The Future of Production Monitoring in Metalworking
There are two key items to highlight as manufacturers adopt solutions to digitize their operations: context is king, and insights are greater than just mere data.
Posted: July 31, 2024
In the ever-evolving landscape of manufacturing, the ability to monitor and manage operations efficiently has always been pivotal. As market conditions become increasingly competitive and the availability of skilled labor diminishes, metal fabrication and machine shops are compelled to innovate and adapt. This journey from past practices to modern strategies is not just about technological advancements; it’s about survival.
The evolution from rudimentary machine monitoring tools to sophisticated, insight-driven systems marks a significant shift in how manufacturers manage and improve operational efficiency. Traditional tools for tracking production are giving way to advanced platforms and ecosystems of solutions that don’t just aggregate data but refine it into actionable insights.
With the commoditization of IoT devices and software tools, manufacturers don’t always need more “data”, but rather need to know how to make better decisions with data, as well as be able to automate manual tasks.
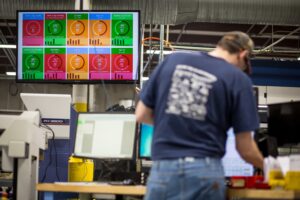
As a result, the future of production monitoring solutions will be characterized by several capabilities that enable manufacturers to get as much value out of their data as possible. It is this need for data access and actionability that is driving innovation in the market, and ultimately carving out the next generation of production monitoring.
Let’s discuss this “future state” of production monitoring. However, keep in mind that these capabilities are, to varying degrees, already deployed in fabrication and machine shops today.
“Basic” Machine Monitoring is Officially a Commodity
Although there has been some degree of innovation in the machine monitoring space, most of the market offers relatively basic solutions. These systems often capture limited data via the application of a sensor or capture data from only certain makes of equipment.
We see these systems come onto the market in the form of basic, inexpensive point solutions, or as extensions of existing products and systems, such as a machine builder offering monitoring capabilities or an MES appending a data collection tool. Typically the quality and actionability of the data hinder the value creation of these tools, enabling them to serve only basic use cases.
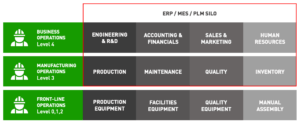
There is differentiation that exists, but it tends to occur at the upper echelon of the market. Advanced production analytics solutions offer the complete data value chain, from deep machine data collection, standardization, and contextualization, to visualization, insight identification, notifications, and workflows, as well as the flexibility and extensibility to integrate with other systems. Rather than providing basic machine performance data, these platforms offer a source of truth for overall shop floor performance and enable better, faster decision-making every single day.
We will see an increase in both market entrants as well as the adoption of these more advanced solutions, especially for mid-size and enterprise organizations. Basic machine monitoring solutions will fail to meet the advanced use cases that the next-generation manufacturer requires.
Data ≠ Answers
We often forget that data is a means to an end. After the capture of data, it then needs to be compiled and structured in such a way that it can be consumed. At that point, the data then needs to be analyzed. And only at that point is there the chance that an insight will be generated which allows us to make a decision or take action.
The market, both vendors and consumers, have been highly focused on getting data. Manufacturers want accurate, real-time data and complete production visibility. But once again, this is only part one of a multi-step process in driving value with data.
The problem is that many of the data and analytics tools that manufacturers rely on, provide only that: data (and maybe analytics). There are a few ways that these solutions will be rapidly improved in the coming years as solutions move from descriptive to prescriptive.
There are two key items to highlight as manufacturers adopt solutions to digitize their operations:
- Context is King:
Raw information on machine performance is helpful, but without knowing information such as when the machine was running, what operator was at the machine, what part was running, what work order the job was connected to, and how the job typically performs, the data lacks value.
This key operational and business information needs to be tied into the production analytics, or the production analytics need to be pulled into management systems; ideally both. Solutions such as those provided by MachineMetrics are already doing this, with more advancements quickly approaching, to ensure that the gap between IT and OT is successfully bridged.
- Insights > Data:
With the sheer amount of information that exists across all the operations and machines being managed on the shop floor, it isn’t surprising how difficult it is to figure out where the biggest opportunities are for improvement.
Automated, accurate, real-time data collection gives us the source of truth to rely on, but does not necessarily provide us the insights to take action on. Advanced solutions are turning production data into key insights at the machine, plant, and enterprise levels. The analytics tools of tomorrow will continue to shift toward predictive and prescriptive analytics, calling out the most pertinent information.
The Proliferation of Specialized Software Systems
ERP and other enterprise systems are unlikely to go away anytime soon. However, we are seeing the proliferation of software systems for the many functions within a manufacturing operation. While users may have historically relied on an ERP or other manual “lean” systems, they are increasingly leveraging specialized software solutions to manage different functions and processes.
Some examples include maintenance systems, quality control software, inventory and warehousing solutions, and quoting software. These specialized solutions are far more capable in their given domain than a generalized management system, like ERP or MES. This, however, does not necessarily solve the data issues manufacturing has historically dealt with.
More systems lead to additional sources of data, creating a higher likelihood of discrepancies and a lack of data unification. These modern solutions must work as an ecosystem, rather than as purely individual systems. As a result, advancements in these verticalized systems, including production monitoring solutions, will result in seamless vertical and horizontal integrations.
This connected factory is in some ways being achieved but there is still a ways to go. Next-gen solutions will require pre-built integrations across shop floor and enterprise systems, as well as an open API to ensure data can get where it needs to be.
These capabilities will continue to be built out to make integrations easier to deploy and more effective in their capabilities. In the case of ERP, this involves the ability to enable data to travel bi-directionally between systems. This is perhaps the most important integration that must be enabled for shop floor systems.
Navigating the Future of Production Monitoring
Today’s production monitoring landscape is fraught with challenges, primarily marked by solutions that offer fragmented data, lack actionable insights, and operate within silos. These shortcomings underscore the need for improved analytics solutions that move beyond mere data collection and focus on generating actionable insights.
There are a number of point solutions and legacy management systems at the forefront of this transition, offering solutions that capture deep machine insights and translate data into meaningful, actionable insights that deliver value for the shop floor and bottom line.