Addressing Common Concerns: Solutions to Support Operators Throughout the Welding Process
When you’re on the job, there’s bound to be a mishap from time to time. What matters most in those moments is the solution you choose to fix it.
Posted: January 24, 2024
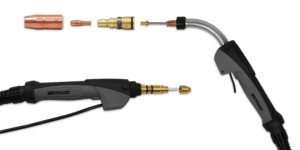
Welding is a very precise and complex job, and laying quality welds requires the right combination of equipment, consumables and settings. Depending on the industry and the workpiece itself, the variables required to do the job well may result in the occasional operational snafu. To help operators work more nimbly when a curveball is thrown their way, we’ve compiled four common concerns that arise during semi-automatic and automatic/robotic welding applications and the problem-solving solutions that can keep downtime to a minimum.
Welding process issue no. 1: burnbacks, erratic arcs and inconsistent wire feeding. These are arguably the most common issues a welder faces on a daily basis, and there are a couple different ways to arrive at a viable solution.
- Liner length
The first step is evaluating the liner. A welding liner is an essential piece of equipment in MIG welding. In fact, you can consider it the backbone of the whole system since it’s the conduit for the wire to get from the feeder to the weld.
Because the liner is such an integral component to the weld process, many times, any issue with the weld can be traced back to a problem with the liner or its setup. If you’re constantly experiencing erratic arcs, burnbacks or chatter, a common go-to solution is to change the tip. That will solve the problem temporarily, but there’s likely a larger (liner) issue at play. For the best chance of success, you need to Goldilocks the liner: It can’t be too long or too short. It needs to be just right; otherwise, you’ll for sure suffer the hardships of a low-quality weld.
An efficient way to fix incorrect liner length is with a locking liner system designed to address liner trim length errors and erratic wire feeding. Once installed, cut the liner flush with the back of the power pin. The liner is locked and aligned with the contact tip and power pin to provide a clear wire-feed path, reducing downtime caused by liners that are cut too short. Overall, there will be less bird-nesting, burnback and erratic arcs and more beads worth bragging about.
- Tip type and quality
If the liner is cut correctly, having the right tip will further help establish a stable and consistent arc, smoothly guiding the wire from the feeder to the arc. That being said, there’s an array of tips out there. Selecting one based on the application, while factoring in the right wire size and determining the right material, can alleviate a lot of weld quality issues. An accurately cut liner paired with the right tip is a one-two punch that will help optimize your equipment to its full potential, reducing downtime, minimizing the likelihood of consumables failing and mitigating weld failures or low-quality welds. Seemingly small tweaks can make big differences in productivity, weld quality and the lifespan of the consumables.
Welding process issue no. 2: hot hands. Welding is a hot job, and being aware of equipment duty-cycle ratings is critical to handling the heat properly. Paying attention to this equipment rating provides the operator with a clear understanding of the machine’s limitations, which is what will prevent it from overheating or failing during use. That being said, even if you’re interpreting the duty cycle correctly, there’s always going to be some heat in the handle (a big reason why a good pair of gloves is a must). However, if you’re experiencing more heat than usual — or more than you can stand — it may be time to look for a new handle design.
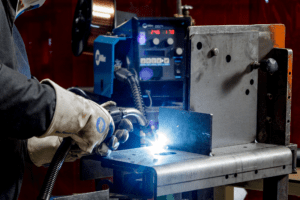
The application you’re working on is going to determine what type of handle to look for. There are plenty on the market, with pros and cons for each. If you’re welding with industrial equipment at high heats, a handle with high glass content is a good option because it provides better heat insulation. However, the higher glass content makes it more brittle, requiring more careful handling. If the nature of the work requires less intense heat, opt for something that’s more pliable and less delicate. With this option, the handle will be less heat-resistant, so its uses should align with the right type of work.
Another issue that arises in welding from the high temperatures is that the neck can get hot, transferring that heat to an operator’s guiding hand. To lessen the impact, it may be tempting to do whatever it takes to provide some insulation between the neck and hand: tape shop rags to it, cut a hose and apply that as a rubber barrier or even wrap the neck in multiple layers of tape. Not only are those options a safety risk, but you may inadvertently trap heat in the neck, causing it to fail. Instead, it’s best to seek out neck grips that are formulated to provide operator relief without sacrificing the integrity of the equipment (or safety of the setup).
Welding process issue no. 3: challenging weld positions. When the workpiece calls for out-of-position welds, using a flex, or rotatable, neck is particularly useful. This is especially true when confronted with confined spaces, complex joint configurations or hard-to-reach positions where a standard welding torch won’t deliver quality results. These specialty necks are made of bendable, heat-resistant materials like rubber or silicone to provide the flexibility needed to perform certain components of a job. Additionally, this flexibility can help alleviate operator fatigue since a more natural welding position can be maintained during the weld, and by extension, it’s easier to maintain proper torch-to-workpiece alignment to produce high-quality welds. While flex necks are beneficial in certain applications, they shouldn’t be used as your standard neck. They’re a more expensive investment and they tend to be more prone to ripping, tearing and burning. Those costs can add up quickly and negatively impact an operation’s bottom line if they’re routinely being replaced, so only using them on an as-needed basis is key.
Welding process issue no. 4: cable length. Tight tolerances are common in robotic welding, so investing in the right gun to meet those needs is important. If the cable length borders on being a bit too short, instead of investing in a whole new cable, try using a power pin spacer. It can provide the extra inches needed to reduce strain on the robot and allow for the workpiece to be welded properly. Over-fatiguing and/or over-flexing the cable could cause it to pinch off gas flow, cause porosity in the weld or result in premature cable wear. If the length is more than a few inches off, then you’ll need to replace the cable because power pin spacers are not intended for multiple connections to add length. The flip side to this is if the cable is too long, you may be able to cut it down to the right size, but if not, it will need to be replaced with the correct size. When choosing between the two options, it’s better to err on the side of a cable that is too short because there’s a more realistic fix in using power pin spacers.
When you’re on the job, there’s bound to be a mishap from time to time. What matters most in those moments is the solution you choose to fix it. Tools and products exist to help alleviate some of the most common concerns welders face while trying to lay the perfect weld, which not only makes the work better but positively impact efficiency as well.
Configure your MIG gun with the consumables and accessories that will provide more uptime and less troubleshooting.