Combilift Transforms the Storage and Handling of Loads in the Metalworking Sector
Whether it’s optimizing warehouse space, improving efficiency in handling large or unconventional loads, or any other material handling challenge, Combilift has the solution for you — or can build one.
Posted: February 20, 2024
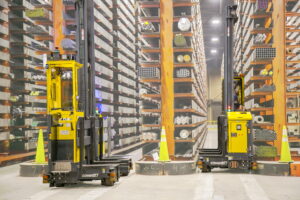
Combilift made history with its world’s first multidirectional C8000 three-wheel, all-wheel drive forklift, released in 1998. In the fall of 2023, Combilift once again made history with the launch of the world’s first autonomous side loader, the Combi-AGT, which has the option for manual operation.
That spirit of innovation keeps things exciting at this Irish materials handling manufacturer, which is a global leader in manufacturing multidirectional forklifts, as well as a leader in providing long-load handling solutions. The company’s global headquarters is located in Annahagh, Monaghan, Ireland, with its U.S. headquarters located in Greensboro, N.C. Greensboro is home to parts distribution, technical support, a help desk and administration. There are also 20 to 25 sales and technical support staff serving North America.
Innovation runs deep in the DNA of Combilift and keeps co-founders Martin McVicar (CEO) and Robert Moffett (technical director) thriving, working with customers and employees to develop cutting-edge solutions to move loads safely and efficiently.
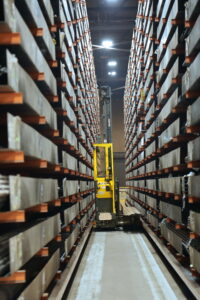
In 2023, a highlight in celebrating 25 years in business focused on Combilift’s launch of five new products: the Combi-LC Blade, Combi Connect, the Combi-AGT, the Combi-CUBE and the Combi-CB 155E (the last three are electric models). These groundbreaking products underscore the company’s dedication to addressing the unique material handling challenges faced by various industries.
Combilift’s core product lines are based around three concepts, said Paul Short, president of North America for Combilift. Those concepts are that Combilift’s products will increase and improve safety for the customer, increase storage space, and enhance production efficiencies.
Core product lines include a number of multidirectional products for handling long loads. “It will help reduce the aisle space required to store long material, whether it is steel beams or bar stock, and traveling indoor-outdoor,” Short said. He said Combilift’s warehouse product features the Aisle-Master for working with 48” deep pallets in aisles as small as 72”.
“We also have our Straddle Carriers, including the Combi-MG line, which is for handling full trailer loads of steel or fully completed air conditioning units or jet turbines — whatever it may be,” Short said. “And then we’ve got our Pedestrian Stackers product line, which has been used a lot in production areas in cell assembly or cell manufacturing, food processing and end-of-line production.”
Short said the Combilift team takes a holistic view of how materials are flowing within a customer’s facilities, from inbound raw material to storage, production and ultimately where the product ships from, as opposed to just reviewing the way a regular forklift moves a load from point A to point B.
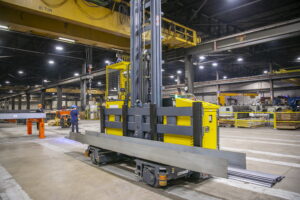
Providing value-added services such as the best warehouse and facility layouts and other recommendations is an important part of Combilift’s success, just as much as developing customer-driven products. For instance, the Combi-AGT is a four-wheel electric stand-on autonomous dual- operational side loader for long loads. “You know, we’ve been working in the metal fab industry from our inception,” Short said. “They’re obviously handling a lot of long loads and a lot of heavy loads, which suits our multidirectional products and our side loaders.”
Short said that Combilift’s steel service center and metal industry customers continue to detail how finding operators to handle long, raw materials has been a pain point over the years. Customers were experiencing the benefits of automation in their production equipment; however, moving raw materials from receiving to storage had not been as efficiently automated. Customers were seeking automated solutions for handling long loads and other unconventional materials, such as automated side loaders.
“We took this on about four years ago to initiate a new project,” Short said. “And we’ve had them running for just over 18 months at customer sites, very successfully, where the operator is no longer needed on the machine. The operator can offer a value-add in terms of order picking, in terms of receiving, and in terms of doing other tasks.”
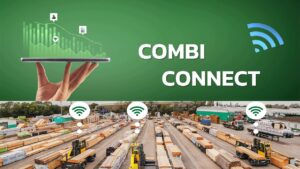
The Combi-AGT has a lift capacity of 11,000 pounds at various lift heights. Its design is based on the Combi-GTE model, an electric manually operated model used in service centers due to its ability to work in rail-guided narrow aisles. In addition to working with its customers to identify the best specifications for the new autonomous dual-operational side loader, Combilift worked with Irish Manufacturing Research during the development process to ensure the integration of the product with multiple warehouse management systems.
Laser-based safety sensors are located throughout the chassis of the Combi-AGT, which automatically slows down or stops the unit, if necessary, when approaching an obstacle. The unit will continue on its way when the obstacle has cleared the safety sensor area. What’s more, the natural feature navigation system on the unit relies on naturally occurring features such as warehouse walls, racks, and columns, as opposed to methods based on wire guidance or artificial landmarks such as reflectors. This means customers will not need to add to or change the infrastructure of their warehouses to use the Combi-AGT in their facilities.
“It’s safer for the operator to not handle the loads within the racks,” Short said. “We can do those A to B routes autonomously and efficiently throughout the day with very little intervention.” Short said that Combilift views the product as a large part of its future and becoming a large part of the business as it continues to expand.
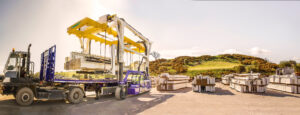
Combilift relied on its own autonomous group to develop the software for the machine logic featured on the Combi-AGT. Short said this has been a big advancement for Combilift in terms of the number of software, systems, and mechatronics engineers that are operating in the company’s factories and in the field. “It has been very successful for the customers, and that is going to feed through all of our other products,” Short said.
Electric Models and Sustainability Goals
Last year, Combilift also launched its Combi-CB 155E, an electric model 15,500-pound capacity counterbalance truck that features multidirectional ability, able to handle both long and bulky loads. The truck features a gas strut suspension cab, super-elastic tires, and a compact wheelbase. “We see that [truck] focused very much on steel fabricators with the beam heavier loads that are used in yards and transferred into buildings,” Short noted. Added Combilift CEO and co-founder Martin McVicar: “The increased capacities that we are offering in our electric range will answer the demand for ever more powerful products, which at the same time help companies to achieve their aims for more sustainable operations.”
Yet another new product released last year is the telematics software Combi Connect, which allows customers and the Combilift team to remotely diagnose a machine located anywhere in the world. The software offers real-time data on fleet performance, usage analytics and maintenance alerts. For example, the impact/shock monitoring feature enhances safety and allows for damage control accountability regarding speed, drive mode, operator presence, time and location logs.
“We can get live feedback from a machine, where updates can be sent as well,” Short said. “This is something we are very excited about. It’s as important for the customer with one machine as the customer with multiple machines spread across locations because it gives them a good insight into the utilization of their service needs, and how the units have been used. And we’ve had a great reception. More and more of those units are shipping out from the factory.”
Short said the Combi Connect technology is another way Combilift can support its customers, who can use the data that is compiled in ways that are useful to their individual businesses. This is one way the company can respond to customers’ needs. Another is addressing the need for electrification from industries using the company’s trucks.
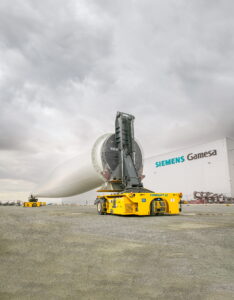
More industries that have not been so receptive to electric material handling systems are requesting these products more and more. “And that is a big change,” Short noted. Combilift produces electric units that can handle up to 26,000 pounds.
Another change in the manufacturing industry is considerations regarding the power supply fueling material handling solutions. Customers are exploring alternative fuels and power sources to meet sustainability initiatives and goals. Combilift designs its trucks so they can be powered by whatever power source a customer chooses. “As long as it [power source] can produce the correct power and voltage and amps that can run the machine, we will work with them,” Short said. “That’s how we’re positioning ourselves in the short term. There seems to be a lot of competing technologies and it’s not for us to decide. I think it’s going to be the customer in the market who will decide what’s going to be successful, and also the reliability of them [power sources].”
Short also pointed out that Combilift will not recommend something that isn’t a solid solution. The company will present the upsides and downsides of power sources, according to the state of the technologies, and will work with customers as best they can to incorporate their power requests.
Customers Provide the Most Valuable Insights
Working with customers to solve their material handling problems is front and center for Combilift. They are so successful at managing relationships and developing top-notch solutions that one manufacturer has even designed its new buildings around how Combilift’s products maneuver and enhance their production output.
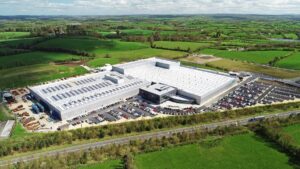
This customer manufactures air conditioning units. Combilift worked with company officials to maximize storage layouts to increase the customer’s flexibility with transport and moving materials to the job. “We have designed machines specifically to handle the full coolers,” Short said. “In terms of our Straddle Carriers, they use that to move product off the production line to their outdoor storage yard and that same equipment is used to load it on the trailers.” The manufacturer uses Combilift’s C-Series and CB units for handling long materials.
This partnership is an example of adding value through design and layout recommendations, which has become part of the customer’s infrastructure in its new plants across the world. Short said Combilift partners with manufacturing companies to develop solutions that handle products in the safest, most efficient way possible that will make their operations more profitable.
For another customer, Combilift’s side loader equipment and value-added recommendations assisted the company in increasing weld arc-on time from 70% to 90% because welders didn’t have to stop while the product was moving over their heads via cranes. This customer had been using cranes to move product from its main line to the fitting area to the welding area, and finally to the paint booth. While it was somewhat of a smooth process, production was held up while welders were waiting on cranes to be available and/or to move jobs.
“We demoed our C-Series unit, and we could move product without anyone having to stand out of the way when a beam was being moved or a column was being moved; we could move down a very narrow way,” Short said. The product was moved 2’ off the ground as opposed to overhead, not interfering with anyone’s work. The customer commented that his help-wanted sign for more welders and fabricators was not necessary; what he needed was for fabricators to be welding and not stopping every time a beam moved via crane.
With the increase to 90% arc-on time, the company realized a large gain in efficiency. Combilift’s C-Series allowed the company’s welders to add value, actually fitting, welding and moving products to the next stage safely without waiting for cranes to move the products.
Cost savings and production efficiencies have also been realized by a manufacturer in Texas that was loading outbound material for steel building manufacturing (buildings, columns and roofs — very mixed loads) seven days a week. They had traditionally been building the loads on semi-trailer beds, where someone was working from the trailer and had to be tied off to avoid the risk of stepping off the trailer. With a Combilift Straddle Carrier, the company could build a load at ground level and lift and carry the load to the trailer, which could be loaded and out the gates in 15 minutes. This allowed the company to reduce their shipping process to five days — down from seven days a week — cutting down on overtime expenses.
“Now they can build the load once, have it waiting once the trailer arrives, load it, and ship it out,” Short said. “They have seen a huge increase in the efficiency and safety.”
Short went on to add Combilift’s products are developed to solve challenges. The company can assist customers with challenging loads if there is a difficult area within their plants, if they are increasing production in their plants, or if they are adding a production line and things are getting tight. “We give our suggestions and how to prepare the area, provide layouts, and how to store the material,” Short said. “We can provide solutions or come up with a new product. A lot of our products resulted from customer challenges.
“Working on unique and new products is what drives our business and keeps everyone excited,” Short continued. “It also makes the environments safer for the customers, making them more efficient so that they can have a more sustainable business in the long term.”
Capone Iron Corp. handles long loads with the C-Series and Straddle Carrier from Combilift.
Combilift at work in a steel aluminum fabrication facility in South Carolina.