Think Outside the Generator Box
Power generation packager adds ESAB Cobot, updates WPS from TIG to MIG and increases production five-fold for a critical part.
Posted: July 18, 2024
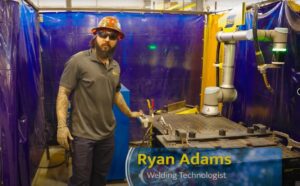
Your energy is your most valuable resource – package it wisely. At Acoustical Sheetmetal Company (ASC), Virginia Beach, Va., sound attenuated and weather-protective packaging for on-site power generation equipment ranges from economical skin-tight enclosures to entire multi-unit power plants. The company’s weatherproof enclosures serve as control rooms, housing generators, pumps, compressors, switchgear and other specialty products. ASC was founded in 1994 and has since grown to 310,000 sq. ft. of manufacturing space on 28+ acres, operating from two campuses and employing approximately 550 people, of which about 200 are welders.
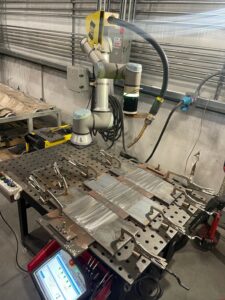
The foundation of a generator package is a diesel fuel cell made from ¼-in. steel plate, I-beams and C-channel. The generator is mounted on top and then entirely covered by a sound attenuated sheet metal enclosure. A typical assembly is about the size of a semi-trailer and weighs 90,000 to 160,000 lbs. A series of lifting hubs/swiveling D-ring assemblies welded to the side of the fuel cell secure the package to a double drop trailer during transportation and are used to hoist the package into place. The lifting hubs define the need for “mission critical” weld quality — and that’s exactly where ASC deployed an ESAB Cobot (collaborative robot).
Exploring Automation
ASC’s current owners acquired the company on February 1, 2019. Since that time, the company went from about 100 to 550 employees.
“And as we’re growing, we look at our technology and what we can do to introduce efficiencies into the manufacturing process,” says ASC Director of Operations Brandon Allen. “We have mechanized track welders and have been exploring robots because we fully understand how helpful they can be,” says Allen, who came from a highly automated packaging industry.
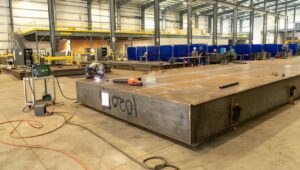
“The problem with generator packages is that they are so big. Trying to put them in a robotic cell just doesn’t work,” he says. “Then we were introduced to cobots, which was really interesting, because they prompted us to think about subassemblies that could be automated.”
To begin their cobot journey, Allen and Adams initially asked another cobot provider to make some test welds on sample parts and they “repeatedly fell on their face.” Fortunately, Allen and Welding Technologist Ryan Adams were introduced to the ESAB Cobot at an event held in conjunction with FABTECH 2022.
“We worked with ESAB Account Manager George Myers and the ESAB automation team. We sent them plates and had them make test welds,” says Allen. After initial success with test welds made at ESAB’s Technology & Research Center in Hanover, Penn., ASC brought in a cobot to test the system in house.
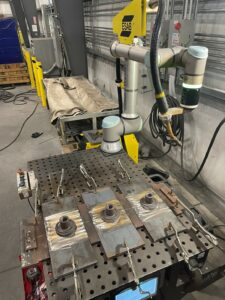
The ESAB Cobot features an Aristo® 500ix heavy industrial power source with a 500-amp output at 60% duty cycle (the same power source ASC uses for some of its manual welding), a RobustFeed U82 wire feeder, Universal Robots’ robotic arm and a Siegmund weld table. To create weld paths, the system uses a software app that runs on a standard smart phone or tablet (Apple iOS or Android) and a “Smart Puck” to hand-guide the torch and record its position with the push of a button.
“The ESAB team put in the time and effort. They proved that the cobot could weld really well,” says Allen. “At that point, it was just a no-brainer to purchase the ESAB Cobot and start welding the lifting rings.”
TIG to MIG
The lifting hub is made from 4340 ultra-high strength steel. The base or “puck” of the hub is welded to an 8-in. wide, ½-in. thick section of A36 bar stock. That plate (which can vary from 1- to 2-ft. long depending on the size of the fuel cell) is welded to the side of the fuel cell with the gas-shielded flux cored process. The company that provides the hubs recommended the TIG process, which ASC followed prior to implementing the cobot.
“When the Cobot came into play, we asked them about switching over to spray transfer MIG welding,” says Adams. “They said that as long as we could do the testing and prove it meets all the requirements, they said it would be fine.”
After getting the cobot in-house, ASC went through two months of running weld samples, cross-sectioning and acid-etching welds in house, refining welding parameters and cobot variables such as torch angle, wire stick-out and travel speed.
“Once we got it to where we were pretty comfortable, we sent a welded hub to a third-party testing lab,” says Allen. “They ran a whole battery of tests, including radiographic, cut and bend, tensile and yield strengths. They ran the hub through every test pretty much that they have, and we passed every test flawlessly.”
Adams explains that the part of qualifying the new WPS involved substituting an ER90S-B9 filler metal.
“We went up to a 90,000 ksi wire instead of a standard ER70S MIG wire,” says Adams. “The as-welded part had a tensile strength in the high seventies to 80,000 ksi.” Other key elements of the WPS and ASC’s process include:
- Grinding the plate to shiny metal.
- Using a fixture to clamp three base plates to the Siegmund table.
- Pre-heating the A36 base plates to 100 oF using a rosebud.
- Pre-heating the 4340 steel lifting hubs to 350 oF using an oven.
- Using a jig made in-house to perfectly center the hubs on the base plate.
- Using the cobot to make two tack welds on each hub.
- Using a rosebud to maintain the pre-heat temperatures, as well as checking the interpass temperature with an IR gun.
Welding a root and cover pass on each hub. “We were getting about 10 to 12 arc restarts during the TIG welding process,” says Adams. “Now we have a start and stop for the root pass and one for the cover pass. That brings down the chance of having micro cracks and related issues. We also follow a post-weld process where the welded hub and plate assembly is wire-brush cleaned, time-stamped, and placed on a heating rack with a heat blanket to cool for one hour.”
“We weld the lifting rings in sets of three. With TIG welding, it took an hour to make three and now we have it down to 12 minutes, or four minutes per plate, and they’re the most critical welds on our units,” says Justin Mitchell, the cobot operator.
With each fuel cell requiring eight hubs, the Cobot lowered total welding time from eight hours to 36 minutes, a 500% improvement in productivity.
“The cobot can do in an hour what was taking someone a day to do,” says Adams. “If I can add three more pieces to the Cobot that people were taking a day to do, I’ll have it running all day and getting the productivity of four people. I don’t have to worry about taking anyone’s job because I have so much work that their time is going to be redirected somewhere else. This is huge for us because skilled labor is very hard to find. It’s a win-win for everyone.”
Allen notes that, “like fabricators everywhere, we have challenges finding TIG welders who can make critical welds. Sometimes 15 months of training isn’t even enough time to become a proficient TIG welder.”
When it comes to training operators, Adams believes that watching a cobot work can help because it consistently demonstrates a proper contact tip to workpiece distance and torch angle.
“Personally, I’ve become a much better spray transfer welder by watching the cobot,” he says. “It takes away all the human errors.”
Longer Arms, Other Welds
Using the Cobot for the critical welding on the lifting rings has prompted ASC to consider adding other jobs to the cobot’s schedule. With the success on the lifting hub, the company is attacking other critical welds first.
“We’re starting to play with different arrangements. This includes the longer UR20e cobot arm and torches with different goosenecks that will give us more accessibility to joints on other parts of the fuel cell,” says Adams. “That’s one of my goals this year. It will also give Justin an operator working under him, as we start growing our robotic activities. I feel like we’re at 5% of the cobot’s potential.”
As a busy company trying to sell many units a year, each taking 12 to 25 days to build, along with a period of challenging employee retention, integrating ESAB Cobots into mechanized jobs is a positive move for everyone. Most importantly, ASC is confident it has a good partner with ESAB.
“I can tell you honestly, the biggest competitive edge and what really sold me on ESAB is the employees that you have and the customer service they provide. It’s second to none,” says Allen. “The ESAB team really worked with us on automation, and it’s been the same way on our Warrior and Aristo manual MIG machines.”