Advances in Welding Technology
Breakthrough developments display ongoing innovation in the welding sector, which leverages technologies such as AI and cobots.
Posted: February 16, 2024
The integration of tools such as AI, vision systems, cobots and easy-to-use software is transforming welding activities, making adjustments in real time, and where cobots are self-programming their weld paths. These innovations continue to level the playing field for small and medium-sized businesses that want to explore or expand the use of automation, cobots and other technologies.
Collaborative Robot Arc Welding Package
ABB’s (Auburn Hills, MI) GoFa™ Collaborative Robot Arc Welding Package is a breakthrough solution that simplifies creating and executing welding sequences, empowering first-time robot users to create high-quality welds without the need for in-depth knowledge of robot programming.
The collaborative robotic welding package is designed for small to medium size enterprises, fabricating shops and first time users of robotic welding equipment. The package makes it easy to change from part to part and is well suited for both low volume, high mix, and high volume, low mix operations. It can be used with power source equipment from any of the major suppliers. The compact and lightweight package contains all the components that are needed to quickly set up and begin welding.
A primary component of the welding package includes the GoFa Collaborative Robot, which is capable of handling heavier payloads for enhanced productivity and flexibility. The Easy Teach Device uses lead-through programming and interactive buttons to determine weld points. Users can automatically generate programming code by simply guiding the robot’s arm along the welding path.
The Wizard easy programming software is a key component of the package that makes it easy to program robots quickly and easily. With its simple graphical blocks, the software allows first-time users to program robots within minutes without specialized training.
Scanning Weld Heads Extend Precision Welding Capabilities
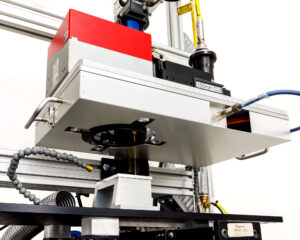
AMADA WELD TECH, Inc. (Monrovia, CA) a leading manufacturer of equipment and systems for welding, marking, cutting, sealing, and bonding, has announced a range of galvo scan heads for precision laser welding applications. Common usages for these scanning heads include point-to-point positioning for multi-point welding, shape welding for hermetic seams, and beam weaving to increase weld width.
Point-to-point positioning is frequently employed where multiple welds are needed over a small area, for example, electronic connector leads. The jump speed is nearly instantaneous compared to either traditional motion stages or robotic motion and can dramatically decrease cycle times.
In contour welding, galvo scanning heads are adept at steering the laser beam in an XY plane to create a seam weld of any programmed shape. This is commonly used for electronic package welding, where a specific motion is necessary to create a hermetic seal, and for lap welding configurations where additional weld contact is required.
Wobble is an extension of the seam welding application, in which the scanning head “wobbles” the beam in a small area to increase the melt pool. This improves the manufacturability of parts with lower tolerances on fit-up between the parts.
The galvo scan heads all feature advanced, intuitive software dedicated to welding, and a configurable pattern to adjust for part geometry and enhance weld performance. An integrated safety shutter ensures a safe work environment for operators.
The heads work with lasers up to 3 kW and field sizes up to 100-x-100 millimeters. Integrate with a linear stage motion to weld at different workpiece heights or add a wobble to linear motion for the accommodation of tolerances in fit-up for seam welds.
Next-gen Welding Platform for Heavy Industrial Welding
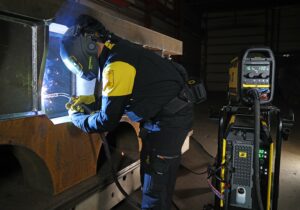
ESAB Welding & Cutting Products’(North Bethesda, MD) Warrior® Edge 500 CX multi-process power source system makes it possible for both new and experienced welders to achieve excellent welding results without a complex setup process. It has built-in connectivity and comes with a subscription to the InduSuite WeldCloud Fleet online software application.
The Warrior Edge 500 CX has a rated welding output of 500 amps at 60% duty cycle for synergic MIG/flux cored, pulsed MIG, Stick, gouging and Live TIG. It features the company’s next-generation digital control electronics for more controlled arc starts and greater arc stability to minimize spatter.
The SPEED mode creates a more focused arc by taking a conventional spray transfer arc and overlaying a modified pulsed MIG wave form on top of it. Benefits of the SPEED mode include improved control at higher travel speeds, reduced spatter, deeper more focused penetration in fillet welds and the ability to weld in more narrow grooves.
The Warrior Edge integrates with InduSuite applications such as WeldCloud Fleet and WeldCloud Productivity to connect data, machinery and processes to optimize fabrication workflow. WeldCloud Fleet enables users to manage welding jobs across a fleet of equipment at one or multiple locations, saving hours of time.
Vision System Sets New Standards with Enhanced Robotic Weld Grinding
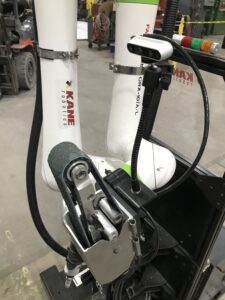
Kane Robotics (Austin, TX) has harnessed the transformative power of artificial intelligence (AI) with visual sensors that replicate the human eye, assessing uneven surfaces and enabling its collaborative robot (cobot) to make real-time adjustments in material removal operations.
“Thanks to AI, we can now teach a cobot to flexibly respond to changes in surfaces based on what it ‘sees’ through a camera attachment,” said Arlo Caine, Kane’s robotics engineer who spearheaded the GRIT Vision System. “The cobot world hasn’t seen this before.”
The new GRIT Vision System expertly manages tasks such as sanding, grinding and finishing in the manufacturing process, thanks to a high-speed camera and AI-driven computer vision integrated with Kane’s GRIT cobot solution.
A human operator sets up the cobot and attaches the necessary tools for the weld-grinding process, then monitors and adjusts the process through a live custom interface. Next, AI takes over. Using the camera, the vision system sees uneven surfaces on a weld or seam. Thanks to rapidly learning AI, the system alerts the cobot’s robotic arm and steers it accordingly.
GRIT Vision System was first introduced at the Paul Mueller Co., a Missouri-based global manufacturer of stainless steel tanks and equipment, which needed a solution for seamlessly grinding welds on large steel tanks used in the dairy, food, brewery, beverage, pure water and pharmaceutical industries. GRIT’s AI software performs live object detection, ensuring accurate tracking even as the weld seam disappears during rotation. When faced with imperfect welds, the system proved it could be taught to detect variations and refine its grinding accuracy.
At the Paul Mueller Co. the GRIT cobot does the tedious and strenuous work of holding the grinder. The vision system manages the tiring task of tracking large seams for long periods. Finally, a human operator sets and adjusts the force level most suitable to the chosen abrasive, grinding speed and number of grind passes to achieve the required finish.
While originally developed for weld grinding, the groundbreaking GRIT Vision System is compatible with various robotic components and customizable for diverse applications, from polishing aerospace parts to sanding furniture.
Smart, Self-programming Robot Sets Its Own Weld Path
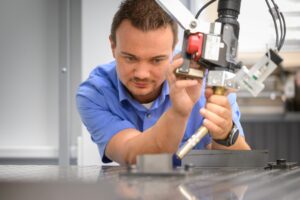
TRUMPF (Farmington, CT) has introduced new sensors that enable its arc welding robot to program its own weld path. The robot makes use of TRUMPF’s new smart seam-tracking technology, which the high-tech company developed in collaboration with the Fraunhofer Institute for Manufacturing Engineering and Automation IPA. Housed in the head of the welding torch, the sensor automatically calculates the weld path for each part.
With conventional welding robots, production workers program a new weld spot into the software each time they want the robot to change direction. This can be time-consuming, especially when it comes to complex parts with many curves or corners. Fortunately, the new smart seam-tracking function makes the process simpler. All the user needs to do is to place the welding robot in the start position, and the technology takes care of the rest. The robot uses the sensor to determine the weld path automatically. The system software quickly calculates the weld spots and creates the welding program for the part. The robot is “good to go” in a matter of seconds, even for complex parts such as spiral arcs. The intuitive user interface can be used to carry out a wide range of welding tasks, such as sealing runs and identical weld seams.
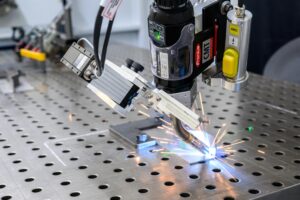
Components for wind turbines and screw conveyors for the animal feed industry are just two examples of areas that can benefit from this innovative and efficient method. Starting in February 2024, Smart Seam Weld Tracking technology is available as an option on new TruArc Weld 1000 arc-welding machines and may be retrofitted to some newer TruArc Weld machines with CMT (Cold Metal Transfer), an optional technology package that ensures high process reliability and energy-reduced welding with fewer weld spatters and reduced distortion.