Resistance Welders are Optimized for Performance, Productivity and Cost-Effectiveness
Economical and streamlined resistance welding equipment is offered in pre-engineered as well as customized solutions.
Posted: January 24, 2024
Be it spot, seam, projection, flash butt or rocker arm resistance welding, fabricators can count on manufacturers of these systems to deliver solutions that will meet their specific applications.
Resistance Welders Available in Pedestal-Type, Projection and Multi-Gun
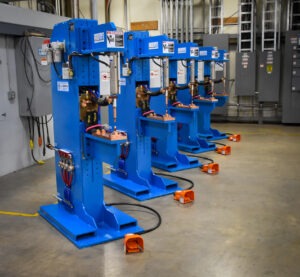
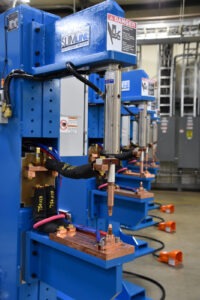
Originally conceived to compete with low-cost imported machines, T. J. Snow Co.’s (Chattanooga, TN) SlimLine brand of resistance welders has proven to be very popular through the years. The durable, compact, space-saving design makes SlimLine machines a cost-effective and efficient resistance welding solution. And built-in forklift pockets make it easy and safe to move the machines.
All SlimLine components are stocked at our Chattanooga location, and we can assemble one to your specs in record time. And now, with many pre-engineered variations from which to choose, customers can zero in on the ideal machine for their application, all while saving money when compared to other options.
The basic single phase AC horn-style SlimLine is a vertical action resistance spot welder with a lower arm and ejector-type electrode holder. An arm brace ensures that deflection is not a problem. Weld forging force is supplied with a dual or triple piston air cylinder instead of an expensive ram.
The platen-type SlimLine is identical to the horn-style except that a copper tooling plate is substituted for the lower arm. This SlimLine model is often tooled to locate and weld nuts and studs, which are often fed automatically.
If more than one weld is needed per part, a natural progression of the SlimLine frame design is to widen the crown and platen to accommodate two or even four weld guns. If offset electrode holders are needed to access weld locations, a ram-type SlimLine is available.
Other options include a three phase MFDC power supply and an electric servo force delivery system substituted for the standard pneumatic cylinder.
New, Ready to Ship Resistance Welders
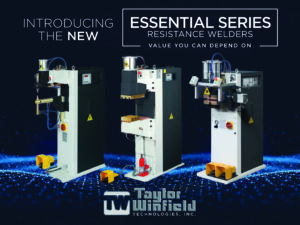
Taylor-Winfield Technologies (Youngstown, OH) now offers a full line of ready to ship, economically priced resistance welders. The Essential Series offers many configurations for spot/projection, seam, rocker arm and flash butt welding. They are a packaged off-the-shelf, economically priced option for resistance welding sheet metal and other parts production. With short lead times at an affordable price, the Essential Series resistance welders are designed to get the job done with minimal investment.
Taylor-Winfield will also continue to offer the legacy Signature Series line of resistance welders that have proven their worth for decades. Options for customizing the Signature Series of welders for specific applications include throat length, welder configurations, transformer size, control options, cylinder size, welder stroke, platen size, fast follow-up, custom tooling, ram configurations, robotic integration and more.
If high production output with minimal downtime is important, Taylor-Winfield has the welding solution to meet your needs. Contact us today at sales@taylor-winfield.com or (330) 259-8500 to discuss your application.
AC Inverters Provide Better Control Compared to Standard AC Welders
AMADA WELD TECH Inc. (Monrovia, CA), a leading manufacturer of resistance welding, laser welding, marking, cutting, and micromachining equipment and systems, highlights its MIB-300A and MIB-600A AC Inverter Welding Power Supplies, which offer increased control resulting in more exact heat input and better quality welds as compared to traditional AC weld controls.
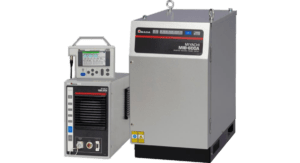
The AC inverter uses inverter technology with pulse width modulation to produce and simulate an AC waveform. Unlike AC welders that use line frequency and depend on well-regulated facility power, the AC inverter can produce an AC frequency from 50 Hz to 500 Hz allowing more precise energy delivery in less time, is not affected by line voltage fluctuation, and provides a balanced three phase load.
The MIB-300A and MIB-600A feature secondary constant current control, up to 20 pulses per weld and the ability to set upslope, downslope and weld interrupt. Up and down slope improves energy input into the welded material and interrupt stops the flow of current if displacement breaches a set level, preventing over welding.
MIB-300A and MIB-600A may be used with the same transformers and weld heads as standard AC welders. With max output currents of 20,000 and 40,000 A respectively, the units may be used for a variety of different welding applications. Common uses for AC inverters include sheet metal welding, wire compacting and brazing.