Abrasive Machining/Sawing/Finishing
IMTS 2024 will feature abrasive machining, sawing and finishing.
Posted: August 1, 2024
Pulse Cutting Saw and Other Saw Automation Solutions
AMADA Machinery America, Inc. (Brea, CA) will introduce the DPG150, Digital Profile Grinder. This is industry’s first profile grinder with a measurable digital projector. The profile grinder enables high-precision profile grinding with a new digital measurement, which dramatically improves productivity and part processing. Stop by to see how well the projector displays detailed shapes on a 4K monitor. To be showcased with the DPG150 is the SSR-6, Rotary Surface Grinder. This grinder provides enhanced usability and exceptional efficiency while the enhanced feed axis speed shortens setup time.
AMADA Machinery America will be in Booth N-237200 and will also showcase saw automation with various band saws, such as Pulse Cutting Saw with a power roller conveyor. The HFA360P, Horizontal Post Style Saw, will feature a modular material handling system with sorting bins.
Also on display will be the CMII75DG, Circular Saw, a high production saw which produces fast and straight cuts. The saw will feature a new modified loading system for both square and round bar material. The VT5063SW, Vertical Tilt-Frame, will feature a custom mini-handling system with a two-strand chain-loader and electric work ejector bar. This saw miters up to 60° left and right and will cut bundles.
In addition to band saws, the company will also feature the Spartan MSIW60D Ironworker, which has five workstations, with LED lighting, and has the strongest stripper in the industry.
AMADA Machinery America has more than 70 years of industry experience and is committed to helping customers deliver dependable service and top-quality work with exceptional grinding and sawing solutions. The company keeps its customers best interests in mind, maintaining the philosophy of “Growing With Our Customers.”
Abrasive Tools for Precision Finishing and Deburring
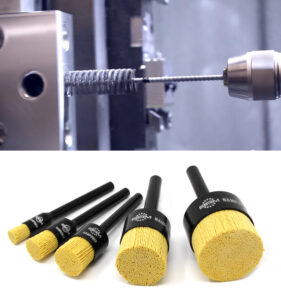
A Brush Research (Los Angeles, CA) invention, the FLEX-HONE® Tool, provides a superior surface finish with a non-directional or crosshatched pattern. Ideal for crosshole deburring, the tool can finish and deburr simultaneously in a single setup and can be run on any rotating spindle. Designed for a variety of automotive, hydraulic, pneumatic and industrial applications in sizes from 4 mm-to-36”. Fine grit hones in 400, 600, and 800 grit are available for finer finishing tolerances resulting in single digit Ra level finishes. Now available in diamond and CBN abrasive to efficiently finish and produce the proper edge radius on harder materials such carbide, ceramic and high nickel alloy steels. Brush Research will be in Booth N-237148.
For OD applications, Brush Research’s NEW Nampower End Brushes are available from ½”-to-2” in a high density, solid end brush configuration. These tools offer more cutting points for increased efficiency and performance. The aluminum, hard coat anodized cups hold advanced ceramic abrasive filaments that have lasted three-to-five times longer than the competition during testing. Available in four grits to accomplish even the most challenging of deburring and surface finishing applications. The tool is designed to be loaded directly into your automated machining center to get to work immediately with no special adaptors needed. These ceramic end brushes are the newest addition to our Nampower Premium Abrasive Nylon offering including disc and wheel brushes in ceramic and diamond filament.
New Advancements in Sawing Automation
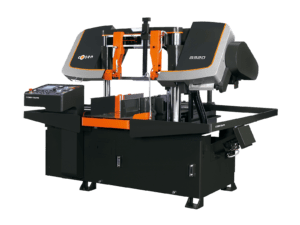
Cosen Saws (Charlotte, NC) is a global leader in band saw manufacturing with an expansive product line and a sales and service network covering all of North America. Voted the No. 1 sawing manufacturer by end-users in this year’s Metal Center News Top 10 equipment brands survey, Cosen Saws is excited to showcase its solutions at this year’s IMTS show. Cosen Saws will present a diverse assortment of cutting solutions and new technologies in automation at Booth N-236931. With more than a decade of exhibiting experience at IMTS, Cosen Saws is proud to exhibit at the show.
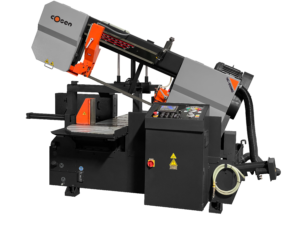
Cosen Saws continues to push the standards of sawing and deliver cutting-edge solutions designed to meet the diverse needs of numerous industries such as automotive, aerospace, steel construction, and more. At IMTS, Cosen Saws will showcase six different saw models, each of which are designed to enhance productivity, accuracy and safety. Visitors to Booth N-236931 will have the opportunity to witness these band saw machines up close and in person, with experts on hand to answer questions and provide additional insights into the company and its solutions.
Visitors interested in purchasing a Cosen will have the opportunity to take advantage of the show specials being offered, details of which will be released Monday, Sept. 9, the first day of the show.
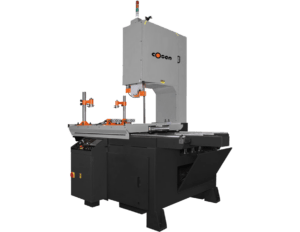
Cosen Saws will be showcasing the following products:
- G320: Fully Automatic, Dual Column Band Saw
Capacity: 12.8”-x-15”
- NC-510MG: Fully Automatic, Miter Cutting Band Saw
Capacity: 13”-x-20”
- C2: Fully Automatic, Dual Post, Dual Miter Cutting Band Saw
Capacity: 10.2”-x-11.8”
- SVT-6070S: Fully Automatic, Vertical Plate Saw
Capacity Height: 23.6”, Capacity Throat: 27.5”
- V-1822: Semi-Automatic, Manual Miter Vertical Tilt-frame Band Saw
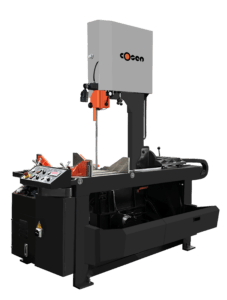
Capacity: 18”-x-22”
- SH-500M: Semi-Automatic, Scissor Style Miter Cutting Band Saw
Capacity: 11”-x -19.7”
Along with these saws, Cosen Saws will also be premiering new advancements in sawing automation. These technologies are designed to improve operator efficiency and enhance production flow. All automation technologies will be revealed and on demo exclusively at this year’s show, and attendees are encouraged to visit Cosen’s booth to learn more.
First in Sawing Innovations
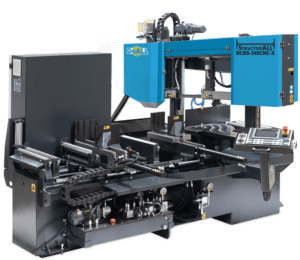
Visit the DoALL Sawing Products (Savage, MN) exhibit to view the ORIGINAL industrial band saw manufacturer and our continued innovations of all things industrial material cutting in Booth N-236949. Discover cutting-edge innovations that will increase your productivity and profitability.
Explore Our Industry Leading Lineup:
- StructurALL DCDS-340CNC-X: Producing precision and efficiency with advanced CNC cutting capabilities.
- TDC-400CNC Olympia Tube Saw: Ideal for tube cutting applications with high accuracy and productivity.
- Hercules DC-540CNC-A: Elevate your production with automatic, controlled precision.
- 400S StructurALL: Known for its precision miter cutting capabilities in smaller quantities. Still made in the USA.
- 2013-V3 with Glide Table: Unprecedented worker safety, accuracy and ease of use.
- Hercules DC-510CNC: High production solution that increases your entire shop’s output.
- Continental Series DC-330NC: Workhorse, easy to use automated sawing solution.
- DoALL Legacy Saw – Model J: Celebrating the legacy of DoALL, circa mid-1930s.
- Blade Line-up: Experience our entire range of industrial band saw blades in action.
- Cutting Fluids: Specially formulated to optimize your sawing operations.
Please note that the lineup of machines and products is subject to change.
Company Brings Its Machining, Testing and Assembly Talents
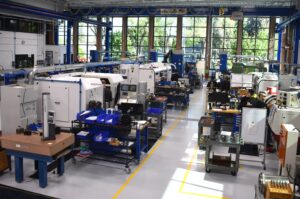
Photos courtesy of FISCHER USA, Inc.
Under the theme of “Technology Leader with Perfect Rotation,” FISCHER USA, Inc. (Racine, WI) will display its branded spindles plus offer a new service at Booth N-237470. With 85 years of experience in high-performance machine tool spindle design, in-house manufacturing and best-in-class repair services, the company will formally introduce the expansion of its repair services and exchange programs for non-FISCHER spindle brands to the North American market.
“We have invested substantially in recent years in new machines, processes and our most important asset, our people, to support our growth,” said Doug Kranz, vice president, FISCHER USA. “Today, we can now offer our full battery of services to work on non-FISCHER spindles most commonly found on high performance, high precision machines.” The company has also curated a special niche in the machine tool market in North America, focusing on more complicated spindles that other repair shops may tend to avoid.
For the immediate future, Kranz explained FISCHER USA will target Kessler spindles, commonly found on large format SW machines, typically used in the automotive market for high-production work. In addition, the company is focusing on Makino spindles for several lines of that builder’s machines, specifically MAG3. “Currently, MAG3 machines are well known to have spindles that only Makino repairs,” Kranz said. “We have been asked to repair them for several years now and have decided to make a major commitment to this type of work. As a result, FISCHER has invested in a pool of spindles and we will repair them, stock them and roll out our exchange program for MAG3 users Q1 2025.”
The MAG3 machines are used primarily in the aerospace sector, where FISCHER has a long history and strong presence directly with the aerospace manufacturers and their first and second tier suppliers.
Finally, FISCHER will target a repair and exchange program for Voumard multi-spindle, ID high-speed grinding machines. The company will maintain a pool of those spindles in stock, ready for immediate exchange with fast delivery and a competitive price point.
In regard to pricing: “Our price points will be lower than the OEMs in most cases, while we maintain the very high-quality standards FISCHER has long established in the American market,” Kranz said.
FISCHER will also display its impressive array of branded spindles and head assemblies for milling, drilling and grinding operations.
Rotary Vertical Grinder Sets New Standard in Grinding
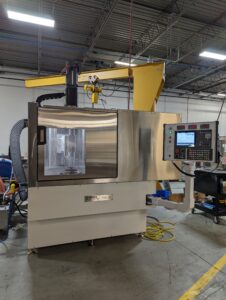
Medical Manufacturing Technologies, Inc. (MMT) (Charlotte, NC), a pioneer in cutting-edge manufacturing solutions, proudly announces the launch of its latest innovation, the Tridex RVG-10 Electrochemical Rotary Vertical Grinder (RVG). This advanced machine sets a new standard in grinding the outside diameter (OD) and inside diameter (ID) of aerospace components, offering unmatched capabilities and seamless integration into manufacturing processes. The company will be in Booth N-237307.
The RVG-10 is the ideal OD/ID grinder for large format round parts, rings, and honeycomb segments, making it perfect for new engine parts and repair applications. With its cutting-edge technology, the RVG-10 handles delicate, thin materials and high-temperature alloys with precision, ensuring superior performance in demanding environments.
“Innovation is our compass at MMT,” said Robbie Atkinson, CEO. “The Tridex RVG-10 is a testament to our unwavering commitment to excellence and innovation. Engineered with precision and advanced technology, this machine sets a new standard in the grinding industry.”
Key features of the Tridex RVG-10:
Heavy-Duty Construction: Built with cast iron components, the RVG-10 ensures durability and stability, making it ideal for demanding aerospace applications.
Precision Engineering: Equipped with preloaded linear guides and ball screws, the RVG-10 guarantees accurate and smooth operations.
Advanced CNC System: The comprehensive CNC system provides high-level control and automation, enhancing efficiency and precision in grinding processes.
Burr-free Grinds: Delivering consistent, burr-free grinds, the RVG-10 eliminates the need for deburring and other secondary operations, thus saving time and reducing costs.
The RVG-10 embodies advanced engineering and precision craftsmanship, providing unparalleled reliability and performance in the grinding industry. By addressing the specific needs of aircraft engine component grinding, this machine sets a new benchmark for performance, reliability and efficiency.
New, Innovative Grinding Technology and Automation Solutions
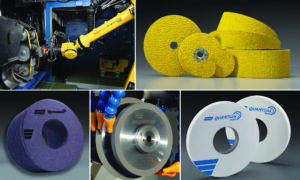
Bottom Row (L to R): Norton Worm Gear Grinding Wheel, Paradigm Wheel and Quantum Prime Grinding Wheels.
Saint-Gobain Abrasives (Worcester, MA), one of the world’s largest abrasives manufacturers, will highlight a wide range of high performance, innovative abrasive grinding products and technology in Booth N-237042. Making its trade show debut is the New Norton RazorStar™ belts, quick-change and fiber discs. They feature an innovative engineered-shaped ceramic grain, a revolutionary technology with unbeatable performance and metal removal rates in the toughest grinding applications when performing off-hand and/or automated grinding. A combination of uniquely shaped razor-sharp grains in an upright position along with a special supersized grinding aid, helps to significantly reduce heat generation for cooler cuts and longer life on a range of materials. In addition to impact grinding and off-hand applications, RazorStar belts are ideal for robotic applications in markets such as aerospace, automotive, oil and gas and general machining.
Also on display will be the Norton Quantum™ Prime Grinding Wheels, which feature proprietary nano-crystalline ceramic grain. The Quantum Prime grain delivers exceptionally high grinding efficiency and part quality, as well as significantly longer wheel life than traditional ceramic grains. Wheels are available in a range of types including OD, ID, gear grinding, toolroom, disc grinding, mounted wheels, surface grinding, creep feed and flute grinding.
Also to be highlighted is the Norton Abrasive Process Solutions (APS) Program, which provides custom grinding expertise by helping customers determine the most optimal grinding or finishing solutions for the application at hand, ranging from simple to complex, off-hand or automated, and for metal fabrication, production grinding and virtually any abrasives operation. The APS Program draws upon the vast knowledge of the Norton team along with access to 30 different machines, and the state-of-the-art APS Robotic Automation Cell. The APS team provides abrasive process development, optimization, automation and in-house testing.
Additional key Norton grinding technologies to be showcased at IMTS include:
- Paradigm® Plus Diamond Wheels feature new premium grain technology that complements a brittle metal bond to deliver even higher grinding performance on carbide round tools and periphery grinding on carbide and cermet inserts.
- Gear grinding solutions feature a new high-performance bond that is designed for gear grinding in extreme, tight tolerance environments will be featured. The portfolio of gear grinding products provides advantages in worm, profile, and bevel applications.
- The New Next Generation NORaX® N889 Micro-Structured Abrasive Belts feature a precise, flexible design for producing consistent, fine part finishes for a range of industry applications.
- For the high performance external grinding of cam and crankshafts and internal grinding applications in automotive and bearing industries, the Vitron7™ cBN Grinding Wheels featuring a high-precision vitrified bond.
Heavy-duty Fabrication Machinery Enhances Productivity
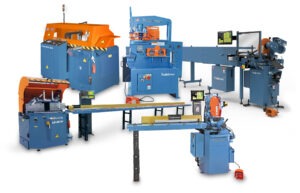
A complete range of general to heavy-duty metal fabrication machinery from Scotchman Industries Inc. (Philip, S.D.) will be presented at Booth E-135200. Live equipment demonstrations will showcase the features, benefits, cut quality and how the right equipment gets more work done with Scotchman products.
Cold saws to be featured in the Scotchman booth will include:
- CPO 350 w/Digital Quick Stop Measuring System – 14” manual cold saw with digital length gauge.
- CPO 350 with AutoLoader – fully automatic sawing system with bundle loader option.
- SUP 600 – large capacity precision upcut nonferrous saw.
- GAA 500 CNC DT20 – precision CNC controlled upcut automatic saw for cutting nonferrous at 90° with 20 mm drill tap.
Scotchman Ironworker:
- 5014-ET Ironworker, the world’s first and only 50-ton hydraulic ironworker with a revolving three-station turret punch. The innovative revolving turret accepts up to three different punch sizes that can be changed in seconds reducing setup time and increasing productivity. This American made hydraulic ironworker features 50 tons of pressure and can punch a 13/16″ hole in a 3/4″ plate. Other workstations include a 14” flat bar shear, rectangle notcher, angle shear, and a tool table for using a large variety of additional tools.
Scotchman 3” Belt Grinder:
- These 3” grinders help reduce grinding time and provide safe, vibration-free material removal. Contact wheel provides safe consistent grinding area. Tool-free belt change allows operator to quickly match abrasive to the application. Working height adjusts to accommodate operator and material. Top grinding table supported by graphite pad increases versatility. Adjustable tool rest, eye shield and emergency stop. Complete machine line up details will be unveiled at the show.
The complete line of products includes hydraulic ironworkers, circular cold saws, band saws, tube and pipe notcher/grinders, hydraulic presses, manual measuring systems, and programmable feed and stop systems.
New Tool Grinder to be Unveiled
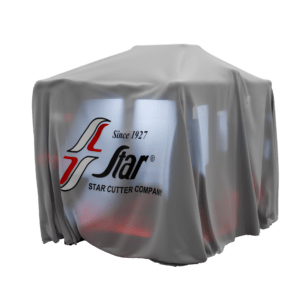
In Booth N-237013, Star Cutter Co. (Farmington Hills, MI) will unveil its newest generation tool grinder – the FLX. This 5-axis grinder offers high-efficiency carbide tool manufacturing within a compact footprint. It has been designed with a focus on flexibility, enabling users to modify features to exactly match their grinding needs. For unattended machining, FLX features a broad range of automation capability, producing large numbers of parts continuously.
The machine flexibility includes an ergonomic design with adjustable features that allow personalized setup to ensure operator comfort. With a grind zone of up to 203 mm in length and 19.05 mm in diameter, the FLX accommodates a wide variety of tool sizes. This breadth of processing is supported by up to 15 wheel changing stations with wheels of up to 6” in diameter, as well by intuitive Flexium Pro CNC, the newest control platform from NUM, helping to streamline operations.
Additionally, the machine can be equipped with truly modular automation that makes field implementation easy, while providing for optimal part quantity and wheel changing. Using waterfall programming, FLX can produce up to 1105 tools (3-to-7 mm diameters) before unloading.
FLX is designed to be precise and accurate in both controlled and uncontrolled climate conditions, giving it broad application across industry, even in harsh environments. It features reduced warmup time, elimination of redundant chiller systems, and 35 mm linear carriages for durable machine movement and longevity.
The FLX has a footprint of 72” W-x-55” D (94.5” D with the automation model), and a height of 73.3”. Machines weigh 7,000 lbs. (9,000 lbs. with automation). Other options include a bolt-on tooling rail with T-slot construction, runout minimizer, and a two-wheel changer (for non-automated machines).
In addition to the new FLX grinder, other Star Cutter products to be featured include:
- TRU TECH T93X Centerless Grinder
- Louis Belet Swiss Cutting Tools
- Round Tools: solid carbide drills and reamers, deep hole drilling solutions, PCD and 3D printed tooling
- Gear cutting tools: hobs, shapers, Scudding® and skiving cutters, and more
- Carbide blanks and preforms
IMTS 2024 will be the first opportunity for users to see the FLX grinder. To arrange an appointment in advance, email sales@starcutter.com.
Starrett to Display Range of Carbide Tipped and Bi-Metal Band Saw Blades
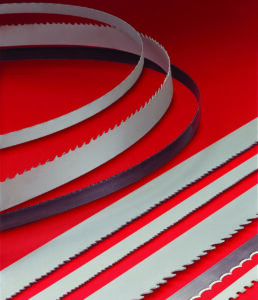
The L.S. Starrett Co. (Athol, MA), the world’s largest saw blade manufacturer and a leading global manufacturer of precision measuring tools, gauges and saw blades, will display band saw blade solutions for challenging cutting applications at Booth E-134130.
Starrett offers a wide range of multi-purpose and application-specific band saw blades including carbide tipped blades which are ideal for cutting extremely hard, abrasive materials and bi-metal for cutting a variety of ferrous and non-ferrous materials. Also, Starrett band saw blades coated with carbide grit and diamond grit cut highly abrasive materials with precision, producing an excellent finish. A complete line of carbon band saw blades are also available for horizontal and vertical machines with manual or gravity feed.
Starrett’s sawing experts will be available at IMTS to discuss application requirements and can help select the right saw blade to maximize sawing operations.
New Filter for HSS, Carbon Steel and Other Ferrous Metals
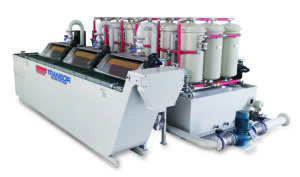
operations such as HSS, carbon steel and other ferrous metals.
Transor Filter USA (Arlington Heights, IL) will introduce an all new series of filtration units in Booth N-237422. The all new Transor Injection Cleaning Concept (ICC) combines Transor’s patented ultra-fine filtration with a magnetic pre-filter. This combination makes the ICC unit ideal for machining operations such as HSS, carbon steel and other ferrous metals where significant stock removal presents a filtration challenge. In typical operations, the coolant oil from the machine is pumped to an inlet on top of the magnetic separator where the majority of the sludge is removed from the oil. This unique process enables the separation of the “dry” sludge of the magnetic pre-filters prior to the dirty oil being introduced into the filter elements. The sludge from the magnetic separator slides down a shoot into a container for easy disposal. In larger units, it falls onto a conveyor that empties onto a dragout. The dragout also captures the sludge removed during automated backflushing process. Like all Transor Systems, the filter elements are cleaned with an automated backflushing cycle that reduces consumable costs with no machine downtime. The ICC also has an enhanced feature that helps to loosen the debris captured by the filter elements and improves elimination from the elevated filter vessels. Additional machine features include operator friendly touchscreen interface, chiller unit for thermal stability that maintains coolant temperature to +/- 0.01ºC, and automatic protection shut-off in case of overload or malfunction.
Innovative Industrial Grinding Solutions
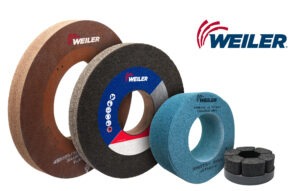
Weiler Abrasives (Cresco, PA), a leading provider of abrasives and power brushes for surface conditioning, will showcase a broad portfolio of industrial grinding solutions. Weiler Abrasives will be in Booth N-237253 to explore engineered solutions for gear grinding, precision grinding, roll grinding, metal conditioning and foundries that help operations increase productivity and solve challenges.
“Our customers often serve industries like aerospace, automative, medical and other manufacturing of precision components where quality, product performance and on-time delivery are non-negotiables,” said Kyle Thompson, sector manager – industrial production Americas for Weiler Abrasives. “We are dedicated to helping our customers improve their surface conditioning processes and deliver precision-made parts.”
Partnering with Weiler Abrasives can help companies unlock their full potential. The company’s approach is built on the foundational pillars of partnership, technology, and service, with the ultimate goal of providing innovative, sustainable, and scalable industrial grinding solutions that are tailored to the specific needs of the customer and their industry. These goals are achieved through a program called Weiler Process Solutions (WPS), a comprehensive process where expert application engineers from Weiler Abrasives access a specific process to identify improvement opportunities resulting in quantifiable cost savings.
Weiler Abrasives is also introducing Precision Express, a new service that matches an in-house profiling cell with on-hand stock, cutting lead times down from months to days. Schedule a consultation at the show to explore a wide range of advanced technologies by visiting www.weilerabrasives.com/imts.