Manufacturer Realizes Vast Improvement in the Quality of Welds, and Greater Visibility Into Robotic Downtime
Highlands Diversified Services in Kentucky tapped into advanced welding operations from Panasonic Connect North America to increase its success in meeting customer requirements.
Posted: April 30, 2024
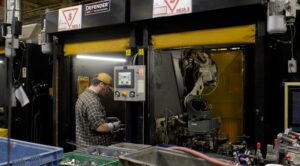
Highlands Diversified Services (Highlands) in Lexington, Ky., is a privately held, vertically integrated contract manufacturing company specializing in welding, metal stamping, powder coat painting, assembly, warehousing, and distribution. Highlands is a full-service manufacturer meeting the needs of a diverse customer base within telecommunications, automotive, aerospace, appliance, and industrial equipment market segments.
Working with new raw materials and increased production demands are ongoing challenges in today’s manufacturing and welding industry. With these challenges, keeping up with customer needs and maintaining high-quality work requires welding teams to adopt advanced robotic technology that is high-performing and easy to use.
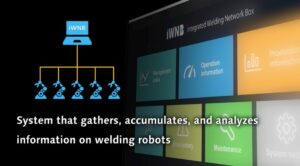
Panasonic has been Highlands’ robotic welding partner since 1998. Since that initial partnership, Highlands now uses many robots from Panasonic. Recently the team specifically turned to Panasonic Connect to enhance its operations with Panasonic’s Super Active torch technology and iWNB (integrated welding network box) software – a system that gathers, accumulates, and analyzes information on welding robots. With this technology on the factory floor, Highlands has experienced a vast improvement in the quality of their welds, has mitigated skills-based hiring and staffing shortages, and has greater visibility into robotic downtime and productivity levels.
Reducing Downtime and Automating Data Capture with Manufacturing Technology
Since adopting the Super Active Torch Technology on all of its Panasonic robotics, the Highlands team saw higher quality welds specific to spatter reduction. The team was also able to dial in schedules for different types of materials with a variety of mechanical properties. With this new technology, the Highlands team has seen increased success meeting customer requirements as it relates to using new materials, all without increasing errors.
After a 30-day trial of Panasonic’s iWNB software, Highlands was able to evaluate the exact conditions that their robots were in as well as pinpoint specific causes of errors and downtime. In an industry where downtime can cost $260,000 per hour, this was a game changer.
“We were excited about launching the iWNB software throughout the factory on all of our robots to give us the productivity analysis that we needed, which links causes of downtime and OEE,” Michelle Hamm, General Manager, Highlands Diversified Services. “It’s the validity of the data that we’re looking at, which in turn allows us to make better decisions.”
Mitigating Staffing Challenges with Easy to Use Technology
In the next decade, it’s projected that there will be nearly 43,000 welder openings annually. Keeping up with customer demands and high-quality work requires welding teams to adopt advanced robotic technology that is simultaneously easy to use. These technologies can successfully support the current and future workforce, augmenting certain tasks for improved performance. This is crucial in an industry like manufacturing, where 75.7% of leaders consider attracting and retaining a quality workforce to be the number one business challenge.
Responsible for all weld and new product development, robot maintenance, and robotic welding teams, Jason Carl, Weld Engineer, of Highlands Diversified Services understands the importance of ease of use on the factory floor.
“There’s not another robot on the market that offers such ease of use and ease of training,” said Carl. “We can bring in a new employee with limited experience and have them programming within three days. This is critical because when you lose someone who’s involved in programming and other important tasks, it really hurts. And it does happen.”
Carl explains the reality of employee turnover in the manufacturing industry and how having technology that is easy to train on and use, is imperative to keeping productivity levels up.
Panasonic Connect’s welding robots and analysis software is transforming Highlands’ day-to-day operations. With increased productivity, visibility into machine performance, and faster employee training times, Highlands can meet the increased demands of its customers and position themselves to easily evolve alongside their customers with advanced technology.