Significant Developments in Grinding Machine Applications Open the Door to New Possibilities
Efficient grinding machines play crucial role in producing innovative and superior products.
Posted: January 3, 2024
High speed, highly accurate and user friendly grinding machines offer precision and versatility, producing favorable outcomes across a range of industries and applications.
Machines Offer Flexibility and Automation
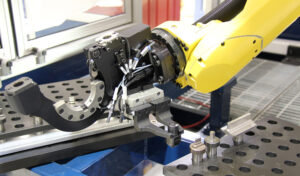
ANCA CNC Machines (Wixom, MI) enable you to beat the competition to the punch with its TX7 and TXcell Linear for your production needs. ANCA has developed several accessories and options that meet the needs of the punch grinding application.
- iPunch: dedicated punch programming software gives you complete flexibility on punch geometry and grinding process parameters.
- iBalance: on-machine wheel balancing software.
- Rotary wheel dresser units fully supported by ANCA dressing software deliver in-process dressing to keep your wheels running true and sharp.
- Auto adjusting coolant nozzles that change position as the wheel diameter reduces.
What makes punch grinding on ANCA TX7 Linear so different? Starting with the basics, TX7 Linear is a 5-axis grinding machine, compared to the 3-axis grinder more traditionally used for punch manufacture. Having these extra degrees of freedom on your grinding machine translates to greater freedom in what applications you can put through it.
In the case of punch manufacture, a traditional punch grinding machine would have been capable of grinding only the outside form of the punch with a single wheel. The TX7 Linear now offers you so much more. Punches will typically have a series of separate machine operations that need to be performed to complete the tool.
What operations on the tool require all the additional investment and effort? After OD grinding a punch may require a roof-top or whisper shear on the punch. Additionally, a tool index mark or feature may also need to be included near the shank of the tool. Typical punches include a single radius dressed into the grinding wheel to create a gentle transition between punch section of the tool and its shank, but in some cases, additional reinforcement radii are added. Finally, there is the inclusion of ejector holes in the end face of the punch that require not grinding but drilling operations. With two-wheel packs available on the 5-axis TX7 Linear, undertaking several of these operations in a single setup is now possible. But take the next step to a TXcell, with its offering of nine-to-24-wheel packs, and all these operations can now be done in a single setup, something that was never possible on a standard punch grinding machine.
The TXcell robot used for changing wheel packs is also used for automated loading of tools, which means you can keep it running for those unattended shifts. Having more than one wheel pack on the machine brings other benefits too. By using different roughing and finishing wheels, grinding operations can now be optimized for stock removal or fine surface finish. The TX7 Linear and TXcell Linear are also ideally suited to the use of CBN grinding wheels.
5-axis Machines Combine Milling with Jig Grinding Capabilities
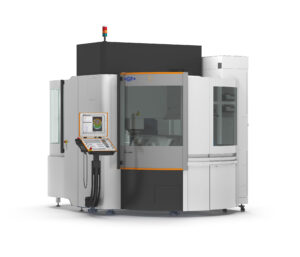
GF Machining Solutions’ (Lincolnshire, IL) Micron MILL S/X Series 5-axis machines feature a two-in-one combination (milling and jig grinding), along with extremely high machine dynamics and consistent thermal stability and accuracy ensure significantly reduced part and mold processing times, and improves quality while providing the shortest machine ROI possible.
The MILL S/X Series includes the 400/400 U, 500, 600/600 U and 800 models, all featuring linear, rotating and swiveling axes. The machines allow users to clamp parts once and perform both milling and grinding operations to not only shorten cycle times but to also eliminate the risk of stacked tolerances from having to transfer parts from one machining process to the next. Linear axis motors and rotary swiveling torque tables provide either a smooth or dynamic milling process for machining accurate parts during short, medium and long milling operations.
For further machining optimization, MILL S/X machines are equipped with the Operator Support System extreme smart machine software module developed and patented by GF Machining Solutions. The module lets users select various settings that take into consideration the machining priorities and the machine parameters.
As a standard, the machines also feature Automated Machine Calibration software that allows users to calibrate their machine in minutes as opposed to hours. This reduces downtime between cycles while with the push of a button ensures stable, long-term precision needed for high-quality parts.
To further reduce processing costs and boost machining accuracy, the Econowatt smart machine module on MILL S/X machines makes it possible to set the machine in a configurable standby and wake-up mode to achieve the perfect thermal conditions for the start of production and to reduce energy consumption.
On the grinding side of the MILL S/X machines, a grinding tool dressing spindle is mounted next to the 3-axis machine tables at a slight incline to allow dressing of any complex grinding tool. The dressing spindle speed adjusts from 3,000-to-20,000 rpm for added dressing flexibility, efficiency and reliability.
For lights-out production, the MILL S/X (U) model machines are easily automated with different pallets, magazines or third-party automation. For automated tool changing, GF Machining Solutions offers simple double-row disc magazines or automatic tool changers. Tool storage capacities range from 15-to- 308 tools, depending on machine model and tool type.
CNC Jig Grinder Offers Flexibility, Accuracy and Operator-friendly Operation
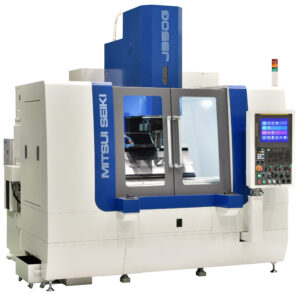
The high-performance Mitsui Seiki (Franklin Lakes, N.J.) J350G jig grinder’s infeed stroke is the largest available among competing machines, with a U-axis range of -3 mm to +50 mm relative to the spindle center. This provides the flexibility to grind small and large diameter holes, as well as multiple features, using a single wheel in a continuous, automatic mode.
“Jig grinders are the most common machine type in small shops and large factories,” said Bill Malanche, Mitsui Seiki USA’s COO. “Most have at least one. Our CNC J350G provides the ability to grind a wide variety of features automatically, without changing wheels.”
To maximize accuracy, the X- and Y-axes of the J350G are hand scraped and incorporate needle roller bearings. Left and right slide ways are V-F flat shaped, and the Y-axis (spindle head motion) is V-V shaped to maximize positioning accuracy. The machine bed consists of a thick, highly rigid casting supported by three level points, assuring consistent perpendicularity and parallelism. Built-in, custom-designed Heidenhain scales contribute to +/- 0.0007 mm accuracy on the X-, Y- and Z-axes.
Table longitudinal travel (X-axis) is 500 mm, transverse travel (Y-axis) is 300 mm, and quill travel (Z-axis) is 100 mm. Maximum distance from the table surface to the grinding spindle nose is 450 mm. The machine’s work surface is 700-x-350 mm and permissible table load is 300 kg. Table and saddle maximum rapid feed rates are 2,000 mm/min and grinding feed rates are variable from 0.1 mm/min-to-2,000 mm/min. The standard high-frequency spindle motor operates from 9,000-to-45,000 rpm. A variety of spindle motor options include an air-turbine motor with 75,000 rpm capability.
High Production Performance Grinder Handles Demanding Applications
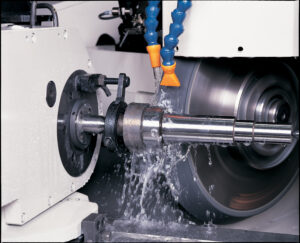
NIDEC Machine Tool America LLC’s (Wixom, MI) PD32 cylindrical grinder delivers exceptional performance for high-speed, high-production grinding applications. With grinding wheel peripheral speeds of up to 60 m/s, an optional 80 m/s configuration, and rigid construction, the PD32 excels in precision and productivity across various industries. The grinder’s combination of exceptional speed, precision, flexibility, user-friendliness, and power makes it an ideal choice for manufacturers seeking to optimize their grinding processes and achieve superior results.
Regarding speed and precision, the PD32’s highly rigid ball bearing wheel spindles ensure stable and accurate grinding even at high speeds, minimizing vibrations and thermal deformation. When it comes to the flexibility and automation on the PD32, the narrow machine width easily integrates into automated cells and production lines. A fixed table design provides a stable platform for workpiece handling and automation; and there are three models with different center distances (500 mm, 1,000 mm, and 1,500 mm) to accommodate a range of workpiece sizes.
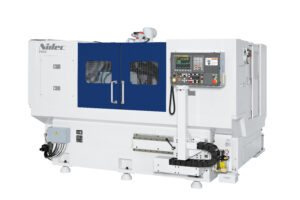
The PD32 handles both shaft and cylindrical parts, offering a versatile and user-friendly solution for various grinding needs. Plunge grinding with a wide grinding wheel enables efficient finishing of multiple surfaces simultaneously. The machine handles components weighing up to 150 kg. A graphical operation screen offers easy programming and workpiece shape definition; and conversational graphic software simplifies data input and makes the machine powerful and flexible.
The PD32 comes standard with an 11 kW high output motor to power demanding grinding applications. The standard 120 mm grinding wheel width (optional 145 mm) enables high-speed, single-shot heavy grinding.
www.nidec.com/en/nidec-machinetool/
Grinding Machines Produce High-quality Bearings
Starrag USA Inc.’s (Hebron, KY) Berthiez RVU grinding machines are continually popular, especially in both the aerospace and energy sectors. Even the smaller capacity (47” table) Berthiez RVU grinder can utilize ‘double’ carriages to cut overall grinding times by up to 30% by having two spindles cutting simultaneously on the same workpiece.
Berthiez machines also offer users the ability to turn and mill as well as vertical grind in a single setup — with no relocating for successive processes. Time is saved and any potential repositioning errors are avoided — thanks to four-station turret positioning capability and a table run out of just <2 micron.
Unprecedented user-friendliness via the Berthigrind software suite is uniquely programmed for each application and is accessed by the Human Machine Interface.
The success of Berthiez grinders in meeting the demand for micron tolerances on bearings for wind turbines, for example, is mirrored on bearings of similar material and hardness in other industries: for instance, aero engine shaft bearings up to 24” diameter and weighing 2.65 pounds; and large roller bearings for mining/cement industries equipment, measuring up to 47” diameter and weighing up to 2,205 pounds.
The RVU range of grinders have naturally evolved, particularly to meet the needs of global manufacturers of tapered, spherical and cylindrical roller bearings of between 39”-and-236” diameter as used in aero engines and energy plant — for example, bearings that are used to drive the rotor in a wind turbine, or position the nacelle and its rotor blades — with machines having table diameters of up to 236 inches, spindles rated from 34-to-67 hp and tables able to accommodate workpiece heights of 31” and weights of 35,274 pounds.
Such high-precision, high-performance demands dictate extreme machine rigidity, and Berthiez machines feature cast iron construction and temperature-controlled spindle and base, plus scraped linear guideways and hydrostatic table with torque motor, as well as dynamic spindle stiffness (electro spindle ——optimized specifically for bearing machining). There is also a choice of large range of water-cooled grinding spindles, according to the type of grinding wheel used and dimensions.