Ultra-fine Filtration Technology for Regrinding Precision Tools
Vomat’s Filter FA 70+ uses high-performance ultra-fine filtration technology to ensure that purified cooling lubricants of the highest purity are always available.
Posted: February 18, 2024
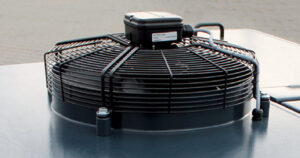
Cleanly filtered cooling lubricants play a decisive role in the regrinding of tools and represent an important quality factor. The filter manufacturer Vomat from Treuen uses high-performance ultra-fine filtration technology to ensure that purified cooling lubricants of the highest purity are always available throughout the entire production process. The Vomat FA 70+ small system is particularly suitable for regrinding. This single-station solution in compact dimensions combines special design features that enable tool manufacturers and resharpeners to produce in a resource-saving and profitable manner.
The dovetailing of climate and environmental protection with production efficiency and profitability in industrial metalworking is becoming increasingly important. One piece of the mosaic is the regrinding of cutting tools. This process helps to reduce the environmental impact at various stages of the tool life cycle, which in turn helps to reduce the CO2 footprint.
This leads to increased demand from the industry for tool reconditioning services from tool manufacturers and companies specializing in regrinding. This is because professional reconditioning and resharpening of high-priced precision cutting tools maintains their performance beyond their initial use and the performance potential is fully exploited thanks to the extended life cycle. Steffen Strobel, Sales Manager at machine manufacturer and filter manufacturer Vomat from Treuen: “We welcome this trend, as it effectively saves resources. At the same time, the integration of climate and environmental protection into production profitability is also becoming increasingly important in the production of cutting tools and their resharpening. More and more tool grinders and resharpeners are attaching importance to the fact that their machines not only offer high efficiency and quality, but also produce sustainably. This applies not only to tool grinding machines, but also to peripheral systems such as coolant filtration systems.
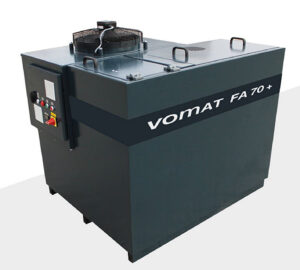
This is where high-performance filter manufacturers such as Vomat come in. The product portfolio of the Treuen-based filtration specialists includes solutions for individual systems, modular systems, central systems and customer-specific special systems with central and decentralized functions. Thanks to numerous design advantages, the filters enable sustainable and at the same time profitable tool production and preparation. The FA 70+ stand-alone solution for tool resharpening is an example of this.
The compact system (dimensions L x W x H: 1300 x 1100 x 1200 mm) has a maximum filter capacity of 70 liters/minute and provides clean oil in NAS 9 quality over a long filtration period. Optional additional modules such as an integrable 7 kW cooling unit with a control accuracy of +/- 1.0 K as well as magnetic and disposable filters enable customer-specific complete system solutions. The residual sludge is disposed of manually using special bag containers.
Steffen Strobel: “State-of-the-art filter, cooling and disposal technology – including HSS pre-filters for mixed processing if required – ensure economic and ecological success in harmony. In addition, our VOMAT Filter FA 70+ is low-maintenance and takes up very little valuable production space thanks to its compact design.”
In order to optimize the operation of the ultrafine filtration systems in terms of energy, Vomat relies on the use of efficient pumps with high efficiency. In conjunction with the optimized process control, unnecessary energy losses are avoided: Vomat systems automatically control the filter flow and backwash cycles as required. This extends the service life of the filter elements and saves energy and costs. At the same time, less heat is added to the medium, which in turn requires less cooling capacity and further reduces energy consumption.
Steffen Strobel: The fully automatic control and regulation of the filter capacity means that energy and operating costs can be kept low. The filtration systems for tool grinding and regrinding are tailored to the user’s specific requirements and integrated into their production process. Thanks also to the high quality of the cleaned coolant during grinding, the reground tools achieve a performance that comes very close to that of a new tool.”