Multi-purpose Solutions Streamline Operations and Keep Your Focus on Efficiency
Advancements in metal forming and fabricating equipment provide the means to step up your game, leading to increased productivity to support a range of applications in a variety of sectors, providing a competitive edge.
Posted: April 4, 2024
Wide Array of Band Saws In-stock and Ready to Ship
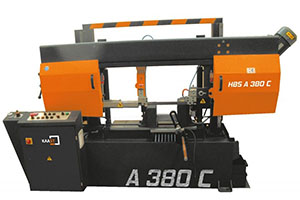
KAAST Machine Tools, Inc. (Aldan, PA) band saws come in sizes ranging from 9”-to- 60” (230 mm to 1,500 mm). Larger capacity saws generally have larger motors providing more torque and allowing the operator to cut faster, not just larger, and to increase the speed at which the blade can get through the material. But as size increases, so do prices. All band saws sold by KAAST are at least semi-automatic, meaning the head movement is controlled by a hydraulic piston, and can be raised and lowered by the operator activating the up/down switch. To run the machine, the operator tightens material in the vise and pushes the start button. The saw will make the cut, then lift the head back to the upper position. Semi-automatic saws are a good fit if you need to make a few cuts in a length of material.
Fully automatic KAAST band saws have a hydraulic piston to raise and lower the head and are either equipped with driven rollers in the vise or a shuttle vise to advance the material. Most fully automatic saws also feature a digital piece counter. KAAST offers an assortment of horizontal mitering band saws, with options for a swiveling head or a swiveling vise, each combined with either a scissor type or dual column set up and offered in fully or semi-automatic.
The KAAST HBS horizontal bandsaws have a wide array of options available. The hydraulic top clamp for the HBS lineup allows the operator to easily, with minimal tack-welding of the ends or strapping, cut pieces of bundled material by applying pressure in two directions simultaneously to ensure a clean and complete cut. If you plan to run your saw continuously a chip conveyor will ensure your chip chute doesn’t overflow, reducing downtime, saving money. The chip auger helps to move larger, heavier chips (e.g., cutting iron with a large tooth blade), which might otherwise sink to the bottom of the chute and not be flushed to the coolant collector. Roller tables, as the name implies, feature multiple cylinders which roll as material is moved across them. A little push goes a long way. While they cannot initiate movement, the rollers greatly ease material movement.
Motor-driven roller conveyors are recommended for use in conjunction with hydraulic top clamps and shuttle vises in fully automatic horizontal band saws. Using a small but powerful motor, the tables help the shuttle vise to move heavy materials into position to be cut. The combination of shuttle vise, hydraulic top clamp, and motor-driven roller conveyor results in a machine made for mass production with minimal hands-on time.
Customers are encouraged to reach out to KAAST, either by phone, email, or through www.kaast-usa.com, for more information, or to stop by the 42,000 sq. ft. Philadelphia-based showroom or our Chicago show room to see firsthand what KAAST has to offer. The company offers one of the most diverse and extensive lineups of machine tools in the industry. The company stands behind its machines with quick shipping of spare parts and excellent after-sales service, as well as providing in-person training and installation.
New Gas-Reduction Nozzle Technology for Fiber Lasers
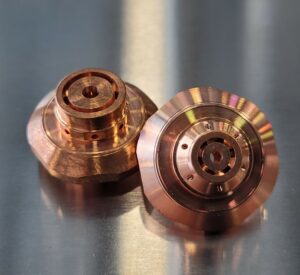
A new patented gas- and burr-reduction technology is now available for the Mitsubishi GX-F ADVANCED Series of AI-enabled fiber lasers, improving cut quality while reducing gas consumption when cutting mild steel. MC Machinery Systems/Mitsubishi Laser’s (Elk Grove Village, IL) proprietary AGR-MIX nozzle technology does not require external blending tanks or high-pressure oxygen. By combining low-pressure air with nitrogen within the nozzle, a blended gas is created that can be easily adjusted based on material type.
“This blended gas not only minimizes or eliminates burr in mild steel, it also reduces gas consumption without the use of any external blending tanks or high-pressure oxygen,” said Ryan Conroy, Mitsubishi Laser product manager. “This saves both money and space.”
To develop AGR-MIX, Mitsubishi Laser built on its no-contact AGR (Assist Gas Reduction) nozzle technology, which reduces nitrogen-assist gas consumption by up to 75%. The new AGR-MIX technology can reduce it even further — up to 50% more.
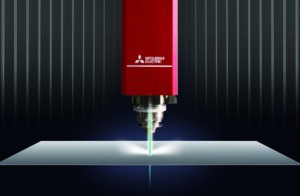
Because assist gas is a significant expense due to bulk nitrogen costs, Mitsubishi Laser has focused its efforts on advanced gas-reduction technologies, including AGR-N2 (100% oxide-free processing while saving up to 75% on nitrogen assist gas consumption) and AGR-AIR (extremely cost-effective, 100% air cutting), in addition to AGR-MIX.
The AGR-MIX nozzle is uniquely structured: Nitrogen is funneled to the center of the nozzle in an air shroud, while a separate chamber funnels some of that air into the nitrogen stream. This produces a mix gas that is made up of about 95% nitrogen and 5% oxygen.
AMADA AMERICA to be the Primary Sponsor of Sato’s Indy 500 Entry
Rahal Letterman Lanigan Racing (RLL) announced that two-time Indianapolis 500 champion, Takuma Sato, will return to the team for the 108th running of the Indianapolis 500. AMADA AMERICA, INC. (Buena Park, CA), a leading global machine tool manufacturer and supplier in the sheet metal industry, will be the primary sponsor for 2017 and 2020 Indy 500 winner Sato’s No. 75 Honda-powered entry in the May 26 event.
Sato competed for RLL in 2012 and from 2018-2021. He has earned six NTT INDYCAR
SERIES wins, four of which have come with RLL, including the team’s second Indy 500 win
in 2020. Sato, a native of Tokyo, Japan, has made 220 starts in the INDYCAR SERIES since his rookie season in 2010, which is sixth among active drivers and 22nd all-time. His Indy car
highlights include wins in the 2017 and 2020 Indianapolis 500. Most recently, Sato competed in oval races with Chip Ganassi Racing in 2023. The 2024 Indy 500 will mark his 15th time to participate in the Indianapolis 500 and sixth with RLL.
AMADA was the primary sponsor of the team’s No. 30 entry at the Children’s of Alabama
Indy Grand Prix at Barber Motorsports Park on April 30, 2023, and this will be the company’s first time to participate in “The Greatest Spectacle in Racing.” They will also be a major associate
sponsor of the No. 30 entry driven by Pietro Fittipaldi for the 2024 Acura Grand Prix of Long
Beach, near the company’s Buena Park, Calif. headquarters.
Revolutionary Punch/Fiber Laser Combo Machine Equipped with
a Multi-purpose Turret
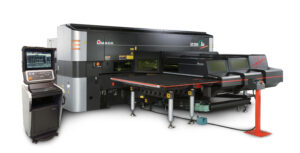
The LC 2515 C1 AJ from AMADA AMERICA, INC. (Buena Park, CA) is engineered for high-speed productivity — combining the forces of a 22-ton turret punch press with the flexibility of a 3 kW fiber laser. To maximize punching productivity in conjunction with laser cutting, the C1 AJ features a 44-station MPT (multi-purpose turret). In addition to ensuring maximum speed, the highly efficient fiber laser uses approximately a third of the electricity when compared to a CO2 system.
The laser head moves in the Y-axis via a direct drive servomechanism for maximum speed and accuracy and is isolated from punching vibration to help maintain beam integrity and cut quality. Reliability is further enhanced by a gap near the laser axis which is engineered to allow cutting gas and slag to escape without impacting processing. A cartridge-type lens provides for simple and fast lens changes. In addition, the use of non-contact sensor technology ensures that the laser beam remains focused on the sheet, thereby guaranteeing maximum quality and consistent cutting operations.
Unique features of the MPT include four tapping tool stations and three innovative die lift stations. The die stations automatically lift to facilitate upward forms while reducing material scratches and preventing downward forms from hitting the forming dies during sheet movements. In addition, a brush table automatically lifts to support material and provides scratch-free processing — eliminating the need for secondary finishing.
Additional features include:
- AMNC 3i touchscreen control
- Barcode reader for rapid program loading
- 44 station MPT (four auto index) (four tapping stations) provides flexible production
- MPT also provides unique forming and tapping functions
- Patented bridge frame construction
- Compact and ergonomic safety enclosure
- Energy saving — ECO Cut and reduced power consumption
- Rapid changeover between synchronized punch and laser
- Flexible table design
- Compact footprint
To keep pace with the inherent high-speed processing of fiber laser technology, AMADA provides a variety of automated material handling systems. One example, the ASR 3015N TK, extends unattended operation to multiple shifts. Its compact tower design produces floor space savings while providing reliable and extremely efficient material storage and handling. Speed and productivity are mathematically predictable and no longer linked to personnel motivation. Preprogrammed commands allow the system to work around the clock with a minimum amount of operator intervention. Flexibility to produce smaller lot sizes in a variety of material types and thicknesses is provided by the additional shelves of the automated tower. In addition, an integrated TK (Take Out) system provides automated single-part separation and sorting. The highly reliable TK system removes the part from the skeleton the instant it is cut free. Then, the part is precisely stacked.
Five-axis Laser Cutting System Streamlines Operations in One Machine
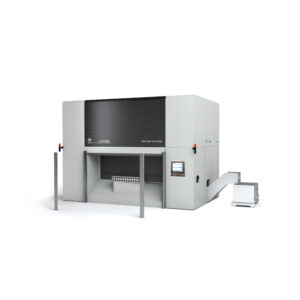
BLM GROUP’s (Novi, MI) LT-FREE Turn Table 5-axis Laser Cutting System is ideal for laser cutting bent and hydroformed tubes, flat and deep-drawn sheets and welded assemblies. This system features a rotary table with two workstations equipped with input and outputs to dynamically clamp parts in fixtures, 3D cutting head with 4 kW power.
The LT-FREE, available with fiber laser power up to 4 kW, is ideal for machining mild steel, copper, aluminum, brass, stainless steel and galvanized steel. There are no limits to part access; trimming and feature cutting can be achieved right on the bend accurately and repeatably.
Efficient and easy to operate, users just select material type and thickness from the intuitive controller, and the machine will automatically set the cutting parameters and the optimal focus position. Traditional cutting, drilling, punching, milling and deburring operations, which are normally conducted in sequence, can now be performed on a single machine. This eliminates set up and “work-in-progress” inventory, as well as reducing material handling to streamline the entire process.
Different material handling configurations are offered to meet specific production needs, while always guaranteeing the flexibility and productivity typical of this 5-axis laser cutting system. The system is equipped with the optional user-friendly CAD/CAM software to create part programs of any complexity in a simple 3D graphical environment.
Efficient Laser Cutting with Intelligence
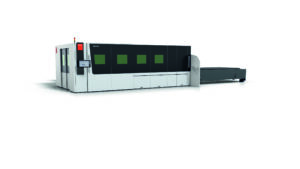
An impressively high cutting speed, an intelligent cutting process, and a new design: this is how the new ByCut Star by Bystronic Inc. (Hoffman Estates, IL) presents itself. With 30 kilowatts and an optimized cutting process, it now cuts steel, aluminum, stainless steel, brass, and copper precisely and reliably – for even more quality. The new power level is exclusively available on the ByCut Star 4020.
The high-end fiber laser stands for high-precision Bystronic technology, a stable cutting process up to the highest laser powers, and for a wide range of applications. With it, sheet metal processors are taking a major step in terms of productivity and efficiency.
Cutting speeds on the ByCut Star increase twice as fast compared to 15 kW and MixGas with sheet thicknesses between 0.24” and 0.59”, and more than twice as fast with thicknesses starting at 0.79”. Piercing times are shorter for sheet thicknesses of 0.59” and above. Sheet metal processors thus benefit from higher productivity at low unit costs, because with 30 kW kilowatts cuts precisely and reliably. It enables maximum flexibility for large series and spontaneous customer orders.
Whether aluminum or steel, the powerful Bystronic cutting head impresses with maximum precision in thin and thick sheets. In addition, with the Advanced Applications option, high laser power (starting from 15 kW) also enables expanded applications in steel and aluminum of up to 1.07”.
NCT & KerfScan is a smart feature package for oxygen cutting and increases the process reliability even in low-manned operations. This feature offers process monitoring, problem solving and continuation of the cutting process in a fully automatic way.
The Parameter Wizard ensures that the correct quality of the cut parts is always selected by obtaining the perfect parameter within minutes — even for inexperienced or less experienced operators. In just a few minutes, this feature determines the perfect parameters with N2 and MixGas for steel from 0.16”-to-0.59” in thickness.
New Two-press Production Cell for Lights-out Operations
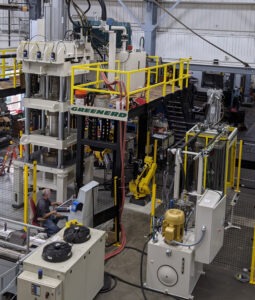
Greenerd Press & Machine Co. (Nashua, NH) designed, engineered, built and turnkey-installed an automated two-press, two-robot production cell enabling unattended production of large aluminum pressure vessels.
Using sensors to locate pallets of blanks that have been placed in a pallet staging area, the first FANUC robot picks a blank, detects and rejects any double-blanks, and transfers the blank to a fully integrated and automated blank lube station. That robot then picks a previously lubricated blank and loads it into a Greenerd deep-draw press with a 76” stroke.
A second FANUC robot then catches and transfers the formed parts to a second Greenerd press for a punching operation. The two-press production cell uses a centralized control station which sets the operating parameters of both presses and controls the action sequences of both FANUC robots. All equipment in the cell is automatically updated with new process parameters when changing between products.
Greenerd provides unique hydraulic press automation solutions for a wide range of industries and applications. “Increasingly, our customers are seeking turnkey, state-of-the-art robotics and other product handling solutions,” said Greenerd Press & Machine Co.’s President and CEO Jerry Letendre. “To meet the demands of today’s challenging applications, we are providing manufacturers with automated press solutions that are flexible, productive and reliable.”
Greenerd’s extensive line of hydraulic presses are available in a variety of styles ranging from gap frame and straight-side to die-spotting and forging presses, with unlimited size and tonnage capabilities.
Hole Puncher is Ideally Suited for On-site Hole Punching
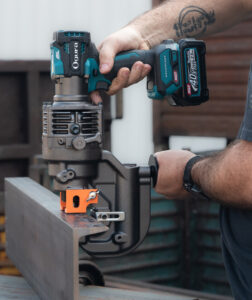
Hougen Manufacturing, Inc. (Swartz Creek, MI) now offers the new battery-powered Hougen®-Ogura™ Punch-Pro™ electro-hydraulic portable hole puncher. The new 40v battery-powered unit, 76004PR model, can be easily operated on-site where electric power may not be available or high up on a man-lift where power is not readily accessible. The unit generates up to 17 tons of punching force and can punch round or oblong holes up to 25/32″ diameter in 3/8″ mild steel in as little as four seconds. The unit’s throat depth is 1-9/16″ and it can punch flat bar, angle iron, H-steel and channel.
Weighing just 24.9 lbs., the 76004PR cordless hole puncher is ideally suited for applications typically done with electric hand-held twist drills. The operator can easily position the tool when working in narrow or awkward positions by rotating the handle 360° in either direction during operation. The punch can be jogged down to the center mark to confirm hole location accuracy. The model includes the new Power Retractable Punch System which allows the operator to power reverse the punch back out of hole. This improves productivity in harder, more elastic materials which tend to grip the punch (not allowing it to auto return to the home position) after the hole is produced.
Its motor is powered by a 40v DC lithium-ion battery that can be fully charged quickly using the included battery charger. It can punch more than 100 holes through 3/8” mild steel on a single battery charge.
High Productivity Bi-Metal Band Saw Blades for Structural Cutting
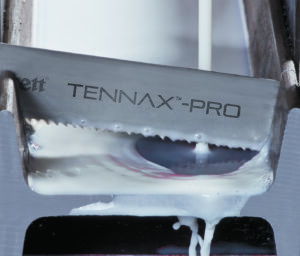
The L.S. Starrett Co. (Athol, MA), a leading global manufacturer of saw blades, precision measuring tools and gages, metrology systems and more, has introduced TENNAX™-PRO Bi-Metal Band Saw Blades designed to cut challenging tubes, pipes, profiles and structural shapes in both single pieces and bundles. Providing lower noise and vibration as well as improved cutting performance, these blades outlast and outperform competitive blades, making up to 25% more cuts per blade.
The TENNAX-PRO Band Saw Blades feature high-speed M-42 steel teeth with a new special tooth geometry/profile that optimizes the tip profile for tube, pipe and other structural cuts, dissipating stress during cutting for greater resistance to wear and tooth breakage. In addition, these band saw blades are designed with an exclusive tooth-setting process, which minimizes pinching when cutting structural and bundled materials.
The blades are ideal for cutting a wide range of materials including carbon steel, carbon steel alloys, stainless steel, and non-ferrous materials. In addition to pipes, tubes, structural and bundled materials, TENNAX-PRO applications include small solids. The blades are available in widths of 3/4″, 1″, 1-1/4″, 1-1/2″, 2″, and 2-5/8″, and can be used with manually operated, gravitational, and hydraulic machinery, making them a versatile and adaptable choice for a variety of applications.
Starrett’s TENNAX-PRO Band Saw Blades replace the Starrett’s Versatix™ MP line.
Monitoring System with Automated Ram Height Adjustment
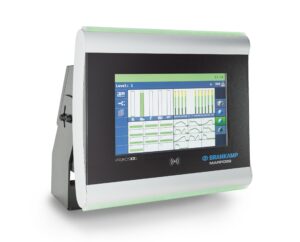
Marposs Corp.’s (Auburn Hills, MI) X3s Brankamp monitoring system with special automated ram height adjustment automatically compensates for variation in sheet thickness, material hardness, tool and machine temperature, speed, etc. during the manufacturing process. Using a mini press wired to the Marposs Brankamp monitoring system and a piece of paper that serves as the variation, visitors to a recent trade show saw how the system automatically sends a signal to adjust the shut height of the press to adjust the change.
These monitoring systems for sheet metal processing (stamping, drawing, coining, piercing, blanking and bending), detect process disturbances such as rising slugs, feed failures, and punch or die breakage, providing 100% monitoring of each individual stroke and protecting the machine and tool from overloads. This helps to immediately identify manufacturing faults as well as part or tool variations, enabling manufacturers to optimize machine efficiency, improve part quality, and limit unplanned downtime and tooling costs.
Monitoring systems are an effective method to gain insight into the forming process and its stability, to detect production faults and quality deviations, and the shut height, if necessary.
Turnkey Metal AM Robotic Work Cell for Faster Production
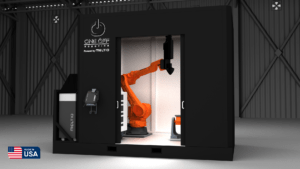
One Off Robotics (Chattanooga, TN) and Meltio (Linares, Spain) are teaming up to develop a breakthrough, ready-to-use additive manufacturing (AM) work cell. This system includes high-touch customer service and comprehensive support to assist end users in any industry.
One Off Robotics is one of Meltio’s key partners in supporting wire-laser metal 3D printing in the USA. Their new turnkey system can be quickly and easily deployed into any factory environment. Meltio is a disruptive wire-laser metal deposition AM technology leader. Their collaboration introduces the One Off Robotics Cell, a turnkey metal AM work cell designed for a faster, more efficient, and reliable part production cycle.
The system produces cost-effective, finely printed metal parts for applications in industries including automotive, aerospace, mining, oil and gas, and many others. With an impressive deposition rate of up to 1 kg an hour, this system excels at creating clean parts that are fully dense and mechanically equivalent to or superior to those created from traditional means. The system seamlessly integrates control of the system, allowing the user to easily adjust settings and print quickly. Its 8-axis system simplifies complex geometry printing and is configured to work with the Meltio Space robotic slicer, as well as other robotic additive software.
The One Off Robotics Cell uses standard welding wire and produces parts that are consistent, spatter-free, and clean. The robot and positioner are installed on a self-supporting platform inside a custom, laser-safe enclosure, which ensures safe operation and quick installation. The system package includes the robot, W-LMD system, 2-axis positioner, Meltio machine vision laser alignment tool, welding camera and safety enclosure. Package add-ons are available for the thermal SWIR camera, multi-material dual wire printing, and hot wire printing for increased speed. Meltio and One Off Robotics will also provide system training and instructional materials upon delivery to ensure unparalleled technical support for end users in any industry.
Dual-Trigger Braking Grinder is the Next Advancement for Angle Grinders
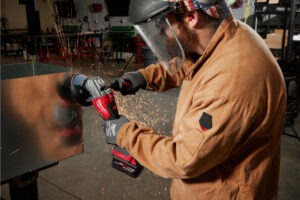
Milwaukee Tool (Brookfield, WI) provides the next advancement in angle grinder technology with its M18 FUEL™ 4-½” / 5” Dual-Trigger Braking Grinder. With dual-trigger activation, a permanent side handle, and AUTOSTOP™ kickback control, this new cordless angle grinder gives users greater control on the jobsite.
With a trigger on the braking grinder’s main barrel and a secondary trigger on the side handle, the dual-trigger activation requires two hands to stay on the tool for operation. The new-to-world side handle design is permanent to the tool, ensuring compliance on the jobsite. For added user control and accessibility in hard-to-reach areas, the side handle can be positioned in 15 different orientations: tilting from 0°-to-90° and pivoting to the left, top and right. An anti-vibration design reduces vibration in the side handle, increasing user comfort during extended use.
For the first time, Milwaukee’s AUTOSTOP kickback control is included in an angle grinder. An electronic clutch detects extreme movement and shuts off the tool, helping prevent injuries from severe kickback. Unique to Milwaukee’s metalworking solutions, RAPIDSTOP™ braking stops most wheels in under one second, allowing users to set down their tools quickly after use. The accessory guard can be easily adjusted without using an additional tool, but not easily removed.
Featuring four variable speed settings between 3,500 rpm and 8,500 rpm, users have additional control in a variety of materials. As an additional benefit, the grinder is compatible with ONE KEY™, which allows users to sync the tool wirelessly with their mobile device or desktop. With this technology, users can identify the tool’s location and utilize integrated tool security.
Rotary Table Blast Machine Features Innovative Vision Technology
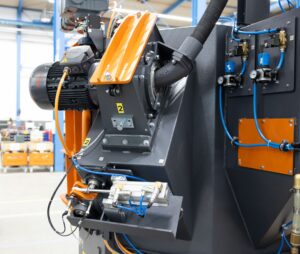
When OTTOSTAHL GmbH had to replace an old rotary table shot blast machine, the company insisted on short cycle times, high energy efficiency and relieving the personnel from strenuous and monotonous physical activities. These challenging demands were met by Rösler (Battle Creek, MI), and the automation specialist Teqram, with the universally usable rotary table Easy Shotblaster RDT 150, equipped with a stationary “intelligent” robot. This robot places the workpieces on the rotary table in a manner that optimally utilizes the entire table area without requiring any teaching operation.
OTTOSTAHL produces up to 30 mm thick, highly precise plasma-cut and up to 300 mm thick flame-cut components. Post-processing operations such as shot blasting, drilling, mechanical chamfering as well as arranging material testing through independent external material testing offices are also offered by the company. Rösler and Teqram developed a fully automatic shot blasting solution around the Easy Shotblaster RDT 150 rotary table machine. The entire blast system is integrated into a manufacturing cell measuring 8-by-8 meters and consists of an intelligent stationary robot and the RDT 150 shot blast machine equipped with suitable accessories.
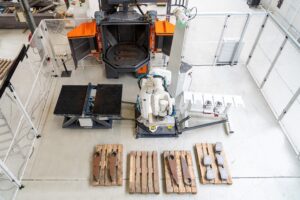
With its innovative image processing technology the vision-controlled robot, with a load capacity of up to 200 kg, automatically recognizes the components placed into its working section, completely independent from their position on the pallet. This eliminates the normally required time-consuming teaching or programming of the robot. Moreover, with the intuitive interface no special knowledge is required.
After the automatic selection of a suitable gripper from the gripper magazine the robot picks up the components and places them on the rotary table in optimum position. Then it provides component data to the machine controls for selecting a suitable processing program. After half of the cycle time is over, the robot automatically turns the components on the rotary table to blast the other side. After the blast process is complete, the robot returns the finished work pieces to the pallet.
The rotary table blast machine allows the blast cleaning of work pieces with different sizes and shapes. The table has a diameter of 1,500 mm and a load bearing capacity of 500 kg. To ensure the required short cycle times the machine is equipped with two Gamma 300G turbines, each with an installed power of 11 kW. Rösler Gamma turbines with their curved throwing blades in Y design generate an up to 20 % higher blast performance. At the same time, they consume less energy.
More Ergonomic, Easy-to-Use Shear
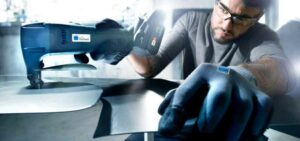
A powerful battery-powered shear from TRUMPF (Farmington, CT) reliably cuts through 0.10”-thick mild steel and 0.06”-thick stainless steel and is now even more ergonomic and easy to use and is available in North America. The cordless TruTool S250 LiHD 18V shear is designed to facilitate work done by sheet metal workers, electricians, pipe fitters, heating/ventilation fitters, stamping workshop operators, coil industry workers, and container or elevator builders.
“More than two years ago, TRUMPF was the first company to supply a rechargeable battery-powered shear – the TruTool S250 LiHD 18V – that could reliably cut through 0.10”-thick mild steel and 0.06”-thick stainless steel,” said Grant Fergusson, national sales manager for power tools at TRUMPF Inc. “Thanks to some further developments, this flexible hand tool is now even more ergonomic and easy to use, even in energy-intense applications.”
TRUMPF’s engineers have reworked the geometries of the TruTool’s cutting table and blade. The blade is now a rhombus shape with a pointed wedge angle. This design, in conjunction with the high-quality materials, ensures users only have to apply very little force and can work for longer periods without getting tired. The new, battery-powered S250 LiHD’s ability to cut curves is also improved thanks to the specified optimizations that allow it to cut even small 0.79” radiuses easily.
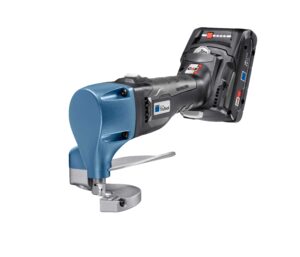
A well-rounded gear head and reduced machine dimensions create another ergonomic advantage. The battery-powered shear is visually appealing and rests perfectly in the hand. The level of occupational safety is increased by an extended cutting table that, among other things, protects the user’s hand during operation. It also prevents any tilting, enabling a fast and reduced-power feed rate.
“Regardless of whether you are processing flat sheets, checker plates or wire mesh, the high-performance, battery-powered S250 LiHD shears separate these metals quickly and reliably with a cutting speed of nearly 23’ per minute,” Fergusson added. “The machine was designed in such a way so there is always a clear view of the work surface and cutting line which ensures a high level of precision.”
Fitted with an 18-volt LiHD rechargeable battery (4.0 Ah) from Cordless Alliance System, the new S250 has a long service life and long runtimes of more than 70 minutes when processing 0.10”-thick sheet metal. In addition to a high-quality battery system, a brushless motor and power head technology designed specifically for the low 18-volt tension, contribute to the tool’s longevity.
Advanced Die Protection Features Added to Press Automation Control
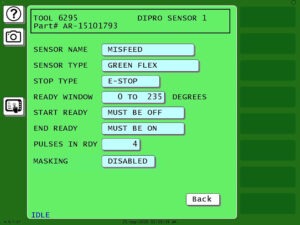
Wintriss Controls Group (Acton, MA) offers advanced Die Protection Features on the latest versions of its SmartPAC PRO Press Automation Controller. Advanced DiProPAC boasts more than 10 new capabilities.
The Wintriss SmartPAC PRO press automation control integrates programmable limit switch, die protection, clutch/brake control, tonnage signature analysis, and automated setup of counterbalance and shut height into one control.
Highlights of the new capabilities include a customizable green sensor type called Green Flex. This versatile cyclic sensor monitoring type now allows for specification of the required state of the sensor at the start and end of the ready window. The sensor can be set to require a specific number of actuations inside the ready window.
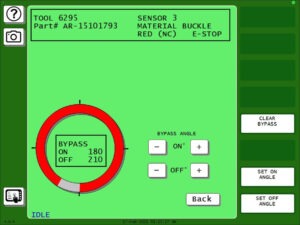
A masking feature is available on most green sensor types, including Green Flex, and is used to monitor events that occur regularly but not on every stroke. For example, applications might include gagging, zig-zag feeds or where multiple cycles are needed to produce part feature events that need monitoring on only some cycles.
To eliminate nuisance stops caused by the material “jumping” when the die opens, a Bypass Window can be programmed for static sensors. During the bypass, the sensor will be ignored, so any nuisance fault during that window will not stop the press. Outside of the bypass window, the sensor is monitored normally.
To save time and increase efficiency, an Auto Reset function has been added to the static sensors so that displayed errors, when removing a finished part, are automatically cleared when the sensor input is appropriately satisfied.
Advanced DiProPAC features also include improved handling of sensor names, sensor enable mode is now selectable by tool, minimum actuation time setting is added to red and yellow sensors and more.