Three Common Myths About CMMs for Small Fabricating Shops
Coordinate measuring machines can help smaller shops stay competitive in a digital age.
Posted: August 18, 2023
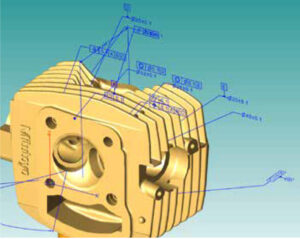
Regardless of what a shop manufactures or what material they work with, they’ll need to perform some level of quality inspection on the parts they create — not doing so can have negative consequences for the business. Coordinate measuring machines (CMMs) are extremely versatile tools that can not only help shops accurately and effectively take measurements, but also be more competitive.
However, many small machine shops might believe that integrating a CMM into the manufacturing process is simply too challenging. Between tight budgets, labor shortages and production demands, some shops may be hesitant to introduce something they believe may complicate things.
While CMMs are an investment, these three myths shouldn’t deter small shops from incorporating them into their operations.
Myth No. 1: Quality inspection is a waste of money.
A common misconception is that CMMs are too expensive to be practically viable for most small machine shops. But the reality is that many budget-friendly options are available. Most CMM manufacturers have a variety of lower-cost models and will work with you to determine which ones might best fit your budget and business needs.
Some shops might also worry that a CMM is too large for their floor or would require equipment to be repositioned to accommodate it, which can be complicated, expensive and time-consuming. However, this isn’t necessarily the case. Many manufacturers have smaller CMMs that can work within a shop’s existing footprint. And so-called “shop floor machines” are even designed to be easily integrated right into the assembly line, meaning they would have a reduced impact on floorspace.
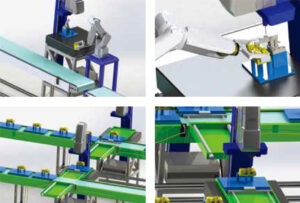
It’s important to understand that while CMMs may not directly contribute to the bottom line, they’re not a waste of money. In fact, you could argue that even small shops can’t afford to not have a CMM. If you’re making and shipping bad parts, that can have extremely negative ramifications for your business, reputation and bottom line.
Myth No. 2: Training employees to use CMMs is too challenging.
Employees at small shops often wear multiple hats, and when you factor in tight production timelines and labor challenges, managers might think that taking workers off the floor to train on a CMM simply isn’t worth it.
To be sure, training takes time. But most CMM manufacturers see themselves as being invested in your success and will provide robust training and support. Along with comprehensive in-person training, many CMM manufacturers will also provide helpful training materials and literature. Additionally, shops will have access to a variety of post-training support resources in case any questions pop up after the training period ends. The bottom line is that small shops won’t be on their own after purchasing a CMM.
As with any new machine, proper training is critical to ensure you can maximize the value of your investment. And although there may be an upfront cost in terms of training time, the payoff in time saved and greater operational efficiencies is more than worth it.
Myth No. 3: Automation isn’t realistic for smaller shops.
One of the major benefits of CMMs is that they can help automate many processes on the shop floor. But while automation has a variety of benefits, smaller shops might not think it’s realistic or feasible. After all, integrating robots and automating operations can be expensive and complex.
However, even small shops have opportunities to integrate elements of automation. For example, shops that produce high-volume parts or run almost continuously can be prime candidates for automation — and CMMs can enable that by eliminating manual inspections and automatically sending error corrections to the machine tool.
Any manual process, whether it’s creating handwritten reports or doing manual checks on a part, takes time and is inefficient. Eliminating or automating those processes by integrating a CMM into your operations can free employees to focus on more critical tasks. At the end of the day, automation can be a very attainable goal, even for small machine shops.
Making Your Shop More Competitive
As part fabrication and metalworking gets increasingly precise, CMMs will quickly become table stakes for machine shops that want to stay competitive — even small ones. Some customers are now requiring shops to own a CMM to provide peace of mind that parts are being produced to specification. And the automation capabilities that CMMS enable can further streamline operations, which is a huge advantage in today’s environment.
If your shop doesn’t have a CMM, it might be time to get one.
Subscribe to learn the latest in manufacturing.