production environments while minimizing capital expenditures, Robots-as-a-Service (RaaS) complements the industry shift toward high-mix, low-volume production. From AI-guided systems to standard industrial or collaborative workcells, the RaaS model allows manufacturers to lease a robotic system and any peripheral technology that suits operational and budgetary requirements. Worker training and customer support may also be included as part of the low-risk service. While companies such as Ambi Robotics play in the supply chain and logistics space, others like Path Robotics offer Welding-as-a-Service (WAAS). These may be a long-term solution for manufacturers or serve as a springboard for diving deeper into capital expenditures of automation equipment. Either way, this concept serves to increase automation confidence, lower implementation costs and risks, enhance production scalability and enable easy maintenance.
Supplier-Managed Maintenance
Maintenance of a robot system is typically very minimal over the life of the robot. Simple scheduled maintenance, like changing grease, is fairly straightforward and is often done by the robot user. However, to make it easier for the end user, multiple companies, including robot OEMs can help manage and perform the maintenance for you. This may also result in extended warranties and more data on how to keep the robot running longer for ultimate return on investment.
From the development of well-thought-out robot designs to the adoption of advanced technologies, multiple innovations are bringing robotic automation to manufacturers of all sizes and industries.
Subscribe to learn the latest in manufacturing.