Optimizing Bonded Cutting and Grinding Wheel Performance
Technologies available on wheels ensure safe and efficient wheel use, which saves your operation time and money, and increases your shop’s productivity.
Posted: August 28, 2023
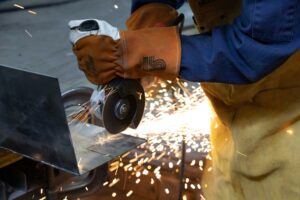
Cutting wheels and grinding wheels are versatile abrasive products used across many applications in fabrication, manufacturing, foundries, construction and numerous other industries. These consumables can have a significant effect on the overall productivity and efficiency of the operation.
Cutting wheels are a precision product used primarily for making exact cuts, whether on structural steel, pipe or plate. Grinding wheels are used when applications call for removing a large amount of material or to clean up welds.
These abrasive products are available in different grains and bonds. Grain types include aluminum oxide, zirconium, ceramic and silicon carbide, with each type offering different characteristics. For example, aluminum oxide provides toughness and good performance for cutting steel. Zirconia alumina is a self-sharpening, tough, durable grain that holds up well in a range of demanding applications. Ceramic grain is self-sharpening and offers cool cutting that does not require as much pressure from the operator. Products made with ceramic grain achieve maximum performance with high-power machines. It’s important to consider the needs of the application, the type of base material and the power capabilities of the tool being used when choosing the appropriate grain.
Benefits of Cutting and Grinding Wheels
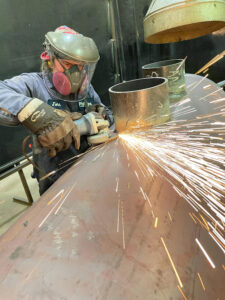
Cutting wheels are all about efficiency. Choosing the proper thickness and dimension of a cutting wheel for the job depends on the workpiece shape, dimension and tool available. For larger profiles, larger wheels are recommended. For thinner materials, thinner products are the best choice. Thinner wheels make a quick and cleaner cut. The thinner the wheel, the faster the cut. Thicker wheels are more stable and side load resistant.
Grinding wheels are thicker and contain coarser grains. Their main purpose is to be used over larger surface areas when there is a lot of metal to remove, and they offer a long product life.
Cutting and grinding wheels deliver numerous benefits, including increased productivity. With cutting and grinding wheels, there is often a trade-off between product life and cutting speed, but some products on the market today, such as the Tiger 2.0 product line from Weiler Abrasives, are designed to optimize both — so operations no longer have to choose. These wheels increase wheel life by up to 40% and match industry-standard cutting speed, allowing operators to increase time spent cutting and grinding and reduce changeover.
Understanding Wheel Life
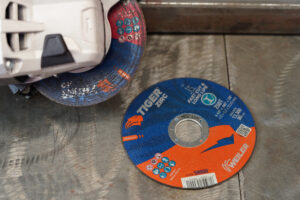
So how do operators know when a wheel should be changed? Typically, it’s time for a changeover when the product stops performing well or doing the work efficiently. Also, the diameter of the wheel gets smaller as it is used. When a cutting wheel gets so small that it cannot get through the workpiece anymore, that’s a sign for a wheel changeover.
Not using a wheel to its fullest life can cost money — both directly and indirectly. It’s throwing money away in the form of usable product, which increases an operation’s consumable spend. But it also increases downtime for the operator when changeover happens more frequently than necessary. From a sustainability perspective, it generates more waste to throw wheels away too soon.
The Tiger 2.0 cutting and grinding wheels from Weiler Abrasives include a visual indicator to ensure that every operator is getting the optimum product life out of every wheel. This marking diminishes as the product is used, finally wearing down to arrow indicators so the operator knows the product has been used to its full efficiency and can be changed. This takes the guesswork out of knowing when to change the wheel. It also helps ensure steady output and consistent wear of the wheels from application to application, which is important for production managers as they plan consumable inventory and budget. By removing the variables from the product’s performance, it becomes a dependable and reliable part of the production operation.
Tips for Efficiency and Optimized Results
In addition to making sure the operator is using a cutting or grinding wheel for its full useful life, following some best practices can help ensure consistent results and save time and money in the operation. Consider these tips for wheel use:
- Put safety first: Be sure to follow all proper safety procedures for using cutting and grinding wheels. All next-generation Weiler Abrasives cutting and grinding wheels will have a QR code printed on them that operators can scan for safety information.
- Choose the right product: First and foremost, be sure to match the speed and size of the wheel to the speed and size of the tool. Be sure the rpm rating of the tool doesn’t exceed the rating of the wheel. A cutting wheel with a depressed center (Type 27) can resist more side pressure and provide safety benefits. But a flat Type 1 wheel will allow the operator to perform deeper cuts.
- Use wheels for the application they are designed for: Don’t grind with a cutting wheel because the product was not designed for that. Grinding with a cutting wheel can lead to product breakage. Grinding requires a grinding wheel or a combination wheel. When switching between cutting and grinding applications, choosing a combination wheel will remove the time taken to switch between a cutting and grinding wheel.
- Watch the angle: Grinding wheels offer optimal performance when they are used at an angle of 25°-to-35°. Operators that grind at too flat of an angle often struggle. When too low of an angle is used, the bonds of the grinding wheel can break down, resulting in pieces chipping off. To provide a solution to this common challenge, Weiler Abrasives has developed an advanced formula for its newest wheels to prevent chipping. This provides more flexibility in the angle used, allowing operators to vary technique more without worrying about damage to the wheel. On the cutting wheel side, keep the wheel at a 90° angle to the surface. Using any other angle means the cut won’t be as clean and there is a chance of damaging the wheel. Thinner wheels are more sensitive to side pressure. Cutting wheels with a depressed center resist more side load.
- Apply proper pressure: When using a cutting or grinding wheel, there isn’t a need to push too hard. Use light pressure and let the abrasive do the work.
- Keep it moving: Don’t dwell with the abrasive in one spot for too long; this will heat the product up and can cause it to glaze over. Keep the wheel moving back and forth with a gentle motion to make the most efficient use of the product.
- Use the correct guard: Always use the guard designed for that product type. For example, when using a Type 27 wheel, be sure to use a Type 27 grinding guard, and when using a Type 1 cut-off wheel, always use a half-moon cutting guard.
Value of Consistent Performance
Choosing the right cutting and grinding wheel for the job and following best practices for using the wheels will improve results. Technologies available on wheels today can also help ensure safe and efficient wheel use — to save operations time and money and increase productivity.
Subscribe to learn the latest in manufacturing.