Self-Indexing Infeed/Outfeed System Enables High-Mix Machine Tending
Machine tending with a cobot and self-indexing infeed/outfeed system enables true lights-out manufacturing for high-mix, low-volume production.
Posted: January 3, 2024
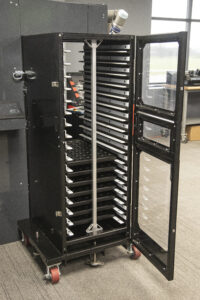
A major labor shortage was already in place before the Covid-19 pandemic hit. It was difficult to replace retiring workers. Then the pandemic affected the workforce, predominantly middle-aged workers, leading to decreased productivity as a result of shutdowns.
There were two almost fully staffed shifts at the PBC Linear machine shop before the pandemic. Operators were trained to load and inspect parts. However, during the pandemic, many operators were forced to stay home to care for family members infected by Covid-19 or to recover from it. The labor shortage made it a struggle to find and retain qualified workers once demand began to grow again.
The primary challenge was reliance on direct labor for productivity. Each process required more hands, and idle machines without operators were problematic. The qualified talent pool was shrinking, and training new employees was inefficient and expensive, causing a widening talent gap.
Engineering a Machine Tending Infeed/Outfeed System for Cobots
Exploring automation solutions in response to the labor shortage and increased demand revealed that collaborative robots (cobots), gaining in popularity for material handling and machine tending applications, promised to be a solid investment.
When designing the infeed system for a cobot work cell, it’s important to consider how parts will be transported to the cell and how the cobot will pick them for reliable insertion into the machine. With manually operated machines, parts often arrive at the work cell in a bin, all mixed together. While not a problem for people, unstructured bin picking can be difficult for robots.
Robots have an easier time grasping parts when there is some space around each part. Therefore, it is helpful to place raw parts on simple trays before giving them to a robot. Our manufactured 3D printers gave us the capability to print custom part trays that could be quickly swapped out in front of the cobots.
However, to achieve longer production runs, we eventually turned to thermoforming, which allowed more consistent replication of high-tolerance trays. These trays ensured that the cobots could pick up parts accurately and reliably without the complexity of an added machine vision system.
Cobots Require Frequent Human Intervention
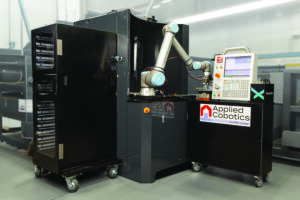
Soon after installing the cobot and tray systems, we encountered serious challenges. Despite a limited work scope of picking parts, the cobots required constant human intervention. Workers had to restock part trays every 30-to-60 minutes, which reduced efficiency and undermined the benefits of automation.
To achieve an unattended, lights-out solution, we developed an automated part storage and retrieval system. This mobile self-indexing infeed/outfeed system, called the Cobot Feeder, includes a base storage and retrieval unit with a UR cobot pedestal. An enclosed steel rack dunnage tower with a 17-tray capacity safely stores up to 50 pounds of material.
The system also includes an HMI touchscreen display for easy infeed/outfeed control, Ethernet IP, Modbus, and standard UR cobot communications. The Cobot Feeder self-indexing infeed/outfeed system recently received UR+ partner certification, which allows any UR cobot controller to control the Cobot Feeder. This UR capability simplifies operation, minimizes the chance of operator error, and improves productivity because operators can now control infeed/outfeed through the cobot control pendant interface.
The Cobot Feeder also includes the Flexxbotics machine interface, part of the Flexxbotics solution, specifically designed to enable robot-driven manufacturing at scale. As part of the UR+ ecosystem, the Flexxbotics solution seamlessly connects and coordinates robots and cobots with existing automation equipment, such as process tooling, workholding devices, the self-indexing infeed/outfeed system, and OT/IT systems enabling autonomous process control.
The Flexxbotics solution bridges the gap between the self-indexing infeed/outfeed system, the cobot, process tooling, and the workholding device. For example, when the indexing system unloads a tray of finished parts and loads the next tray containing different parts to be processed, the Flexxbotics solution communicates the part program to all four machines, enabling complete work cell changeovers without operator intervention.
High-mix, Low-volume Production
Modern manufacturing is highly competitive, and companies are looking for innovative ways to improve production. Traditional manufacturing methods are difficult, costly, and time-consuming to use when making precision parts in small batches.
The self-indexing infeed/outfeed Cobot Feeder was first used to support a machine-tending cobot that loaded variously sized linear plain bearings into a grinding operation. The self-indexing infeed system keeps ample supplies of bearings of various sizes within reach of the cobot. The cobot continuously loads bearings onto a ramp fixture, from which the bearings roll into the grinding machine magazine, increasing shop efficiency.
It was previously workers’ responsibility to load the bearings manually. Now, the cobot helps them avoid repetitive strain injuries as they do not need to reach above their heads to insert bearings into the opening of the ramp fixture repeatedly. Furthermore, the Cobot Feeder ensures that cobots always have a supply of bearings for uninterrupted operation, thus freeing workers to focus on other tasks, such as quality control.
Cobot Feeder Benefits
Because the cobots and the Cobot Feeder self-indexing infeed/outfeed system were installed three years ago, the manufacturing plant has experienced improved efficiency and safety. It was the integration of the Cobot Feeder with the cobots that led to a transformational effect.
The company increased its employee value by cross-training. That, combined with adding interesting new technology such as cobots and the associated automation, and shifting work from manual labor to managing automated cells, attracted younger employees. Thanks to cobots performing dull, dirty, and dangerous tasks, we now have a safer and more engaging workplace that’s more appealing.
ROI of the Cobot Feeder Self-Indexing Infeed/Outfeed Solution
A high return on investment was realized through the Cobot Feeder and the cobots. A two-month return on investment was achieved by maximizing productivity on the machines and operating them 24/7. As demonstrated by the Cobot Feeder ROI calculator, the system is cost-effective and can generate substantial profits.
Collaborative Automation Revolutionizes Manufacturing
By linking communication between cobots, the self-indexing infeed/outfeed system, process tooling, workholding devices, and OT/IT systems, connected automation has transformed operations and demonstrated the potential of collaborative robotics in modern manufacturing. In addition to alleviating labor shortages and increasing productivity, maximizing technology use has created a more engaging and safer work environment. This innovative solution has not only improved the company’s efficiency and profitability but has also made jobs more attractive to young workers.
Originally developed for internal use, the Cobot Feeder is now an available product to purchase for other manufacturers. Combining a Cobot Feeder, cobots, process tooling, and workholding devices with the Flexxbotics solution, manufacturers have the tools to solve problems related to material handling and labor shortages while delivering enhanced returns on investment.