Refine Welding Workflow with Top-notch Surface Prep and Finishing Tools
Minimize defects, and most importantly, keep your operators safe with the latest surface prep tools.
Posted: June 14, 2024
The quality of your surface preparation and finishing processes leads to better product outcomes and increased efficiencies.
New Line of Right Angle Grinders and Sanders
Dynabrade, Inc. (Clarence, NY) has introduced a line of 1.3 hp air tools. These new high quality air tools are available as a Right-Angle Disc Sander and a Right-Angle Depressed Center Wheel Grinder.
Available in 4”, 4-1/2” and 5” diameters, the tools are excellent for fast stock removal, metal clean up prior to welding, removal of weld beads and various material removal applications. The Depressed Center Wheel Grinder is available in either 12,000 rpm or 13,500 rpm. The grinder is ideal for use with Type 27 Grinding Wheels. The 1.3 hp Disc Sander, available in 12,000 rpm, is for use with a wide variety of coated abrasives.
The tools feature a governor assembly for maintaining rpm under load. Also included is a safety-lock throttle to prevent accidental start-up and a spindle lock for fast, easy abrasive/wheel change. A two-position side handle for left or right-hand use is included. This vibration-dampening handle also reduces vibration to the operator’s hand. This line of air tools was also designed with a Wick Lubrication System, which extends gear life when the tool is properly lubricated with gear oil. Also included is a 360° rotational exhaust for directing the exhaust away from the operator. The Depressed Center Wheel Grinder also includes a safety guard and wheel flange kit.
Next Advancement in Angle Grinders
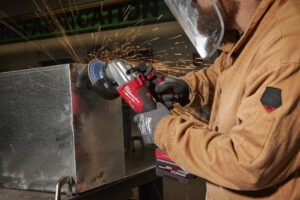
Milwaukee Tool (Brookfield, WI) provides the next advancement in angle grinder technology with the introduction of their M18 FUEL™ 4-½”/5” Dual-Trigger Braking Grinder. With dual-trigger activation, a permanent side handle, and AUTOSTOP™ kickback control, this new cordless angle grinder gives users greater control on the jobsite.
With a trigger on the braking grinder’s main barrel and a secondary trigger on the side handle, the dual-trigger activation requires two hands to stay on the tool for operation. The new-to-world side handle design is permanent to the tool, ensuring compliance on the jobsite. For added user control and accessibility in hard-to-reach areas, the side handle can be positioned in 15 different orientations: tilting from 0°-to-90° and pivoting to the left, top, and right. An anti-vibration design reduces vibration in the side handle, increasing user comfort during extended use.
For the first time, Milwaukee’s AUTOSTOP kickback control is included in an angle grinder. An electronic clutch detects extreme movement and shuts off the tool, helping prevent injuries from severe kickback. RAPIDSTOP™ braking stops most wheels in under one second. Featuring four variable speed settings between 3,500 rpm and 8,500 rpm, users have additional control in a variety of materials. As an additional benefit, the grinder is compatible with ONE KEY™, which allows users to sync the tool wirelessly with their mobile device or desktop.
Milwaukee is committed to improving productivity by providing performance-driven and trade-focused solutions so users can perform an entire day’s work on one battery system.
Buffing Wheels Achieve Superior Results and Require Minimum Compounds
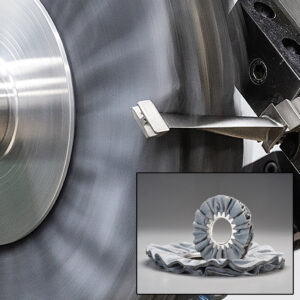
Saint-Gobain Abrasives (Worcester, MA), one of the world’s largest abrasives manufacturers, offers innovative Norton FAB (Fixed Abrasive Buff) buffing wheels that virtually eliminate the need to use buffing compounds. Norton FAB wheels feature a unique design that incorporates abrasive grains into the buffing wheel and consistently results in excellent single digit Ra values ranging from 1-to-5 Ra. Norton FAB wheels are tear resistant, waterproof and durable, providing significantly longer life than traditional cotton buffs.
Due to significantly decreasing the need for buffing compounds, Norton FAB wheels offer a more efficient, cleaner and safer way of buffing. There is less cumbersome, time consuming clean-up in buffing operations and post-clean-up processes. Without the requirements to purchase, apply, clean-up, and dispose of large amounts of compound, costs are minimized. Also, less buffing compound improves worksite safety and reduces the environmental impact of compound disposal.
Norton FAB wheels have a premium silicon carbide abrasive which is uniformly dispersed and applied to both sides of the cloth, resulting in more consistent buffing performance. Norton FAB wheels can be easily incorporated into robotic buffing applications. Key applications for the wheels include automatic or semi-automatic buffing, cut buffing and mush buffing in a wide range of markets such as automotive, hardware, oil and gas and more. The wheels are effective on hard alloys as well as soft metals such as aluminum and brass.
Cutting, Grinding and Combo Wheels Cut Through Inefficiencies
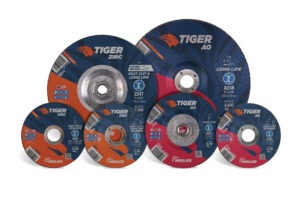
Weiler Abrasives (Cresco, PA) offers the next evolution of abrasives — the Tiger 2.0 zirconia alumina and aluminum oxide cutting, grinding and combo wheels. Designed for demanding metal fabrication industries such as shipbuilding, pressure vessel and heavy equipment fabrication, these abrasives help cut through inefficiencies, safety issues and labor shortages that prevent companies from doing their best work.
In addition to offering fast cutting speed, Tiger 2.0 wheels last up to 40% longer to increase efficiency in operations’ cutting and grinding applications. The wheels feature an award-winning blotter design that includes an industry-first, patent-pending Optimum Use Line. The line is a visual indicator that helps the operator use the wheel to its full life. In some cases, users experience three times more efficiency than with their previous abrasives.
Tiger 2.0 grinding wheels feature anti-chipping technology, an advanced bond formulation that reduces uneven edge wear and chipping to improve safety and the user experience and extend wheel life.