Welding Technologies Significantly Simplify Tasks
Robotic welding leads the way, providing flexible, dependable, ergonomic, and versatile solutions.
Posted: April 3, 2024
New Compact Resistance Welding Workstation Simplifies Tasks
AMADA WELD TECH INC., (Monrovia, CA) a leading manufacturer of welding, marking, cutting, sealing, and bonding technology, offers the WR Series of Resistance Welding Workstations. The new WR Series Workstations combine a power supply, transformer, weld head, process monitor, and workbench into a compact workstation that simplifies operator welding tasks while maximizing quality and reliability. They are ideal for applications such as making copper electrical connections, hot crimping, welding and sealing RF and hybrid devices, and automotive component assembly.
The WR series uses closed-loop DC inverter technology with up to 60,000 amps provided on the secondary for repeatable results. A unique cascade feature enables the use of one power supply with several workstations. They can be integrated with either AMADA WELD TECH MH-1501 or KN-200A weld heads, providing fast follow-up and allowing for complete metal fusion without weld splatter.
The weld monitor captures weld data and makes instantaneous comparisons to a known good reference, providing an alert when conditions fall outside of defined weld limits. The data can be additionally used for advanced analysis in statistical process control programs or overall equipment efficiency programs to provide information on production efficiency. The data is stored in a database for tracking and tracing purposes.
Safety features include anti-tie-down buttons to safely initiate the weld cycle and shielding to protect the operator during production. The adjustable electrode approach to controlling pressure and speed helps to facilitate safe handling and avoids damage to fragile parts.
New Cobot Model Offers 35% More Reach and Capacity
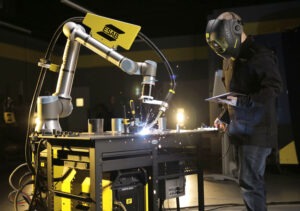
ESAB Welding & Cutting Products (North Bethesda, MD) now offers a second ESAB cobot option for MIG and pulsed MIG welding applications on steel, stainless steel and aluminum alloys. The new 5’-x-10’ table with UR20 (Universal Robots) robot arm provides 35% more reach and a 67% higher payload to accommodate larger parts. The new system uses the same software app that runs on a standard smart phone or tablet (Apple iOS or Android) and “Smart Puck” to hand-guide the torch and record its position with the push of a button as ESAB’s original Cobot (32”-x-48” table and UR 10e robot arm). Unlike the complex programming pendants of other cobots, the ESAB cobots enable operators to create a weld sequence as simply as they can create a song playlist.
The ESAB cobots feature a Universal Robots UR20 or UR10e industrial robot arm. UR is the automation industry’s leading provider of cobots and has an installed base of more than 75,000 cobots. Welding components include ESAB’s Aristo® 500ix pulse power source, the RobustFeed U82 wire feeder, an air- or water-cooled torch and accessories. The ESAB cobot costs a fraction of a pre-engineered robot cell, does not require a programmer, ships quickly and deploys in hours.
A Siegmund 5’-x-10’ or 32”-x -48” welding table organizes components and enables moving the cobot around a shop. The entire package ships on a pallet typically within two-to-three weeks of ordering from a distributor. Set up takes a few hours following step-by-step instructions accessed with a QR code. If a user has the skills to set up an industrial MIG system, they have the skills to start automated welding with the ESAB cobot.
ESAB also offers a cloud-connected software app for free, fast in-app support from a team of experts that respond to inquiries in two-minutes or less, and there is access to knowledge articles and an extensive list of tutorials. The app automatically stores weld sequences, enabling them to be recalled even if they are deleted from a device. Users can add charts to track production data and consumables use, as well as share part programs between cobots.
A “pro plan” for the software is also available, which extends chart visibility from seven-to-30 days and enables users to export chart data, among other functions.
“When I first saw the ESAB cobot, it was exactly what I had envisioned,” said Brett Skyvington, president and robot programmer of Skyvington Manufacturing Inc. “It actually lived up to the advertisement hype about how easy it was to program — we had guys in the sales demo writing programs on it in the first 40 minutes.”
Reliable and Flexible Solution for Robotic Welding
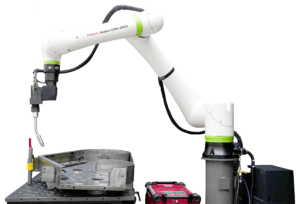
FANUC America Corp.’s (Rochester Hills, MI) CRX-25iA welding collaborative robot (cobot) offers a 30 kg payload and 1,889 mm reach. FANUC’s collaborative robots are easy to use and flexible solutions for companies looking to improve productivity and solve labor issues. FANUC’s entire series of CRX collaborative robots are reliable, flexible, and designed for eight years without maintenance. Easy-to-use interactive programming allows operators to teach points using hand guidance or a Tablet TP with drag and drop icons. In addition, all FANUC CRX welding cobots support FANUC’s advanced features including iRVision®, Touch Sensing, Servo Torch, Thru Arc Seam Tracking (TAST and Multi Pass (MP).
New Extraction Systems and Ergonomic Fume Extraction Torch
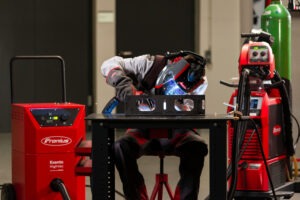
The greatest possible protection from welding fumes is more than just compliance with standards. Going beyond the standards shows companies take responsibility for their welding specialists, and everyone working in their immediate vicinity. To assist, Fronius International (Portage, IN) offers the user-friendly Exento extraction welding torch and two mobile, high-performance Exento extraction systems as effective protection against welding fumes.
These new extraction solutions are a perfectly coordinated duo, consisting of the ergonomically designed Exento fume extraction torch and the compact, mobile high-vacuum extraction system Exento HighVac. This combination is particularly effective for MIG/MAG welding, removing welding fume as soon as it is created. Thanks to the high-quality filter, the Exento HighVac mobile extraction system eliminates more than 99.9% of the captured welding fume particles.
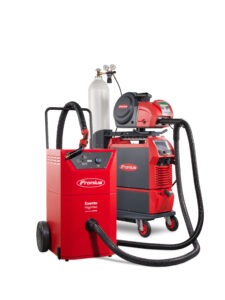
The Exento LowVac is a low-vacuum extraction system suitable for all welding processes, such as MIG/MAG, TIG, and MMA, with an impressive flow-optimized extraction hood design. As a result, significantly less extraction arm tracking is required than with conventional systems.
With the newly designed and EN ISO 21904-1-compliant Exento fume extraction torch, welding fume is captured with pinpoint accuracy, before it can spread. In the design phase, the development team paid particular attention to optimal ergonomic design and easy operation. For example, the desired extraction level can be controlled directly on the handle with a bypass valve. Rubber inserts ensure a non-slip grip, and the included LED lighting proves useful when welding in dark areas, and for quality control. With three different choices of user interface, from a torch trigger on the top to an up/down rocker and the JobMaster, there is a torch type for every welder. The torch also offers significantly more freedom of movement while welding through the use of the ball joint that attaches it to the 1.3 meter long, leather-protected hose.
Weld With Two Times the Clarity
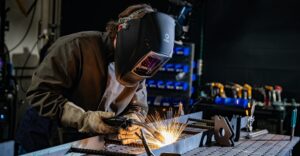
Miller Electric Mfg. LLC’s (Appleton, WI) ClearLight 2.0 is the latest auto-darkening lens technology from Miller, designed for welders by welders to deliver two times better visibility before, during and after every weld.
ClearLight 2.0 Lens Technology provides two times better clarity vs. the leading 1/1/1/1 lens benchmark as measured by the ANSI Z87.1 visibility test. ClearLight 2.0 allows a greater range of colors to pass through the lens, which allows for a more natural view eliminating the artificial blue, green or yellow tints when helmets are down for superior visibility. Also, ClearLight 2.0 increases contrast and clarity, which gives welders a clear and detailed view of the workpiece, puddle and wire — making it possible to create more accurate, high-quality welds. This can also help to further productivity and reduce rework for the benefit of an operation’s bottom line.
Thanks to the continuous visibility between light and dark states, ClearLight 2.0 lens technology also increases welder comfort by eliminating the need to constantly flip the helmet up and down. Less time with the helmet up also helps decrease eye strain, reduce neck strain and fatigue, and improve protection against preventable injuries.
ClearLight 2.0 Lens Technology is offered in numerous Miller® auto-darkening welding helmets, including the Digital Performance™, Digital Elite™, Digital Infinity™ and T94™ series.
New Series of Fume Extractors Available in Three CFM Ratings
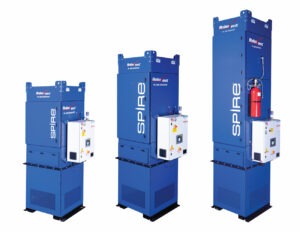
RoboVent (Sterling Heights, MI) has released an updated modular version of its popular Spire™ robotic weld fume extractor. Known for its small footprint and versatility, Spire is now available in three sizes and CFM ratings to accommodate a greater range of airflow requirements. The Spire series is designed specifically for robotic weld fume collection.
With three sizes, the new Spire series allows manufacturers to tailor their dust collection system to their exact needs for greater energy savings and lower overall operating and maintenance costs. “The new, modular Spire can now be sized to better meet the needs of manufacturers with smaller robotic cells or individual robots,” said Rick Kreczmer, president, RoboVent. “You don’t always need the 5,500 CFM that the full-size original Spire provides. We now offer Spire in three sizes, so manufacturers aren’t paying for airflow they don’t need.”
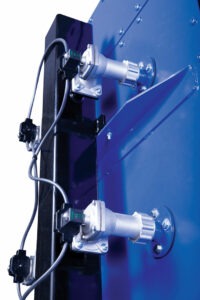
All of the Spire units have a footprint of just 36”-x-36”, or about the same size as a wire barrel, giving it the smallest footprint per CFM in the industry. All three units will retain the same small footprint as the original but will have different heights to accommodate different filter configurations.
The modular system was designed for energy savings and versatility. The units are ducted directly to the weld cell, eliminating the need for complicated centralized ductwork. And since they are small, they are easy to move with the cell if production lines change. “We designed Spire as a cost-effective and versatile alternative to centralized, ducted dust collection systems,” said Alysha Yinger, director of engineering, RoboVent.