When Pretty Welds Aren’t Enough
Shops struggling with outside disruption and competitive pressures should look into robotic automation as these techniques continue to make significant advancements.
Posted: February 15, 2024
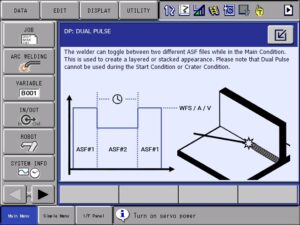
To overcome talent gaps, stringent demands and ongoing disruption, company leaders continue to adopt advanced technology, including robotic automation to improve operational efficiency and product quality. One robot segment that garners considerable attention is arc welding. Representing more than 55% of robot usage worldwide1, the on-going focus to enhance current weld methods for increased precision and efficiency continues to reveal groundbreaking improvements. Thanks to advances in gas metal arc welding (GMAW) power supplies, as well as improvements to communication interfaces between robot controllers and newer power supplies, for example, augmented welding performance is now possible via alternating the heat input of the weld process in real time.
Enhancing Proven Techniques
It is commonplace today for welders that utilize semi-automatic GMAW to implement a range of techniques to vary heat input along the weld path. One example is how a welder can use his hand to oscillate the weld torch forward, then pause along the weld line. This forward movement creates the desired penetration, and the pause then serves to fill the region and concentrate heat briefly in a certain region of the weld seam. Often used in contrast to a continuous forward motion, this method can improve GMAW’s ability to create the desired surface profile and weld integrity.
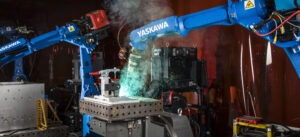
Likewise, with proven technological advances, it is possible to implement a varying heat-input technique using an automated GMAW process. Unlike a traditional path where the robot controller utilizes a weaving motion to duplicate the manual welder’s weld torch movement, this new process employs periodic changes to electrical output (“heat input”), rather than physical oscillation.
With this in mind, some automated GMAW welding power supplies offer control modes where different heat input conditions and/or output modes (i.e., non-pulsed, pulsed, wire oscillation, etc.) can be switched during the weld process. For example, it may be preferable to perform a spray arc pulse cycle for a period of time, then switch to a lower heat input non-pulsed mode for another period of time, before switching back to pulse mode.
For welding power supplies that do not offer this built-in function, easy-to-use pendant applications, such as Yaskawa’s Universal Weldcom Interface (UWI), provide similar control and enable easy management of any weld process or parameter. Compatible with most robotic welding power sources with modern digital interfaces, pendant applications like this can be used to adjust voltage, amperage, wire feed speed and more.
Where heat input settings and output modes are concerned, a digital interface can define these parameters in two separate Arc Start Files, allowing the robot controller to switch back and forth between the files during the weld cycle. Known as Dual Pulse, timers are used to specify duration in the Primary and Alternate weld files, creating a flexible way to define the frequency (total time) and the balance (time 1/time 2) of pulsation between the two settings. Note: changes in the weld settings are normally between 2-to-5 Hz, with the frequency controlling the spacing between ripples in the weld bead.
Discovering Helpful Advantages
Ideal for aluminum, but also relevant for steel, stainless steel, and others, variable heat input (Dual Pulse welding) welding with automation systems provides multiple benefits:
- Improved surface cosmetics: Foremost is the ability to create TIG-like cosmetics that reproduce the layered penny look. While the switching of heat input has been used for years to improve weld bead cosmetics, especially for aluminum, the alternating of heat input also provides optimized quality and accelerated return on investment of the entire robotic system via improved weld process robustness.
- Higher travel speeds: As seen with the high thermal conductivity of aluminum, it is possible for the heat from the weld to exceed the travel speed, which causes the bead to get wider and possibly even burn through. With robust tools, robots have the ability to taper weld parameters over distance, so the wire feed speed can be reduced proportionally while traveling to help compensate for this. Note: traveling between high and low weld settings provides a cooling period that can help balance heat input and typically eliminates the need to vary parameters during the weld.
- Superior gap bridging: While time and planning should be taken to ensure proper fit up of parts so that gaps are not present, nevertheless, gaps will still occur. With the help of the widening pulse arc profile, dual pulse and general pulse processes can help in closing, at least minor gaps at the weld seam.
- Improved surface profile: By alternating the high and low current, the effect of the pulsing tends to wet out the filler and base metal for a more even, flat surface profile.
Overall, these advantages serve to improve process robustness. These methods, along with the use of sophisticated power source technology and feature-rich pendant applications, allow robot users to overcome historic application and programming barriers. As robotic welding techniques continue to see significant advancements, decision-makers struggling with outside disruption and competitive pressures should look into robotic automation – as manufacturers that execute operational strategies via modern technologies will most likely adapt to market pressures for ongoing success.
1 Welding Robot Market Size in 2023, Precision Reports, 2023