The Economics of Scale: Coil-Fed Laser Processing
The advent of turnkey and completely integrated coil-fed laser processing systems promises to enable serious reductions in part costs.
Posted: September 29, 2023
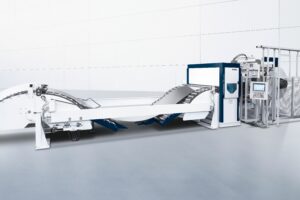
It’s not an unusual sight in the metal processing world to find cut-to-length blanking operations or stamping operations fed by sheet metal on rolled coils. When feasible, processing material coils instead of stacks of flat sheets can offer distinct economies of scale in the factory. The setup time for individual coils compared to individual sheets is rather long due to the size and weight of rolled material; however, this is more than offset by the elimination of material setup once the coil is loaded. One coil will keep feeding metal processing operations many times longer than a single sheet. Coiled sheet metal tends to be very competitively priced compared with the same weight of sheet metal that has been cut to size and stacked, so raw material savings can also be achieved by working from a coil. Still, starting from coil stock isn’t an approach very often applied to metal fabrication because of the handling involved and inherent limitations.
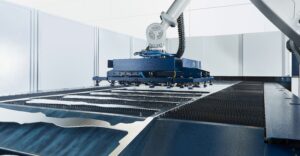
Due to these basic considerations, coil processing only becomes attractive in higher-volume, lower-mix metal processing operations. Unfortunately, feeding a cut-to-length line with a shear or a stamping press further limits the flexibility of operating from coiled material. These processes are really geared toward making very few varieties of parts, or even only one part. In many high-volume, low-part variety operations, flexibility is not a high requirement, but stamping can still be too restrictive to be economical. A factory that has to produce 30 different part numbers in a shift on a specific production line doesn’t need a huge degree of flexibility, but they probably need more than a stamping line can provide. Additionally, if the parts are subject to regular revision, stamping will be increasingly costly.
Highly Productive Laser Blanking from Coil
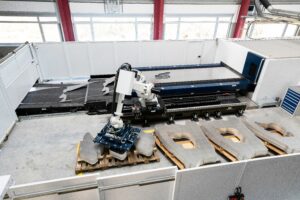
Enter the coil-fed laser cutting line. These systems combine the excellent material utilization possible with coiled sheet metal to the high degree of processing flexibility of flatbed laser cutting machines to make a system that is something of a hybrid. It is much more flexible than a stamping or cut-to-length line, yet still focused on providing excellent throughput and low cost-per-part in the high volume, low variety production environment. A coil-fed laser cutting system can process a wide variety of finished parts or sized blanks without any costly and time-consuming retooling, only a few minutes of reprogramming that can be accomplished parallel to the current production on the system.
A coil-fed laser system can be utilized to feed a limited variety of parts (really based on material type and thickness, because changeover is to be avoided) to downstream sheet metal fabrication operations, like bending and welding. In factories that are accustomed to processing very long runs in the same material type and thickness, but need the geometric flexibility of a laser, the coil laser could be an excellent strategy to ratchet down production costs. Whether the laser is required because of regular part revisions, or very complex part shapes, or just due to the tolerance and precision of the features, the coil laser system addresses these needs at a potentially much lower material cost than a dedicated sheet cutting machine.
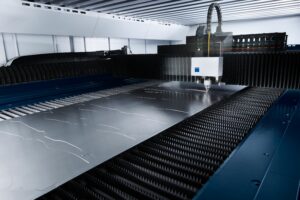
Laser coil lines could also be deployed as a blanking and sheet cutting system to feed other flat sheet processing operations. Take the case of a contract manufacturing facility with a large number of simultaneous cutting processes going on: laser cutting machines, punches, plasma cutters all following their own production plans, churning out parts. A coil laser system could be used to feed high quality sheet material to other parts of the factory, according to schedule, faster and more easily, than truckloads of stacked sheet metal can be delivered over the road by a vendor and unloaded from a trailer. A setup like this could allow a large-scale fabricator that requires high production flexibility to still see the benefit of starting from a coil.
In addition to feeding a laser cutting process directly from a coil, these systems can include an integrated leveling step as well. Passing the incoming material through a leveling process removes stress inherent in the material and tends to result in uniformly high-quality sheet metal. If material bowing during and after the sheet cutting process is a high concern, pre-leveling the raw material addresses this well. Leveled material also forms more consistently in bending operations and shows reduced deformation during welding compared to unleveled sheet metal. In this way the ability to integrate leveling into the sheet cutting process can truly result in substantial savings and reduced rework further down the production value stream.
Without the need for heavy customization, the installation and ramp-up period for such a line can be reduced dramatically. Standardization of the components in the coil-fed laser production line also makes programming and operating the system, not to mention maintaining it over the long term, much easier to manage. With the ability to have robotic part and blank sorting as a final step, these systems are also ready to be part of a highly automated smart factory. The advent of turnkey and completely integrated coil-fed laser processing systems promises to enable serious reductions in part costs in the right manufacturing setting and might just create a new business model for large-scale fabricators.
Facebook; Twitter; Instagram; YouTube; LinkedIn
Subscribe to learn the latest in manufacturing.