Steel Warehouse is a Trusted Solution
When Nathan Lerman started Steel Warehouse in 1947 in South Bend, Ind., with partner Herman Segal, he couldn’t have imagined the scale of the products and services the company would someday offer, as well as the incredible growth the company…
Posted: June 17, 2024
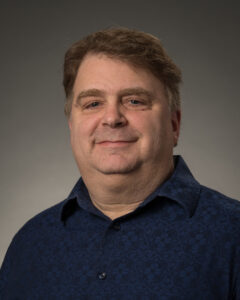
When Nathan Lerman started Steel Warehouse in 1947 in South Bend, Ind., with partner Herman Segal, he couldn’t have imagined the scale of the products and services the company would someday offer, as well as the incredible growth the company would experience, expanding to a global presence. (Segal sold his interest to Lerman in the 1960s.)
Seventy-seven years later, based on a long tradition of strong personal relationships with its customer base, Steel Warehouse’s team continues to implement its core principle of taking a deep dive and understanding the needs and challenges of its customers. Which can be a challenge in an age when information can be found online immediately.
Listening to customers and understanding their needs goes beyond the processing aspect of projects, noted Marc Lerman, chief commercial officer and executive vice president for Steel Warehouse. “It is really understanding what the customers are trying to do and trying to understand their pain points and how we can help them solve the problem,” he said.
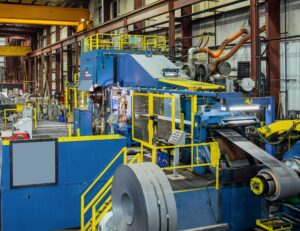
For example, he pointed out a “memory free steel.” “For the temper-passed cut to length, we have a temper mill in line with our leveling,” Lerman said. The company added machinery in the late 1990s and early 2000s to support value-added functions. “We realized there was a big need for what today is pretty standard: memory free steel,” Lerman said. “Which means if you hit it with the laser, you get spring back unless you have the memory eliminated or reduced significantly. So that’s what our equipment did. It was not our innovation. But we took it and ran with it because we felt strongly that it was a really good idea, and we have eight of those lines now. Those were very unique in the beginning and they’re less unique today.”
Expertise in a Vast Array of Steel Products
Steel Warehouse carries a range of products, and is primarily a flat roll processor, Lerman noted. The company’s processing capabilities include temper pass cut to length, pickling, blanking, slitting, shearing, laser beveling and plasma cutting, stretcher leveling and temper pass coil to coil. Services include metallurgical consultation, inventory management and JIT delivery.
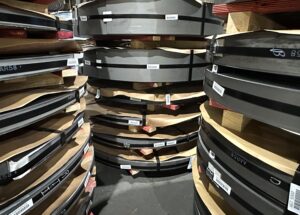
Hot rolled oiled and pickled (HRPO) steel is just one way for Steel Warehouse to differentiate its products and services. With the continuous coil-to-coil and sheet picklers, the steel goes through a series of hydrochloric acid tanks or applications to remove the scale that forms on the surface in the steel-making process. This scale-free surface is then coated with either electrostatic oiling or another controlled oiling process to keep the newly cleaned surface protected.
Lerman said that when it comes to the pickling process, Steel Warehouse has spent a lot of time and effort being able to pickle heavy gauge steel in a high-quality way. “It is not for every application,” he said, as it is ideal for customers that are experiencing challenges when processing materials and scale is getting in the way of painting or welding, as examples. For one customer conducting pre-processing of their parts, as well as post parts processing before sending the parts through the paint line, the HRPO product eliminated an entire process, Lerman pointed out. The pickled product also assisted the company in extending the life of its dies due to the fact that scale is rough on dies being used to stamp out or press products.
When compared to hot roll or blasted material, the surface cleanliness, smoothness and consistency produced via the pickling and oiling process delivers benefits to applications including stamping, laser cutting, painting, welding, press braking and roll forming. Steel Warehouse is the only company in the world offering hot-rolled-pickled and oiled steel -sheet and plate from .080″-to-2″ thick (1” thick from coil) and 30”-to-96” wide.
Forward Thinking Innovator
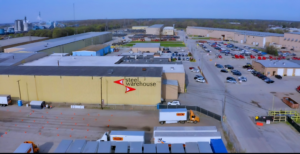
Lerman said that in addition to listening to customer input regarding products, Steel Warehouse also considers geography. “We have invested in various places around the country, and in Latin America, with a location in Mexico and one in Brazil,” Lerman noted. “We are also in the process of opening a new location in Hickory, N.C.” That facility will feature a cut to length line for sheets and will conduct some burning for customers in the region.
In addition to maintaining a number of facilities to serve their customer base, the Steel Warehouse team continues to innovate and develop products that allow customers to think out of the box regarding design and applications. Lerman noted that market changes and trends cause people to innovate, which is a good thing.
For example, Steel Warehouse has metallurgists on its staff. That team works with customers, primarily those involved in fabrication, to develop alternatives when producing parts so they might present cost saving alternative solutions to their OEM customers. Lerman said the company has a great understanding as to what mills all over the world are making, enabling the team to apply their vast expertise and knowledge in steel processing.
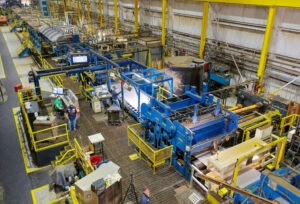
“We know how it [steel] is going to react in the different processes,” Lerman noted. “We marry up the products with the chemistry and mechanical properties and that has been successful.” For example, the AR450 abrasion resistant product isn’t made in a light gauge material in coil and is typically only available in plate. Working with one of its mill partners to develop the product, Steel Warehouse now offers the product in coil in widths which weren’t available in the past.
“If you’re making a dump body and you need an abrasion-resistant (AR) product, or if you’re making a cement mixer or something like that, those are examples of where we’ll sit down with the customer to explain the benefits of an AR strip product,” Lerman said. While the product is expensive, it allows customers to lightweight their products, such as a dump body or with a product that is hauling a payload. The light gauge coil applications pique a customer’s interest when it comes to lightweighting products, eliminating steps and saving money.
In other novel initiatives, Steel Warehouse is researching new ways to utilize its temper level line capabilities to achieve even flatter and higher quality steel sheets. The company is underway with trials and plans to announce new capabilities soon.
In regard to the ever-evolving world of industrial robotics and automation, the staff at Steel Warehouse is also ready to lend its expertise and insights to customers. The team encourages customers to think in-depth about their product as well as the robots and automation they are bringing into the company and how their parts production will react with the type of equipment and services they are buying. Customers may require different products or products with enhancements that they don’t currently have in place, such as those to achieve surface quality flatness.
“Flatness has gotten more and more important because if you’re doing a lights-out operation you need to have that consistency in the quality or its going to be more challenging,” Lerman noted.
The Steel Warehouse team has adapted and come out on top of challenges thrown at the industry throughout the years, such as steel price volatility. Lerman noted the landscape is much different than in the 1990s when there were anywhere from 20-to-30 steel mill options regarding flat roll; today there are approximately six mill options.
In the 2000s, the price of steel per ton skyrocketed in a span of just a few months. Suppliers such as Steel Warehouse had to adjust from selling based on the ability to offer lower prices to increasing the prices customers would need to pay for products. “We had this kind of transformation to the industry that completely flipped,” Lerman noted. “I think it was revealing at the time, the way the environment was at that time. It was very, very difficult to sell.”
However, “all of the challenging and difficult times like that one really helped shape our company and helped us rethink things,” Lerman pointed out. “In the end, going through tough times really helped us a lot because what we realized was that if we’re — and I’m not speaking for other companies — but if we’re going to sell somebody, we really have to sell them on value instead of price because price is really not sustainable for our solvency. We’re not going to last if we’re having to chase the last dime.”
Nathan Lerman would no doubt agree.
Get Physical
At its South Bend, Ind., headquarters campus, Steel Warehouse has added a brand new wellness amenity, which is available to all of its nearly 500 employees. The company refurbished an empty building in the middle of its nearly 1 million-square-foot campus to create an ultra-modern gym, complete with a full complement of machines and equipment, as well as a company trainer.
“We view our employees the same way we look at our customers and suppliers: as partners, part of our family,” said Marc Lerman, chief commercial officer and executive vice president for Steel Warehouse. “I don’t think there are too many service centers that have a gym within the middle of their plant.”
The gym is another benefit the company can offer its employees. The owners pride themselves on being a family-owned company and taking a longer-term view, one not beholden to shareholders. “I think that is a differentiator when you are dealing with us,” Lerman noted.
A Deep Dive into Pickled Steel
The scale-free surface produced by hot-rolled-pickled and oiled (HRPO) steel or “pickling” improves metal fabrication processes such as laser cutting, forming, bending, stamping, welding and painting. Much like blasting, pickling removes mill scale from a steel substrate surface. However, there are significant differences in the descaling technologies; blasting uses abrasives particles and pickling uses a chemical process to remove the scale. Blasting creates microcraters on the surface of the metal, and it requires the application of a coating for rust protection. These surface inconsistencies can impact laser beam focus and cut quality, as well as creating a duller paint finish.
When pickling steel, the chemical process is immediately followed by drying and oiling, which provides a clean and consistent surface on the plate, resulting in ideal surfaces for painting and fabricating processes. Fabricators can gain up to 25% faster cuts in the laser cutting process, and realize closer tolerances and nesting, resulting in less scrap between parts.
Regarding stamping, press braking and roll forming processes, users benefit from a deeper draw, and closer tolerances because there is no sticking to the die, ensuring longer die/tooling life.
When it comes to welding processes, pickled steel products eliminate grinding of weld spatter, as well as achieving precise measurement and robotic welding of larger parts without rework.
Regarding finishes, glossier finishes are achieved with less paint; and projects use up to 30% less primer.