Advanced Remote Monitoring and Control Technologies Transform Metalworking Applications
The emergence of new advanced remote robot monitoring and control capabilities in the fabrication and metalworking sectors marks a new era in combatting downtime, while protecting companies from cybersecurity risks.
Posted: January 3, 2024
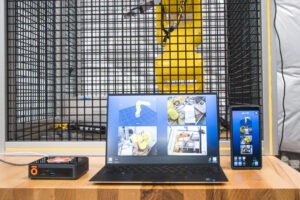
Unplanned downtime: two words that strike fear into the hearts of production managers everywhere. With production at a halt and losses mounting, finding a safe and effective fix quickly makes a huge difference to companies concerned about their bottom line.
Traditional approaches to fixing robot downtime are inefficient and costly. Integrators will travel onsite to fix the robot and get production up and running again, but by the time that happens the customer is down tens, if not hundreds, of thousands of dollars, or more.
It’s enough to put many small- to medium-size businesses (SMEs) off deploying automation altogether. Considering the inevitability of some form of robot downtime and the jaw-dropping costs associated with traditional methods of fixing robot downtime, the prospect of spending more on ongoing operational costs than on the initial robot investment is, understandably, a bridge too far for many small companies.
But what if there was a way to monitor robots remotely?
The Pandemic Spotlight
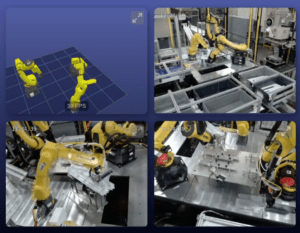
The Covid-19 pandemic highlighted the effectiveness of traditional remote robot monitoring technology, but it also placed a spotlight on the limitations of traditional systems.
On the plus side, the benefits of traditional remote robot monitoring software are now proven and understood: Companies can restart production faster, gain access to robotics experts more quickly, and reduce troubleshooting costs. The global market for remote monitoring and control systems was estimated at US$23 billion in 2020. By 2026, it’s expected to reach US$31.7 billion at a CAGR of 5.4%.
Consider a metal bending and forming application, where precise angles and forces are critical. Robot downtime can bring the entire production line to a halt. Remote monitoring systems can raise an alert, sending an integrator on their way to the workshop.
But the latest remote robot control system allows integrators to correct errors remotely. It also allows them to make adjustments to bending angles and force parameters, enabling quick fixes and seamless transitions between different metal types and thicknesses — all without leaving your desk.
Traditional Limitations
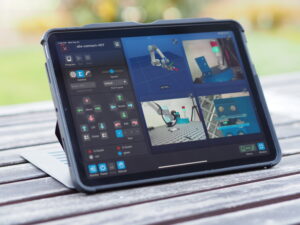
Not all remote monitoring and control systems are the same. Some provide monitoring only, which means integrators receive alerts but are no closer than that to solving the problem. Most provide a layer of analytics capabilities that allow companies to tweak their automation for better performance, using KPIs such as overall equipment effectiveness. Many systems, relying on the cloud, expose facilities to a plethora of industrial cybersecurity risks — and all the time and costs associated with managing and mitigating those risks.
If the pandemic showcased the benefits of remote robot monitoring, it also left many users, particularly integrators, wanting more. Receiving an alert is one thing, but what if integrators could remotely move a robot arm, thereby solving the issue from their desk rather than having to travel on site? Meanwhile, cybersecurity concerns left many users of remote robot control technology wondering whether they could access the robot in a safer way. On top of all that, physical safety requirements meant that remote robot control was either not available at all or limited to the point of uselessness.
What if there was a way to remotely monitor, diagnose, and control your robots without having to take on additional cybersecurity and physical safety risks?
Paradigm Shift
The latest remote monitoring and control technology addresses all those concerns. The new technology enables real-time remote access, monitoring, diagnosis, and correction of robot issues in ways that address very real concerns around cybersecurity and physical safety.
Consider an automated machine tending application involving a cobot that picks and places expensive metal parts while also operating the CNC machine itself. Downtime could be caused by something as simple as a part not being gripped properly. Instead of having to wait for someone to get onsite for such a small fix, the latest remote robot control system allows integrators (and end-users) to move the arm and gripper to correct the error — enabling a rapid return to production and saving many thousands of dollars in the process.
Cybersecurity and Workplace Safety
Consisting of several USB or IP cameras, a compute box and software, the new plug-and-play system provides 24/7 low latency video and data access to any robot cell. Once secure remote access has been configured, integrators can monitor and manage automation remotely from anywhere via any browser-capable device. When an error occurs with a robot, the system sends out an alert via that secure connection, completely avoiding the cloud in the process. If required, the robot can be remotely moved to correct an error, enabling a quick return to normal operations.
By using direct, secured connections, the new technology, which works on both legacy and new automation, protects metalworking facilities from a host of cloud-related cybersecurity risks, while ensuring data integrity and access control.
Physical safety is another key concern in metalworking and fabrication facilities — and until now, a major obstacle to the adoption of remote robot monitoring and control technology.
Material removal jobs, for example, such as sanding and polishing are repetitive, dangerous and hard to fill. Welding jobs are also harder to fill and bring their own set of safety hazards. This combination of labor shortages and ergonomic concerns has driven a surge of automation adoption in those application domains.
But until now, remote control of such potential hazardous automation was considered to risky for all but the most expert users and the most advanced setups. That’s no use to the vast majority of fabrication and metalworking shops, however.
The new technology enables remote robot control without violating the robot’s safety permissions and restrictions. This means that the velocity, acceleration, and joint limit settings on the robot are always obeyed when remote controlling the arm.
Whether your robot is feeding metal sheets to a machine press, drilling holes, or performing laser welds, safety is paramount and knowing that robot errors can be corrected remotely in a safe way is a gamechanger for the way robots are deployed in metalworking and industrial verticals.
Cui Bono?
Manufacturers benefit from improved analytics, and reduced error recovery time. SMEs benefit from lowered barriers to automation adoption.
Time management is a major issue for integrators, especially with demand for automation rising all the time. Many integration firms have to pass on opportunities for new projects due to limits on the way they traditionally handle robot downtime. Until now, that is.
The new remote monitoring and control system multiplies integrator productivity, freeing up time to take on new customers. When the time it takes to fix robot downtime is measured in minutes rather than hours and days, integrators can support additional customers without making any sacrifices in terms of quality.
And the industrial robotics sector as a whole benefits from technology that supports safe, secure remote robot monitoring and error recovery and makes automation economically and technically feasible even for the smallest companies.