Why Every Shop Should Invest in Tool Holders
When you put real thought into your selection of tool holders the job goes off without a hitch, even faster than anticipated.
Posted: April 23, 2024
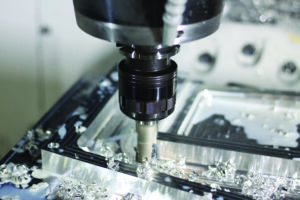
Imagine a machine shop is replacing some equipment when it receives an order for a run of valve bodies. The order is big, and the only equipment left to upgrade is a set of tool holders. The shop owner, in a hurry to get started, doesn’t put much time or thought into selecting his tool holders. He just picks a brand he’s heard of and gets to work.
At first, the run goes well. However, runout accumulates faster than expected, ruining finishes and causing rework. Several workpieces have to be scrapped altogether. The end products still meet specifications, but the job took longer than originally planned. The shop owner isn’t sure he’ll get orders from that client again.
All this could have been avoided if the shop had put a little more thought into its investment.
Common Misconceptions
Unfortunately for our hypothetical shop owner, sometimes even experienced operators make assumptions that lead to bad decisions. Here are a few common misconceptions:
- Cost is king. A higher or lower price doesn’t always correlate with higher or lower quality. But owners looking to save money, or owners who want “premium” equipment, might look at the price tag first and other factors second. In reality, cost is just one factor out of many — you shouldn’t flinch at higher prices, but you shouldn’t treat price alone as an indicator of quality either.
- One size fits all. Some companies claim to offer “universal” tool holders that can accommodate any need. This “one size fits all” claim is often misleading, however, as these tool holders are often only compatible with a single clamping option. By contrast, BIG DAISHOWA offers a wide range of tool holders to meet the specific needs of each project — collet chucks, mechanical milling chucks, hydraulic chucks, shrink fit holders, side lock holders and end mill holders, for example.
- Some metrics aren’t as important. While some metrics may draw more attention as you select your tool holder, all deserve equal consideration. Think about precision in taper and flange specifications. An operator might give them less attention because they’re more focused on material composition. Or maybe they prioritize clamping force above all else. Whatever the reason, some metrics go overlooked.
- Clamping force is universal. Speaking of clamping force, it’s so fundamental that some operators may assume every tool holder hits a similar baseline. As a result, they might prioritize other metrics. Unfortunately, not every manufacturer meets that expectation. Even if every past tool holder offered similar levels of clamping force, shop owners must always give it thorough consideration.
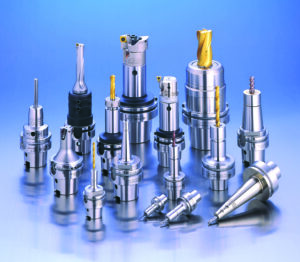
BIG DAISHOWA uses carefully selected materials and strict control of dimensional accuracy for optimal quality, offering a wide range of standard holders to meet all production requirements.
These are only a few of the many misconceptions that drive operations to make less-than-ideal choices when picking tool holders. An owner might still get good performance out of the wrong holder, but eventually, even minor issues will pile up and throw an entire operation off track.
Key Benefits
If you take the time and energy to invest in an ideal tool holder, your shop will see some serious benefits.
- Maximum precision and accuracy. This one may seem obvious but think back to that misconception about universality. Just because a tool and tool holder are compatible, that doesn’t mean they offer the best fit possible. The better the fit, the higher the rigidity, the lower the chatter and the higher the precision. Whether you’re working with dual-contact or traditional tool holders, the right one for the job will get you the most accurate results.
- Work that’s tailored to your needs. Think through the jobs your operation often takes on, as well as any fields you might expand into in the future. If you have a clear picture of your current and future needs when you make your investment, you’ll get better results down the line. Meeting specific needs might require buying multiple individual tool holders, investing in modular systems or even both. But either way, the result is the same: higher quality and consistency.
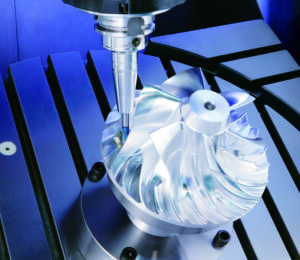
Increased tool life. Less chatter doesn’t just mean higher precision. It also means less stress on other components. This lengthens tool life overall, protecting everything from your cutting tools to the spindles themselves. It also means less unplanned downtime or rework. You’ll get the most possible work out of every tool — and have a better sense of when they’ll need replacement.
- Savings in the long run. High prices don’t always mean high quality, but sometimes, a more expensive tool holder may be the one that best suits your needs. In these cases, don’t be put off by sticker shock. You may pay more upfront, but in the end, you’ll get more use out of every tool and better results with every workpiece. That’s less money spent, and more money earned, over the course of the tool holder’s life.
- New benefits from new technologies. You may already be satisfied with the tool holders you have, but don’t let that put you off from considering an upgrade. Tool holders have advanced by leaps and bounds in the last few years alone. Newer models offer features older models may not. For example, some holders have embedded sensors, which can flag issues with workpieces or tools as soon as they occur. Others might use advanced coating technologies to enhance durability. There’s a world of new features out there and shops can seriously benefit from embracing them.
Let’s go back to that run of valve bodies. This time, the shop owner puts real thought into his selection of tool holders. He ends up spending a bit more money and buying a few more holders than he’d originally planned. But the job goes off without a hitch, even faster than anticipated. The client is pleased, and the shop gets more work — a win-win situation, all because the owner understood the importance of investing in the right tool holders.